We may receive a commission when you use our affiliate links. However, this does not impact our recommendations.

The other green giant. At 9′ tall, this Zimmermann band saw has more than twice the throat capacity as a typical 14″ home shop band saw.
A St. Louis physician spent years assembling the perfect shop.
The problem with many “dream shops” is that their visionaries never wake up and get on with building any furniture.
There’s nothing inherently wrong with building a hobby shop and having the shop alone being the hobby, but this magazine is about building wooden things inside a shop. So it seems a waste when I visit a shop that never sees a speck of sawdust.
For the last few years, I’ve been following the progress of Dr. Kent Adkins, a young surgical urologist outside St. Louis, who has been methodically planning and constructing an 1,800-square-foot shop attached to his home by a breezeway.
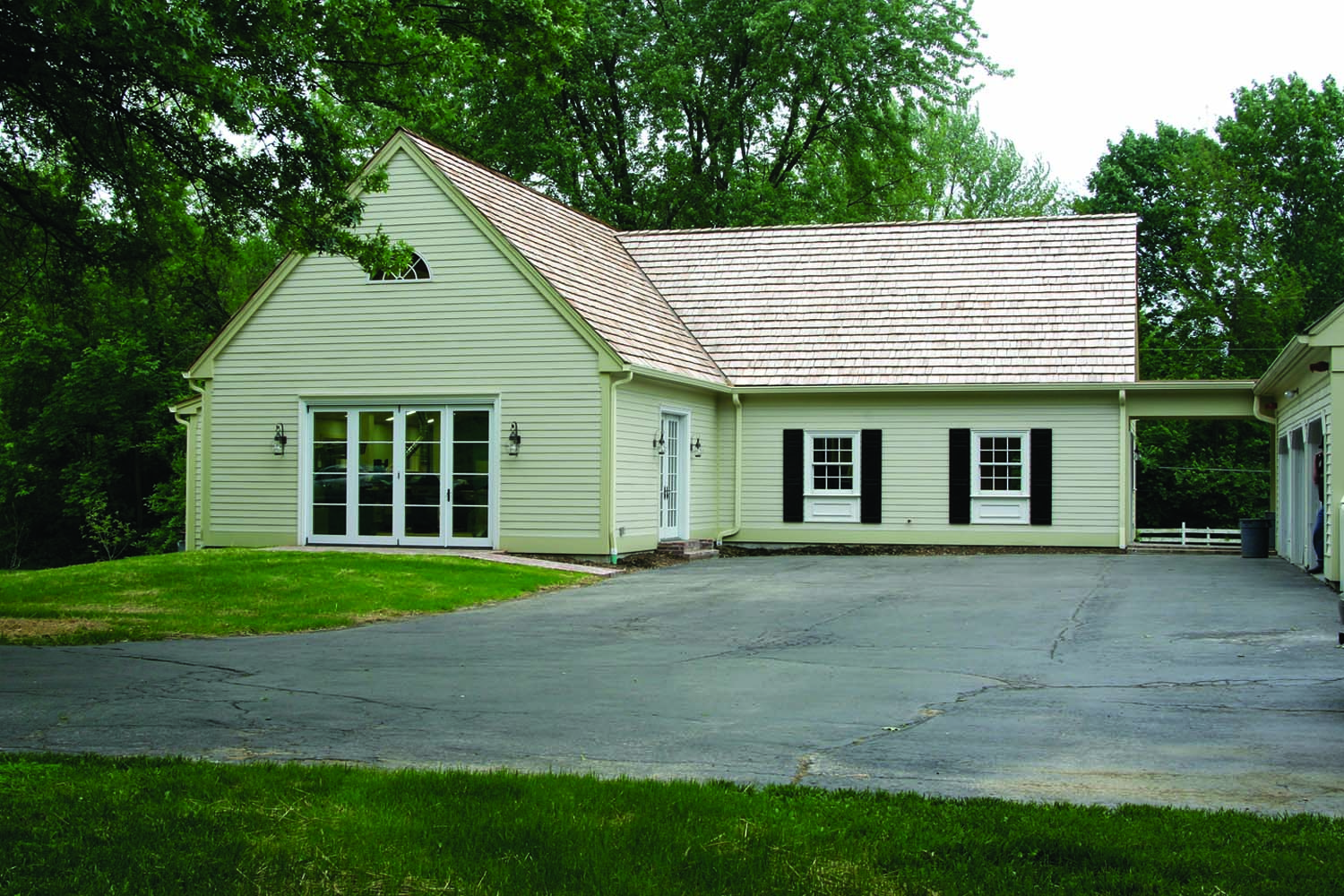
In pleasant surroundings. Adkins’s shop is at the end of a quiet cul-de-sac surrounded by trees and a garden.
