We may receive a commission when you use our affiliate links. However, this does not impact our recommendations.
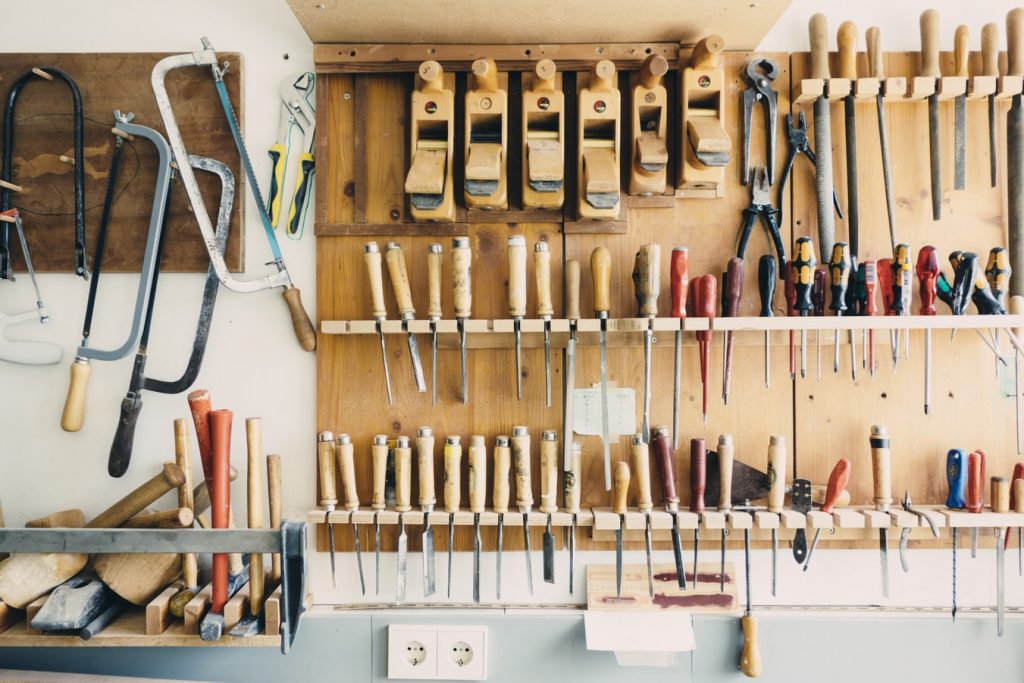
Photo by Barn Images on Unsplash
Basic woodworking tools are different from beginner woodworking tools. For one thing, I don’t like to use the word “beginner” unless I am using it accurately. It’s not a very useful label, in my opinion, because it implies that there are clear-cut and hierarchical steps in your growth as a woodworker. Who wants to return to grade school during his or her valuable shop time? So I only use the word “beginner” when I’m talking about someone who is touching woodworking tools for the first time.
It’s Basics Week 2024! Use the code Basics25 to save 25% off your first month or full year of PopWood+.
“Basic,” on the other hand, is a word that allows for growth – and that’s exactly what you want in your woodworking tool kit. You want to be able to take the same kit with you through many years in the craft. With my basic woodworking tools list, I wanted to provide a core set of tools that will serve you well from project to project. I’m especially concerned these days with the transition to hardwood furniture making, as opposed to plywood boxes of various sizes. That’s the transition I’m making right now in my own work!
The other crucial thing I am concerned with is having tools that will allow me to work efficiently with rough cut or reclaimed lumber, because I need to save money on materials. Paying full price for many board feet of smooth, dimensioned stock is a fairly quick way to go broke – or at least lose your love of woodworking.
Note that I am by no means reinventing the wheel with this list. I am borrowing heavily from the Popular Woodworking Magazine “I Can Do That” list from years ago. I have refined that list to suit my style and, again, to take into account the use of rough lumber.
