We may receive a commission when you use our affiliate links. However, this does not impact our recommendations.
Learning about CNCs at the Marc Adam’s School of Woodworking
Furniture manufacturers and large cabinets shops have been using digital tools and CNCs for decades. But, for hobbyists and small to medium shops, digital woodworking is just now getting started. Being a new kind of woodworking, it’s certainly different. That means there are new things to learn.
A few weeks ago, I taught two classes at the Marc Adams School of Woodworking. One, a weekend intro, the other, a 5-day hands-on furniture project. For the class, I designed a hall table. To give the student’s a choice, I designed 6 tables based on the same architecture. Here’s a peek at the designs, below…
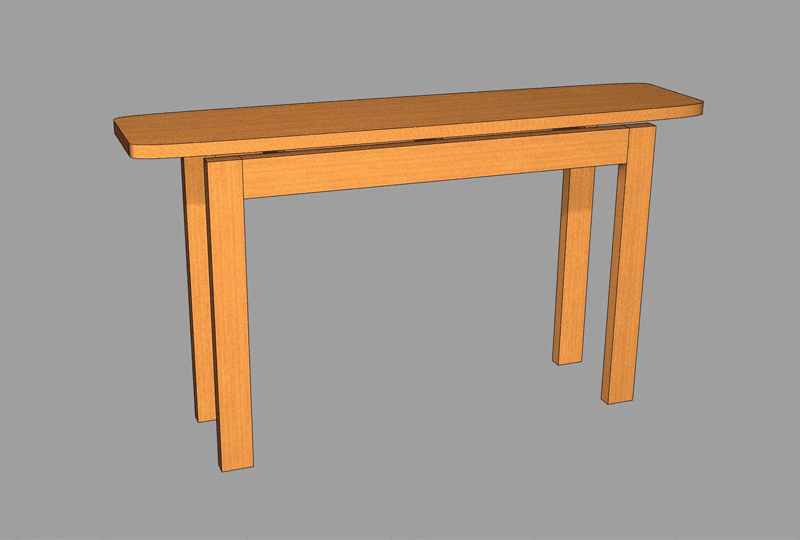
Six variations on one theme. CAD software opens up many possibilities for refining the design.
Anyone who has taught will tell you, it is hard work. Fortunately, it’s always fun and you meet the nicest people in the classroom. Many are eager to learn and enthusiastic. Woodworkers are fun to work with. These classes were no exception.
The weekend class got an introduction and a peek at the world of digital woodworking. We talked about CNC machines, software and the skills needed. We made a few things, including the chair pictured below. It was quickly made out of a 1/2 sheet of plywood. What makes this chair a little different is that there is no joinery at all. It’s held together with plastic zip ties. The surprise to everyone who tries it out is that it really works. It’s certainly not a replacement for real joinery techniques and solid wood, but it sure is fun to make.
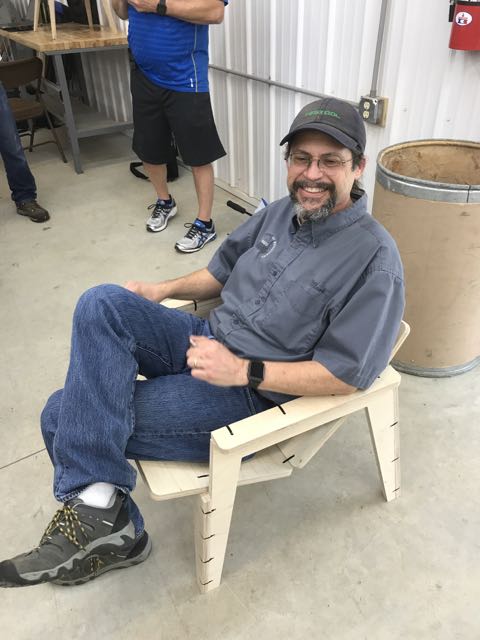
Mark Sterner trying out a zip tie chair with a flexible back. The staff at the Marc Adams school make a teacher’s job and the student experience delightful. Mark is my partner in crime at the school when it comes to all things digital.
If you have a CNC and want to make one of these chairs, Will Holman’s terrific plan and digital files for this chair are available Here’s a link.
