We may receive a commission when you use our affiliate links. However, this does not impact our recommendations.
In Conversation with Plane Maker Karl Holtey.
Editor’s Note: This article originally appeared in the December 2020 issue of Popular Woodworking Magazine.
In 2015, acclaimed hand plane maker Karl Holtey announced his impending retirement and was working on the 984 panel plane: what he intended to be his final production run of hand planes and the last word in a career that resulted in a reputation for an unwavering focus on perfection and the development of several technical innovations that had an impact far outside the boutique world of high-end hand planes. Karl and I spent several days that autumn in his workshop in rural Scotland talking about plane making and his journey to becoming widely recognized as one of the greatest plane makers in the world, an interview that can be found in the April 2016 issue of Popular Woodworking.
Now it is 2020, much of the world is several months into lockdown as a consequence of the Covid-19 pandemic, and Karl recently announced his latest design—the 985 smoothing plane. Wait a minute: surely he retired in 2015? Apparently not, and in late December 2019, Karl quietly appeared on Instagram under the handle @karlholtey, offering an insight into his manufacturing process. Word soon slipped out that Karl Holtey was still making planes.
An Unusual Retirement
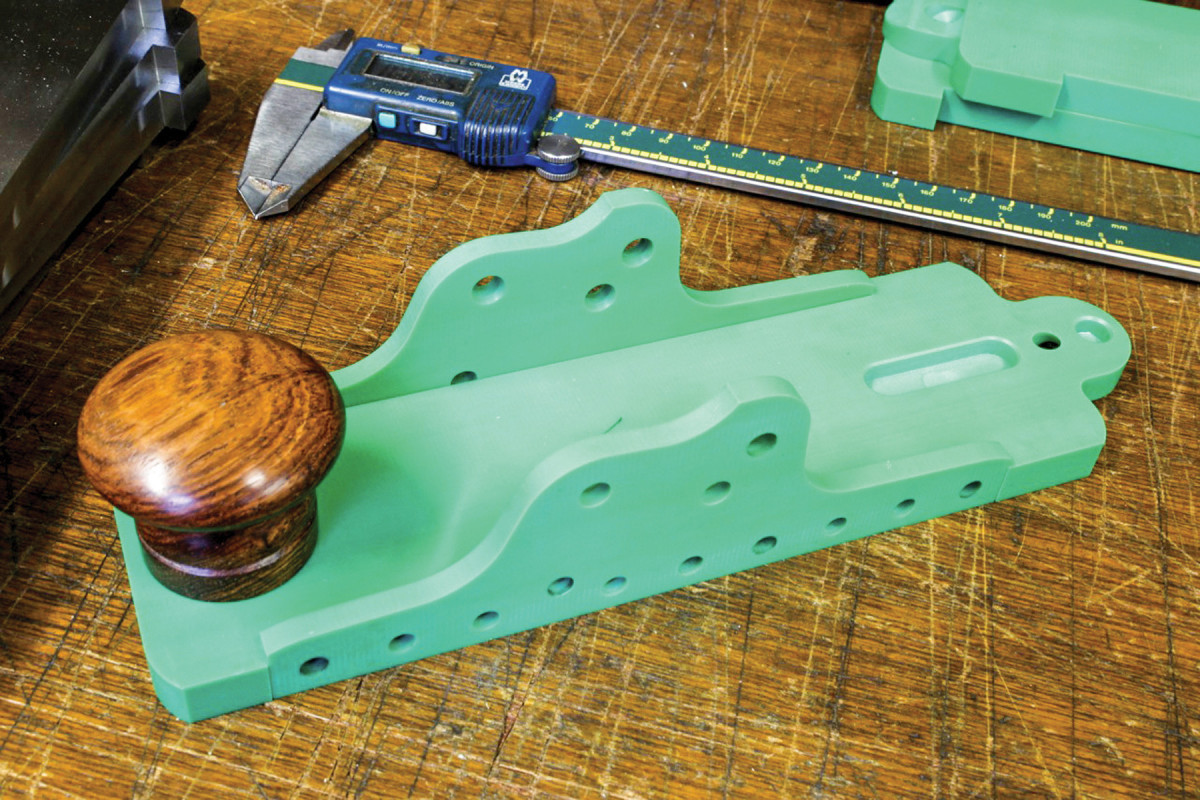
1. Plastic prototype for the 985 smoothing plane.
In the five years since we last spoke, Karl concluded his run of 984 panel planes, and then produced a second run of the 983 block plane. His motivation in revisiting the 983 was that he had sold the final plane from the initial run and did not have one for himself. Instead of making a one-off, he decided to do a full production run, a decision that he would not repeat. “I forgot how much work was involved in a production run,” he explains, “I prefer to do smaller batches now that I’ve retired.” Despite the birthing pains of that second batch of 983 planes, all but one plane has now sold.
