We may receive a commission when you use our affiliate links. However, this does not impact our recommendations.
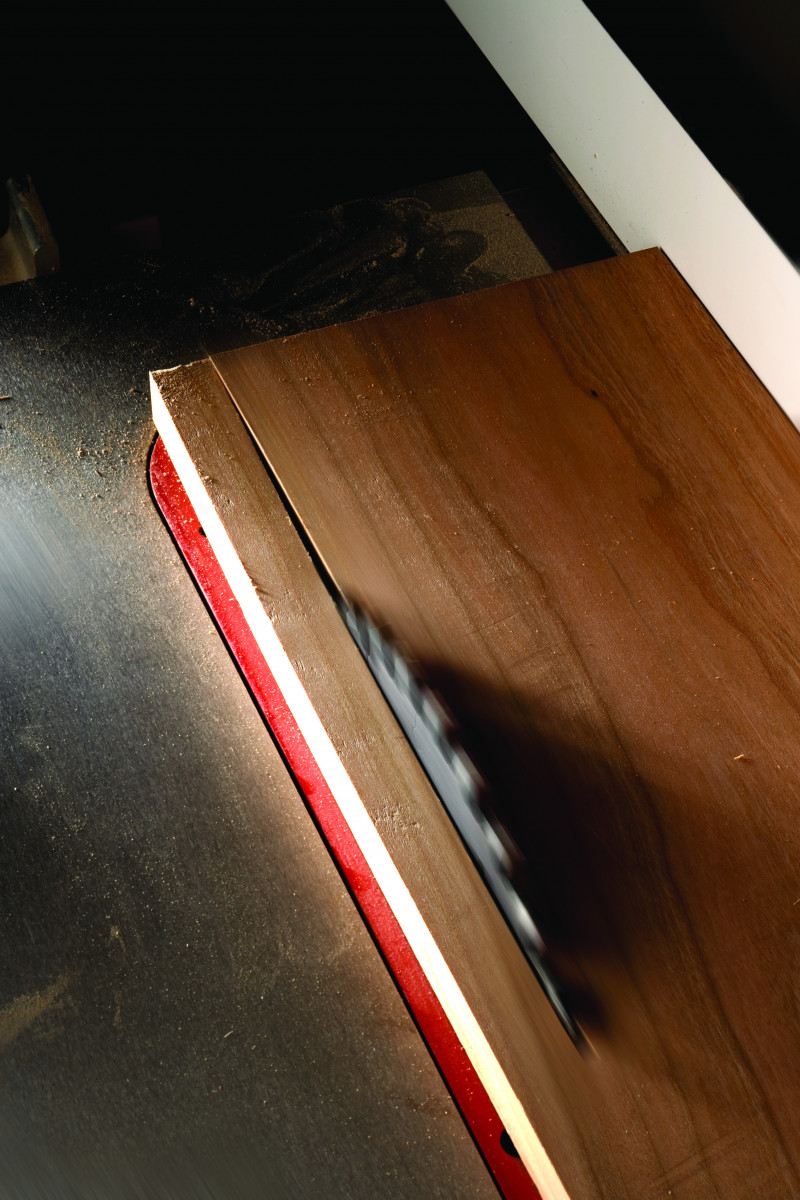
Danger ahead. Without the proper safety gear and procedures, you are vulnerable to kickback at your table saw.
The fundamental rules (and devices) to keep you clear of danger at your saw.
I once heard that 90 percent (or more) of all table saw accidents involve some type of kickback, where the work flies back at the operator. Imagine what would happen to table saw accident statistics if we could eliminate kickback altogether. The table saw would go from being one of the most dangerous machines to one of the safest.
I often ask for a show of hands during my safety demonstrations of how many people have ever experienced kickback. Nearly everyone sheepishly raises their hand. I then ask how many people have experienced kickback more than once, and it’s almost the same response.
Why is that?
It’s clear that accidents occur to both the novice and experienced woodworker, but why would something as potentially dangerous as a piece of stock being kicked back at more than 100 miles per hour be an experience anyone would ever want to have more than once?