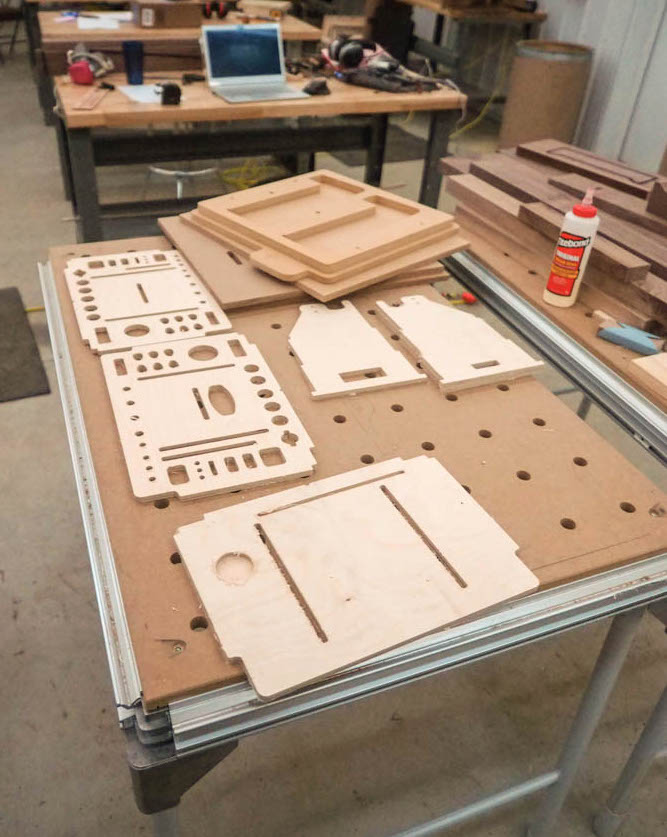
Parts for the CNC tool box Systainer insert that I designed for the weekend class students. Photo courtesy Ashley McCorkle
In the 5-day, hands-on class, students built one of the table designs mentioned above. I’ve said it before, CAD software and design are really the most powerful tools in digital woodworking. To get a taste, I invited a few more advanced students to use my designs as a starting point to personalize their tables. For example, student Tim Cooper took my contemporary surfboard table top a step further by laminating together cherry and walnut for his 60’s rendition. Surfs up, dude!
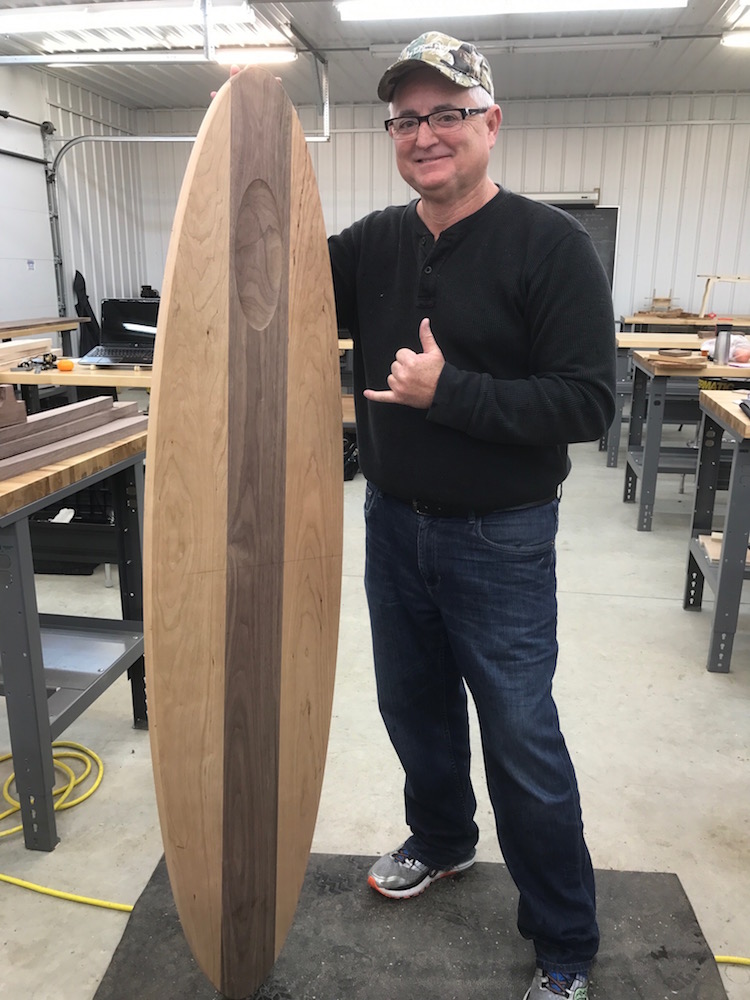
Using a CNC, Tim Cooper striking a pose with his surfboard hall table top at the Marc Adam’s School of Woodworking.