It would be easy to assume that Adkins simply picked the machines and tools with the highest price tags for his shop, but that would be an insult to the years of passionate research Adkins and his friends have put into searching the world for tools that are the best in class and safe as possible.
I’ve seen Adkins on the floor of the International Woodworking Fair, picking apart the features and details of machines, veneer presses and even hand tools. He traveled twice to the Ligna woodworking show in Germany. I’ve watched him question sales representatives with the insight of a journalist. And in May 2010, I got to operate his crane.
Yes, the man has a crane.
During a warm spring weekend, Adkins opened his new shop to friends, neighbors, family and two editors – myself and Senior Editor Glen D. Huey. During our evening in his shop, we picked through every nook and cranny of his wood-floored soaring shop space, ran his machines (mostly German) and were impressed with what Adkins has accomplished.
A Tour of the Machinery
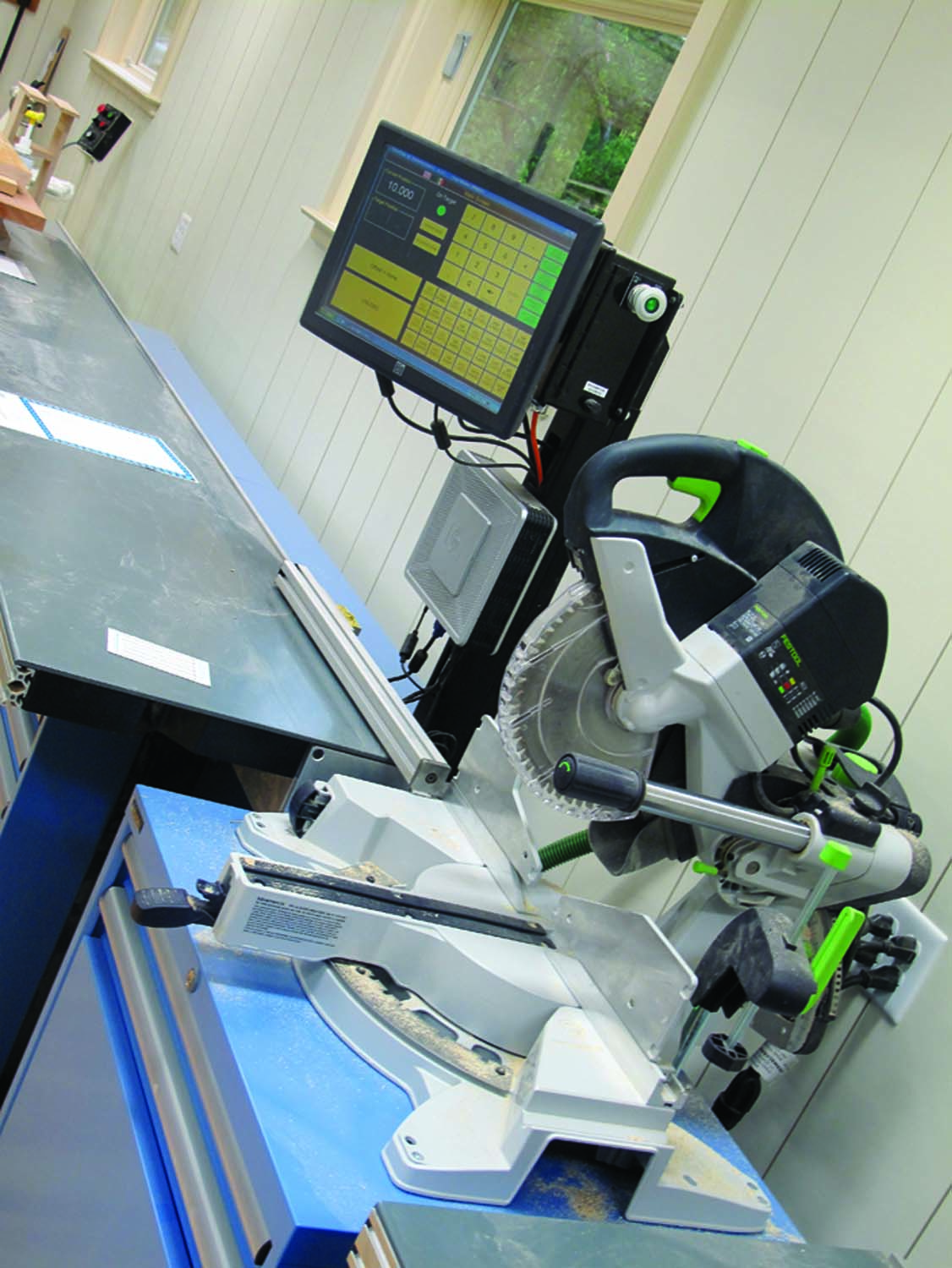
Finely chopped. The computerized RazorGage stop system on this Festool miter saw setup makes cutting stock to length a breeze.