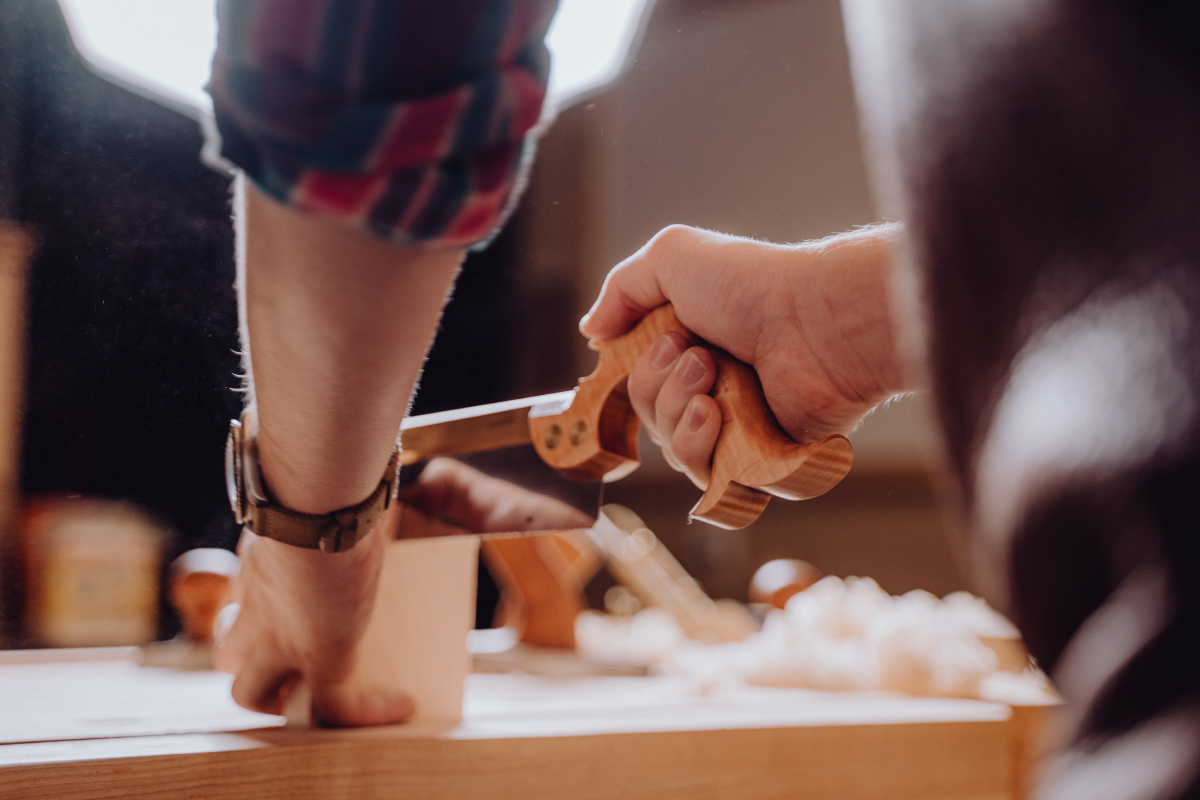
Photo by Bailey Alexander on Unsplash
My Basic Woodworking Tools List – Furniture Focus
1. Power jointer and thickness planer. I have developed various means of straightening the edges of my stock with hand-held tools, but I don’t see a way to efficiently flatten the faces of rough or reclaimed lumber without a power jointer. It’s part of the first few steps for any furniture project, and I want to be able to move through this step quickly and into the more interesting work. The thickness planer is also a huge time-saver, compared to hand-held tools.
2. Circular saw, for rough dimensioning (especially long rip cuts). If you have a good table saw, that’s even better, because you can of course use a table saw for all sorts of joinery work – not just dimensioning.
3. Hand saws, a router and two router bits. These are the tools I use for cross-cutting, straightening edges and cutting boards down to final width. The two router bits are a straight cut bit and a flush trimming bit.
4. Jigsaw, for cutting curves. A coping saw is also nice to have for detailed work.
5. Combination square and tape measure, along with crayons, pencils, a knife and an awl for marking.
6. A power drill or two, and bits as needed.
7. Rasps, files, a random-orbit sander, a smoothing plane and a block plane. These are the minimum for smoothing all surfaces of the final work, and doing it efficiently. Don’t forget that you’ll need sharpening supplies for the plane blades.