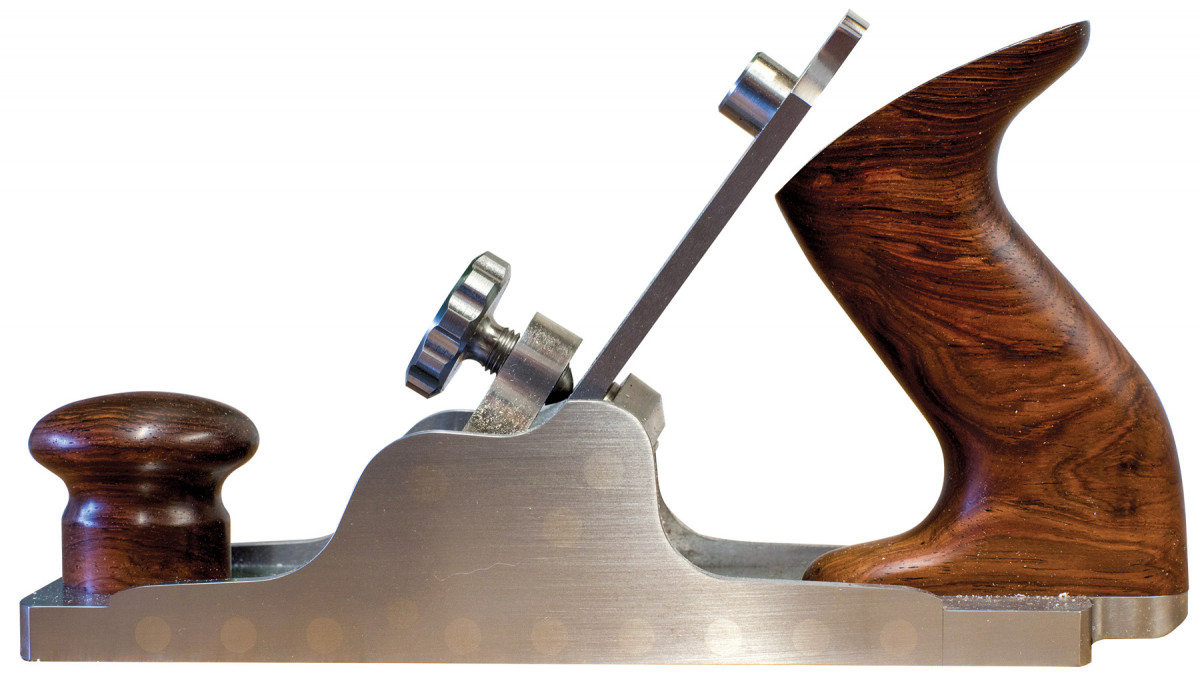
2. The 985 is an exercise in simplicity with no chipbreaker or adjuster. The tote is angled forward for increased comfort.
In fact, Karl’s retirement has been marked with an enviable rate of productivity, and he shows no sign of slowing down. Instead, retirement seems to represent a change in how Karl approaches his plane making rather than in ceasing work. “It has allowed me to do things and explore designs that I didn’t have time for before,” he explains, with the focus on smaller batched work “taking some of the pressure off.”
