We may receive a commission when you use our affiliate links. However, this does not impact our recommendations.
Devon Campbell is designing and building world-class tools from his shop in Queensland.
Sometimes, the universe has a way of connecting the dots, whether you’re looking for it to or not. Back before the last Handworks Tool Show in the Amana Colonies, I was browsing some of the Facebook groups, seeing who was attending. Someone, and I apologize—I can’t recall who, mentioned that there was a last minute addition to the show, a company called Ironbark Toolworks. I recall seeing it, but I didn’t pay much attention, as there’s a lot of small tool makers that pop up once or twice and disappear. Little did I know that I would cross paths with Devon Campbell from Ironbark Toolworks, and want to share his story.
Tools From Down Under
Devon Campbell, the founder and owner of Ironbark Toolworks, started manufacturing and selling tools in 2020. Originally from Colorado, Devon moved to Australia to be with family, and has been exporting his tools from down under ever since.
Ironbark originally caught my eye at Handworks with their beautiful layout tools, unique spokeshaves, and edgy-looking block planes.
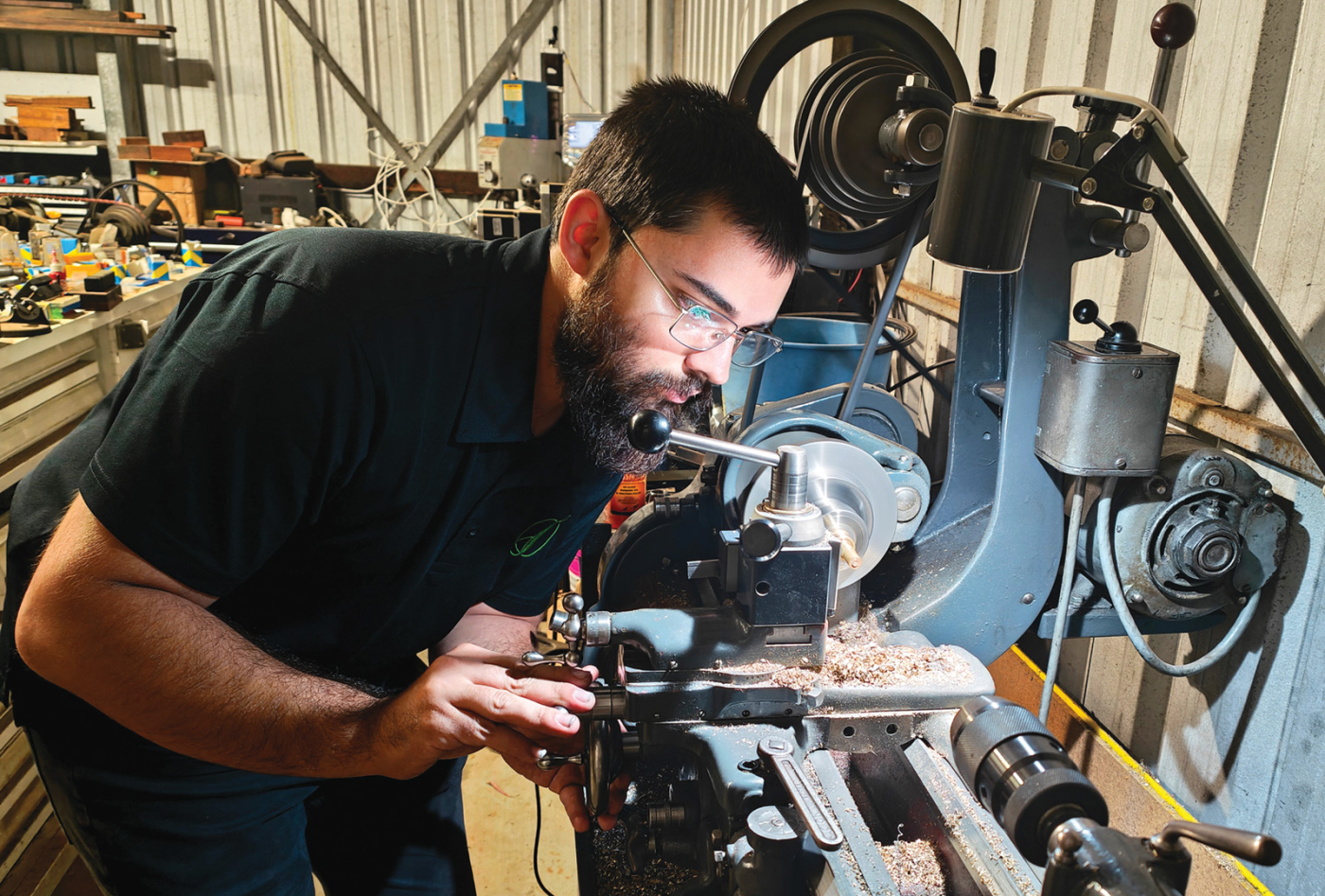
Devon Campbell spends his working hours hand making each and every tool that leaves the Ironbark shop.
