We may receive a commission when you use our affiliate links. However, this does not impact our recommendations.
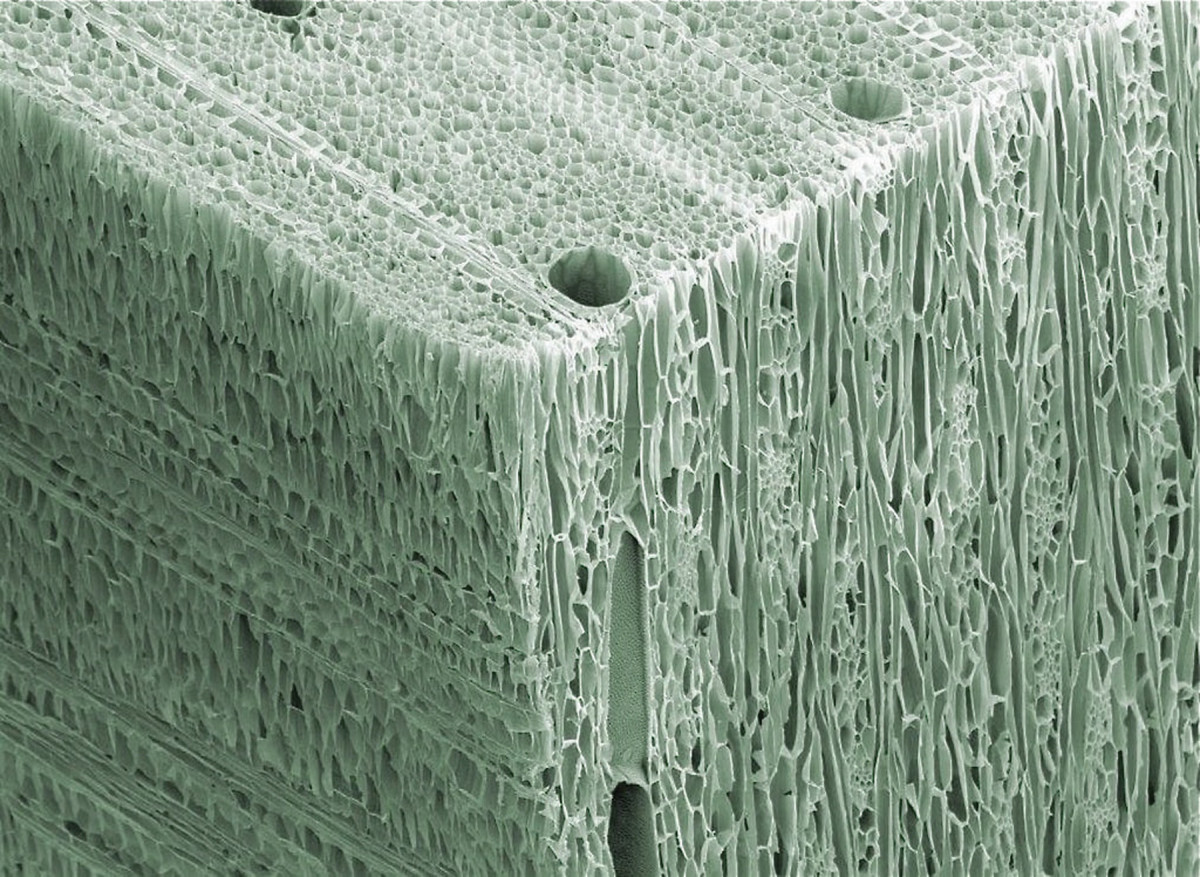
Magnified wood grain. When viewed through a microscope, the grain of wood becomes clearly visible. Think of it as miniature soda straws.
A better understanding of what causes grain raising will help you manage it.
Grain raising, including its causes and how to handle it, is not well understood by woodworkers. This leads to instructions that result in your sanding more than necessary to remove it and often not making the problem better. Understanding what’s happening in the wood will help you improve your work. First, some definitions.
To begin with, the very term “grain raising” is a little misleading. When we speak of grain in wood, we usually mean the visible boundaries between the tree rings. So, for example, with plain-sawn oak the boundaries are wide and clearly visible.
To understand the grain raising that creates fuzz on the wood you need to take a different perspective of grain. The grain that’s being referred to here is the tiny cells or fibers that makeup the wood. These cells are way too small to be visible except under magnification. So to make this explanation clearer, think of them as a bundle of miniature soda straws.