The shop is L-shaped with three entrances: a door in the breezeway, French doors by his table saw and a folding curtain wall of windows that faces out into his front yard. On a nice day, Adkins can open up this wall and bring in the outside breezes.

A shapely shaper. This Martin shaper makes smaller machines look like toys. It features a head that can tilt both ways.
As you walk in through this opening, you see an AL-KO dust extractor to the right that Adkins can switch on and off using his iPhone. In front of that is a Kundig edge sander. Off to the far left is a Oneway 2436 lathe. But those machines are almost invisible compared to the huge numerically controlled Martin shaper equipped with an Aigner fence and power feeder. After using Delta and Jet shapers, this Martin is like experiencing alien technology. The throat plate opening around the cutterhead is motorized and closes using eccentric rings. The head tilts 45° both ways. And when you look up, you see three more Martin machines – a T45 planer, a T54 jointer and a T60 sliding table saw.
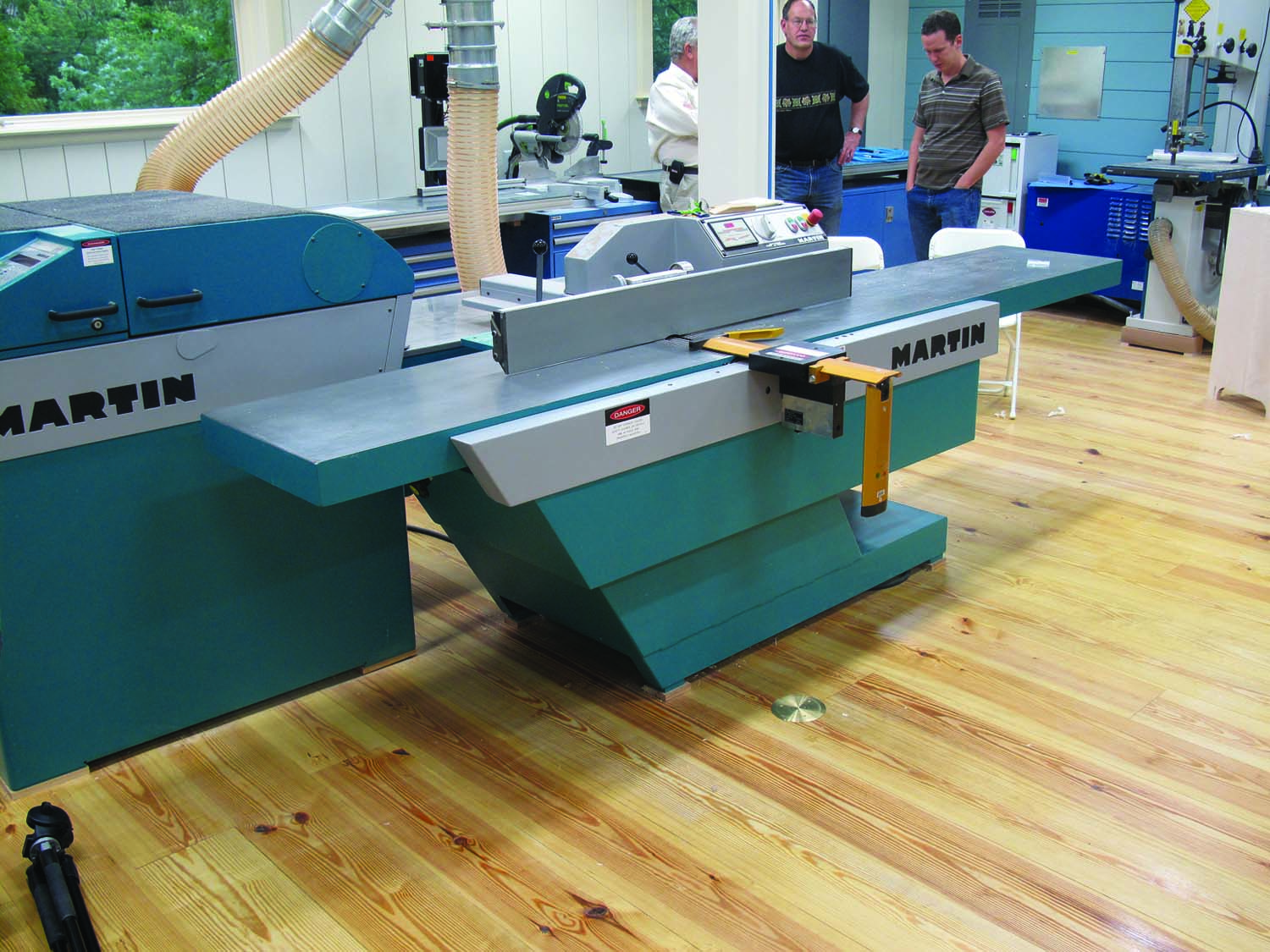
How wide? This Martin jointer can handle boards up to almost 20″ wide.
