We may receive a commission when you use our affiliate links. However, this does not impact our recommendations.
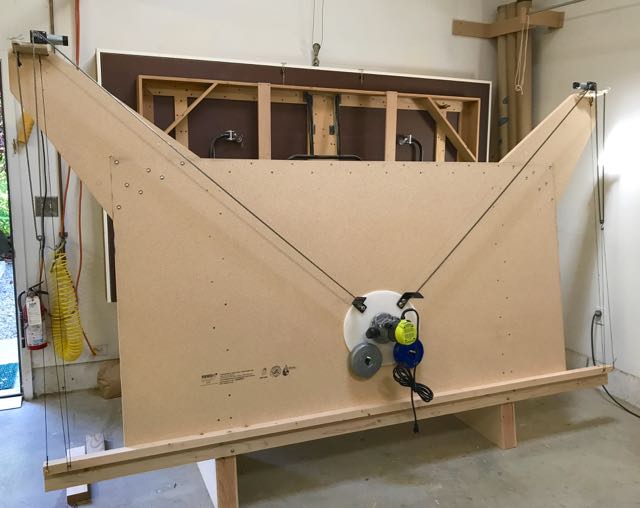
The Maslow $350 CNC kit. The simple base in the photos was designed and built by Curtis Erpelding.
Last December when I started this series on the Maslow CNC, my goal was to evaluate the $350 kit with a focus on how it might fit into a hobbyist woodworker’s world — the kind of machine a woodworker in a home shop who might want to try a bit of digital woodworking at a low price. With that in mind, I look at the Maslow CNC and come up with two basic questions to answer.
First, does this machine fulfill the needs of a woodworking hobbyist? Considering that most woodworkers and the readers of Popular Woodworking magazine primarily work in solid woods, in general, the answer is no. The Maslow is not designed for cutting solid wood. Since it moves a router resting on a small base, that makes it better suited for working on large sized sheet material like plywood or MDF.
To work properly, it needs a large surface area to keep the router flat as it moves. Smaller solid wood boards are usually too narrow. That’s not to say, that you can’t be clever and clamp together several boards of the same thickness to increase surface area when you’re trying to cut a single board in the middle of the stack. In other words, with a little work and clamps and a number of passes you could cut solid wood.
Since cutting large flat materials is what the Maslow is designed to do, that doesn’t mean the machine isn’t still useful to hobbyist woodworkers. If the team achieves its intended accuracy of 1/64” (.4 mm) the Maslow could be used to cut patterns for shaping solid wood on a router table or shaper. 1/64” is not joinery accurate by any means, but for many pattern parts and shapes in furniture or other woodworking projects, it might be accurate enough. Critical lengths would have to be checked carefully to make sure all parts intended to be the same length match.
When it comes to patterns, from my own experience as a furniture maker using hundreds of them over the years, I believe in the value of good patterns. Whether you make your own on a CNC like a Maslow or have someone else CNC them for you, patterns are a good thing. A good pattern makes your work better, more accurate and by using them, you’re far less prone to making mistakes. Also, if the Maslow — or any CNC, along with good CAD software opens you up creatively into exploring more adventurous shapes in your work than straight lines than that’s a bonus.
How useful is the Maslow?
Second questions, how practical is the Maslow CNC? Two answers. As a very basic, bare bones CNC, using the Maslow requires some user involvement. It’s a hands-on experience when it comes to the technology involved. That’s not so saying that you wouldn’t get used to doing regular procedures on the machine quickly. You just need to always be aware of what’s going on when using a machine like this. It’s less a woodworker’s CNC then a “maker” kind of CNC project designed for those that want to explore the world of digital fabrication. Unlike assembled consumer or commercial CNCs with tested pre-packaged software/hardware solutions, the Maslow requires extra attention and a willingness to work through problems as they come up.
Other considerations are the physical size of the Maslow and how well it performs. In terms of space-saving in a small shop, it’s wonderful that it’s set up vertically so you could move it out of the way or position it close to a wall, but it still has a big footprint that requires about 12’ of length. Inside the 48” x 96” working area, the sweet spot in the center is about 30” x 72” of useable space. That’s certainly plenty of working area for most plywood cutting tasks.
Then there’s the speed issue. The Maslow is slow. How slow? To illustrate, imagine this: Take out a 48” long ruler and pencil and draw a 30” line along its edge and take a whole minute to do it. Or, just watch the video above. It’s pretty slow. Don’t expect to get a lot of work done in a hurry — which makes using it as a professional tool, doubtful. The good news is, once running a job, it works on its own. You don’t have to hold onto a tool or move it to operate it. It just runs. While the Maslow is taking its time doing its thing, you can be in another area in your shop working on something else.