How did you come to decide to build tools, and why Australia?
I developed a love for music as a young kid and that evolved into a curiosity about how instruments are made. In middle school, I would spend breaks with a guitar builder in my home state of Colorado learning how to make musical instruments. After graduating college, I found myself living in Hawaii, working at a cabinet shop.
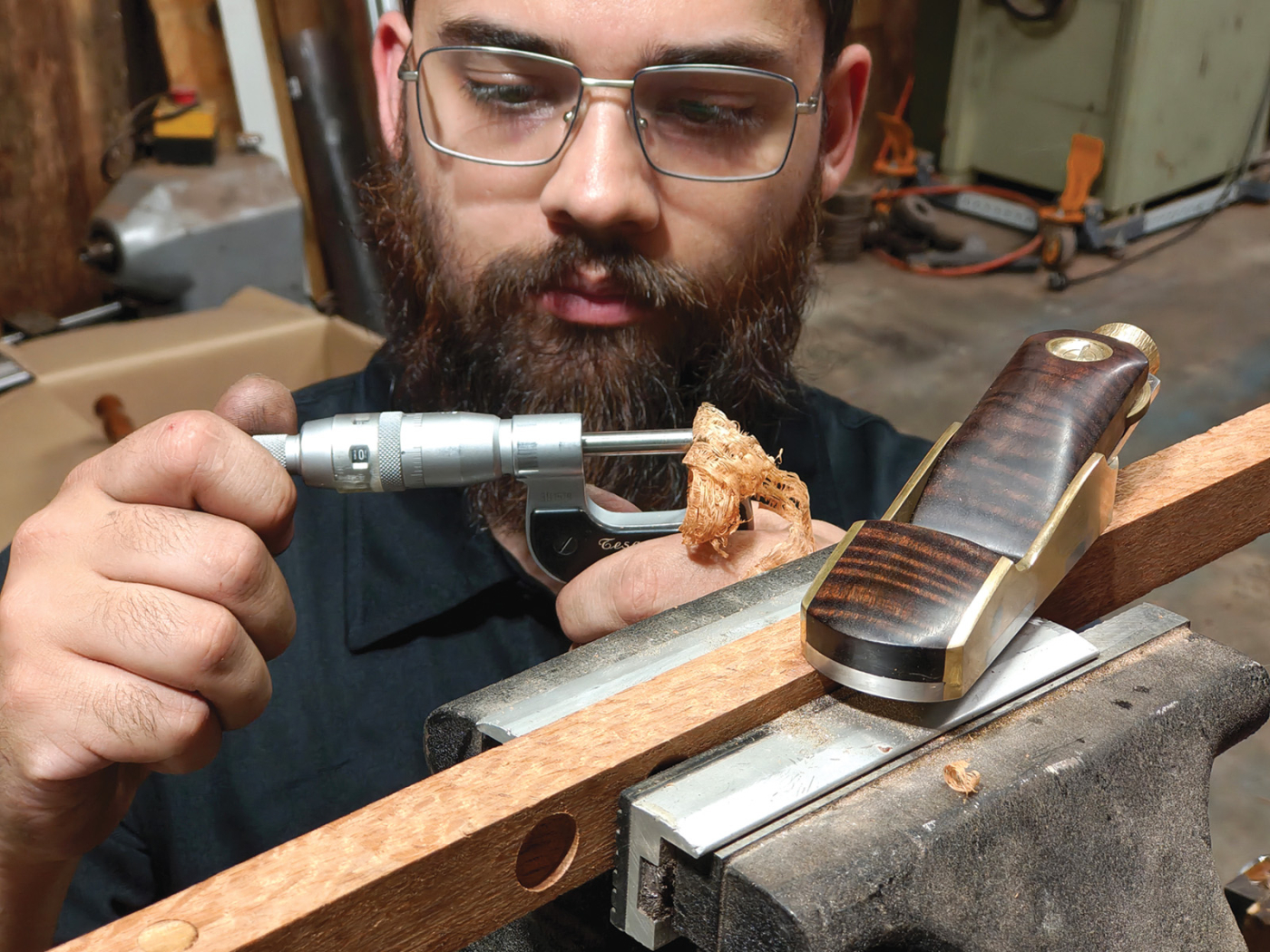
This includes the machining, sharpening, and testing of each tool.
My alone time was spent in my home shop, away from the noise of production machinery. Since my interests frequently came back to musical instruments, I would frequently find myself making jigs and fixtures to hold and work the organic and unusual shapes prevalent on a guitar, as well as the tools to work on them. Slowly, I found my interests pivoting more and more towards the tools as I realized that there is a wonderful community of people who shared my excitement towards them. I would drool over images of planes from Konrad Sauer, Tony Rouleau, and Karl Holtey. I gave it a few tries with varying levels of success, but my priorities at the time were still split between school, an uncertainty of my professional future, and my woodworking hobby.
A couple years later, I moved to Australia following my sister who had done her PhD there. I knew that I was interested in making tools and that there is a rich culture of tool makers in Melbourne. I was very fortunate to spend a bit of time with Chris Vesper and Peter Mcbride learning how to approach a tool as a piece of art and how to efficiently work form and function into a cohesive identity. During that time, I joined Carbatec, which is one of the largest woodworking tool and machinery retailers
in Australia.
I am very grateful for the time I had at Carbatec since it reinvigorated my belief that I could have a future in tool making. It informed me about the gaps in the market, and my salary funded my workshop and accelerated me into being able to make things that I had previously thought to be prohibitively expensive or impossible. My tool making dreams finally felt possible and I felt like I was up to the challenge, so I started Ironbark Toolworks and began marketing my own line of tools intended for woodworkers who appreciate how high quality and beautiful tools inspire high quality and beautiful work.
What made you want to build your own tools, and what do you see as a need in the community?
I wanted to make tools that are beautiful and collection-worthy while also being the practical, default ‘go-to’ tool for woodworkers of all experience levels. That’s a big task, but I thought that it was doable through clever design and a good understanding of all the expectations around a tool. My tools are designed to be easily maintained and repaired to ease any concerns of woodworkers who think they are too beautiful to use. They are made from modern materials to outlast and outperform their older counterparts, and they’re engineered to be efficient at their intended purposes without being finicky to set up or use. They’ve also been made using continually improved processes to reduce cost and achieve a price point within reach of woodworkers who know that these tools will be of use to them. To my knowledge, this combination of principles isn’t available elsewhere on the market, but they are the priorities that I look for in tools I buy and I believe those priorities are shared by my customers.