If you ever go to one of the big industrial woodworking shows, be sure to stop by the Martin booth. The company’s planer (which can handle almost 25“) boasts that it can remove up to 7⁄16“ of material in one pass. We were skeptical. So Adkins ran a thick white oak board through the machine. The Martin didn’t protest and the board emerged perfect.
The jointer handles boards almost 20“ wide, has a motorized infeed table and a SUVAmatic guard, which is remarkably different than the North American “porkchop” guard. The jointer begs to be used. And we obliged. It’s like having endless power and endless capacity.
Behind the major machines is the bench area, which looks out onto a garden through bay windows. Flanking the bench are two band saws, a small 24“ Agazzani band saw and the largest band saw I’ve ever seen in a home shop – a Zimmermann with a 31“ throat – a machine that barely vibrates when you power it up.
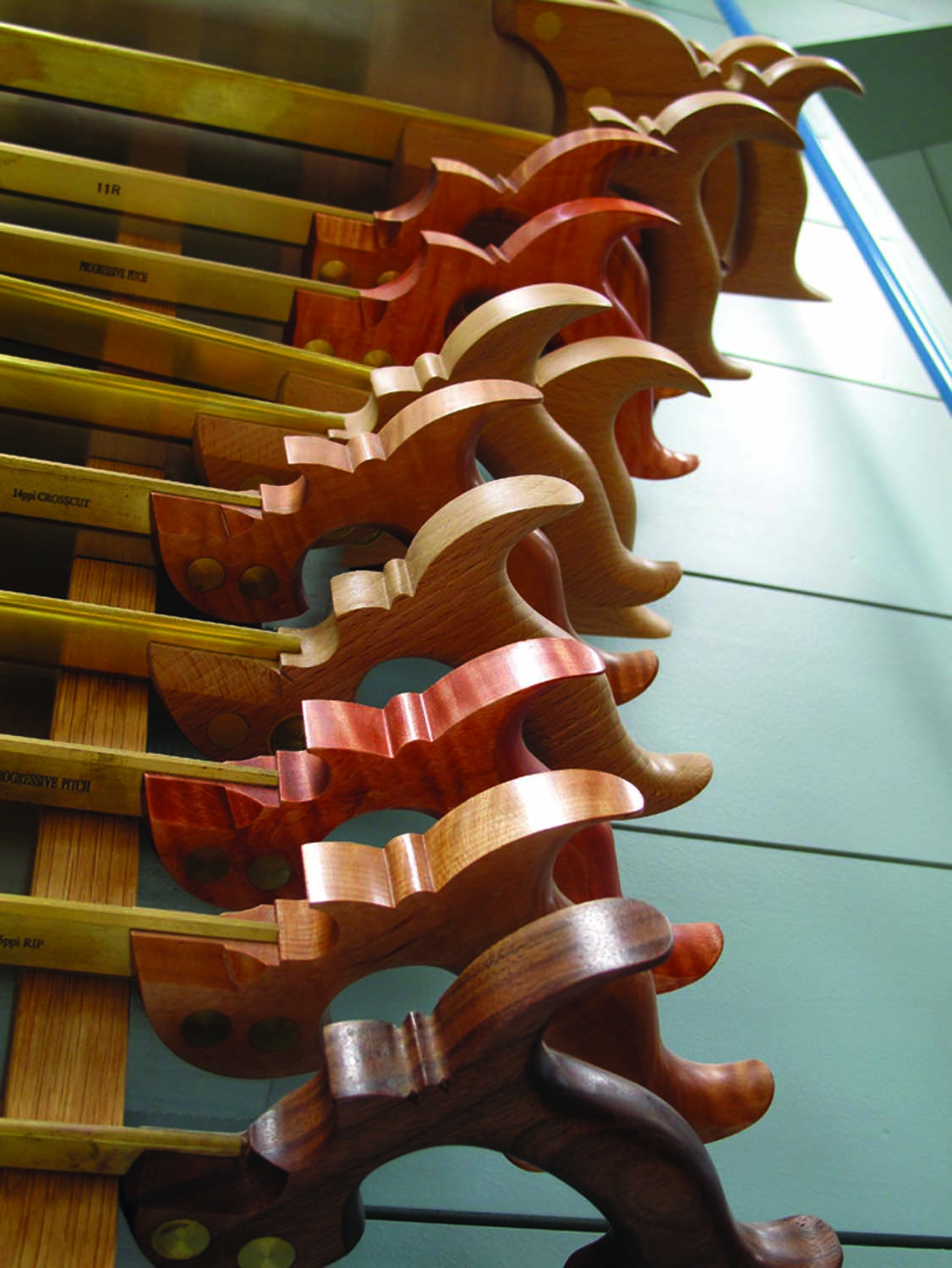
I saw that. As much as Adkins likes power tools, he also has a fine assortment of hand tools that he uses on his projects.
In the far corner is a Festool miter saw that is paired with a RazorGage system, which I had never seen before. Here’s how it works: Punch in the length of the stock you want, and the device moves the stop to that exact point. It’s also programmable to handle your entire cutting list.
The last major machines are a Kundig 43” wide-belt sander and a Maka mortiser, which uses a “swing chisel” to cut mortises and is impossible to describe with words. (We’ve provided a link to a video at the end of this article.) All along the walls of this corner of the shop are Lista storage cabinets filled with hand tools that are almost all French-fitted into their drawers, plus there is a dedicated area for sharpening hand tools here.
Above all these machines is a loft where Adkins stores his wood, plus the small remote-controlled crane that allows him to bring his material to the shop floor.
And There’s More

In the works. In the bench area are two dressers Adkins was building for his children. They were built using a combination of hand and power techniques.