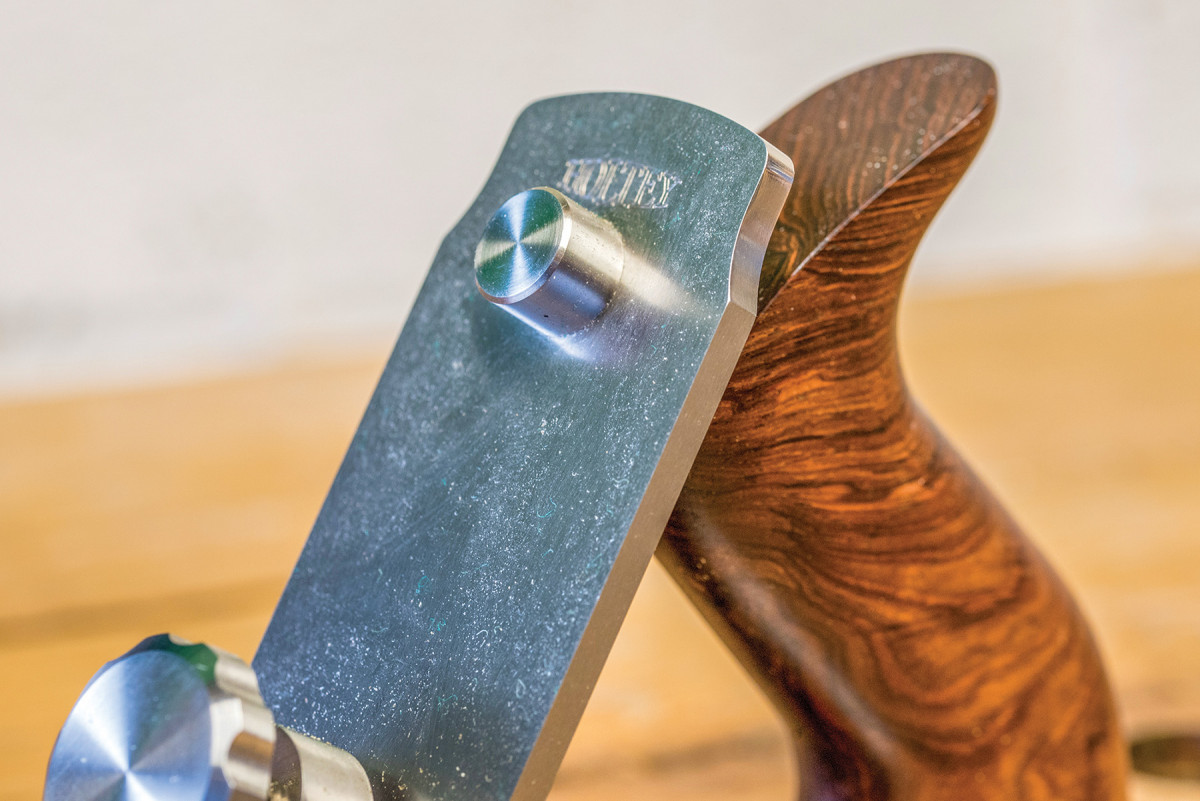
3. Depth of cut and blade orientation is adjusted by the setting post.
This change in outlook has not dulled Karl’s creative drive or pursuit of the perfect hand plane. So, what keeps him in the workshop making planes during retirement? “Vanity. I’m a naturally competitive person, and I love being the best at what I do,” he says. “I can’t explain, it has always been there. If I have an idea about making something, I can be very driven to make it.” The interest in hand planes he attributes to his apprenticeship as a furniture maker when he became frustrated with the tools he was using. And at 71, he still finds himself thinking through new designs and approaches constantly: “I’m fabricating planes in my head constantly,” he tells me, “when I’m walking the dogs, driving, just living.”
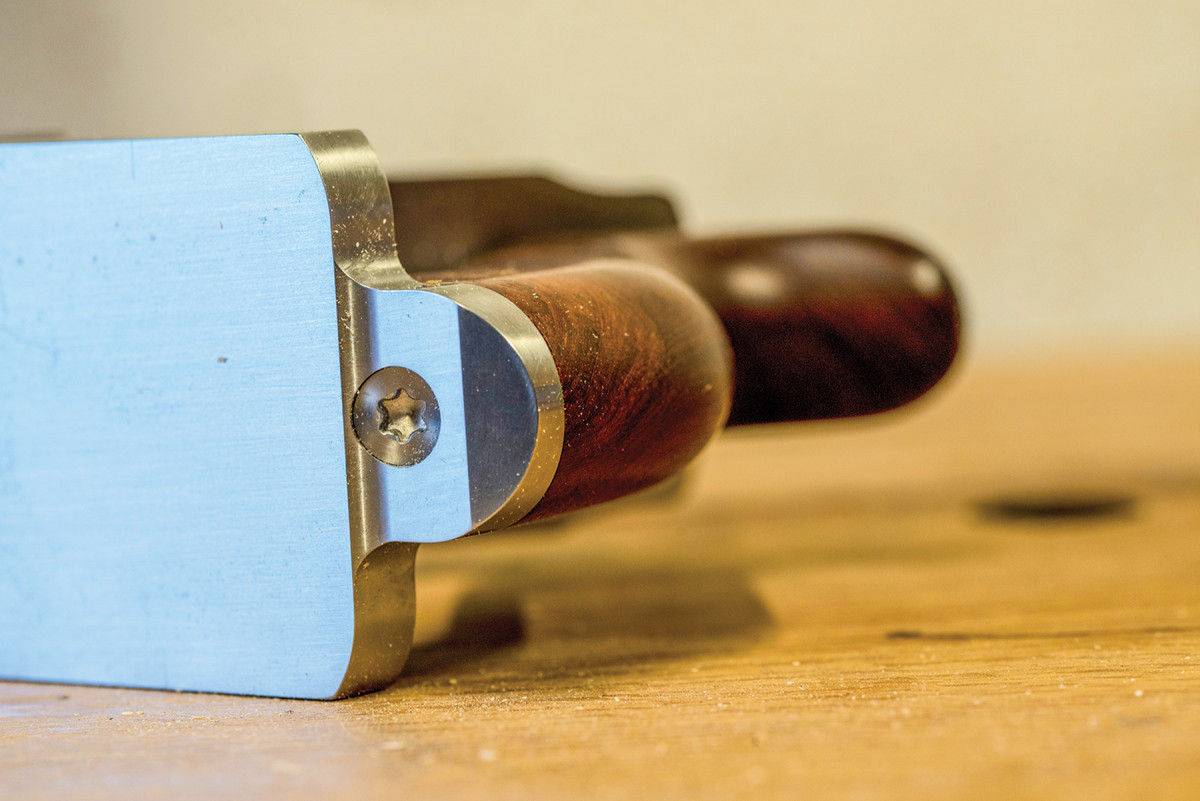
4. The rear tote is fixed in place through the underside of the sole.
Following that second batch of the 983 block plane, Karl made a run of six of the 984 smoothing plane, revising the design as he did so. Dubbed the 984s, this batch was initially to use up a collection of spare handles and components, but Karl could not help but revise the design to create a new twist on his celebrated bevel-up panel plane. Originally a 13 5/8“ long plane, the 984s features a shorter 12 1/2“ long body and omits the striking chamfering of the original. Says Holtey, “I just love it like that. I don’t want to put the original No 984 down but leaving the chamfering off makes it look very much more serious and business-like. I am changing my ideas about some of the decorative side of the work.”