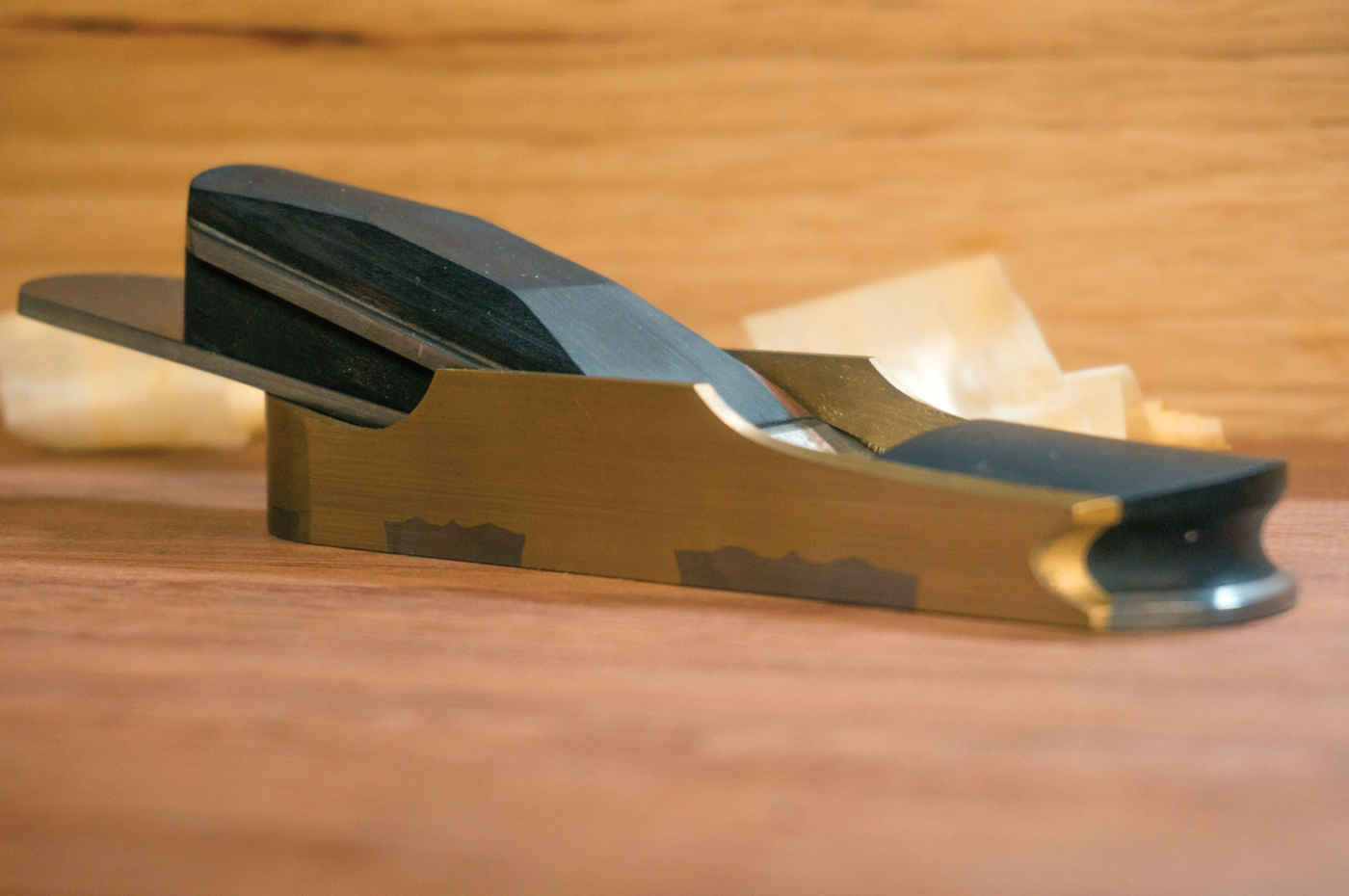
Devon’s block planes are edgy, yet somehow classic. They’re designed for an ergonomic feel as you use them.
What would you guess the future holds for Ironbark Toolworks? New Products and expanding the line?
