We may receive a commission when you use our affiliate links. However, this does not impact our recommendations.
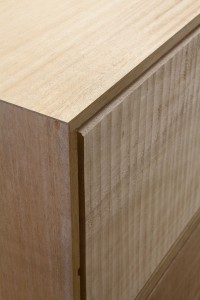
All dovetails: The corners of this chest are all constructed using full-blind or half-blind dovetails.
When I took my first woodworking class in 1993 I was gung-ho to learn two things: through-tenons and through-dovetails.
At the time I was intoxicated by Arts & Crafts furniture and exposed joinery. For many woodworkers, I suspect that exposed joinery sends a message: This piece is made well. It’s not made using corrugated fasteners, hot-melt glue and rubber bands. It’s like buying a fried chicken breast where you can see the bones instead of a chicken nugget, where you cannot see the beaks.
So I spent years perfecting these exposed joints to get them looking seamless right off the saw. I don’t regret those years of effort. But as I’ve gotten older, my tastes have changed. I still love bomb-proof joinery, but I don’t really feel the need to show it off to the world.
To be sure, some people are going to look at my furniture and assume it’s more like a chicken nugget than the real bird, but I can live with that.
So what do I focus on these days? In no particular order: form, crispness of detail, the fit of the movable components, the surface finish and (this is huge) the grain. Oh, and the hardware, but you knew that.
This week I finished up building the two carcases for this Campaign Secretary I’m building for Popular Woodworking Magazine. These cases are chock-full of dovetails, but when the whole thing is together it just looks like two boxes with a couple rabbets.
I love it.
What I see when I look at the carcase is not the lack of joinery. Instead, I see the fact that the grain is a continuous flow from the bottom edge of one end, across the top and down to the other bottom edge.
I also like the back of this piece. It’s not flashy, but I had to use a fore plane to dress everything flat and I left the traverse marks left by the curved iron, what Joe Moxon called “dawks” in his 1678 book. That texture, even though it will be hidden, says “handmade” to me now.
Of course, after I finish this chest, my next Campaign-style case piece is going to smash all my above sentiments. Think: riveting the wood.
— Christopher Schwarz
But if you struggle with dovetails….
Check out Chuck Bender’s DVD “Dovetailing Apprenticeship” – an excellent way to learn from a real master of the joint. If you want to try a bunch of different hand-cut joints, Ron Herman’s “Joinery Challenge” DVD introduces you to nine essential joints. If you like books better, hunt down a copy of Charles Hayward’s “Woodwork Joints.” It’s the standard.
Here are some supplies and tools we find essential in our everyday work around the shop. We may receive a commission from sales referred by our links; however, we have carefully selected these products for their usefulness and quality.
Hey Chris, where did the woodworker-chicken idea come from? ;-))
Cheers man, Erik.
Why, Chris! That carcass looks positively European with such clean lines! I love the minimalism. Is that a word?
Good article, as usual, Chris.
Glad your latest taste is for hiden joinery. I studied woodworking, in the 60’s and the emphasis was on blind joinery. Full-Blind dovetails on carcasses and half-blind in drowers. The teaching was of 4 years, 2 years, using only hand tools 2 years using machines and hand tools.
Using only hand-tools the full blind dovetail is one of the most dificult joint. Special care is to be taken on the 45 deg lip, and when sawing the dovetails one has to be carefull not to nick the lip with the saw, but when it is well done, it gives a special sense of accomplishment.
But now, I also like the looks of exposed jonery.
I’ve also been experimenting with hidden joinery for cases.
I first tried the hidden dovetail which worked nicely but still left the stepped corner and exposed end grain along the joint.
I then did a case with the hidden dovetail and with the edge and corner mitered so the joint looked like a simple miter.
I also did another case with a fully hidden finger joint with mitered corner and edge. Same mitered corner look with a finger joint buried inside.
With both cases, I cut the sides and top from a single glued up panel so the grain and joints matched up.
If someone has a copy of Moxon’s 1678 book, they might want to update the Wikipedia entry for “Joseph Moxon”. A number of his other books are listed, but not that one. In addition, there’s no mention of his being a woodworker, although it mentions that he made maps, globes, and mathematical instruments.
I suppose that being the first tradesman elected as a Fellow of the Royal Society trumps woodworking. This really is a big deal: his contemporaries in the Royal Society included Isaac Newton, John Locke, and Christopher Wren. Not bad company for a “tradesman”.
There is a story (which may not be true of course, given the media’s love of Royal gossip), that Viscount Linley (son of the late Princess Margaret, sister of our Queen) who is a well respected cabinet maker, when a young man, showed his Grandmother (Queen Elizabeth the Queen Mother) a box made with hidden dovetails.
This was no doubt an exquisitely wrought piece. He apparently told his grandmother all about the technique required to hide all the evidence of joints. The Queen Mother (who was in her eighties, at least) then asked why he had gone to all this trouble to produce a box without any evidence of the skill required to produce it.
There is really no moral to this tale, except to enjoy your own achievements.
By the way, the chest looks fantastic, and I await developments. I love campaign furniture.
The cases look great! I really like the “scalloped” look of the back, that could look pretty nice on a frame and panel door, on the floating panel.
Chicken nugget description deserves a Pulitzer.
“That texture, even though it will be hidden, says ‘handmade’ to me now.”
I have a rather different take on that: That texture, to me, says, “production work.” That is, the texture is there because the cabinetmaker was trying to make a living, and couldn’t afford to take the time to include details that most people wouldn’t ever see. Such marks are the 17th- and 18th-century equivalents of the regularly-spaced planer marks that modern-day woodworkers can see on machine-produced surfaces that haven’t been cleaned up (and that most other people don’t notice).
Since I work wood for my own enjoyment, and am not under any time pressures (unless you include my wife wondering if I’m ever going to finish the doors on those bathroom cabinets…), I have the luxury of taking the time to work on those mostly-but-not-entirely-unseen details, and so I do.
That, to me, is what really says, “handmade.”
-Steve
Reminds me of Japanese small tansu joinery.
http://youtu.be/U98YYBeG7NI
I’m right with you Chris, though not nearly as skilled. I plan on building a matched pair of nightstands in flame birch, using carcass construction instead of leg & apron so that I can get grain wrap up one side, across the top and down the other side. After your last few posts I’ve decided to go the secret mitered dovetail route. Why fear the joint, just learn it and cut it, right?
I built a shoe rack recently:
http://www.forums.woodnet.net/ubbthreads/showthreaded.php?Cat=&Number=5742281&page=&view=&sb=5&o=&vc=1
I used 1/2″ BB plywood. joined the top to the sides with box joints. Then veneered the whole box (and front edges) with shop-sawn veneer. No joints exposed.
Joe?
Back in the day when these things were made to withstand extremes of climate, were blind dovetails used so as not to expose end grain, rather than for aesthetic reasons?
Nice touch with the dawks.
I guess the mitered full-blind is not period correct? You’d look really lazy if you executed that, though.