We may receive a commission when you use our affiliate links. However, this does not impact our recommendations.
Get clean cuts and a nice finish from a challenging piece of material.
A live edge (or natural-edge) bowl is one of the iconic forms of modern woodturning, and it is still a great way to show off a beautiful piece of wood. It’s also a good test of your developing turning skills. Good tool control is crucial for getting a clean cut and a smooth curve, especially on the wings of the bowl, where it will be difficult or impossible to adequately sand out any major defects.
The procedure is similar regardless of the size or other aspects of the piece. A limb or log is cut down the center. The outside curve of the limb or log will become the rim of the bowl. This half-section is mounted either between centers (as in this article), or on a faceplate or screw chuck, to turn the outside and to prepare the foot for re-mounting. It is then re-mounted on a waste block (as here), faceplate or chuck to turn the inside. A final mounting either between centers (for a simple foot like the one shown here), or in some kind of jig, allows the foot to be neatly finished.
Although the basic format is simple, small variations in shape and detail can have a considerable impact on the overall appearance of the piece, so making these bowls can be a good exercise in design as well. The bowl can be almost any size; you’re limited only by the size of limbs or logs available and almost any species will work. The bark may be left on or removed, the rim may curve in or out, the piece may be deep or shallow. The bowl may have a plain or fancy foot, or no foot at all. There are many possible variations within this ostensibly limited form. Exploring them can sharpen your eye as well as your turning skills.
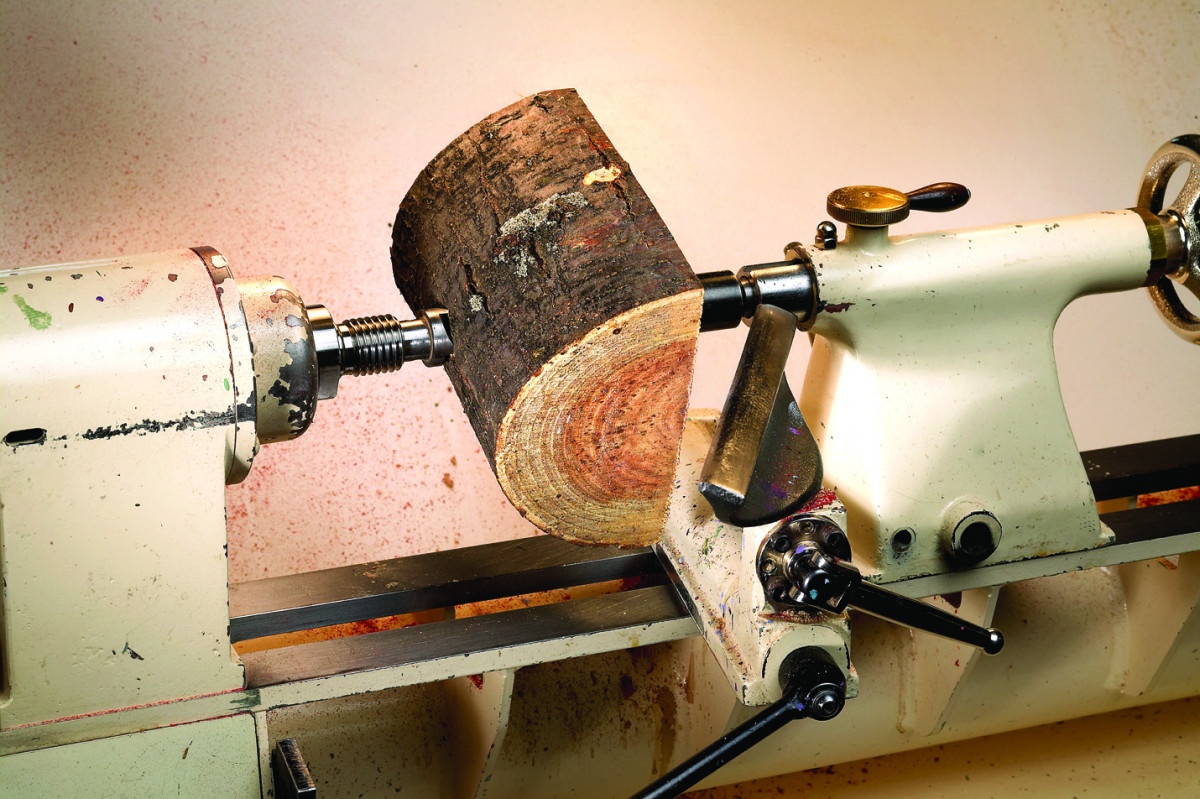
1. To set up to turn a natural-edge bowl, the workpiece is mounted between centers with a spur drive in the headstock and a live center in the tailstock.
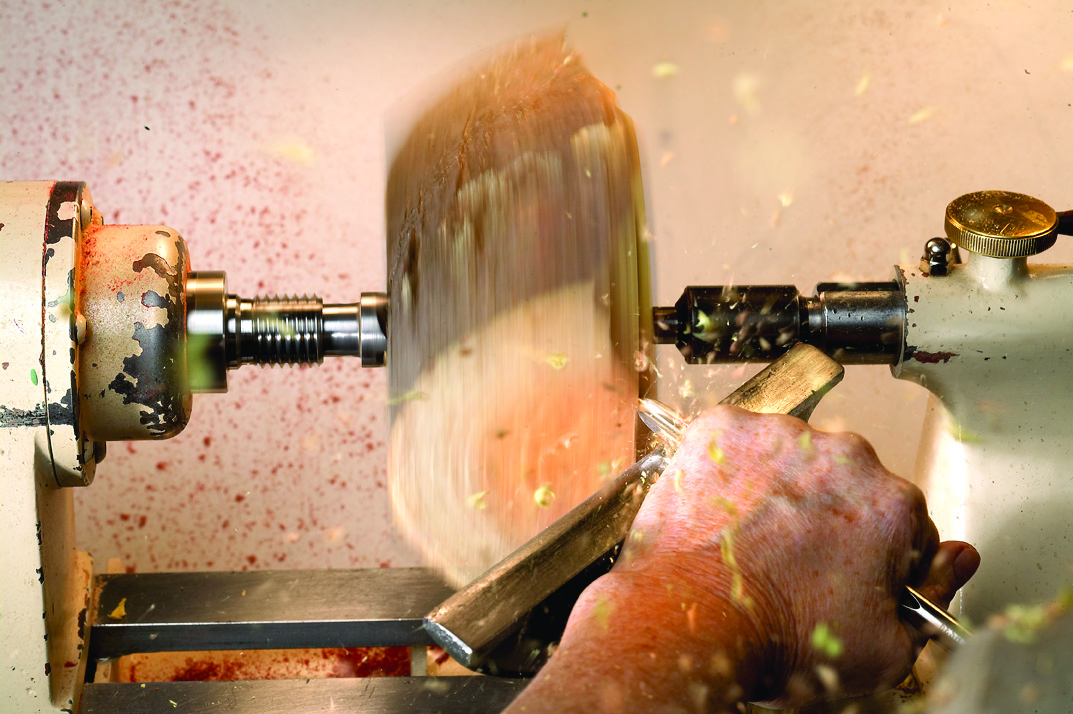
2. Begin cutting the outside shape with a bowl gouge. You should cut from the base (the center of the limb) toward the rim, or top, of the bowl (the bark side of the blank). The flute of the tool should be pointing in the direction you are cutting, and you should be using the low side of the gouge to cut (that is, the part of the edge most directly supported by the toolrest).