Ironbark Toolworks is still a small company, but it has been met with a lot of support and encouragement that I’m on the right track. Since I started Ironbark Toolworks, I would regularly release new products and I expect that to continue. I have a plethora of tools in my mind that I feel I could make meaningful contributions to, so they will undoubtedly start trickling into my product offerings as I find the time to develop them and recognize their demand.
On the business side of things, I hope that I can grow the company and start hiring employees as sales become more predictable and frequent. Right now I am committing most of my time to my current product offerings to stay on top of orders, but I would like to spend more time developing new products and I think training an employee could help with that workload. I also think there is space for Ironbark to embrace longer term projects like developing machines. Ultimately, there’s no way to know exactly what the future holds, but I will make sure that everything I sell is up to the standards consistent with the rest of Ironbark’s offerings and that I respect the priorities of my customers.
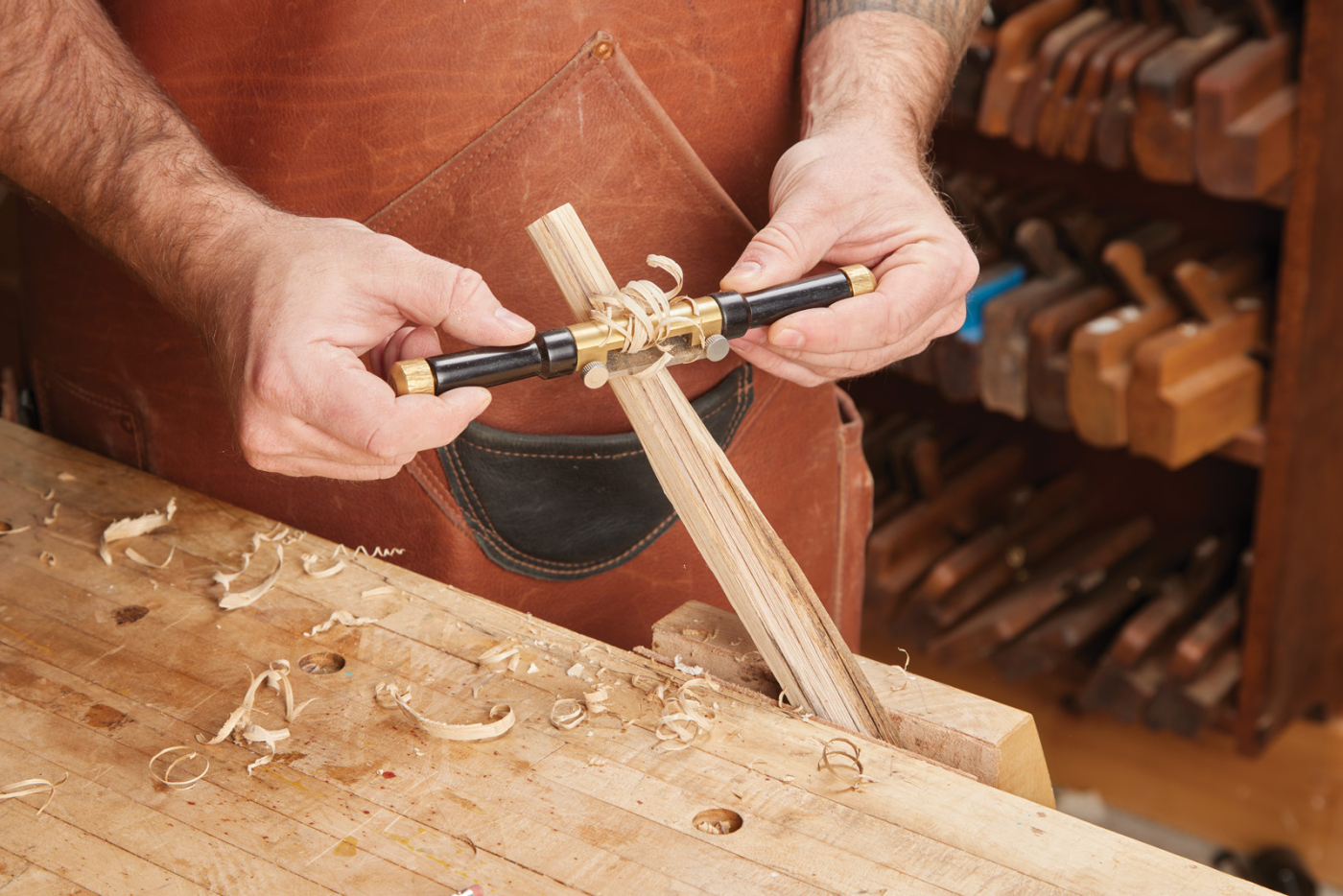
In use, the Ironbark spokeshave works similar to a cigar shave style spokeshave.
