We may receive a commission when you use our affiliate links. However, this does not impact our recommendations.
Did you know that woodchips can tuck themselves under a planer’s blade? Well, as crazy as it sounds it really happen to me last week.
We have a great thickener planer in our shop. It’s a Ridgid machine that is built well, works well, and is priced well. We bought it two or three years ago and I have been enjoying using it quite a bit. Its components are robustly built from steel and aluminum components, and I wholeheartedly recommend it for anyone who needs a good planer. A few days ago, as I milled a board of hard maple I noticed that the board left the planer with a distinct and significant tear-out pattern.
I have never seen such a deformity and decided to look at the blades’ assembly, speculating that perhaps they dulled out. What I saw surprised and puzzled me. I found that woodchips had gotten stuck in between the blades and their bed. How could that happen I thought, after all, isn’t the blade clamping bar, the one that is screwed over the blade and provides tons of pressure over it, supposed to have prevented this from happening? What kind of maple board could have caused such a problem? Is it because this particular board was extra hard and fought fearlessly with the blade to the point that its extra dense fibrous chips wedged themselves in? Or perhaps this has nothing to do with the maple board but was actually a result of an operator error? This brings us to the incident that happened a week before.
Two weeks ago, as I was milling some seat stock for our 8th grader stool project I possibly made a mistake. As I was feeding a slab into the planer I heard a bang and instantly the stock shot out of the planer. I was aware that the catapulted slab had an uneven upper surface which was also unparallel to the bottom surface, but in general, this should not have been an issue since the planer’s job is, after all, to gradually surface the uneven top to make it parallel with the bottom. Was it perhaps because the slab was a piece of greenwood with a softer than usual surface, which caused the rubber feed rollers to skid and prevented them from securing the work? In any case, the slab was just too off-kilter for the machine so the outcome was a reflexive response by the poor planer. And like someone who eats something that upsets their stomach the machine vomited back the slab quite violently. Immediately after this I examined the board, did some corrective resawing on the band saw, and then reintroduced it to the planer for a satisfactory resumption of the milling process. In the following few days, I milled basswood and pine and it all looked fine.
Whether it was the maple or the pine board that caused the chips to tuck themselves under the blade, I still needed to deal with the issue. I unplugged the planer, opened the blade assumably hood, and one by one unscrewed the clamping bars, lifted the blades, and removed the packed fibers underneath them.
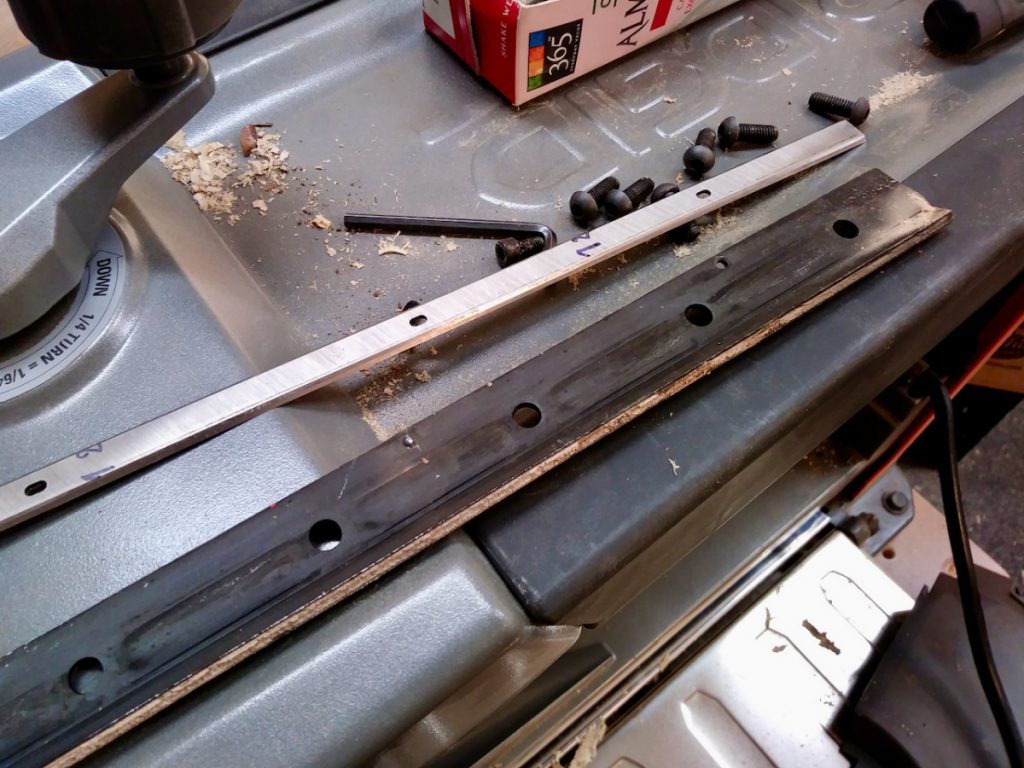
The blade (thin and shiny) and the clamping bar (dark gray) before cleaning. Notice that I labeled the blade cutting edges for reference. #1 is the edge I am using. As the 1st edge gets dull I will turn them around so edge #2 will face the wood.
I reassembled everything and gave the planer another chance with the maple board. This time the results were very satisfactory. I intend to monitor the situation of the blades and check if new chips get tucked underneath them. If they do, that means that the bars that clamp down on the blades are not providing sufficient pressure – which is a mechanical engineering misdesign. Let’s hope that this will not happen again and that a call to Ridgid Customer Service department will be unnecessary.
Here are some supplies and tools we find essential in our everyday work around the shop. We may receive a commission from sales referred by our links; however, we have carefully selected these products for their usefulness and quality.