5. The setting post allows the blade to be adjusted in any direction.
In terms of new designs, he has plans to make new types of planes but nothing that he is yet ready to share with the outside world. As a plane maker that started out building replicas of celebrated Norris infill planes, much of Karl’s career has been spent trying to mitigate the effects of wood movement within metal plane bodies, a design problem he is returning to with his new planes. As he explains, “I am trying to think of new designs where I can incorporate more wood without compromising the stability. Wood sells all by itself and people don’t get excited by metal work or engineering. I have been experimenting on my Instagram postings to see where I get the most likes.”
985 Smoother
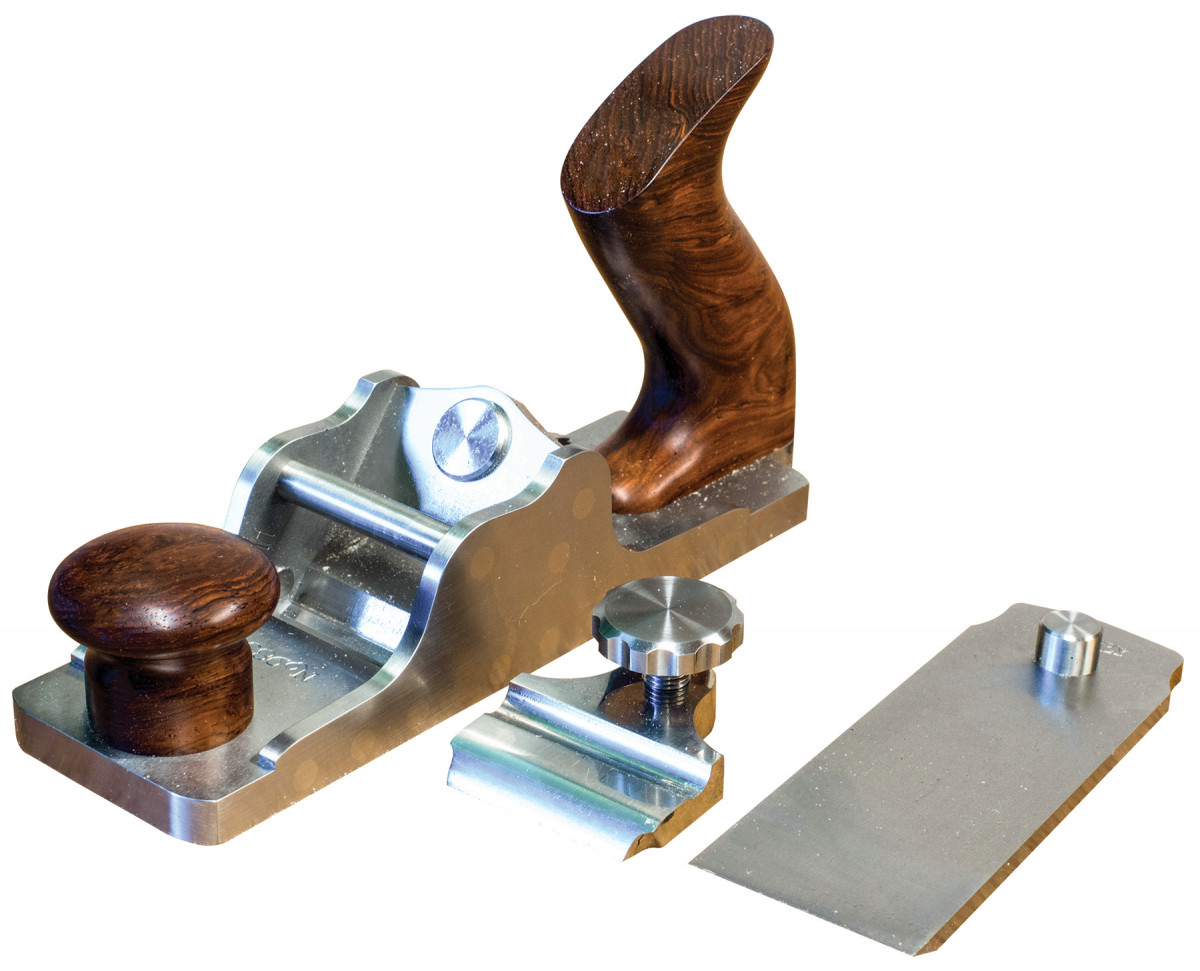
6. The disassembled 985.
The 985 represents the first brand new design of Holtey’s retirement. When asked about the origin of the plane, Karl explains that it started as “a tiny little idea in the back of my mind. I borrowed the basic shape from a Spears plane. I drew it out several years ago and was blowing hot and cold about the design. I wanted the plane to be as short as possible—a smoother doesn’t need to be long. A lot of historic smoothers are 71/2“ long, but that was compromising too much on the handle and bun area. The whole design process was about seeing how small and short I could make the plane. I couldn’t have an adjuster and keep the length down, nor was there enough room to fit a traditional sneck to the iron.”