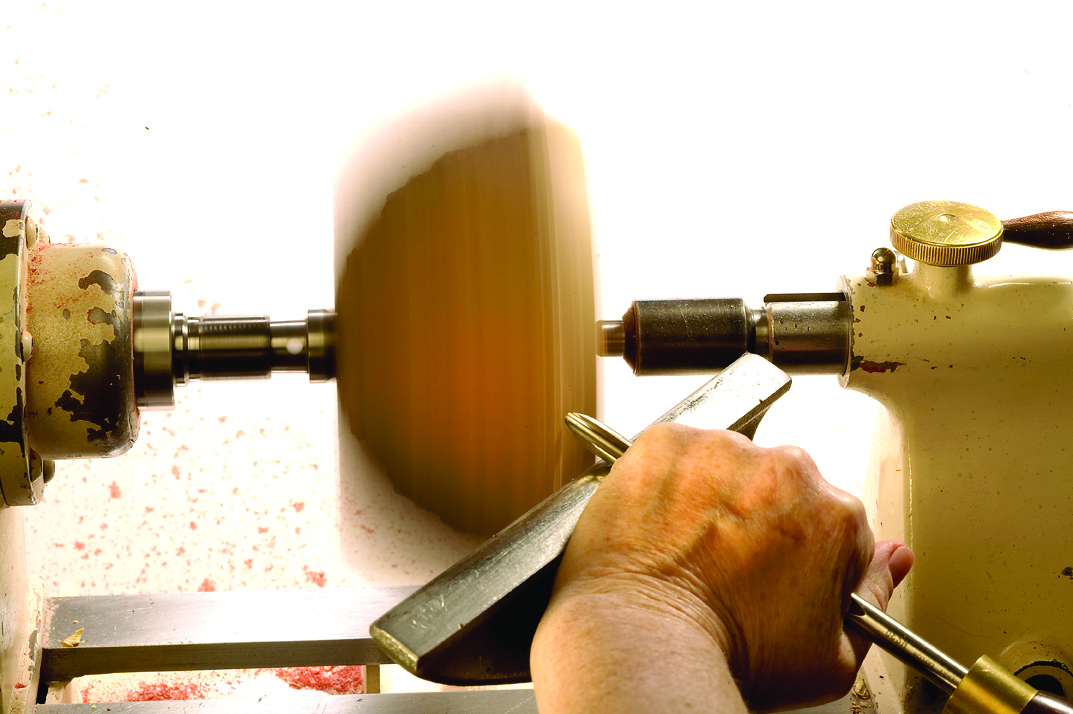
3. As the piece spins, you can see the shape of the outside curve of the limb (this will be the rim of the piece), surrounded by a ghost image of the entire limb section.
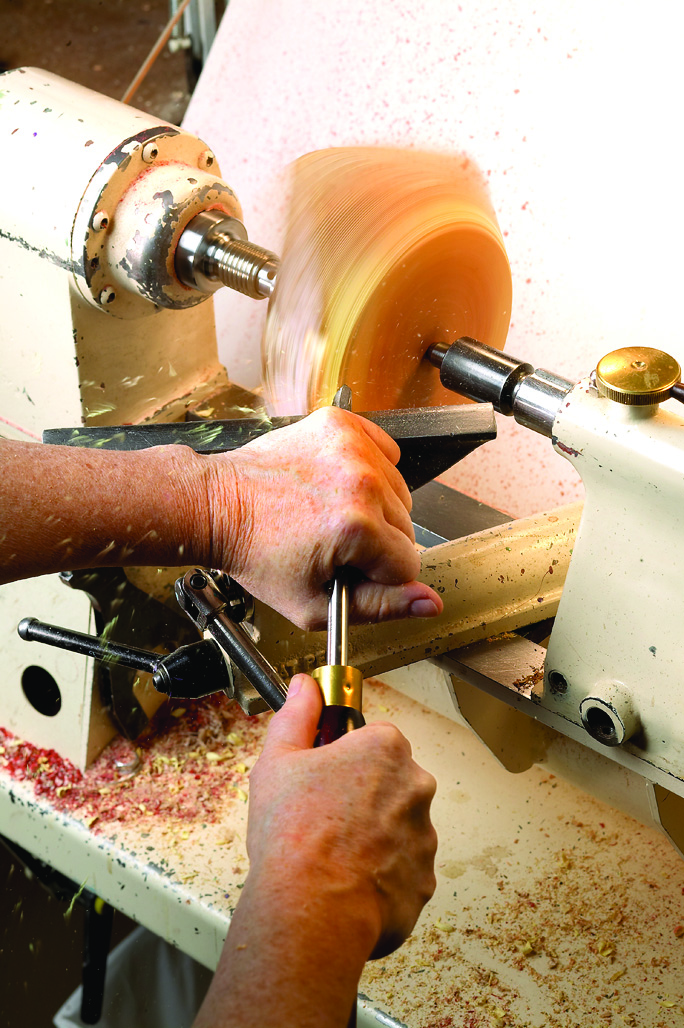
4. Getting a clean cut and a smooth curve when alternately cutting wood and air can be difficult. You must slice across the irregularity, rather than bouncing along on it. Instead of moving the whole tool forward, try using your left hand to hold the tool firmly down against the toolrest in one spot. Then …
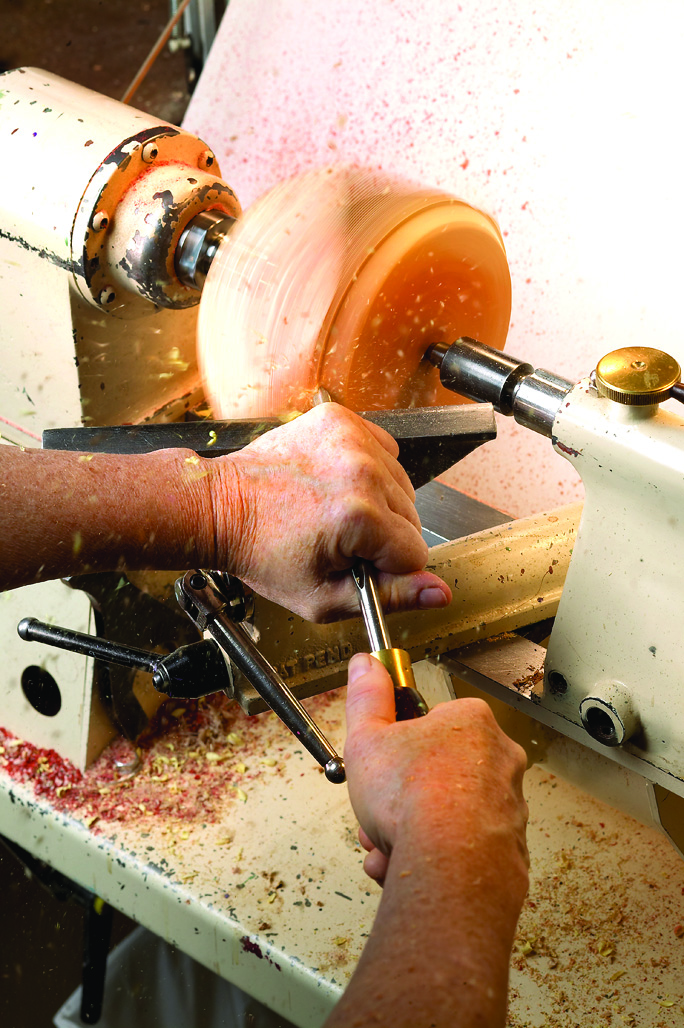
5. … lever the tool across the cut. Use the leverage the handle affords by holding it toward the end with your right hand (my right hand is close in only so both hands can be seen in the photo). Swing smoothly through the cut…
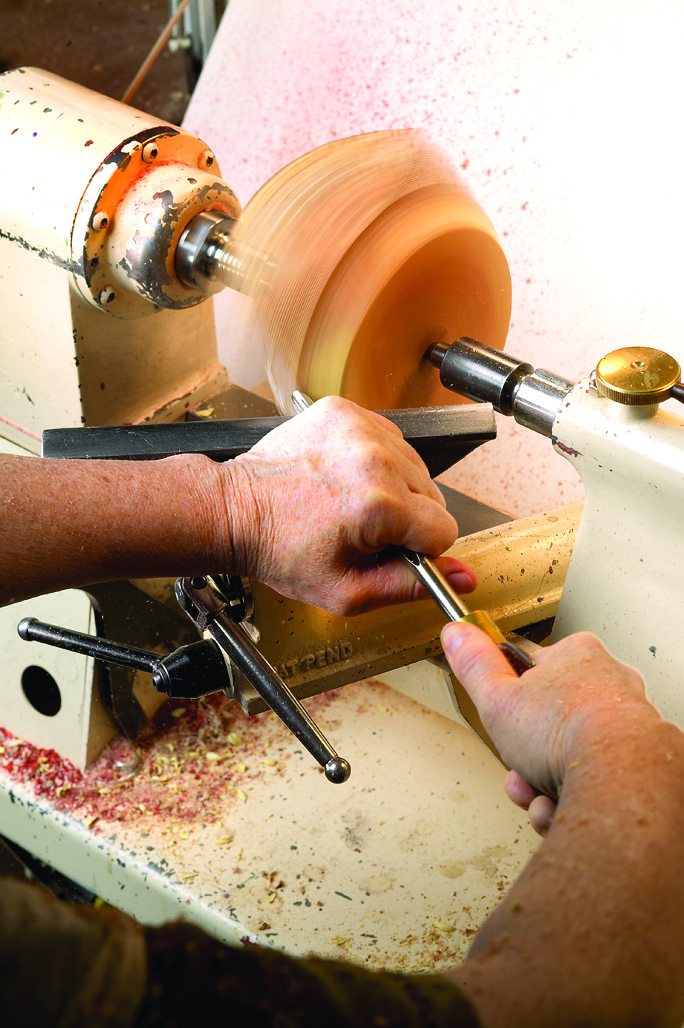