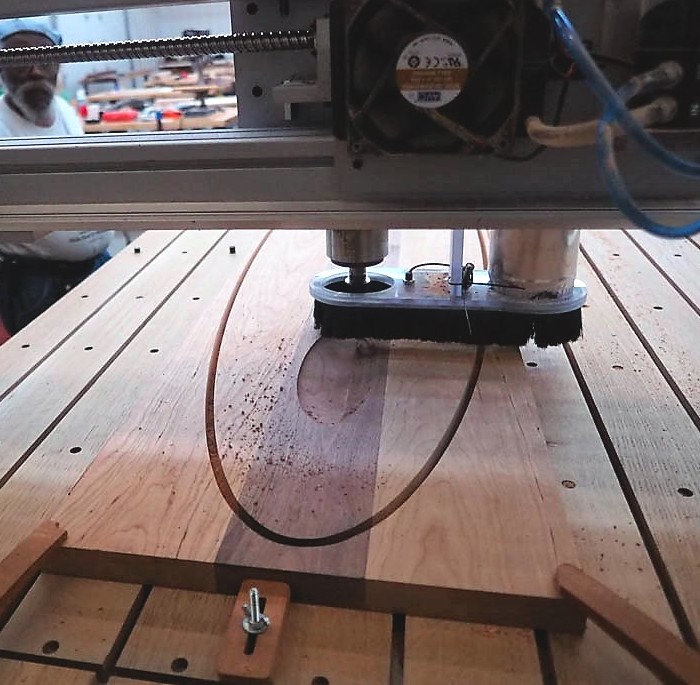
Carving an oval dish into the surfboard table. Photo courtesy Ashley McCorkle
Carving 3D Table Legs
Bjorn Rettig took his design into the world of 3D. With experience in both RhinoCAD and RhinoCAM, he took a more advanced approach to his table. In the photo below, you can see his table legs being carved with a tapering cove and a progressive, rounded surface.
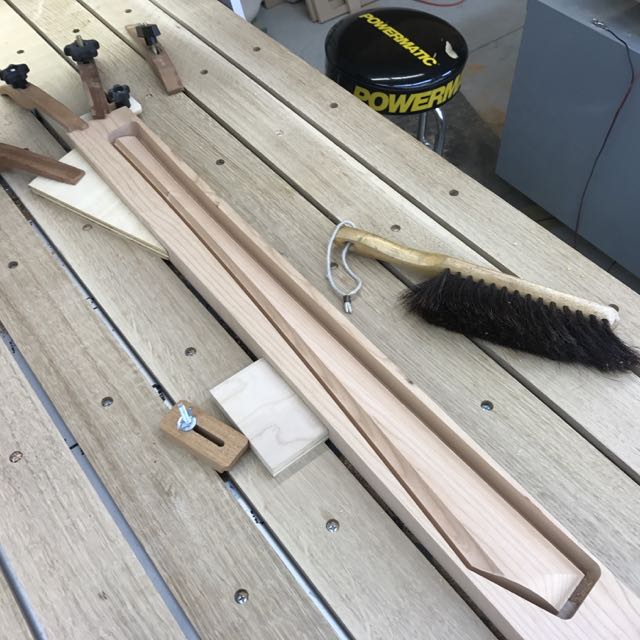
Taking a table leg a little farther into the world of 3D carving. Bjorn Rettig designed his table leg with a progressive round over and a tapered cove cut.
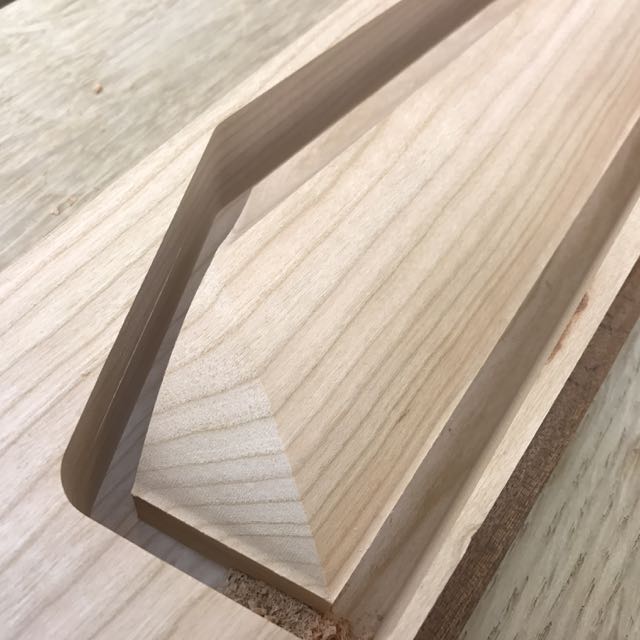
The top of the leg connects a corner to detail a soon to be milled table apron.