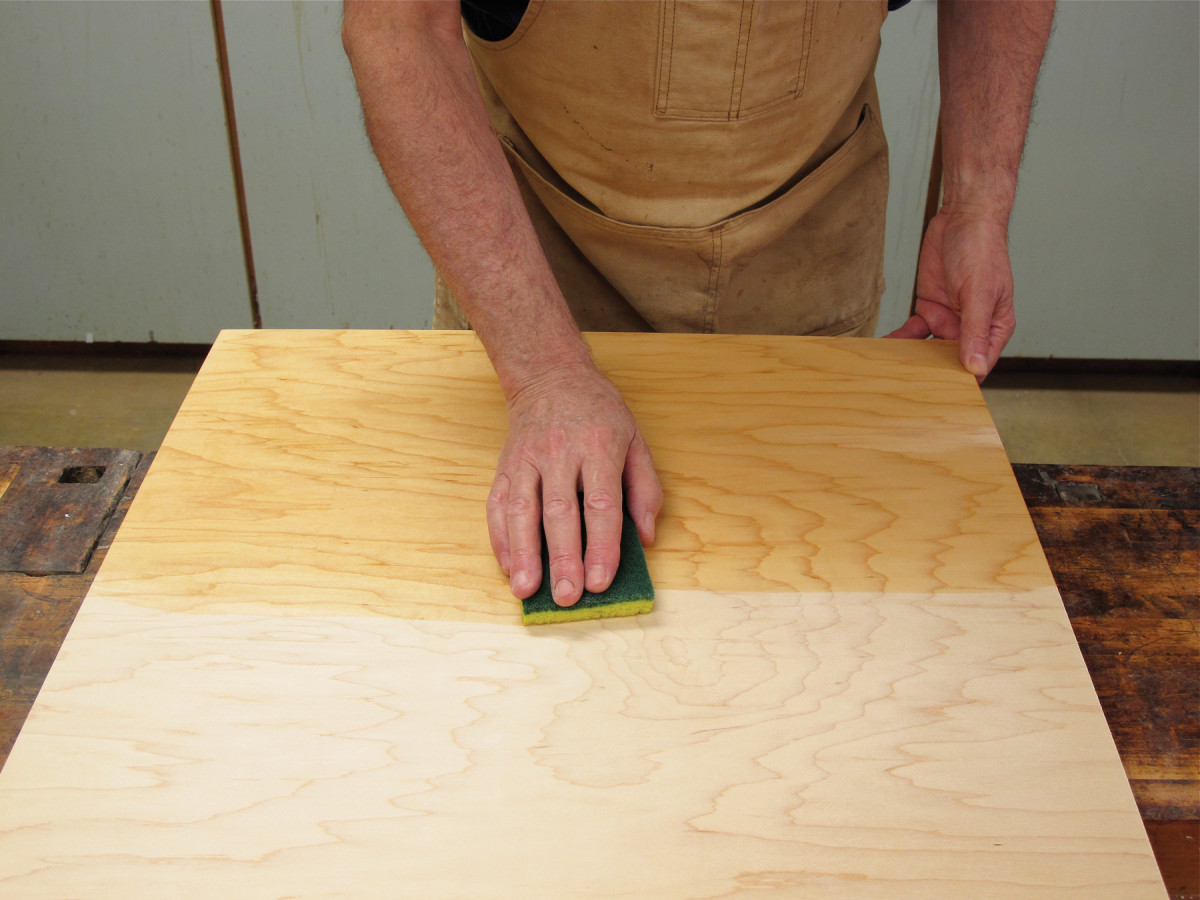
Wetting wood. One way to deal with raised grain is to raise it before applying the finish. Use a rag, sponge or sprits bottle to wet the wood, then let it dry.
Like the soda straws, the cells in wood are largely hollow and much longer than they are thick. In wood the cells are held together by a “glue” called lignin, which also contains the extractives that give wood its color.
When you saw or plane the end grain of wood, you have to use very sharp blades or the sides of the cells tear and collapse.
When you saw or plane the long grain, a similar thing happens, just much less so. Still, if your saw blade or jointer or planer knives aren’t sharp, they cause the cell walls to collapse or the cells to press into layers of cells underneath.
The same thing happens with dull sandpaper. Sandpaper is expensive, so it’s natural to use it for much longer than we should. The dull grains of abrasive tear the walls of the cells and press them into the cells beneath rather than smoothly cutting them off.
When moisture is then introduced in the form of humidity or, especially in the form of liquid water, these pressed and torn areas swell so the surface feels like peach fuzz. This is what we refer to as grain raising.
If you want to try an experiment, run one piece of wood over a jointer and hand plane another with a very sharp plane iron. Don’t sand either. Then dab some water on each and feel them after the water has dried. There should be much less grain raising on the hand-planed wood because the cell walls have been cut clean.
