We may receive a commission when you use our affiliate links. However, this does not impact our recommendations.
When it comes to doing precision work that has to be performed over and over again, it’s easy to fall into the siren whine of the router.
The router is probably my least-favorite woodworking tool. I don’t like how it is noisy. It never produces a ready-to-finish surface for mouldings. And it can destroy a workpiece faster than any power tool I’ve dealt with.
I attribute my dislike of this tool to a personal defect in my head. I have seen authors and co-workers work wonders with this tool. For me, almost every encounter is frustrating. So it might be a genetic problem.
Today I tried to get past my dislike of the tool and made some crazy complex templates for some brass pulls I’m installing on a teak campaign chest. These pulls require recesses in two different layers, and there isn’t a single right angle.
So I carefully made a template from MDF, but I discovered I had made a few cutting mistakes. No problem. I made another template from MDF. That one worked fine for the first two sample cuts, but the MDF was too soft. The bearing on my pattern bit compressed the MDF and the recess was too big for the hardware.
So I used Baltic birch plywood for the template. Surely that would be hard enough.
It wasn’t. In two critical areas the birch compressed and left a gap between the wood and the hardware.
I had started this process at 11 a.m. At 5 p.m. I realized I had been fussing with these templates for six hours and didn’t have a single pull installed.
I grabbed a chisel. And within 20 minutes I had a pull installed.
If you love your router, then more power to you. I have – after 23 years of messing with them – realized that I am not a router guy.
— Christopher Schwarz
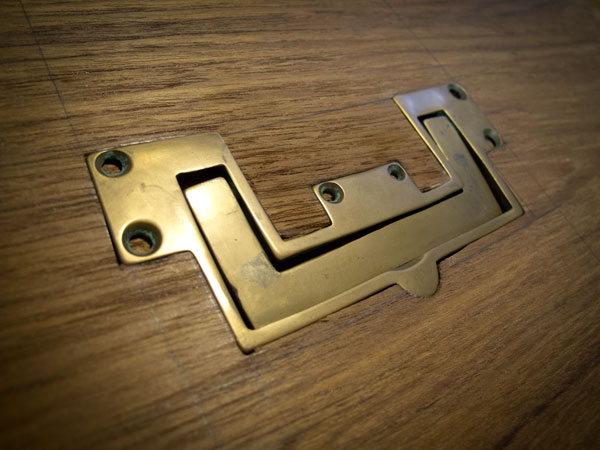
A pull I installed with a chisel. There are some small gaps that can be fixed with splinters, glue and dust.
Here are some supplies and tools we find essential in our everyday work around the shop. We may receive a commission from sales referred by our links; however, we have carefully selected these products for their usefulness and quality.
I’m just starting to learn to use hand tools extensively. Pretty quickly, I developed a distaste for powering on my machine tools. The noise is a big part. First the whooshing drone of the dust collector, then the sound of the table saw, planer or, worst of all, the router. Finally after completing the cut I often forget to power off the dust collector or leave it running for the next step. The shop is so much more peaceful with the sounds of hand saw, plane and chisel. Not to mention the safety. Never will a router plane yank a workpiece violently from my hands.
The accuracy, for a newbie for me, was surprising. I always assumed that a well tuned power tool would be more accurate than it’s hand powered cousin. I was wrong. Once one develops the skill and sensitivity with hand tools, it’s easier to be extremely accurate. The idea of choosing what side of a knife cut to snuggle up to is not something I ever considered using a table saw (it is now). I was accurate before but, like sharpness, the path to accuracy narrows with experience.
Good thing this blog is in writing, can’t hear much anymore because of my router:-). Seriously, if you are woodworking for the joy of it, a few hand tools and classical music in the background is where it’s at. If you are making a living at it the set up and time taken to do good router work are worth it when making multiples of an endeavor. However, when making one or just a few of something I find that more and more I can do it faster and as good or better with a few hand tools. I would add a small router plane from Lie Neilsn to the chisel and possibly a couple of carving tools. Get the bulk of the waste out in any manner you choose, router, brace, drill, whatever works for you. Do the fit up with a few simple hand tools and you will be done before the router only person has their jigs set up and are ready to go. Now if you are making a dozen identical chairs, spend the time making the jigs. But to do quality work you will still need to finalize the fit up with a chisel.
Ah, this has been a very successful blog post. A lot of interest and information trading has gone on here.
I’ve learned a lot.
I like to use Super-Glue (Cyanoacrylate) on the edge cuts of MDF. It’s fast, and makes the soft edge as hard as the face. (This is also the method I use if I need to paint MDF) The bearing likely dug into the template because it had debris on it, turning it into a sanding drum. Clean and lubricate the bearing. You can eliminate the wear on the template/jig, if you use a guide bushing, with an oversized template made by tracing around the part with an Offset wheel gauge. Veritas makes a nice set.