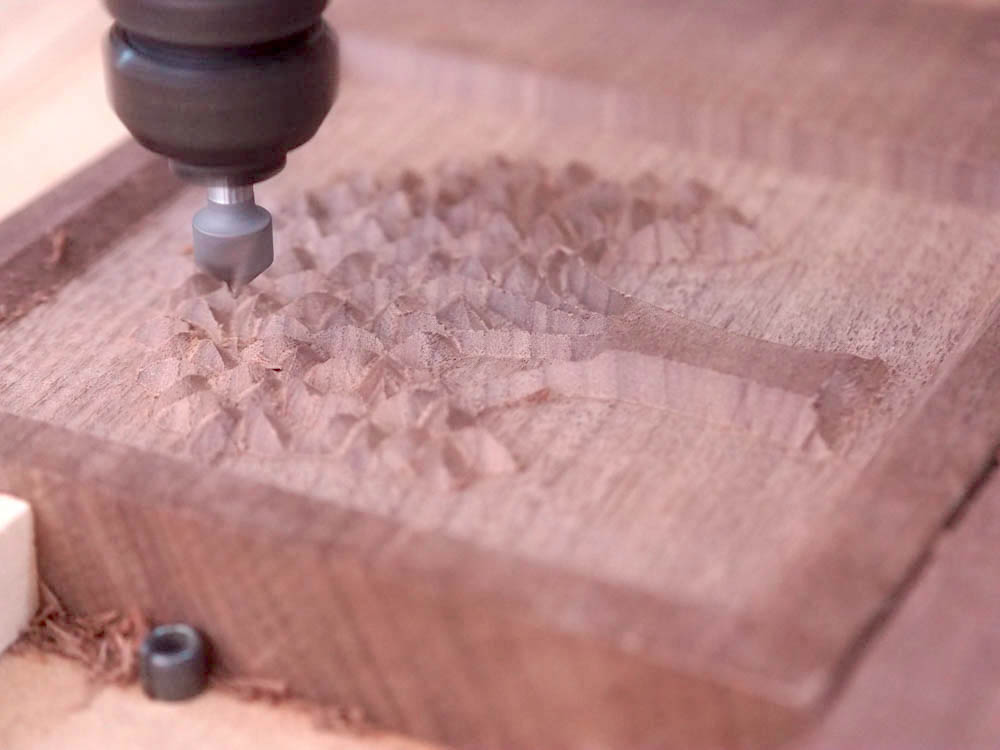
Using a VCarve technique to create a walnut inlay of the Tree of Life. Photo courtesy Ashley McCorkle
The following are three things that I emphasize in every class. This kind of woodworking may involve digital tools but, it is still woodworking. Wood being wood means there’s always special issues to deal with. Woodworking knowledge, skills, and experience really help. Second, if you want to get really good at this you need to get comfortable at creating drawings in CAD. Finally, don’t rely on your design instincts. Good design sense rarely comes naturally. Good news: design is a skill and therefore, learnable. Kinda like learning to play a musical instrument. Knowledge, exercise, and practice will take you most of the way. Work hard to become a good designer. It’s the secret sauce that makes anything you create better and unique.
I’ll be back at the school in October with a CNC woodworking skills and techniques class for those more familiar with the tools. Think of it as a beyond-the-basics hand tool skills class for woodworkers who plan on adding digital tools and skills to their shop and want to use them regularly in their projects and work. A lot of emphases will be on moving beyond 2D based designs and into the world of 3D. The idea is to put a little shape into your work. And, just for fun, there’s a weekend class where we’ll make all kinds of holiday gifts using CNCs, laser cutters, and all the other woodworking tools in the shop —digital woodworking experience is not a requirement.
Here are some supplies and tools we find essential in our everyday work around the shop. We may receive a commission from sales referred by our links; however, we have carefully selected these products for their usefulness and quality.