8. Joinery gadgets? I’m not yet sold on buying a biscuit joiner or a pocket-hole set. Again, if you already have them I think they are great. But I’m looking for projects I can complete with a combination of hand-cut joints, router joints and straight-in screwing. We’ll see how it goes.
9. Chisels and a wooden mallet.
10. A hammer and some screwdrivers.
11. A Workmate, a puttering bench and clamps. Until I can invest in a large furniture-making workbench, I think I will be able to make do with the Workmate and a small bench. Again, we’ll see how it goes. A good-sized supply of clamps, of course, is always necessary.
Here are some supplies and tools we find essential in our everyday work around the shop. We may receive a commission from sales referred by our links; however, we have carefully selected these products for their usefulness and quality.
The tool that improved my woodworking the most is a good 12” combination square. A “must have” on my list. The second is an adequate workbench. I love my Workmate, but it is not ideal for planing anything over a foot or so unless I pair it with a planing board.
As far as power tools go, a 6-8” jointer and a planer are essential time savers. I’ve hand jointed 10” wide x 8+ feet long hard maple boards. Even with the right tools, it is not easy work. I’d rather spend my precious shop time doing the joinery, inlay, veneering, etc. that I like, rather than the grunt work of preparing 10’s of board feet for use.
The real key to tool selection is to match it to what you want to build. Same with the size of the machinery. If you like building small boxes, you might not need the 37” bandsaw or the 5 hp table saw, but if you love making kitchen cabinets or large case pieces and exotic woods, then they may be just what you need.
The tool that improved my woodworking the most is a good 12” combination square. A “must have” on my list. The second is an adequate workbench. I love my Workmate, but it is not ideal for planing anything over a foot or so unless I pair it with a planing board.
As far as power tools go, a 6-8” jointer and a planer are essential time savers. I’ve hand jointed 10” wide x 8+ feet long hard maple boards. Even with the right tools, it is not easy work. I’d rather spend my precious shop time doing the joinery, inlay, veneering, etc. that I like, rather than the grunt work of preparing 10’s of board feet for use.
The real key to tool selection is to match it to what you want to build. Same with the size of the machinery. If you like building small boxes, you might not need the 37” bandsaw or the 5 hp table saw, but if you love making kitchen cabinets or large case pieces and exotic woods, then they may be just what you need.
Heheh. Your list of “11 (or so)” tools is probably closer to 24+ tools.
Jointer/Planer is top on my list as well, but in my shop, a $250 vintage 14″ bandsaw is superior to a circular saw for ripping (and cuts curves as well).
A powered router is strictly forbidden…I would rather use my hand skills and take credit (or apologize) for each joint. 😉
My $0.02 worth. I agree with the thickness planer [mine is 10″] but anything over a 6″ jointer is expensive and space-consuming, so use hand planes as in your later blog. I inherited an 8″ table saw that my dad and I used to build a 12′ outboard boat back in 1955. I’ve used it for ripping, but I’m having second thoughts because of safety issues. Some have suggested a band saw for ripping, which is quieter and safer to use. I gave my router away [and hope to get rid of my Freud biscuit joiner and 6″ jointer]. A quality eggbeater drill works every bit [pun not intended] as well as a power drill, and they cost less. A coping saw and a jewelers saw negate the need for a jigsaw unless you are into making puzzles. Chris Schwarz has a video short on one of the Highland Woodworker series showing how to joint the edge of a board with a plane and a simple jig on the workbench surface. Another reason to bypass the jointer.
Bob Newman
I enjoy reading the comments about what is considered a basic need in tools. I purchased and read Christopher Schwarz’s “The Anarchist’s Tool Chest” and considered the tools he listed in it. I have them all and then some. You could call me a tool collector, my family does.