Recommendations
By this point, the advantages and limitations of a $350 CNC kit should be obvious. If you’re realistic in your expectations, geeky enough, on a tight budget and patient, or just want to try it, the Maslow is a fun project. Just keep in mind that the Maslow CNC is not like a conventional CNC. If you’re interested, the bad news is the last batch of Maslow’s sold out very quickly. The good news is the Maslow team is building a signup list for a possible new batch this fall. If you’re inclined, get your name on the list. Here’s the link.
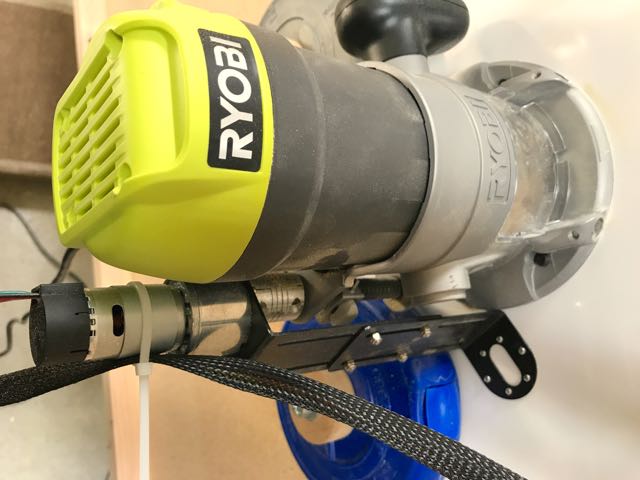
The Z-axis option for the Maslow is another motor that’s mounted to the side of your router. It moves the router up down as instructed by the controller. A recommended option.
If you do decide to build a Maslow, I recommend the following improvements and options.
Get the Z-axis Option
If you order a Maslow CNC, get the Z-Axis option. It’s less than $70 and well worth it. To make it work you’ll need to pick from the list of tested routers, but once you have it setup, it’s great. Since most cuts require multiple passes, this option takes care of resetting the Z height for you.
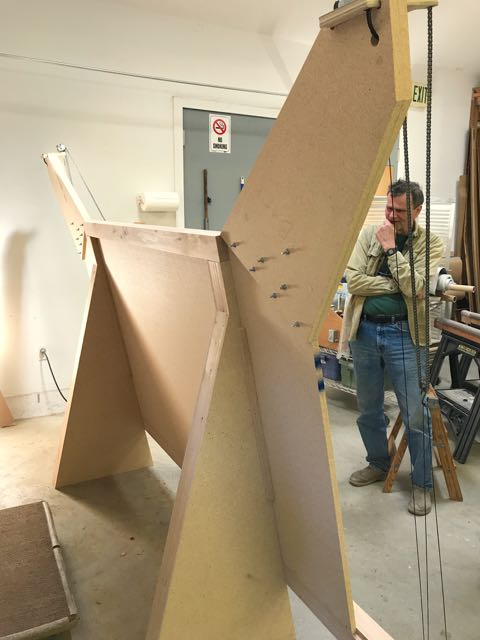
Curtis Erpelding studying his Maslow CNC. Note the details in the frame and base. 3/4″ particle board for the base. Double thickness wings. Leg supports stiffened with 1/2″ particle board gussets. A rigid 2″x4″ at the top. The result is a stiffer and flatter frame.
Build a Better Maslow Frame and Base
The design for the Maslow frame and base is simple. It’s easy to build and cheap. But, the furniture maker in me wants to do better. I’m not alone. Fellow furniture guy Curtis Erpelding’s interpretation takes it all the way. He’s built the base, right – the frame, bed and wings are stiffer. The base is flatter. All desirable features in any CNC.
Bonus: his version is even simpler to build and cheaper than the Maslow version. In pretty much every way, it’s better. Yes, one could build an elaborate and even fancier base out of hardwood but before you over do it, keep in mind the Maslow’s purpose, cost and level of precision. If you’re building a Maslow, you can learn from Curtis’ simple, strong and inexpensive solution. I recommend it.
If you’re leaning toward his design, there’s no real plan available. But, it’s simple to extrapolate. Starting with the Maslow dimensions from their plan, just study the photos I’ve posted of his version of the base and router sled. Be picky about your choice of 2″x4″ material. Start by milling all the boards flat and square. The frame stands are gusseted with 1/2” particle board sides. He’s used 3/4” on the base and doubled the arms to resist flex. When milling, he a puts down a 1/2” spoil board on top of his 3/4” base to keep it in good shape. Everything is bolted or screwed together for simple and quick replacement. All excellent improvements.