Thin Finishes
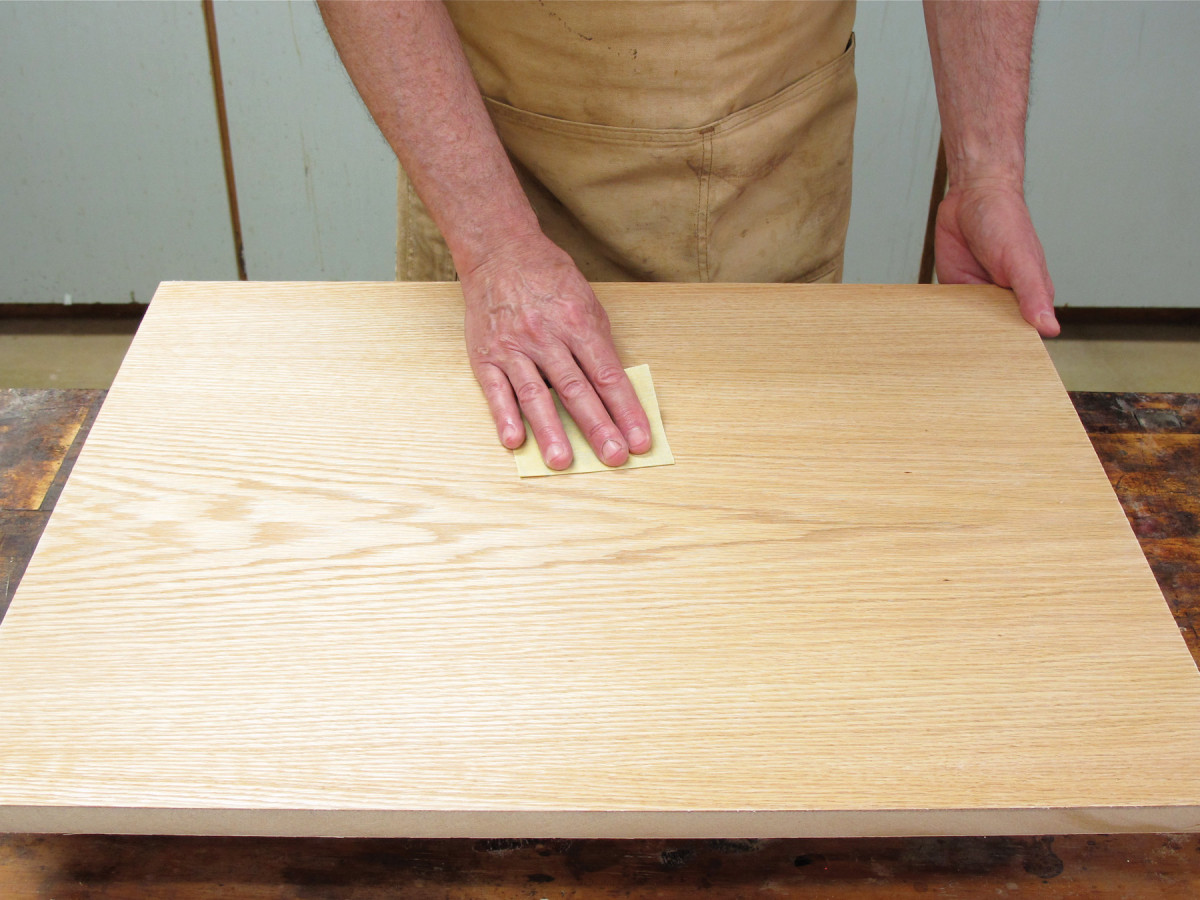
Sanding raised grain. After the wetted wood has dried, sand it just enough to remove the raised grain, no more. Use a fine grit sandpaper, for example, #320 grit as I’m using here.
Many years ago I was sitting in the office of a prominent woodworker who was raving about the qualities of a popular brand of oil finish. He was making the point of how resistant this finish was to moisture.
He had a couple of bookcases in his office that he had finished several years previously with this finish. So I walked over and ran my hand over the surface. I expected it would feel rough because I had experienced that at home on wood that I had finished with the same oil finish after several years. But the surfaces were smooth like they had just been sanded.
