We may receive a commission when you use our affiliate links. However, this does not impact our recommendations.
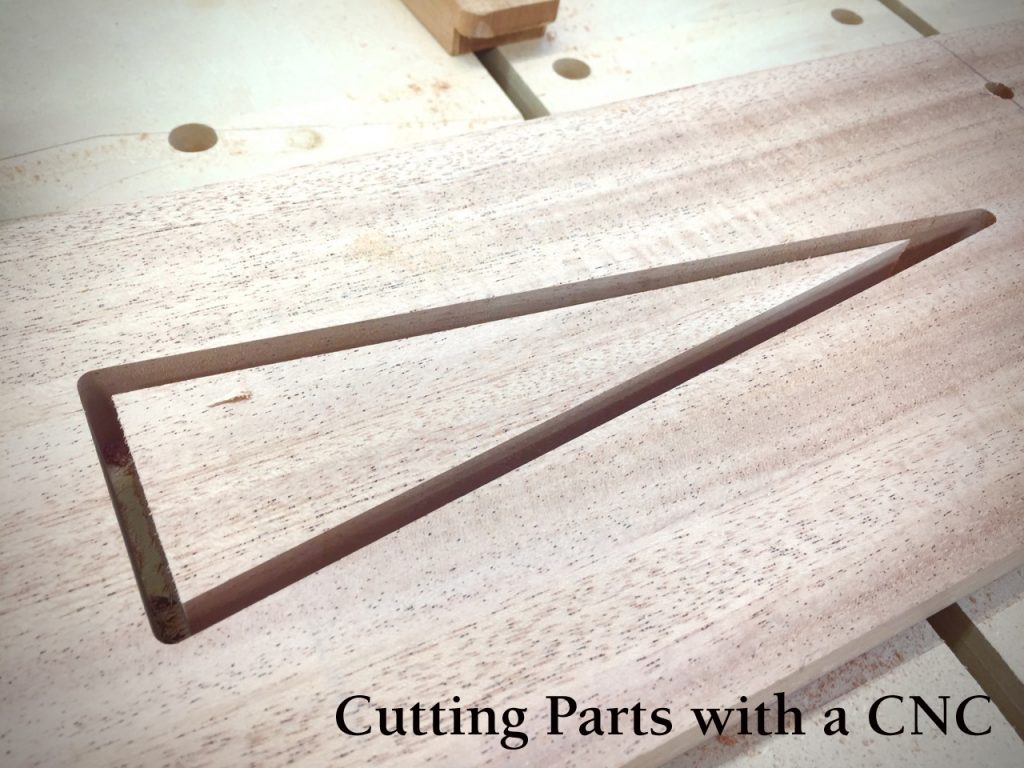
Cutting a narrow triangle-shaped opening with power and/or hand tools is anything but simple. Cutting parts with precise details is a task well suited for digital woodworking and CNCs.
How I use a CNC: Part Two
In the previous post, I gave an overall explanation of the process that I use to make furniture parts with a combination of various power tools and hand tools. Essentially, it’s a hybrid process of power and hand tools that many other professional and hobbyist woodworkers use. The goal is consistency and accuracy. I mill and square up materials with jointers, planers and saws. Then, I rough cut and final shape parts to my patterns.
Stock Preparation
So, how does the process change when you use a CNC to cut out your parts? For me at least, some things are the same. I still prepare my stock with the same tools as before with saws, jointers and planers. Getting your boards flat and square is even more critical when using a CNC. You want the boards you’re going to CNC very flat. From this point on, everything changes.
Below is a simple example of the CNC doing what it does well: accurate part cutting. In this example, we’re not cutting out a complete part, just a shape in the middle of a board. A long, thin triangle. As simple as it looks, I’ve had to make this exact cut many times. It’s been difficult with any combination of power tools and hand tools. The red triangle in the drawing below shows you the area I need to remove.
A Challenging Cut for Woodworkers
Here’s the problem: The triangle is very narrow. It’s about 2-1/2” wide at the top and tapers down over 9” to a sharp point. It might seem simple but in practice it’s been a difficult detail to cut out accurately. I’ve tried all the woodworking processes that you’d expect. The most successful technique has been to drill holes in the corners, then jig saw or scroll saw out the triangle. So far, I’ve been unhappy with the results. Even holding a jigsaw to a guide, the walls of the triangle are not perfectly straight and smooth. So, after rough cutting, I set up a two-step shaping process with the pattern to get the walls straight. But, we’re just getting started. The sharp end of the triangle keeps it challenging. Time for rasps, files and lots of sanding in a difficult-to-access area before the job is done. After a lot of time-consuming work, I’ve never been completely happy with the quality of the results. This job is all about precision. That makes it a perfect task for a CNC.