6. … until the tool exits the cut. Then move your left (fulcrum) hand, and repeat. Keep the toolrest close to the workpiece, and keep your gouge very sharp. Faster lathe speed will also help, but be careful not to exceed a safe speed for your lathe and for the size of the workpiece. Remember, this kind of turning tends to be more out of balance than regular bowls, even when the rounding has been completed.
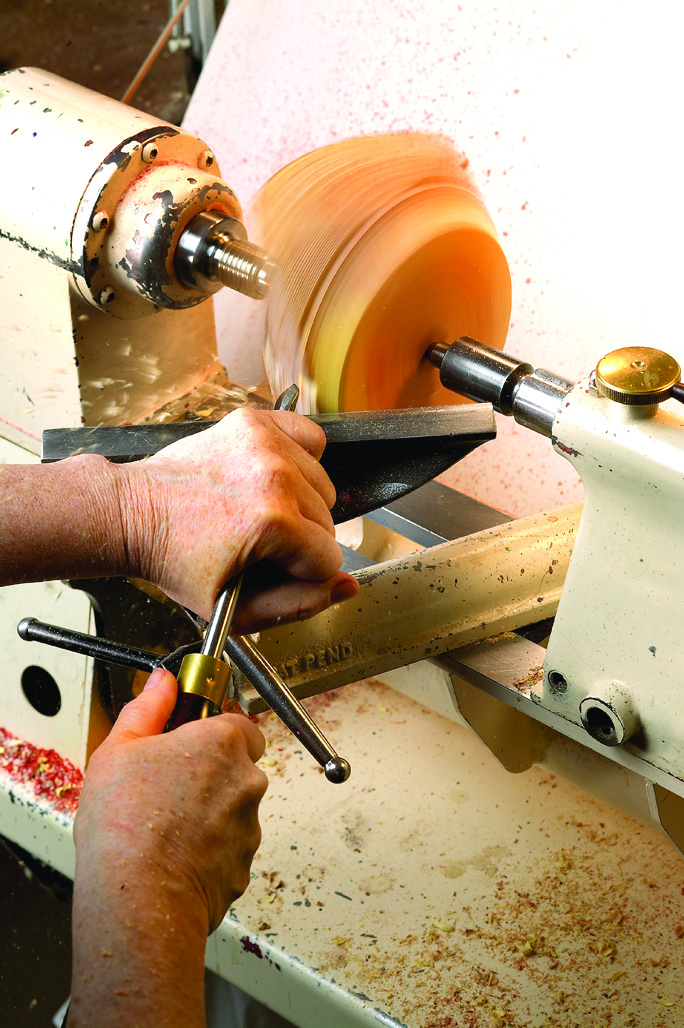
7. Continue shaping the outside of the bowl. Keep the tool sharp and pay attention to controlling it. Push up the side of the bowl (into the cut), not toward the axis (into the workpiece).
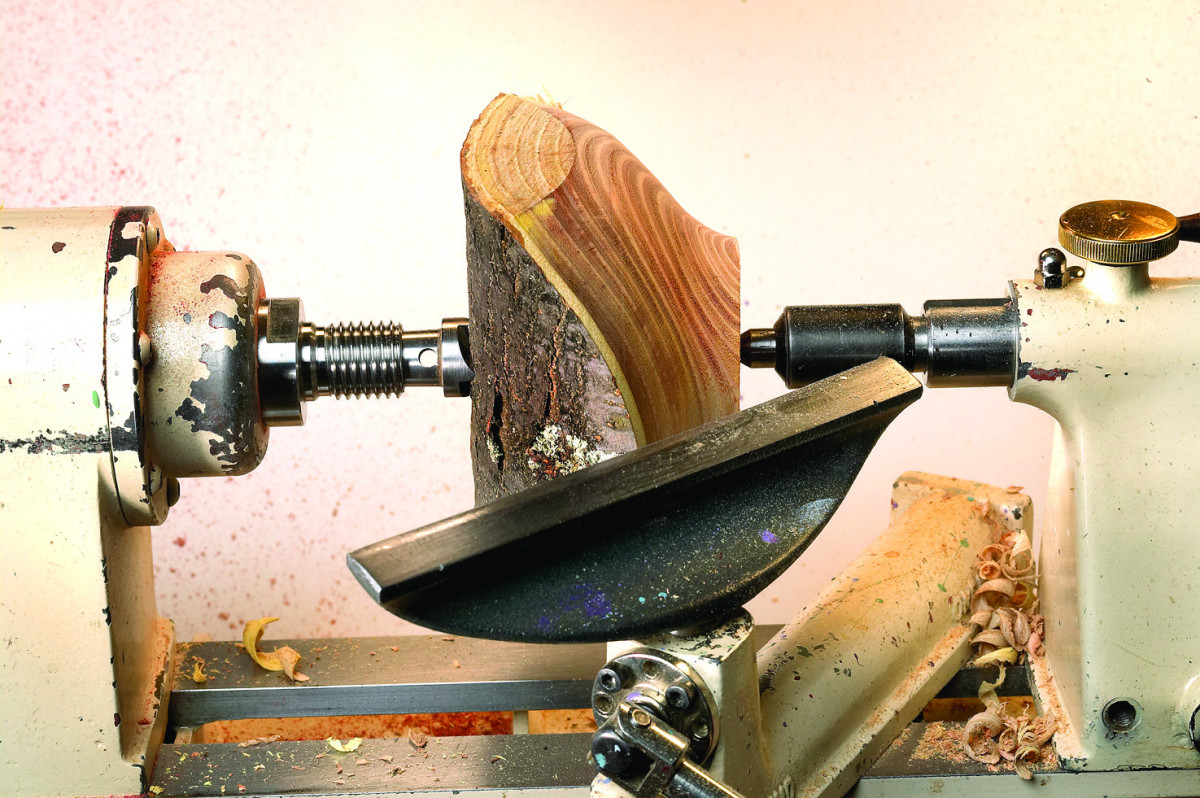
8. With the lathe stopped, you can see whether you have turned away all of the flat ends of the section. With the flat ends gone, continue to refine the shape and the surface until you have a bowl you like.