About forty years ago I purchased a Shopsmith Mark V because I lacked space for a large shop, and also moved around the United States a lot. Later I purchased another Shopsmith Mark V Model 510 for the increase in table size and flexibility. I do wood working as a hobby, not to do many projects as fast as possible. I also have every tool and accessory that Shopsmith makes for the two primary tools. Their quality is excellent, and while I enjoy antique tools like the 1912 three phase electric Camel Back Drill Press I purchased for my son’s shop, the Shopsmith does every thing I have ever needed.
In the sixty years of woodworking I have found two tools of increasing necessity. One is a band saw. I can do most of my work with a band saw and hand plane. The second tool is a bow saw, or actually several bow saws. They will replace the band saw if required, though they are slow. One I made about twenty years ago has a one and a half inch wide rip blade and is about thirty inches long. I think the blade is from an old industrial band saw blade I picked up and sharpened into a rip saw blade. It works very well on ripping lumber, logs, etc. Though it tires me out to much to use it now.
Anyway, this is my two cents worth, and a little different view point from others expressed here.
The one item I would add that would be a Dowel Max. Once you use this for all kinds of joinery you will find it can do the job!
More than a decade ago I spent 2 weeks in Maine aspiring to learn furniture making. On my return home I started enthusiastically planning to turn my basement into a proper shop – with all the “essential” tools I had learned to use. My list reflected my engineer’s preference for buying quality and quickly exceeded $25k in power tools alone (table saw, band saw, joiner, thickness planer, drill press…) even before solving the power, lighting and dust challenges.
Then I managed a reality check and put the whole project on hold for later in life when I would actually have time to work in the shop.
Now as I approach retirement, I am excited to read that Chris Schwarz and Tom Fidgen are embracing the “unplugged” workshop approach. Instead of a basement, I now have a detached garage (in a condo neighborhood), and both the power required and the noise generated by power tools would be problematical.
While I understand the time-saving potential of power tools, woodworking will not be a paycheck for me. I look forward to a future article from you (or Chris, perhaps) listing “Basic Woodworking Tools for the unplugged workshop”.
I agree that this list, plus comments, was starting to look like “stone soup” … but I have to say that it looks like some order is now emerging from the chaos. Thanks for all the helpful comments! We’re hoping this helps move woodworkers forward in their basic knowledge and in setting up the right kind of shop.
Dan, my work space that is available for power tools is quite small, about 6′ x 20′. It may seem like a lot on the surface, but a long rectangle is a bear to work in. It requires a lot of serpentine action. That said, I don’t have too much room for large footprint tools. I have settled finally on three big tools; a small bench saw, a thickness planer, and a drill press. I had to forgo the jointer, so I use hand tools to make up for it’s absence (as I do with a lot of my hand tool techniques). I have gotten to the point where I can flatten one side and true an edge of a board reasonably quick. I then finish it up with the thickness planer and table saw, giving me a nice flat board. I guess what I am basically saying is, there’s more than one way to skin a cat, and don’t write off hand tools as a quaint way to experience the past. They worked for thousands of years, and still do! Thanks for the blogs, they make for great reading.
Better add a sliding t- bevel, a protractor, and a compass.
We could have a whole discussion on which hand saws to squire.
Like you, I too am benchless. I built the “Mozilla” Molson vice variant from last year’s issue (I forget which) and it comes in handy for a lot of operations. I clamp it down to a piece of plywood that I have covered with formica (actually, it’s two pieces that I have piano-hinged together for easier storage) laid across two sawhorses. As long as lateral thrust is not involved, this is a pretty stable way to work. I also have a Zyliss vise for working on smaller pieces. I’ve made do for nearly forty years with a radial arm saw and circular saw. I have only recently acquired a planer and router table (both on wheels) It makes the garage croweded because also sharing the space are two motorcycles and about 400 board feet of rough sawn Camphor. I currently attend classes in woodworking and this coming semester I’ll be enrolled in a class for handtools only (and sharpening).
The planes and chisels are somewhat useless without the tools to properly make them shop ready and sharpen them. Therefore, either get a good set of stones or proper grades of sand paper and a flat surface such as a piece of float glass or granite tile.