Editor’s Note:
Devon makes beautiful layout tools and hand planes. However, in my opinion, one of his nicest tools is his spokeshave. It’s one that you need to really hold to understand how it’s different. You can see it in the photo above and the exploded view below.
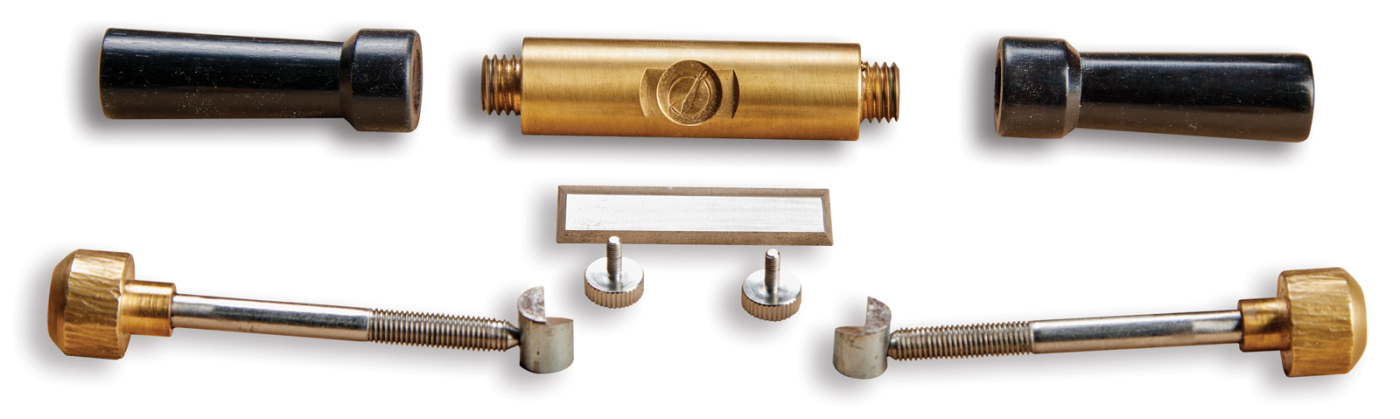
An exploded view of one of Devon’s original spokeshaves shows the blade capture mechanism, as well as the immaculate machining.
The Ironbark spokeshave differs from traditional shaves in a number of ways. In form, it more closely resembles the old “cigar spokeshaves”. However, the blade mechanism is different. The brass knobs on the ends of the handle engage with pillar blocks embedded in the body. These dovetailed blocks lock on the edge of the blade to really lock it in place. The blade depth mechanism is simply two knurled thumb screws that rest on the back of the blade. As an owner of more spokeshaves than I would admit to, I believe it’s probably my favorite.
Ironbark Toolworks are available both on the Ironbark website (IronbarkTools.com.au), as well as from Leslie at Heartwood Tools (HeartwoodTools.com).
Here are some supplies and tools we find essential in our everyday work around the shop. We may receive a commission from sales referred by our links; however, we have carefully selected these products for their usefulness and quality.