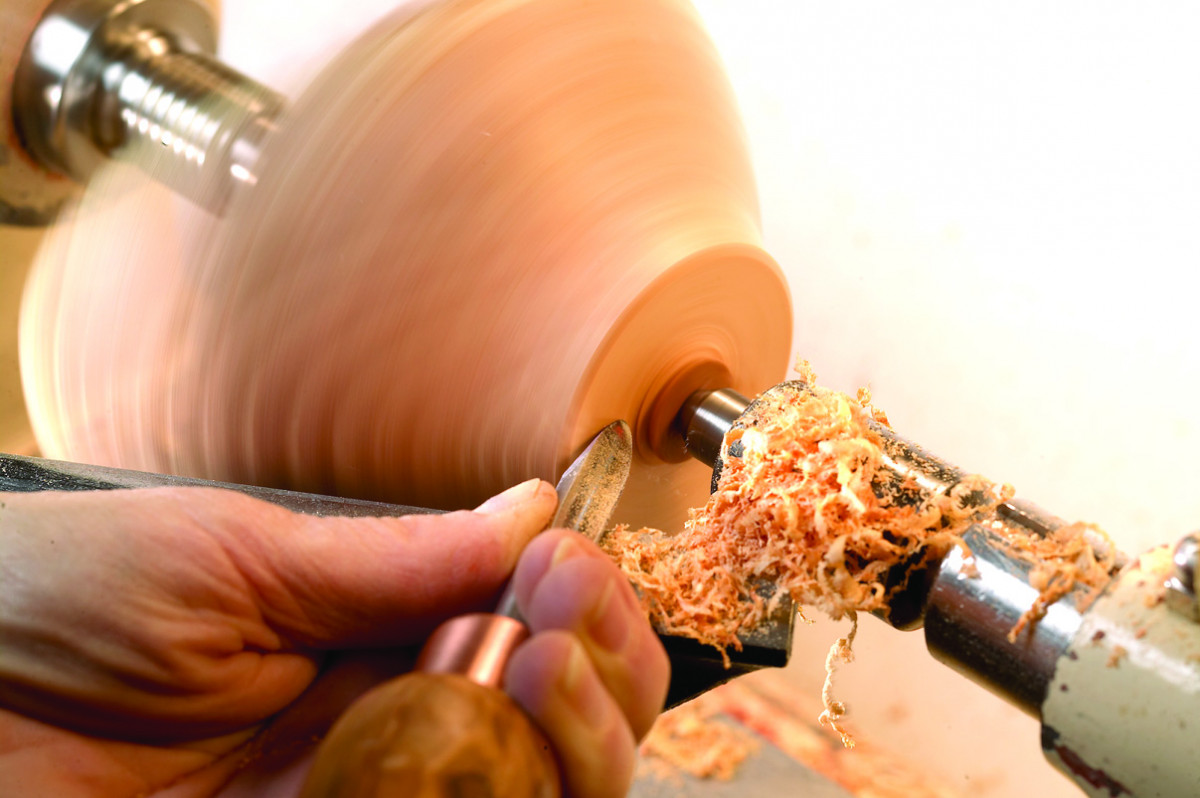
9. With a fingernail-grind spindle (detail) gouge, even up the foot and turn it flat.
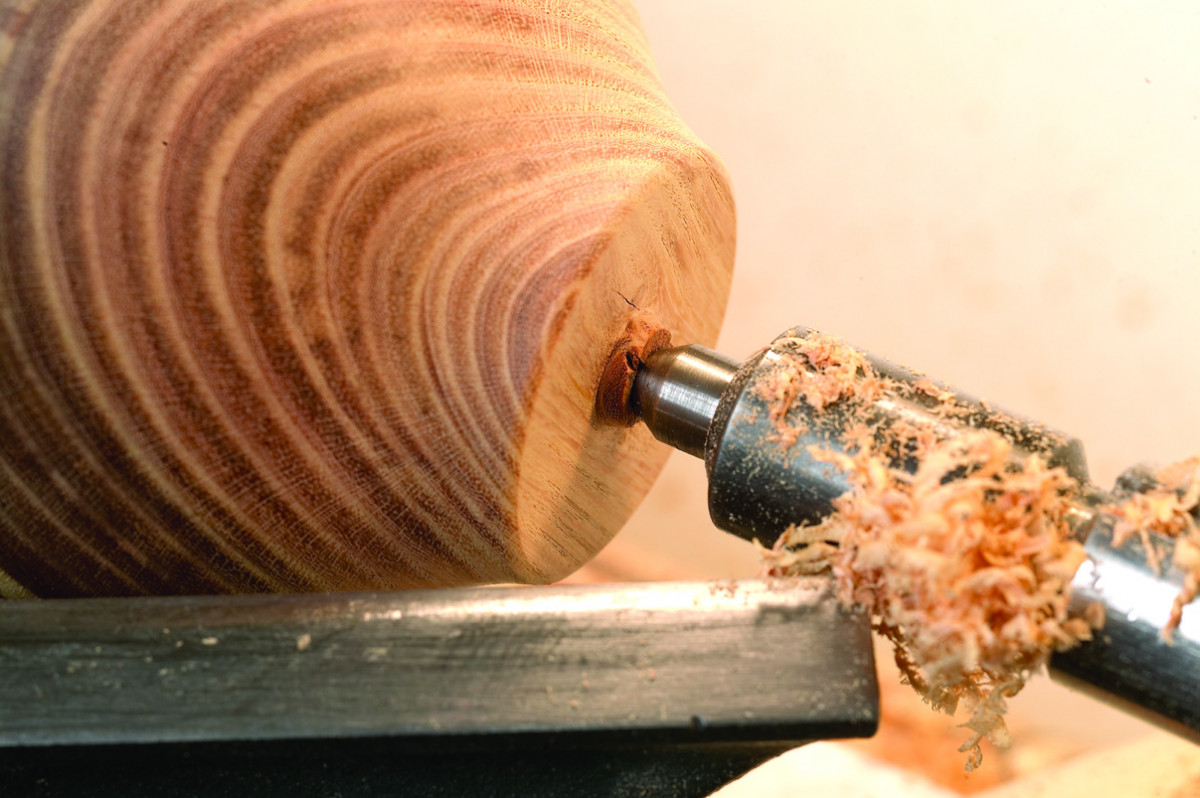
10. Leave a clean, slightly tapered nub in the center of the foot. This will be used to center the bowl for the glue mount. I find this a convenient, quick and safe way to mount a smaller bowl such as this one. If the piece were larger, I might mount it on a faceplate (using a nub the same diameter as the opening in the faceplate to facilitate centering) or a chuck (which would necessitate mounting the piece on a faceplate or screw chuck in order to turn a recess in the foot for the chuck jaws).