I’d also add a metal scraper as well, but then a proper metal file is needed to prep the edge. One can always use a screw driver to turn the burr.
A logical next post would be to list the basic shop made tools, such as a shooting board and bench hook. If one uses a table saw or band saw a cross-cut sled is not necessary, but easy to make and is ideal.
Dan, I’m worried about you. The stress must be getting to you. Somehow you’ve lost your ability to count. By my estimation, your list has at least 29 items, some of which are actually “sets” of items, like chisels or crayons, which I only counted as one item. Perhaps you need a break from all that blogging, and time to get back to basics, like counting. I can help. Come over to my shop and we can count things like parts, items on the honey-do list, and for extra credit, screw holes. Don’t worry about making mistakes, I’ll guide you through it, and we can round up if necessary. Ha!
On the subject of a circular saw.
I just moved overseas and had to give up all of my power tools due to space limitations and power incompatibility. Upon arrival the first power tool that I bought was a cordless drill/driver and the second was a circular saw. I then modified the saw to improve its performance for cabinet quality work by putting a zero clearance baseplate (just a piece of 1/4″ plywood screwed to the base) this allows the saw to cut plywood panels without tearing up the edges. I also bought a length of aluminum rectangle tube stock for a straight edge. Together the straight edge and the zero clearance baseplate makes the circular saw a fairly accurate tool for plywood construction projects. It’s not as easy to use as a Festool track saw but it cuts almost as clean and cost about 1/5th the price.
Never did see the charm of tablesaws. Even when I had the space I preferred a bandsaw for almost any job. Better by far for long rips and it won’t try to amputate your fingers or spear you with flying projectiles.
I’m not sold on the need for a power jointer for flattening a surface. That said, I do have a Shopsmith 4″ jointer.. It’s great for jointing edges, and perhaps flattening the occasional rails and stiles, but it of course is inadequate for surfacing wide boards. Would a six inch jointer be better…..not by much. So what do we do? Go to an eight inch, or better yet a ten inch jointer? Now we’re getting into really big, heavy, and electrically hungry machines that are not really suitable for the small shop that is likely to be in a small shed or garage.
I work with a lot of rough sawn boards (Wood Mizer) that are up to 12 inches wide. The worse defect is twist. First I saw the stock to rough project lengths and then using winding sticks, I attack the twist with a #5 hand plane, gradually moving the winding sticks toward the center. If there is bow or cup I can plane that out also. I now have a reference surface that can go thru my planer. The finished boards are perfect. This is not really difficult or excessively time consuming.
Somehow I overlook #1, the jointer and thickness planer, and I saw all the other tools and immediately thought that this was my first set of tools I bought when I started working as a carpenter on a friend’s crew. Then I saw my oversight and just couldn’t get over how incongrous those two items were to the rest of the list. Had I seen a scrub plane and a jack plane I would have more harmony in the list.
I think everyone’s first large power tool should be a table saw, even if it’s just a contractor’s saw. My first was a 12″ radial arm saw 35 years ago, but now I feel it was a mistake and should have been a table saw.
When the body adjusts to the energy and muscle required to use hand planes, happiness and progress is possible.
I am finally getting to practice my woodworking more after years of collecting tools. By using tool reviews and thinking of the kind of work I would like to do, I have accumulated a nice set of tools without purchasing many mistakes. I decided to use Paul Sellers book and videos and start learning from the beginning. He starts with projects that begin with a small set of tools. One of those tools is a spokeshave. Even though I know much of what is in the first lessons, I have picked up a few new tricks, and am learning to use my tools more efficiently. My most important tools are my workbench and vise. The workbench was tough to build as I was on the floor using hand planes; not a good way to work. I have no jointer; did get a small planer and made a sled for it so I can flatten a board. My tools are in my house, so there is no room for a big table saw or bandsaw. I have a chopsaw and a piece of an old Craftsman tablesaw I got for free. It has to be moved outside to use. A circular saw with a guide is handy. My guide has a plate on which the saw is mounted. The plate slides on aluminum angle (with help of rollers) which is screwed to plywood. Once the initial cut is made in the plywood, the plywood is simply lined up with your cut marks and clamped down.