Kickback can be a product of both through and non-through cuts. Once it starts you can’t stop it, and only Superman can react faster. The kickback zone can actually be anywhere in the shop. That’s right – anywhere! The main (and most dangerous) line is toward the operator and directly in front of the blade. However a “kicked” item can ricochet off something and head in any direction, and boards with some significant width that kick back can pivot sideways as well.
I believe that most woodworkers don’t understand the cause and cure of kickback, so let’s take a look at both.
The Mechanics of Kickback
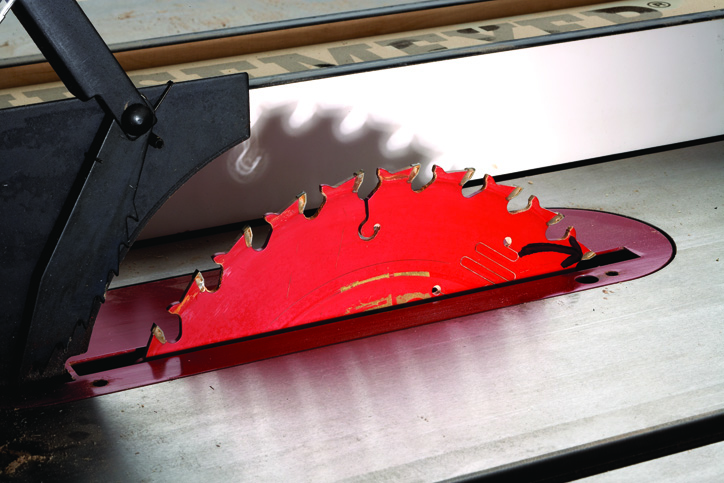
Up, forward and down again. If you follow the marked tooth in the series of photos above, you can see how initially the tooth lifts the work up. Then it pushes it forward. And finally it pushes it down.
Kickback occurs when a piece of wood is unexpectedly thrown back toward the operator. The lifting and throwing force of kickback starts at the back of the blade, not the front.
To get a better understanding of how this force is created, unplug your saw and mark any tooth with a felt-tip marker. Now rotate that tooth to where it just starts to rise above the table at the back of your saw’s throat plate.
If you follow this one tooth as it rotates it will give you a better idea how a piece of wood is lifted and thrown forward. When the blade rises through the table at the back of the saw it has an initial vertical lift. As the blade continues to rotate and reaches the top of its arc, the vertical lift begins to transform into a horizontal thrust. By the time the blade moves from the top of the arc back down toward the saw’s table, the horizontal thrust transitions back to vertical. By now all the force is moving down towards the table on its way to doing it all over again.