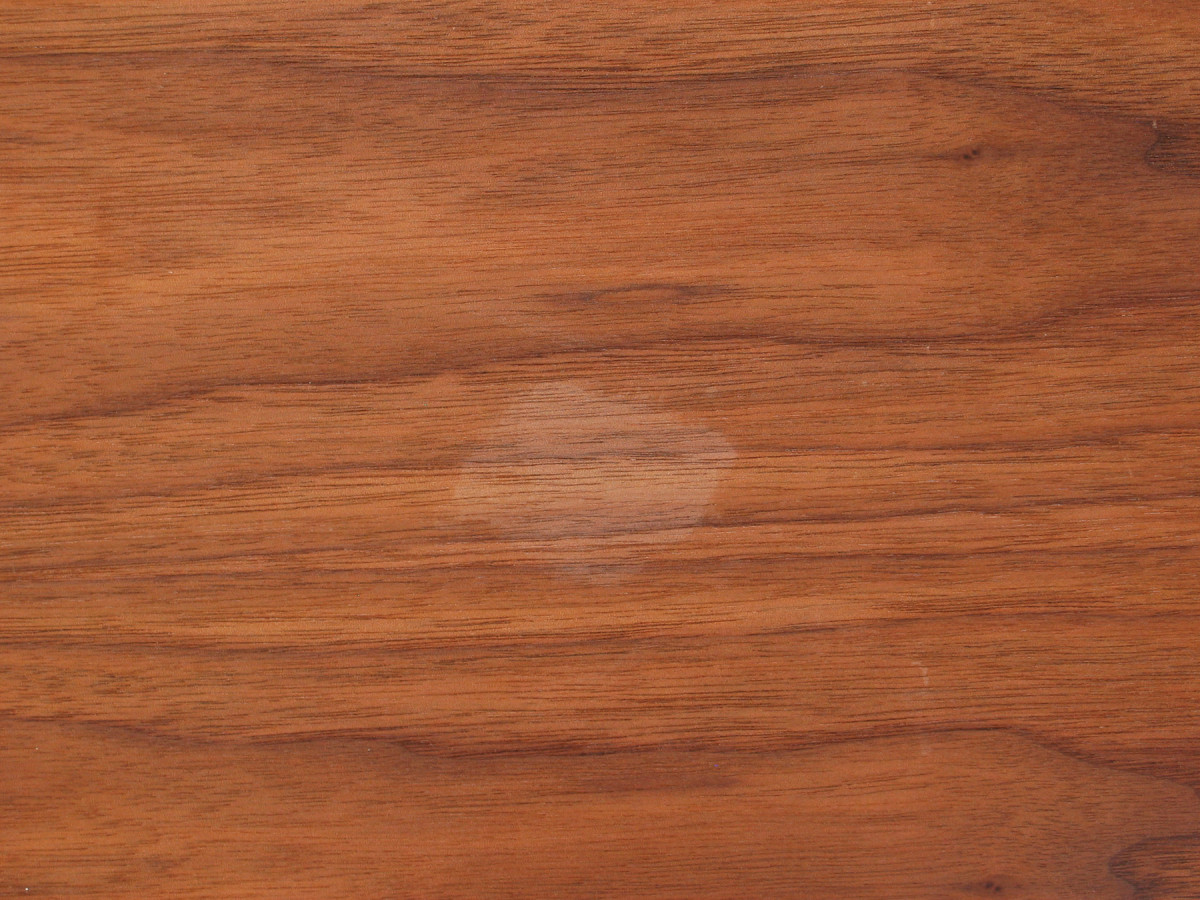
Water damage. If you haven’t raised the grain and sanded it smooth under an oil finish, a puddle of water can get through the finish and raise the grain, which will show up lighter if the light reflection is right.
It was not until I got home that I realized the explanation. This friend lived in the desert where there was almost no humidity. There is a lot of humidity where I live (though not nearly as much as near the Gulf Coast).
So the explanation was that an oil finish, with no build, isn’t thick enough to block humidity from getting to the wood and causing the pressed and torn cells to expand enough to be felt.
The lesson I learned from this experience was that the best practice when using an oil (or for that matter, wax) finish with no build is to raise the grain first by wetting the wood and sanding it smooth after it has thoroughly dried.