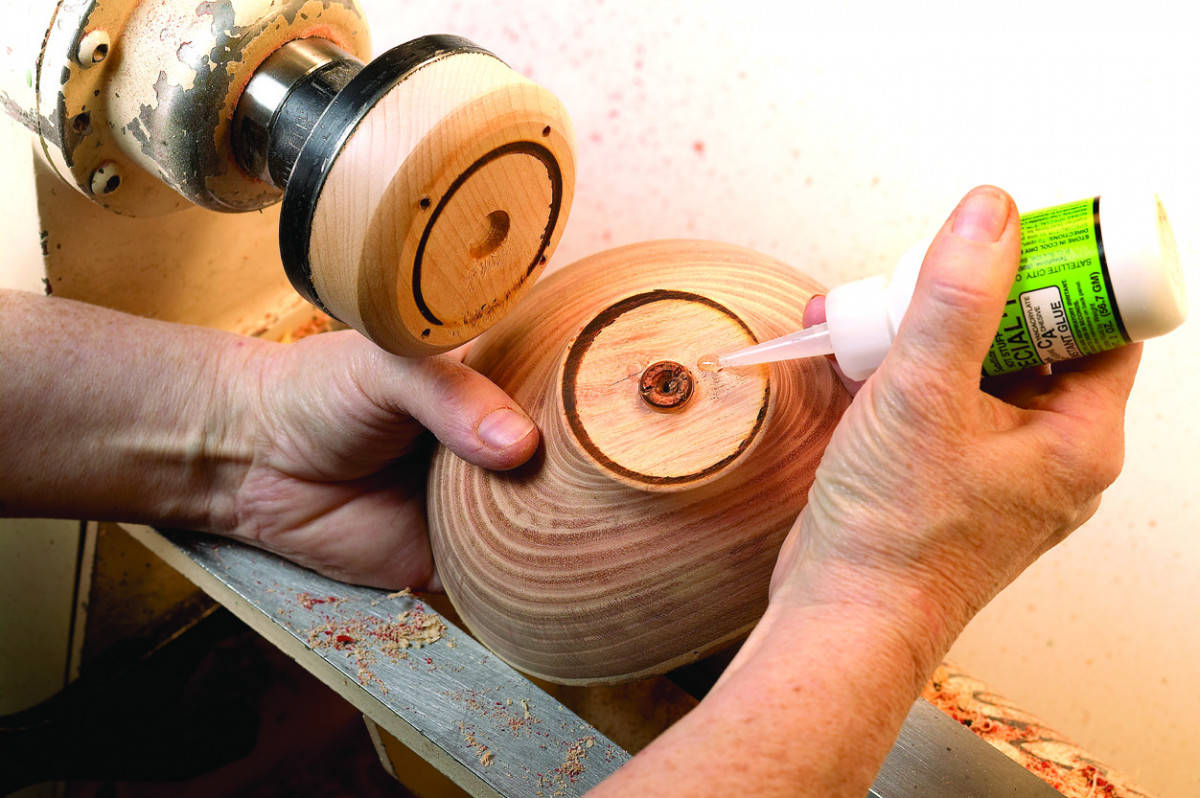
11. Mount a piece of waste wood (don’t use very soft wood, or easily split wood such as oak) on a faceplate, turn it round and flatten the surface. Measure the nub you left on the bottom of the bowl, transfer this to the waste block, then cut a slightly tapered recess. I test the fit by pushing the bowl into the waste block with the lathe on (leaving the burn marks seen here), but if you aren’t comfortable with this, just try the fit with the lathe stopped. Adjust, test, and repeat until you have a good fit. Put thick cyanoacrylate glue on the bowl bottom, spray accelerator on the waste piece, then mount the bowl.
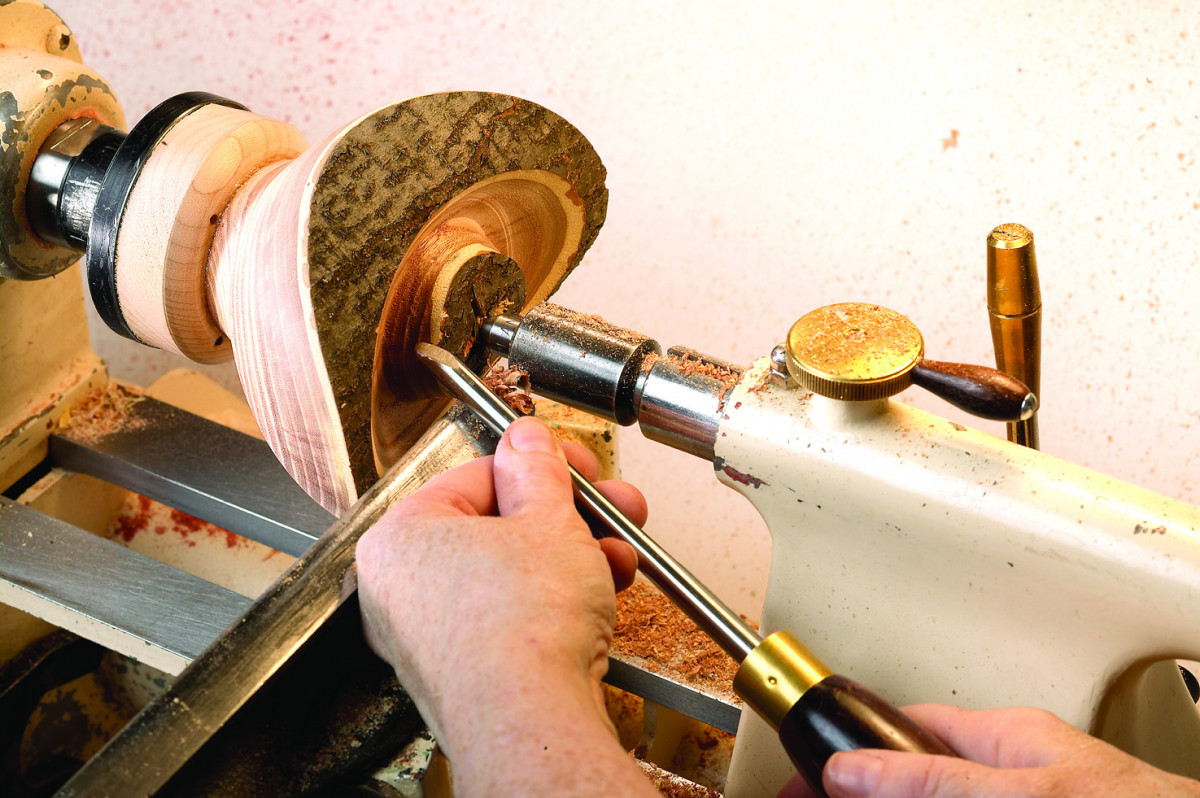
12. You may be able to bring up the tailstock for support as you begin to excavate the bowl. But be careful to cut only on the right side of the gouge, as cutting with the left (high) side is much more likely to cause a bad catch.