To help students understand how much lift a rotating blade has, I move them over to the 20″ disc sander (unplugged, of course). As the sandpaper disc rotates, you can safely sand wood on the side that is rotating down toward the table. But move the wood to the lifting side and the piece is immediately lifted up. A table saw blade works in a similar fashion.
The Causes of Kickback
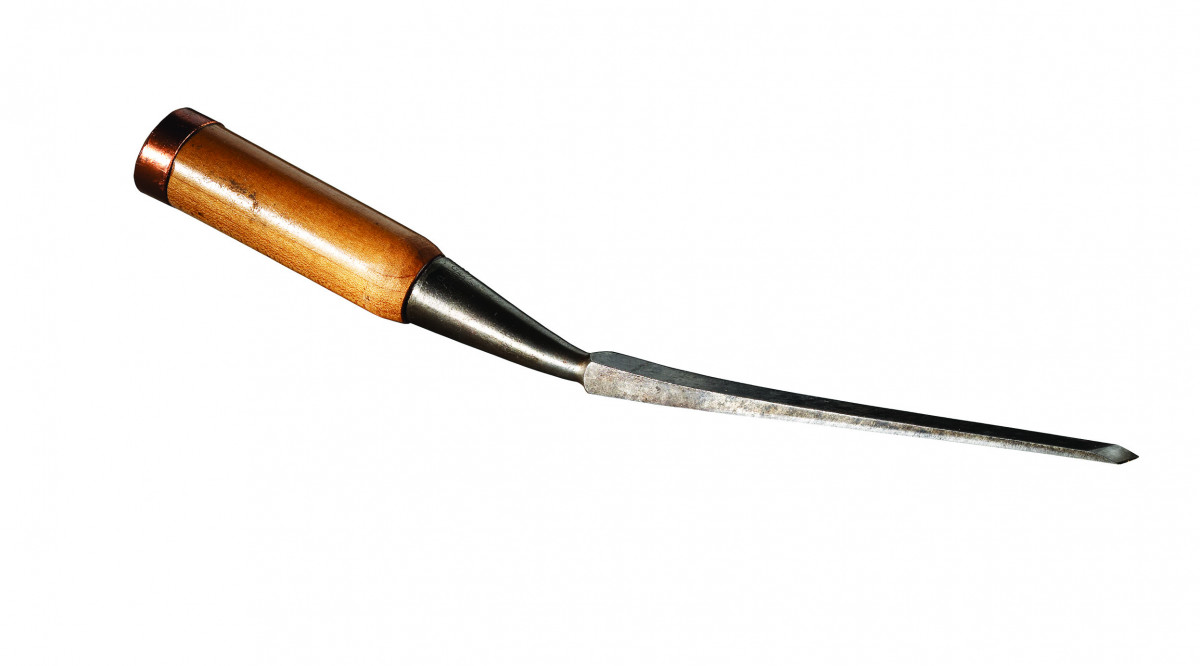
The power of kickback. One of the magazine’s former editors experienced a kickback on the table saw that resulted in the board flying back and striking a bench chisel, bending it.
OK, so we know that kickback occurs at the back of the blade, but what are the series of events that can cause the stock to contact the back of the blade?
By far the most common cause is binding or pinching. This happens when a piece of wood becomes trapped between the rotating blade and a stationary object, such as the fence or the guard. The following is a list of reasons that stock can kick back:
1. Crosscutting a piece of wood with the miter gauge on the left side of the blade while the fence is being used as a stop on the right-hand side of the blade – blam-o!
2. In some cases kickback is created if the saw kerf closes around the blade.
3. Make sure the fence is parallel to the blade. If the fence is toed inward toward the blade, it can cause the wood to come in contact with the back edge of the blade.
4. Cutting twisted, distorted, knotty, crooked or springy wood.
5. Freehand cutting or cutting wood that is not flat on the table, such as round stock.
6. Losing control of the work or letting go of the wood at the same time it’s in contact with the saw blade.
7. Not following through when ripping, or stopping before the cut is complete.
8. Intentionally or unintentionally allowing the wood to “drop” on top or to the side of the back of the blade.
9. Backing out of a cut.
10. Improper setup of the machine’s guards, fixtures or hold-downs.