If you can buy a bunch of tools at one time, you can save a ton on shipping, as the more you buy, the lower the rates. Also, take advantage of free shipping offers. Compare to see where you can get the best deal. Whatever you buy, make sure it is high quality. I have a Nicholson backsaw I bought at a local store before I knew of the woodworking suppliers. It has never been used much, but cuts much slower than saws such as Gramercy or Lie-Nielsen, even though mine have smaller teeth than the Nicholson.
Always be on the lookout for usable wood. You might be able to salvage some. You can use a metal detector to find nails and screws. You don’t need a full fledged metal detector. I use a pinpointer made by Garrett. If your wood has some woodboring beetles you can still use it if not eaten too badly. A healthy dose of cyfluthrin will take care of them.
I was talked in to getting a biscuit joiner. Could have done without it.
Got to be able to sharpen. I got a piece of plate glass and sandpaper. A few old oil stones inherited or given to me.
A Zyliss vise has been quite useful. Don’t know why we never hear of them.
A scrub plane can reduce thickness fairly quickly on small stock, like stuff too short for the planer.
While reading the posted comments, it occurred to me that this list is getting to be like the old story of “Stone Soup”, One by one every tool gets added to the basic list.
What tools do we use the most? That would be another interesting topic.
I don’t use my lathe often, but much more frequently than my jointer. The table saw is my workhorse but I really value my planer, band saw, drill press, chop saw, belt/disk sander and brad nailer. But I guess it depends on what you like to make. I’m really eclectic – classic furniture to whirligigs.
Real quick story: Recently, I had to help my brother with some furniture and cabinet issues, but there were a few problems. First he lived 3 hours by car and my wife needed our only car. I’ve had a scooter for a few years, but have only used it for local trips with small needs. Since weather was changing and I needed a break away from my other half, I decided to make the trip. I installed my motorcycle saddlebags to the scooter and loaded the necessary tools for the trip. Where’s the motorcycle? That’s another story. Of course the saddlebags are small and the scooter only had a massive 50cc engine; vrmm, vrmm. Although I have a shop full of electric and traditional hand tools, only the smaller hand tools would make the list for this trip. So, here is the list from that trip: (A few may be missing)
2 small Japanese pull saws, a western push saw, fret saw, set of chisels, bit brace with a roll of arbor bits, rabbet plane, side rabbet (trim) plane, 2 shoulder planes, 3 set of diamond stones, slip stone, multiple files, a rasp or two, 2 small bar clamps, a mini vise, hand scrapers, scratch beader with cutters, combination plane with cutters, smoothing plane, jack plane, block plane, combination square, steel straight rule, 12′ tape measure, small bottle of glue, a few short dowels, 2 marking gauges, and a few different marking instruments (awl, pencils, marking knife).
Now, I know this list only contains traditional hand tools, but my circumstances led me to this choice to complete the job. After all, he is my brother and he’s helped me once or twice. Not all woodworkers will want to take the time and effort to go strictly with hand tools. That’s fine; different circumstances and preferences will lead the way. Most people wouldn’t drive a scooter full of tools to assist their siblings either. Sounds crazy, but I enjoyed the trip through the mountains. Once I was there, I still needed a way to rip through lumber. I also needed a can of finish. As needed, a few jigs and templates were constructed from the purchased lumber.
I was telling my brother of the different ways I sharpen and he seemed interested in the slab/sandpaper method. When I went to get the extra supplies I picked up a slab of granite, adhesive, and sandpaper for sharpening. When the job was completed, the saw, the can of finish, and the slab with sandpaper were gifted to my brother. I could have shortened my list a little,
I consider this my “basic” tool list. Although I do not have a dedicated box for these tools, I assure you that they have a great home in cabinets, on shelves, and laying around on benches. When I do need to take my hand tools somewhere, the larger tools end up in a simple tongue and grooved latch box my grandfather owned. The smaller tools are always in my overall pockets. Overalls work great. They have multiple pockets, they’re comfortable, and they protect your upper body and legs. You only have to deal with small chunks of wood getting into the pockets, which can be dealt with if you or your other half are crafty enough to sew some flaps. It doesn’t bother me though. Thanks for your time.