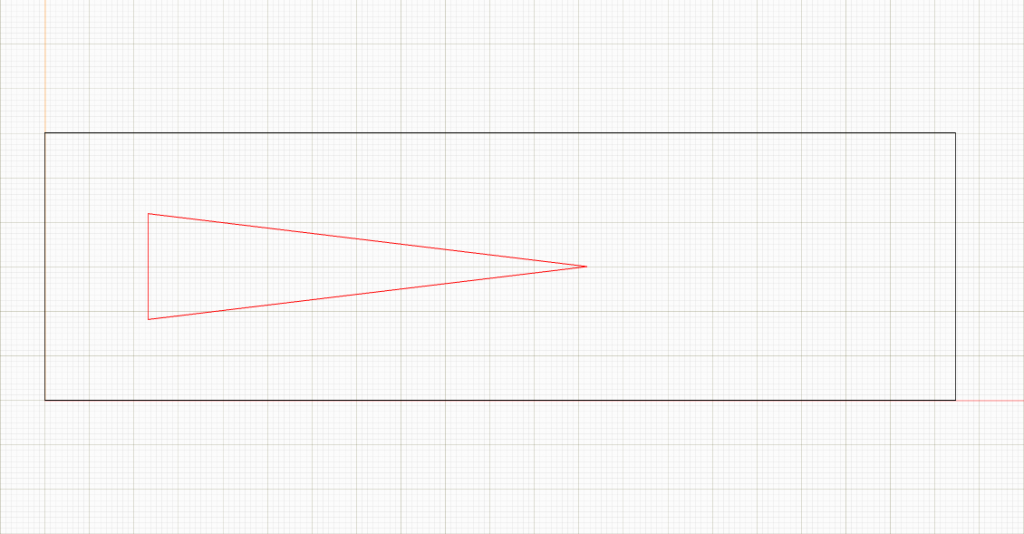
The red area in this CAD drawing is a narrow triangle that I want to be cut out of the board.
First Draw the Part, Then Cut It
After drawing the board and the triangle in CAD and then programming the CNC with CAM software to make the cut, I place the board on the bed of the CNC, align it, clamp it tightly and begin. I cut my way down in steps to the full 1” depth of the board just as you’d do with a router. Small connecting pieces of wood at the bottom of the cut called “tabs” or “bridges” are left to keep the triangle just slightly attached to the main board. That keeps it from rattling around during the last pass and potentially damaging the part.
You can see the tabs being machined in the video below when the CNC pauses, rises up and then drops down. Total time to cut the triangle opening: 116 seconds. The results are perfect. When you add in the time for changing boards and clean up, eight boards were completed in 20 minutes.
Sometimes a small detail is a big challenge. Cutting this narrow triangle out of a board is particularly difficult using other woodworking techniques. With a CNC it’s done quickly and accurately.
Though this triangle is only a simple example, it should give you an idea of how accurately and quickly a CNC router can machine parts. If we were cutting a complete part with any combination of curves or shape, there’s a bit more involved but in general, the process is pretty much the same.
As I said previously, a CNC can do many things. Certainly, it does some tasks better than others. And, as always, some tasks are better left to hand or power tools. Accurate part cutting just happens to be one woodworking task a CNC does very well.
Here are some supplies and tools we find essential in our everyday work around the shop. We may receive a commission from sales referred by our links; however, we have carefully selected these products for their usefulness and quality.
We had a CNC vendor give a talk to our group on this subject. We tend to machine very small and precise elements. We learned that inside cut outs of rectilinear nature will have rounded corners that are the radius of the cutting tool. These have to be hand worked. In addition for sharp cuts such as the triangle one could run past the end point of the wood (say the hypotenuse) and do the same on the converging cut (say the adjacent side) creating the sharp end of the triangle and eliminating any round overs. Does that make sense?
I can see where the CNC router helps with cranking out parts by performing the bulk of the work. However, you still have the 3 corners to work by hand if you want them to be sharp points. did you try a router and templates for cutting out the part? Also, the CNC shown looks more advanced than most of the hobbyist ones on the market. How much did it cost, and what is its capacity?
I’m enjoying Tim’s blog postings about CNC stuff, incorporating CNC into a woodworking shop, whether pro or hobbyist. I am dabbling and learning using 2nd hand Rockler stuff. I am still a 90+ % hybrid woodworker using a mixture of hand and power tools, with a trend toward more hand tools, but I see many possibilities for CNC in a workshop, for carving, sign making, template production, etc. I know some craftsmen using CNC in fine guitar production, especially electrics, but also acoustics, and I don’t mean factories.
I’m sure you will receive some negative feedback about using CNC, but I see no reason for not supporting the use of CNC for the woodworker who can become facile with the methods and software and employ this technology in efficient and unique ways.
Hi Tim
Can a CNC machine make the wedges for Hollow and round planes?
Tks