11. Applying the entire pushing force toward the off-fall or free section of the work instead of pushing toward the fence.
The Cures for Kickback
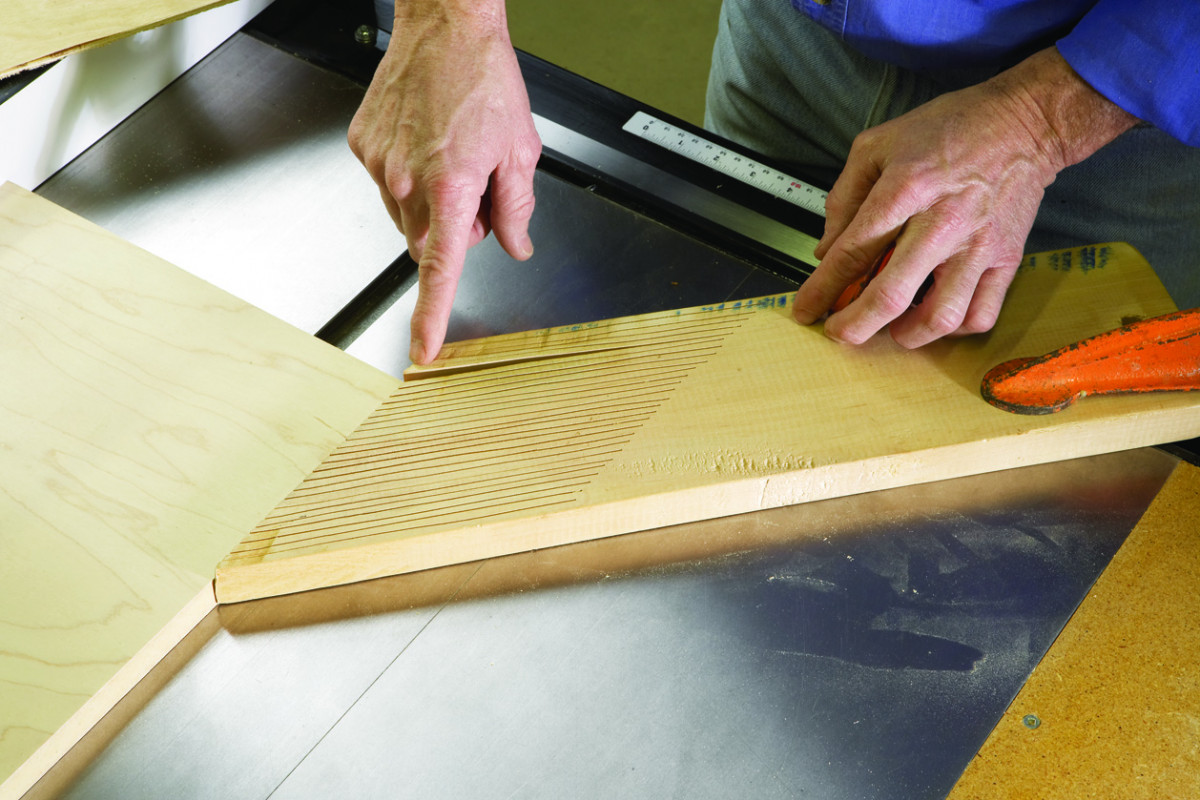
A proper featherboard. The fingers of a featherboard are consistent in size and springy, as shown. You can clamp them to the table or to the fence to help improve the safety of many operations.
Use the guard. The best cure for kickback is to deny the wood access to the back of the blade. A splitter, especially a riving knife, is by far the best protection you can give yourself.
Double-check all your setups and plan your cuts carefully. Be aware of all the pinch points or bindings that could be created during any cut and plan your work first. And although this isn’t a cure for kickback, there are blades that have anti-kickback fingers behind the teeth that limit the chip or depth of cut. These blades are sometimes sold as anti-kickback blades, but they do not eliminate kickback.
Now let’s look at two important devices that can help you avoid injury, but only if you use them properly.
Featherboards and Push Sticks
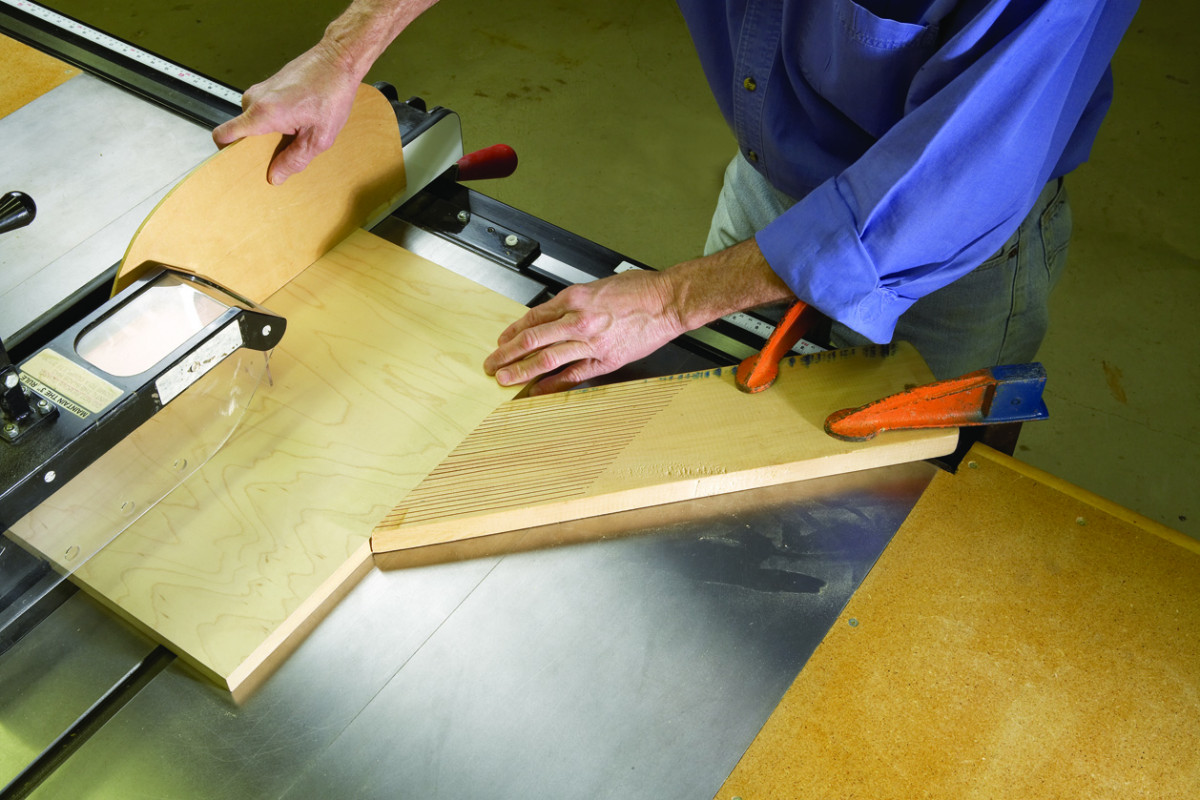
Better together. Here a push stick is used with a featherboard. The push stick keeps the work flat on the table and moving forward. The featherboard, located in front of the blade, presses the work against the fence.
Dr. Jeffery Greenburg, a brilliant hand surgeon and pretty fair woodworker, told me that he has never treated a patient whose injury occurred because of a push stick or any other safety device. As a matter of fact, a common reason accidents occur is from not using a safety device. Push sticks and featherboards are easy to make, inexpensive, can be made to any size and are expendable.
