We may receive a commission when you use our affiliate links. However, this does not impact our recommendations.
Have you seen all the new CNC machines available to hobbyists these days? Everybody who sells woodworking tools seems to carry at least one model. Maybe you’ve been thinking about buying one. If you’re computer savvy, you could have a lot of fun with a CNC router. On the other hand, you might be hesitant to spend upwards of $2000 for this technology.
Adding CNC to your shop doesn’t have to cost a small fortune; you can build a sturdy and accurate three-axis CNC router for about $1000, and that price tag will get you most of the features you’ll find in commercial models selling for $3000-$4000.
You’ll need some kind of sheet material to make the machine’s body, and that can be MDF, plywood, UHMW or HDPE plastic, aluminum or steel. I recommend using something that’s at least ¾” thick so that you end up with a rigid frame. To stay within the $1000 budget, choose MDF. It’s flat, easy to work with and inexpensive.
Each axis will require a combination of guide rails and bearings for motion. There are plenty of choices for these components, but aluminum rod is an easy option and won’t cost as much as most of the others. Just make sure the rod diameter is large enough that the shafts won’t sag. You can also drill and tap holes in the shafts and mount them to the machine’s frame. You’ll have to cut notches in the bearings, or buy bearings that are made for this type of mounted shaft.
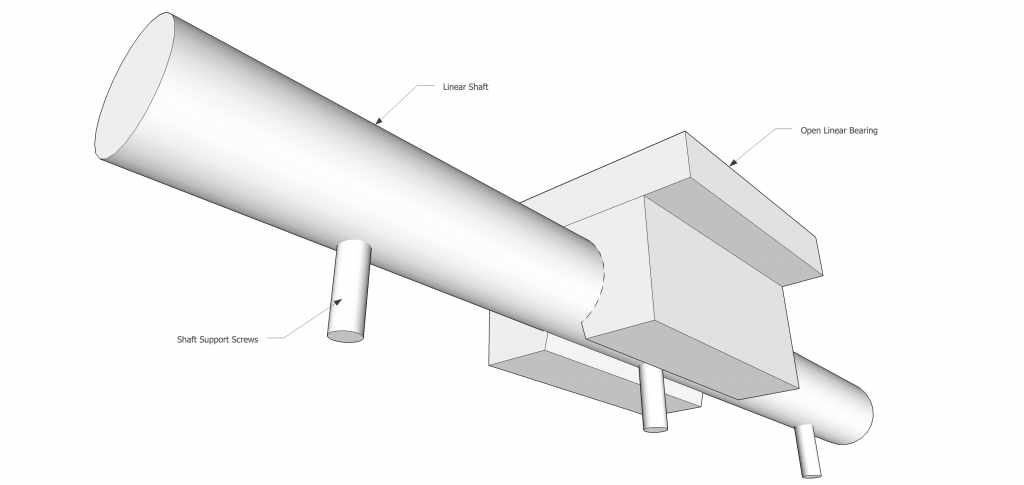
Long shafts may need to be supported to prevent sagging. Open bearings are made to accommodate supported shafts.
The bearings can be made of ¾” thick UHMW plastic, which is a low-friction material that’s easy to machine with standard woodworking tools. To make a bearing out of plastic, just drill a hole the same diameter as the corresponding shaft. I like to split the shaft hole with a saw kerf, which allows the bearing to slide a little more easily. Drill and tap some mounting holes in the edge of each bearing and attach the bearings to the machine with bolts.
The easiest way to drive each axis is with a lead screw and nut. You can be super-thrifty and use threaded rod, but this won’t give you the kind of accuracy CNCs are know for, so I suggest ACME screws. These screws have trapezoidal threads and can work with special anti-backlash nuts that reduce slop.
You can buy a kit with the motors and all the required electronic components for as little as $100, but at this price, you won’t get an enclosure for these parts to protect them from damage or exposure to dust, water or other harmful materials. A few manufacturers make what are called “drive box kits” that include an enclosure, and are usually simpler to connect than the cheap kits you have to wire up yourself. Both types of kits require a PC with a printer port, or parallel port. You’ll also need the controller software, and there’s an excellent program called Mach 3 that will get you up and running for $175.
Three-axis routers are simple machines, and once you understand how they work, you can easily build one with a few basic tools. Although building a router doesn’t require any computer skills, using one certainly does. You need to be computer literate to setup, program and operate your new router.
Would you like to learn more about building your own CNC machine? Register for Nick’s new Popular Woodworking course, Build a CNC Router, which starts April 29.
Here are some supplies and tools we find essential in our everyday work around the shop. We may receive a commission from sales referred by our links; however, we have carefully selected these products for their usefulness and quality.
sounds like an interesting project, and one I want to make at some point, when I have the time and money.
some time ago I came across this: http://www.holzmechanik.de/solidis_eng.html
maybe you can see something there that’s helpful.
best,
JFH