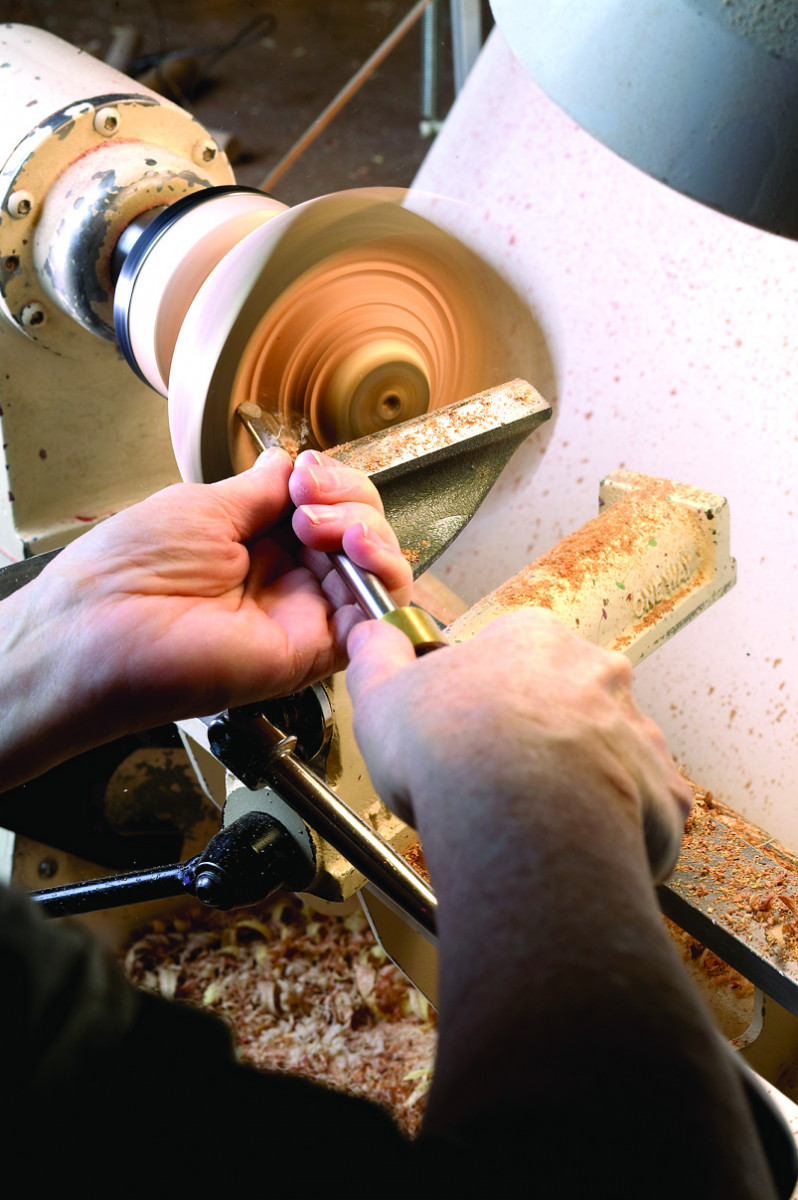
13. Continue removing wood from the interior. Cut from the rim toward the center/bottom. Stop each cut before you reach the waste left from the previous cut. If you run the gouge into the waste, it will catch.
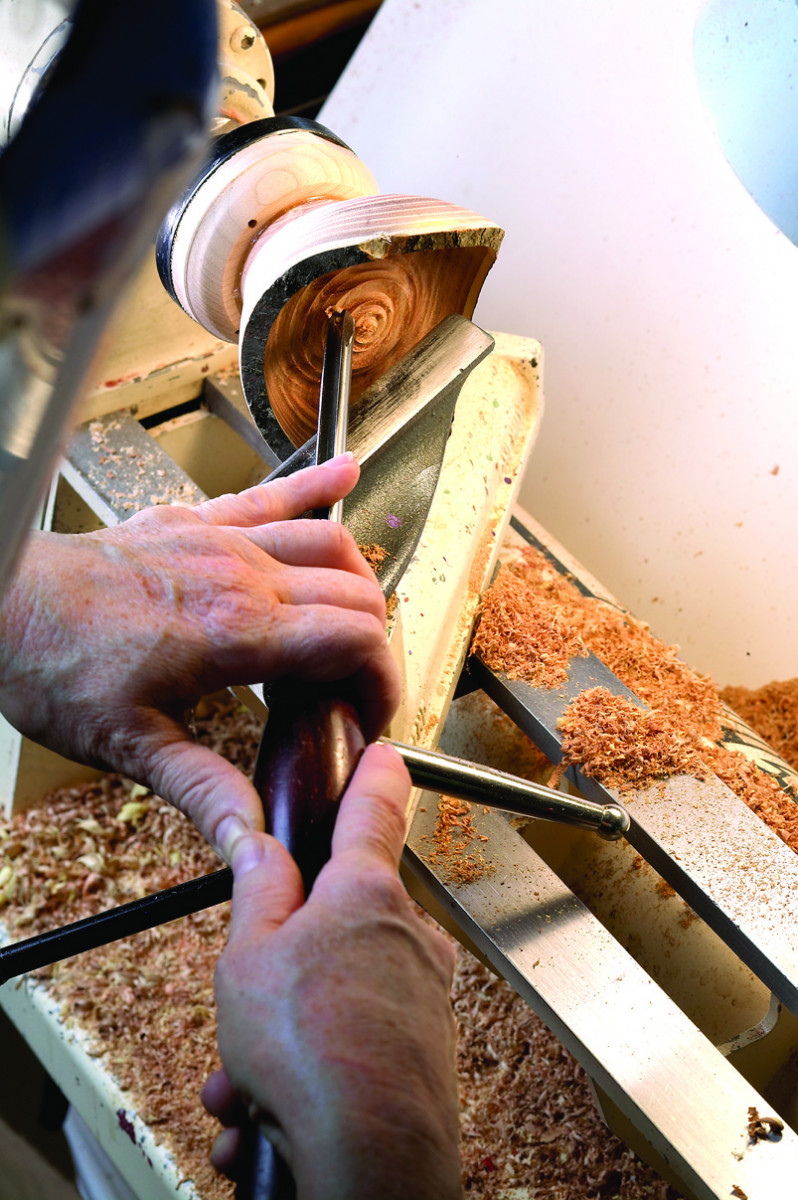
14. You can cut from the center down on the waste left in the middle. This uses different muscles, giving you a rest, and uses the other side of the gouge, meaning fewer trips to the grinder. It also applies force primarily toward the headstock rather than laterally, lessening the chances of pulling the piece off the mount. Cut top to bottom, right to left (downhill) and use the left (low) side of the gouge. (This is a smaller bowl, which I quickly mounted and turned to just this point after blowing apart the previous one. Oops.)