How Much to Sand
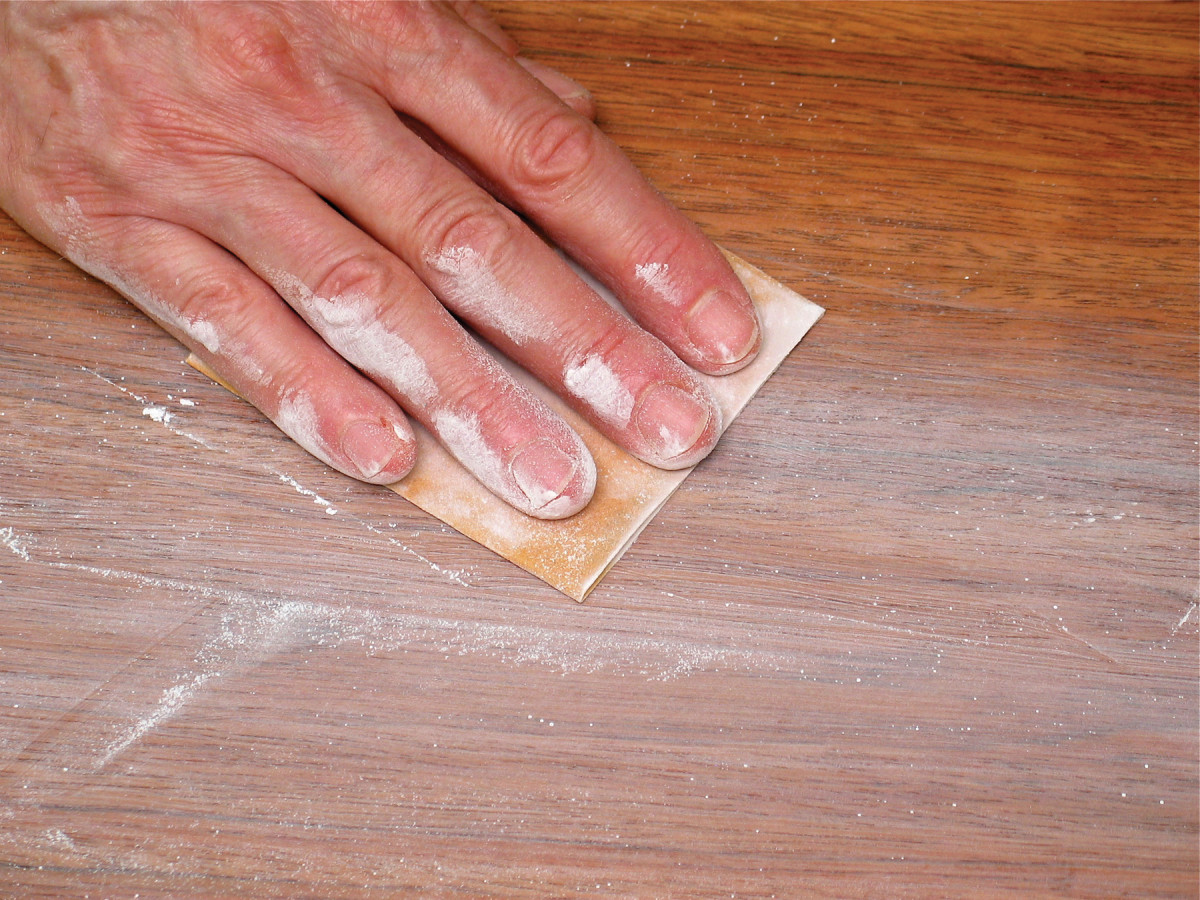
Sanding sealer powders. When using a film-building finish such as alkyd varnish or lacquer on large or multiple objects, you can speed your work by applying a first coat of varnish or lacquer sanding sealer and sanding it smooth. Then apply several coats of the finish.
Here’s the critical point. The cells or fibers that get smashed and torn by the pounding they get from a jointer or planer or from dull sandpaper are only a few cells deep. If, in sanding the raised grain smooth, you sand deeper than this damage, especially if you’re using dull sandpaper, you will expose fresh wood that will have almost the same susceptibility to grain raise again.
So in removing raised grain from wetted wood you need to use fresh sandpaper of a fine enough grit so you just make the wood feel smooth. Don’t sand deeper than this. Appropriate grits are usually between 220 and 400.
If you are applying a film-building finish such as shellac, lacquer, alkyd or polyurethane varnish, or especially a water-based finish, another way to deal with raised grain is to “bury” it with your first coat. Simply apply this coat, then sand it smooth after it has dried. Then continue with your additional coats.
The same procedure works with a water-based stain or water-soluble dye. Apply the first coat of finish to bury the raised grain, then sand this coat smooth after it has dried.
If you are finishing with alkyd varnish or lacquer, especially on multiple or large objects, you may want to use a varnish or lacquer sanding sealer for the first coat. Sanding sealer powders when you sand it in contrast to alkyd varnish and lacquer, which gum up the sandpaper, slow you down, and cause you to use more sandpaper.
Polyurethane varnish and water-based finish don’t gum up sandpaper as long as you let them thoroughly dry, so there’s no need for a sanding sealer. In fact, it’s not wise to use a sanding sealer with these finishes because it weakens the bond to the wood.
Here are some supplies and tools we find essential in our everyday work around the shop. We may receive a commission from sales referred by our links; however, we have carefully selected these products for their usefulness and quality.