-LW-
As someone who is just progressing past being a “beginner” (just getting into building furniture) in the woodworking community, I would say there are a number of changes I would make to your list. First, I would say that a power jointer/thicknesser does not belong on the list by any means. They are way too large of an investment and take up a lot of space (not to mention you can buy your stock at the desired dimensions). I also strongly disagree with the concept of joinery devices. As someone new to the trade, I feel this is a very important skill that must be developed, not skipped over by buying devices power devices that achieve a single goal. I think the jigsaw should be replaced by a good bandsaw. I just purchased my first major power tool and it was a 14″ bandsaw and not a tablesaw for space reasons as well as versatility. The bandsaw allows me to resaw, cut curves, (now that it is adjusted for drift) rip pieces of stock accurately that are thicker than a table saw could handle, etc. Once the cut is complete, a handplane can remove any saw marks and square/flatten a surface. It is also really useful for cutting tenons and dovetails. Handsaws can be used for crosscutting and anything else the bandsaw cannot handle. As for a bench, if you are getting into woodworking, this should be your first real project (and it is not expensive to make). You are also missing a good vise to be attached to the bench.
I agree with the rest of what you listed when it comes to hand tools (not powered) as well as a drill and router as these are the tools I have found useful. You are spot on about sharpening supplies and measuring/marking tools, they are very useful.
Lots of good comments! I do think it is a bit of stretch to include a jointer and surface planner on the ‘basics’ list – we’ve got a slippery slope here! And a lot of different approaches – money, space, time, resources, etc. But lets plunge ahead. If you buy your wood already (or mostly) prep’ed, then the jointer & surface planner can be postponed. You definitely need a way to accurately measure linear distances (e.g. length, width) so a good ruler and tape measure. You need to be able to measure squareness – so you need a good combination square. You need to be able to mark the wood – so a good marking knife, an awl, some chalk, a fine pencil, etc. You should have some decent chisels (and good ones don’t need to cost a lot!). You will need to sharpen them (again not expensive – piece of plate glass and some sandpaper). You need a way to accurately cut your wood – a couple of good handsaws and a file or two for sharpening. You really should have a decent work surface/work bench/etc – a good first project by the way. Last of the basics – a good drill (3/8″ vs battery type). Lastly (I could go on but room is lacking), take a look at Paul Seller’s video’s for simple but highly competent work.
I have used a Workmate successfully for years and I am in the process of building an upgraded replacement for the work surfaces. My replacement bench top will be a little longer, much thicker and it will have and extended apron between the two halves to greatly improve holding wood vertically for dovetailing. With this simple upgrade it turns the little Workmate into a very capable portable woodworking bench.
A fine list, to be sure. But a few things of note pertaining to the itemized list above:
1: Table saw in place of a jointer. Any number of tips in previous issues address straightening edges of boards without a jointer. A jointer serves one purpose, but a tablesaw can serve many (just watch your local Craigslist for a decent one to come up.) The thickness planer is unavoidable, but until you can afford one, buy stock in the thickness you need.
3. Router bits- for the cost of two good ones, you can get a pack of decent ones that will get you rolling. These are, after all, router bits (prone to replace) and not shaping cutters. That too will come in time. Oh, and don’t forget a 1/4″ tongue and groove bit.
6. I would recommend one corded drill and one cordless. Generally I outfitted my corded drill with the countersink combo bits and used the cordless to set screws (thanks to the torque collars) and finish by hand tightening.
8. A 5/32″ slot cutting bit for #3 solves the biscuit joint problem. A couple of quick jigs to plunge your pieces and you have a fairly universal biscuit cutting solution. Also a dowling jig (General, Kreg). They are cheap, fairly accurate, and can keep your face frames and glue up panels pretty well aligned.