There are a lot of articles, drawings and details written on how to make elaborate push sticks and featherboards, but most professionals make the simpler types for two reasons: They are easy and quick to make, and when they get cut and nicked you don’t feel so bad. They are the ultimate sacrificial tool.
Featherboards Not a Cure-all
Featherboards, spring boards, combs, anti-kickback fingers, spreaders and magnetic hold-downs all hold the work down or against an edge, and they act like a spring. A featherboard is a piece of solid stock with multiple kerfs that are equally spaced along the grain. The end of the piece is cut at a 30° to 45° angle. Featherboards can help minimize kickback, but they do not eliminate it, as some commercial featherboard manufacturers suggest.
Featherboards are designed, for the most part, to be clamped to the table or fence. Clamping them to the fence is usually not a problem. But clamping to the table can be a challenge. To get around this, some commercial featherboards have either built-in expansion bars that fit in the miter gauge’s slot or heavy-duty magnets. If you use shop clamps to secure your featherboards, use two clamps to prevent the device from pivoting.
If a simple clamping solution is not readily available, try placing high-strength, fiber-woven carpet tape on the down side of the featherboard. This will hold it to the table but will not quite give the “stay-put” holding power that you can get with a clamp.
Featherboards that are clamped to the fence help keep the wood flat against the table and provide some kicking resistance. They can be placed anywhere along the fence where a downward force is needed. Be aware that fence-mounted featherboards can sometimes be restrictive. Table-mounted featherboards provide force toward the fence and offer some kicking resistance. It is vital that a table-mounted featherboard never be placed beyond the front edge of the blade. If mounted behind the blade, the force will push the wood into the back of the blade.