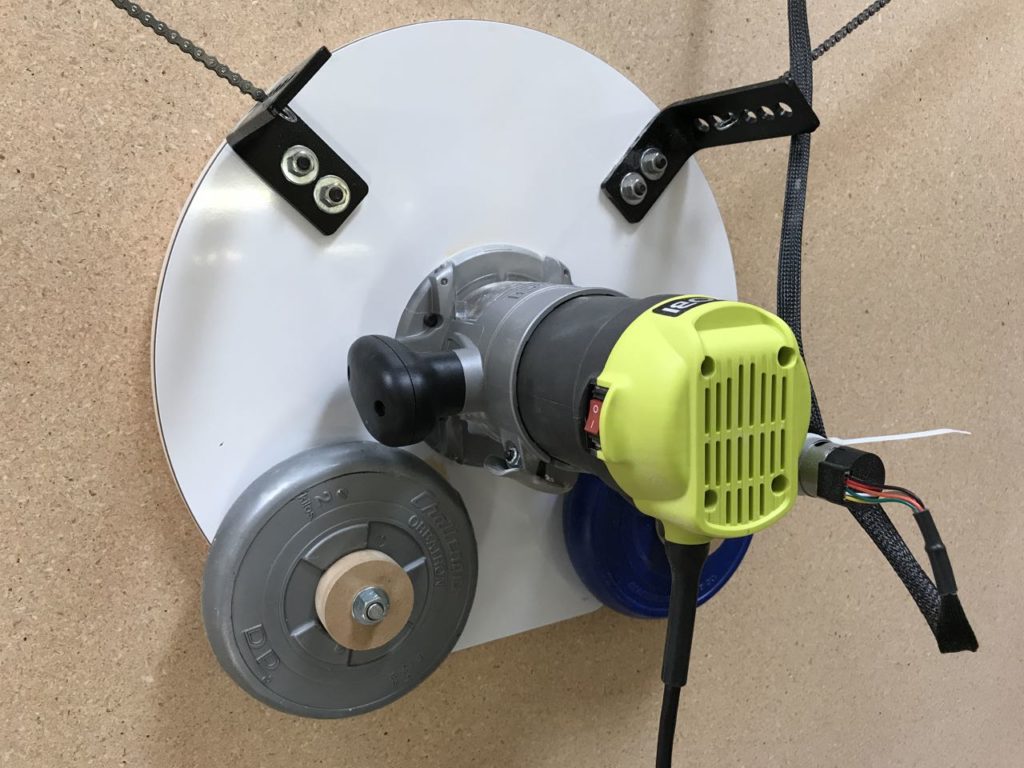
Curtis Erpelding’s rigid router base for the Maslow is made out of Baltic Birch Plywood with a smooth laminate on the bottom to reduce friction.
And, don’t forget the router base. Curtis has built a good one using rigid plywood with a laminate surface to reduce friction.
Engage with other Maslow Owners
One of the most valuable features of the Maslow world is its engaged owners in their online forum. If you have a problem or a question, there’s a lot of people who’ll be happy to help. Besides any issues you might come across building it, testing it or learning to run the Maslow you can expect the machine and software to continue to get better and better. Keep on top of the latest developments in the forums.
Interview with Bar and Hannah
Here’s is more information about the Maslow and how it works at the Tested studios by two of the founders of the company, Bar and Hannah.
The Maslow CNC, looking ahead
The Maslow CNC kit, at only $350 and assembled with easily available materials is a remarkable achievement for a large size CNC at such a low price. And, because the designs and software are publicly shared through open source rules, you could, in theory, build one for even less if you were willing to scrounge around for parts. But, fair warning: if you decide to do it all on your own there are a lot of details you have to get just right to make it all work. Letting the team at Maslow get all the parts together, document the project, write the software and test everything makes that $350 look even more like a good deal.
Looking ahead, I expect to see a lot of interesting creations by Maslow users. And, this is certainly not the last version of this CNC design we’ll see. With the project being open source, continuing improvements and heavier duty and more accurate versions are likely to appear in the future. I expect to see interesting new derivatives of this clever hanging router CNC configuration.
Special thanks to Curtis Erpelding for all his work building and testing the beta Maslow CNC that I used for these articles. If you’re building a Maslow, study his excellent frame and base. Smarter, cheaper, better.
To see the entire series on the Maslow CNC click here.
Here are some supplies and tools we find essential in our everyday work around the shop. We may receive a commission from sales referred by our links; however, we have carefully selected these products for their usefulness and quality.