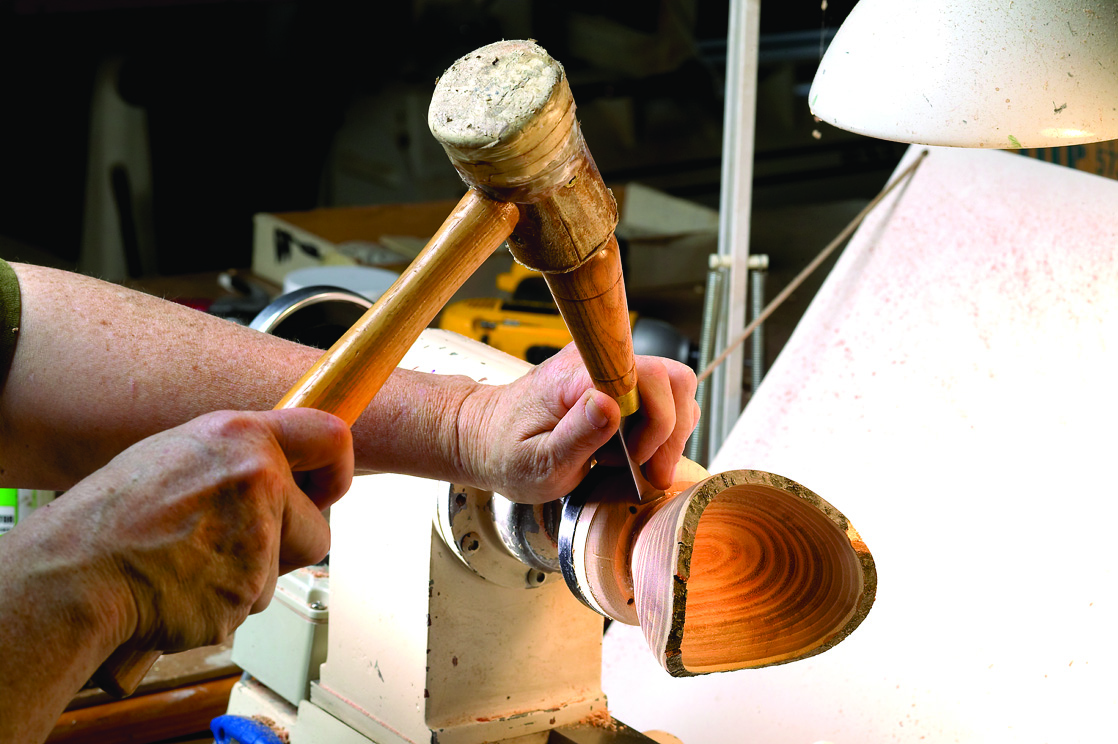
15. When you have completed the excavation of the inside of the bowl and sanded it to your satisfaction, remove the piece from the glue block. Put a towel on the lathe bed so the piece doesn’t get damaged if you don’t catch it. Place a flat chisel along the glue joint and tap sharply with a mallet. It should pop right off.
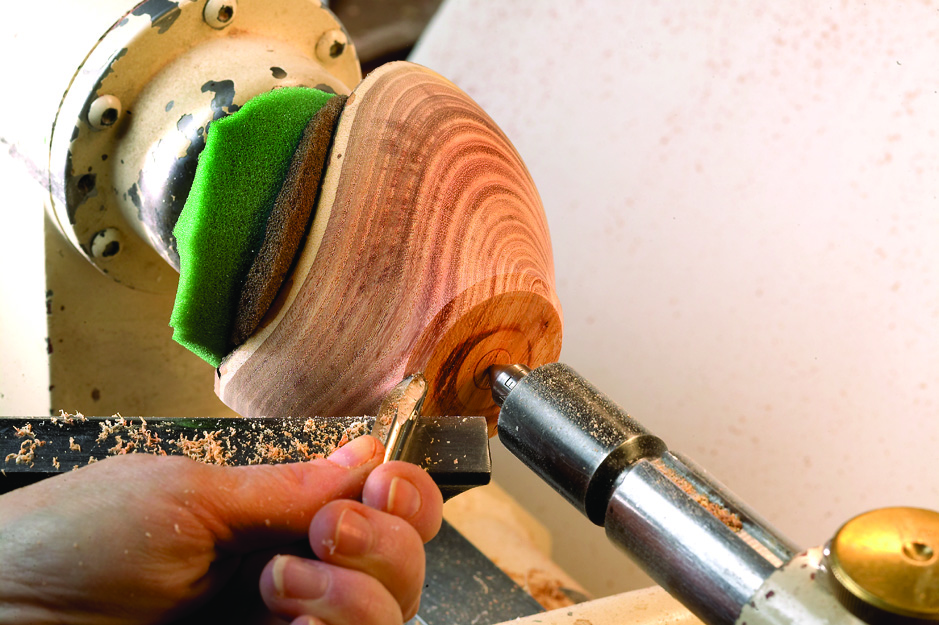
16. The piece is mounted to finish the foot. Turn a rounded edge on a waste block (you may want to use a larger waste block for this), place some foam between the block and the bowl to protect it, and bring it up the tailstock (with live center in place) to hold the piece. Slow the lathe speed down, and trim the glue off of the edge.
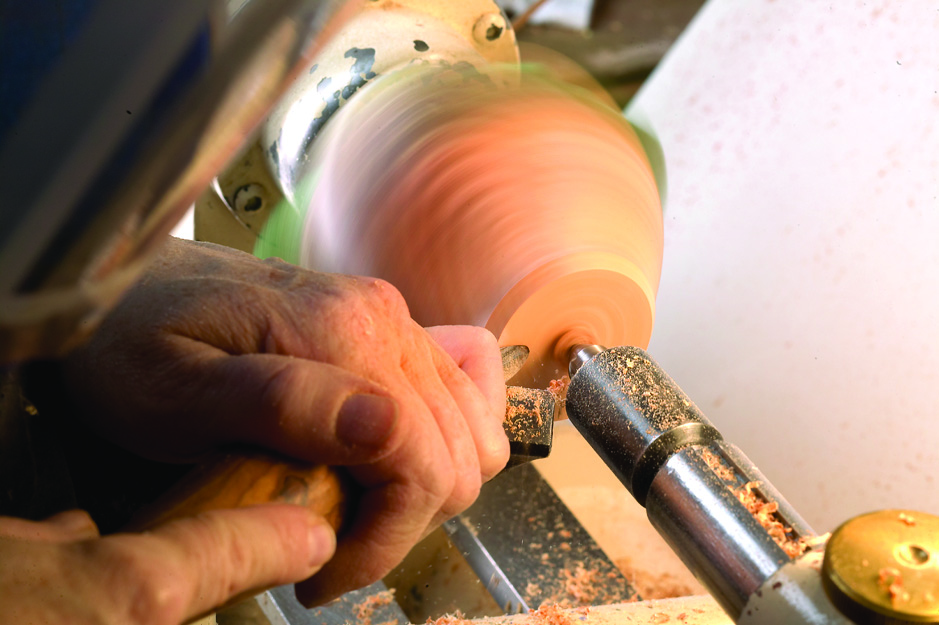
17. Turn a clean, slightly concave surface on the foot. After the piece is removed from the lathe, you can carve off the little nub (left in the center) with a small carving gouge and sand it smooth. PW
Power Sanding Natural Edges
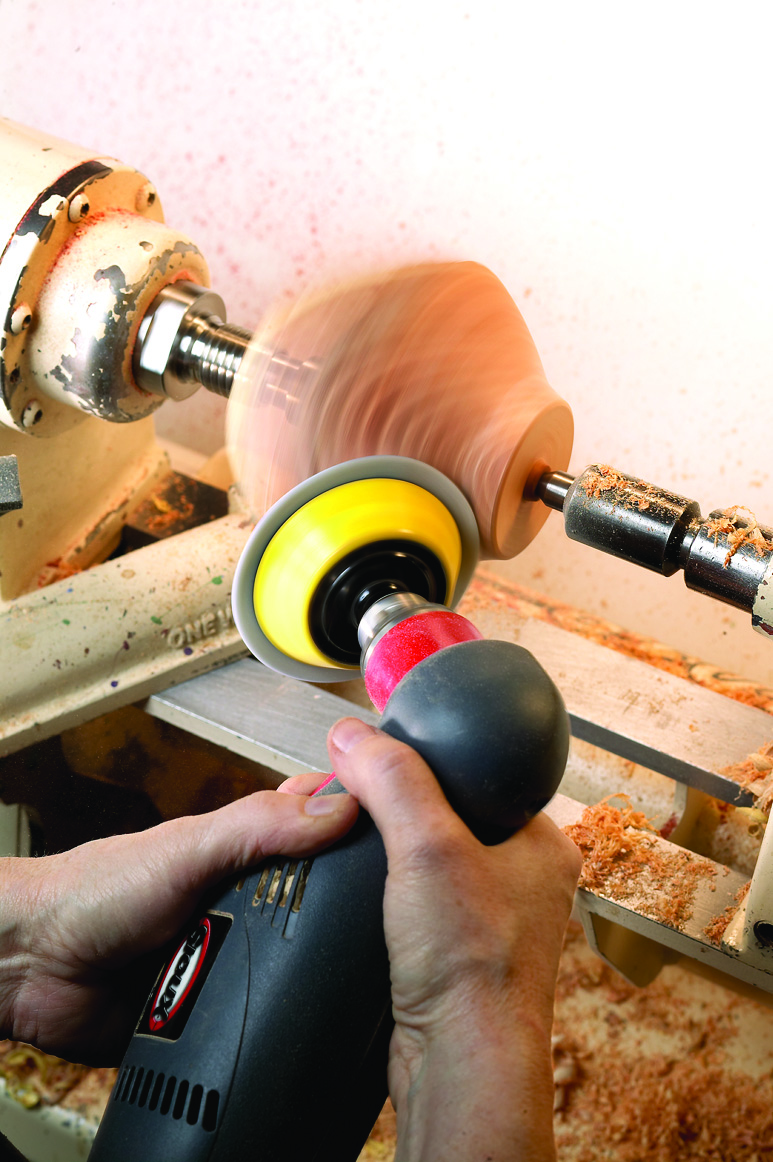
The sanding disc is mounted in a reversible drill.The disc surface at the point of contact should be going in the opposite direction from the bowl surface at that point. Here, the disc is contacting the wood at approximately 2 o’clock; the arrows show direction of rotation.