The Proper Use of Push Sticks
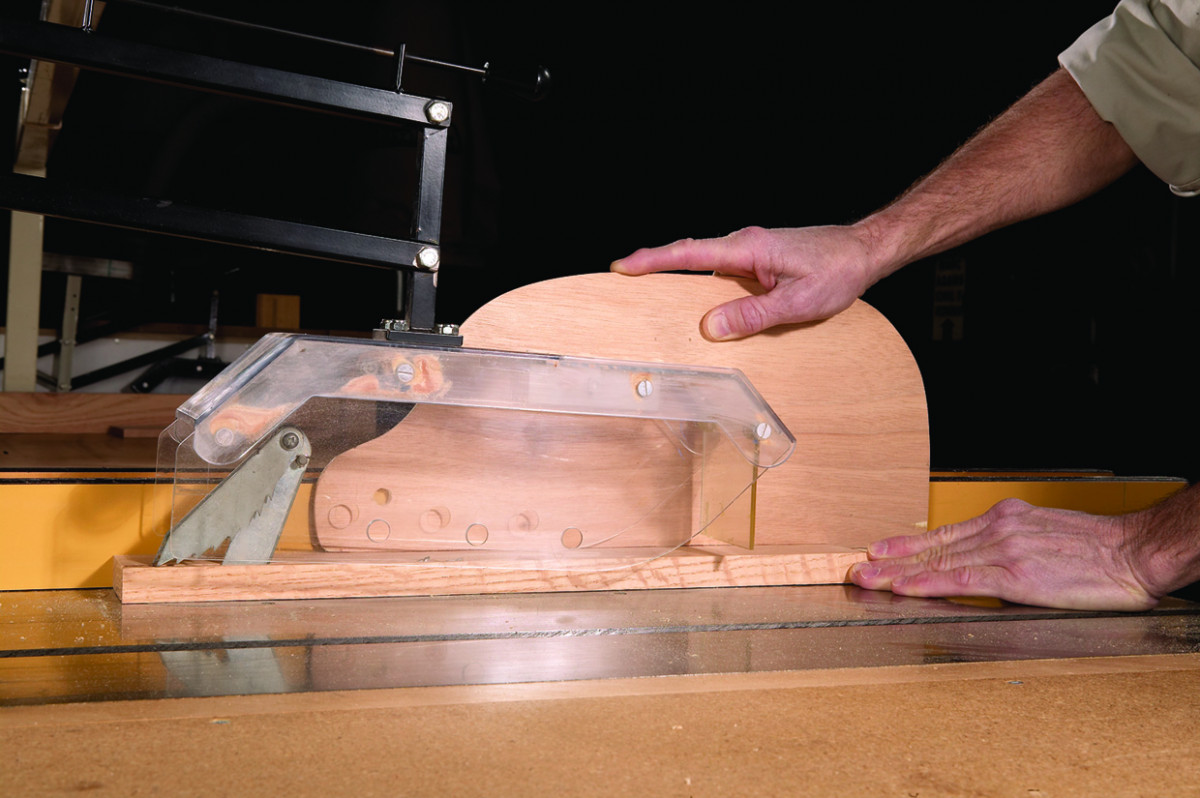
A good push stick. Here’s one of my frequently used push sticks. It hooks over the back of the work and presses the work flat against the table.
Push sticks are used to help push the stock through the cut while keeping your fingers clear of the blade. A good push stick can help hold the work against the table while pushing forward at the same time.
They are an absolute must when cutting narrow or thin stock. Push sticks come in all shapes and sizes, and it’s a good idea to have several different types and thicknesses ready to go. In most cases the width of the push stick should be less than the distance between the saw and the fence.
I prefer to use a push stick that both hooks on the back edge and sits on the top of the board. This type of push stick gives me more control and helps keep the stock from tipping up while moving past the blade.
It is important to understand when, and when not, to use a push stick. As long as you have your hands on a board when making a cut, you will always have a great degree of control. As soon as you use a push stick, you lose a portion of that control.
I always recommend that you use your hands for pushing your work when you have more than a 3″ clearance from the guard – you simply have more control. If your hands will be within 3″ of the guard, however, then a push stick is definitely necessary.
Be aware that you will lose some control. As a matter of fact, if you use a push stick with a downward force on a board that is off the table, it could cause the board to tip upward. Push sticks just aren’t effective or necessary at the beginning of a cut on a long board.
I keep my push stick handy and when my push hand gets to that 3″ limit, with my left hand holding the board firm, I use my right hand to pick up the push stick and finish the cut. I also keep a second push stick to the left of the table so that my left hand has access to a push stick as well. Be aware that sometimes push sticks can slip off the stock and cause a very dangerous situation. Always keep your push stick hooked firmly over the edge or side of the board.
Here are some supplies and tools we find essential in our everyday work around the shop. We may receive a commission from sales referred by our links; however, we have carefully selected these products for their usefulness and quality.