Chris, you can also do it the same way gunsmiths inlay locks and side plates; file a “draft” all around the pull, set it on the wood in the same orientation that it will be when finished, trace or scribe all around on the bottom of the pull. Then, rough the waste out with a hand brace or drill. Remove the rest with a small chisel up to the line. Smoke the pull and set it in. Remove the black marks until the pull is flush. Takes less time than you might think. Try it, you will be happy with the clean, tight fit.
mike siemsen has the right approach. Use the router to remove the bulk of the waste and do the precision work with a chisel and marking knife. Sand cast hardware has so much variation from piece to piece that even if you got the first pull perfect, it is unlikely that the next would fit the same. Machined hardware is (usually) more consistant, but you limit yourself to what is available. Routers have their place (i don’t mean the garbage can) but don’t ask them to bring more precision to the job than you are capable of yourself. On a large cabinet job I had 200 olive knuckle hinges made in china, rights and lefts, and not two fit the same. I undersized my jig a thirty-second and hand chiseled them all for a tight fit.
Well, I think that the router works fine but as with other tools using a router is not a gift; it is a skill. Once the skill of using a router is mastered then there is no doubt the tasks get done quicker and better; almost too perfect and that is the problem if you want a hand finished look. I guess one also has to consider how many tasks must be repeated. Sometimes the hand tools are quicker than the machines. There is also a beauty to a quiet shop whose silence is only disturbed by hand tools but this is not for a real woodworker; it is the gentleman woodworker meaning the money does not have to made from producing goods. If your living depended on real woodworking you would have to take lessons from Norm and Tommy or David Marks.. Had Roubo access to a router he would have mastered it and instructed in the use of this fine machine. As I get older I appreciate the relative silence of hand tools but my routers have made and saved me a lot of money. Yes, I have fine hand tools but if my living depended on them I would be teaching hand tool woodworking. As you know it is more lucrative than actually doing it. Very few woodworkers can make a good living with hand tools alone as I am sure you know. In order to really make a fine living at it you have to elevate the work to art and get an art price for it. That involves another level of expertise called marketing and that skill exceeds all others when it comes to making money as I am sure you know.
With cast brasses they need to be hand fit as they are all different. I would lay the brass upside down in place where it goes, trace around it with a pencil then waste out the center section to depth with either a router or hand tools staying at least an 1/8th inch away from the line(freehand), use a 1/4″ bit in the router, do it in more than one pass if it is deep. I would then put the pull in place and screw it down, then knife around it and chisel to finish. Patterns or templates are OK if you have many to do the trick there is to not rout against your template when hogging stock but just for a final light clean up pass. This puts only light pressure on the template. Waste could also be removed to depth with a center bit in a bitstock or a Forstner bit at the dril press.
I am left wondering if you used all of that time 11AM till 5PM trying to make the same router/bit combination work for you? All you confess to is going from MDF, a poor choice if you are heavy handed as you found out, to BB ply, a good choice, many would have started there. Every time you use hand tools on a job, do you find the first one you pick up does all aspects of the job? Seems you are whining about not being flexible at all. For delicate work where you need control, were you using a 3Hp plunge router? Or something smart like a Dremel tool with a flat base, something where you can actually steer it to where you want it. Unbunch yer panties, and go flexible. Either that or just use yer hand tools for everything. Done properly a routed relief will be faster once you figure out how to pattern route, will offer you exact duplicates, and to a perfect depth. Not being a “router guy” is clearly a choice, however a poor one for one professing to be a pro woodworker. This article leans toward saying, because you couldn`t do it, it can`t be done.
I will use a Bosch Colt for these kinds of inletting to gain control. But when I only have a few to do, or they are inconsistent in shape or manufacture as in hand cast, I use a chisel and a non-powered router like the Stanley 71 to get them in without gaps.
routers require a bazillion jigs, templates and the like to do quality work. Hand work is essential for all of us at one time or another why not use chisels in lieu of a router?
Amen, Chris! I feel exactly the same way…my router is the least-used tool in my shop…it’s mounted in a router table and there it sits. You did a nice job installing the pull…I enjoy your articles and your work….keep it up!
Is it possible that because your drawer pulls begin life as castings that they each vary ever so slightly from their brethren? When great precision is not a requirement of the end product, the pattern, wax and casting process produces quite a lot of smallish variations between individual castings. Additionally, as castings cool, angles change “just a bit”. Then as castings are de burred and individually finished, dimensions from unit to unit wander just a bit once again.
So your perfect template for casting “a” may not be as perfect for casting “c”.
You are so right about MDF and router bits. For small batch runs of parts, I use 1/4 inch aluminum plate at my bearing surface. It can be worked with wood working tools, and does not compress.
Masterfully performed! The choice of pull and the teak is gonna make a beautiful piece.
I use 6mm MDF as a profile and a 1/8th router bit to get an exact match. No problems.
Art