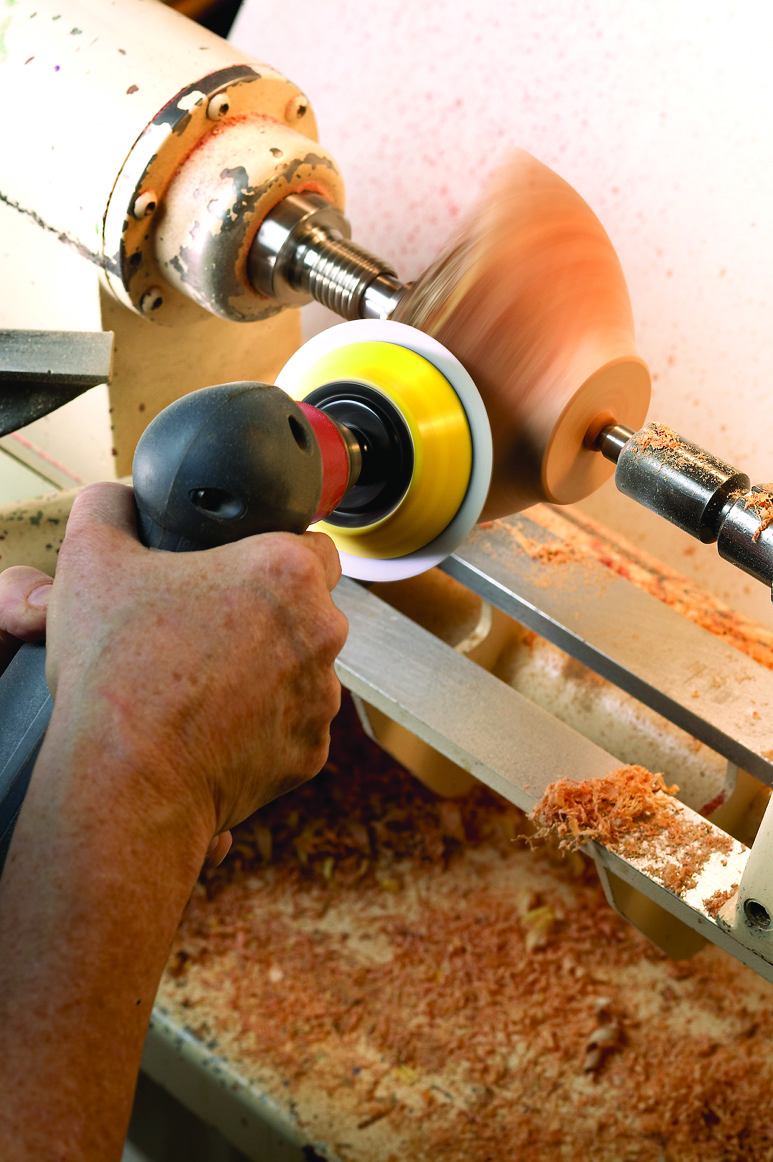
Here the disc is contacting the wood at 11 to 12 o’clock; this means the disc surface is traveling off of and away from the edge, not into it. It’s very important to hold the disc in the correct position. Keep it at the level of the surface of the wings and let the sanding grit do the work. Don’t push the disc toward the bowl, or it will tend to be caught as the voids come around in between the wings of the bow. At best this will round over the leading edges of the wings; at worst it could grab and damage the disc or even pull it into the gaps.
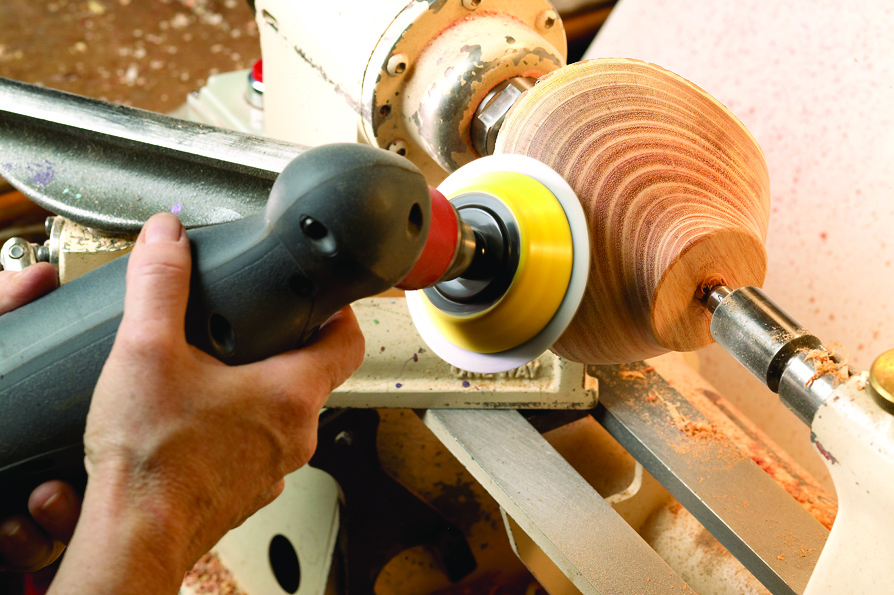
It still may be necessary to do some power sanding with the lathe stopped. This tends to leave heavier scratches that are more difficult to remove, so use a soft foam disc, and pay particular attention to eliminating all marks from the previous grit before moving on to the next. —JD
Here are some supplies and tools we find essential in our everyday work around the shop. We may receive a commission from sales referred by our links; however, we have carefully selected these products for their usefulness and quality.