The door at the far end of the shop leads to a smaller room that features a flat-screen television and video equipment that allows Adkins to watch woodworking videos while he’s not building in the shop. And off to the left of that is a nice bathroom with a shower.
A quick tour of his house shows that Adkins is anything but an armchair woodworker. His house is filling up with the the things he has built, from an enormous kitchen table based on Sidney Barnsley’s work to a cannonball bed he turned on his Oneway.
Since our visit last May, Adkins has kept in touch with us via e-mail, but these e-mails are entirely different than ones he sent us before. They are all photos of the work he has been churning out from his shop and the plans he’s drawing up for future projects. Adkins has turned his passion and enthusiasm toward his furniture work and away from the means to make it.
“Some people play golf. Some people collect fancy cars,” Adkins said while standing in his shop. “This is what I do. I make things.”
My day in his shop really made me rethink my own 375-square-foot shop at home. I built it 10 years ago but never finished off the concrete floor, cinderblock foundation or open stud walls. But last summer I vowed to change all that to make it a place as inviting as Adkins’s. I added a white oak floor. Drywalled the studs. Covered the cinderblock in beadboard and traditional moulding. And I painted everything with care. It’s a much nicer place as a result. And though I don’t have room for a crane, I can still dream about one.
Christopher is a long-time journalist and the editor of this magazine – but he’s wondering if it’s too late to go to medical school.
Here are some supplies and tools we find essential in our everyday work around the shop. We may receive a commission from sales referred by our links; however, we have carefully selected these products for their usefulness and quality.
Enjoyed the article but what happened to the slide show and links? Am starting design for a new shop and am interested in any information available on Dr Adkins shop. I really like the idea of making the shop nice looking to make it more enjoyable to work in. The equipment is impressive for a home workshop or a professional shop, I’m ready for some German equipment.