11. For $150 in 2×4’s and plywood, you can have yourself a nice assembly table. Double up the benchtop with two layers of 3/4″ and some wood glue. Clever cutting will still give you enough for a shelf down below. Top it off with some 3/8″ hardboard and there is nothing you can’t tackle.
11-2. Pipe clamps, I have about 10 of them with varying lengths of black pipe in 1′ increments. I can switch out the clamps for larger lengths on larger projects, or downsize as needed. (very rarely do I need more than 6 clamps on a project during drying time, and when I do, it’s time for a cup of coffee and a 1/2 hour break while I wait) You keep your initial investment down, and buy them as you need them to increase your collection.
I’d like to add some type of sharpening system to your list. A simple sandpaper and slab system, stones, or the more expensive slow grinder system. Although listed, files should be in this sharpening/maintenance category as well. You’ll need these as soon as you purchase a majority of hand tools. They’ll be needed throughout each day of using the tools. Initial setup and routine maintenance will give better results with less fighting the grain and tool. Whether your a beginner or a master, the tools must be sharp and maintained.
Thanks
-LW-
Being new, I’m not sure, but wouldn’t a band saw be one of the basics as a Jig saw blade can flex, thus not leaving a straight edge?
Clamps. I prefer bar clamps. Can’t see anyone getting very far without them. A necessary item in my view.
I personally think a pocket hole jig is a great beginner tool. Especially if you want some just “screw in” joints. Some of the ICDT projects use pocket holes. And if it’s good enough for the authors of those project, it’s good enough for me.
I would add a router table to the list. It’s a very versatile piece of equipment.
Most of it makes sense, but I question the first item.
A planer (and especially a jointer) is nice but not strictly necessary. You can do quite a bit with surfaced lumber (and sheet goods) to start with, and the jointer especially tends to be big and heavy.
I think it depends on the type of woodworker you would like to become. Are you more interested in traditional “electric free” carpentry or are you drawn to the ease and convenience of modern machinery? Also, I think you should take into consideration what kind and how much shop space you have available. I have worked with all the modern machines for years now, and are just presently finding personal satisfaction in traditional woodworking. In fact, last night I built my very first bookcase with just a few “powerless” hand tools. So in all, I would suggest some personal reflection…What type of woodworker do you want to become?…and from there garnish your shop appropriately.
Make a tool box that teaches you fundamental carcase construction techniques.
You can put off a jointer/planer, but I’d hate to see a woodworker quit because they are frustrated, or find rough dimensioning distasteful.
loose the joinery gadgets
A strong/portable light source for both working/rake purposes. Winding sticks might be nice. No clamps?
Just for the record, a jointer and planer are not from the ICDT kit – the philosophy on that column is, indeed, beginner AND basic (hence the Workmate). The tools we suggest in the ICDT manual are for those who are working at a kitchen table or in a backyard; the tools the editors would recommend for someone who is quite sure he or she wants to pursue serious furniture making would be rather different.
I would hardly call a jointer/thickness ‘basic’. Very useful and time saving, but far from basic. Sorry, but it has no place on a ‘basic woodworking tools’ list.
Being without machinery to dimension and dress rough timber myself I can definitely see the benefit, but I think the investment (both in money and space) in machinery like this is premature for ‘basic’ woodworking. Additionally, without some other machinery (table saw, bandsaw) you’re still going to have trouble dimensioning smaller timber for projects from large/rough stock (e.g. producing timber strips for case fronts, ripping to reduce thickness, etc).
I also think that the inclusion of a smoothing plane as a ‘minimum’ for finishing is a bit off the mark. A smoothing plane leaves an amazing finish, but you can still get a good finish with sanding. You are however missing a jack plane from your list. A jack plane is an absolute must for any joinery work.
I consider myself a newb. My experience is that good work holding is crucial to the process. Some sort of beefy (inexpensive) bench has to be in the ‘top 10’ list.
I use my workmate pretty much only to gang cut dovetails on construction grade one-by lumber since building a bench from two reclaimed solid core doors.
Card scrapers are cheaper than random orbit sanders and they don’t make tons of dust or ruin your hearing.