The 985 is one of my best. I like it very much. The 7 7/8” long smoothing plane features a 11 5/16” wide blade bedded at 54˚, with no chip breaker or adjuster, and comes in either stainless stool sole with brass sides or stainless steel throughout. -Karl Holtey
Designing within those parameters led to one of the most striking features of the plane—a setting post set into the face of the blade. “I was getting the idea that some people expected a Holtey plane to have an adjuster,” he says, “so as an afterthought, I decided to put in a setting post on the blade to be tapped with a setting hammer. I am more excited by this plane than any others that I have made. For example, the No 983 was an innovation and the No 985 is just a simple plane I just love to bits.”
The setting post can almost be taken as a microcosm of Karl’s work—at first glance it is an incredibly simple feature, but behind that simplicity lies a great deal of work and problem solving. The fitting for the post is cut only once the blade is hardened to 62 Rockwell, which requires special tooling. To ensure that the post remains fixed, the mounting is countersunk and peened into the blade.
The plane also features some other subtle but significant design details. Firstly, the bed of the plane prevents blade from protruding more than 1mm, preventing the blade from dropped out of the plane. Secondly, the rear tote has a subtle forward tilt compared to many planes, which results in a more comfortable grip and less flex in the user’s write. The rear tote is secured in place by a substantial steel spine which is 10mm at its thickest, meaning that the handle is, according to Holtey, “bomb proof.”
Design Process
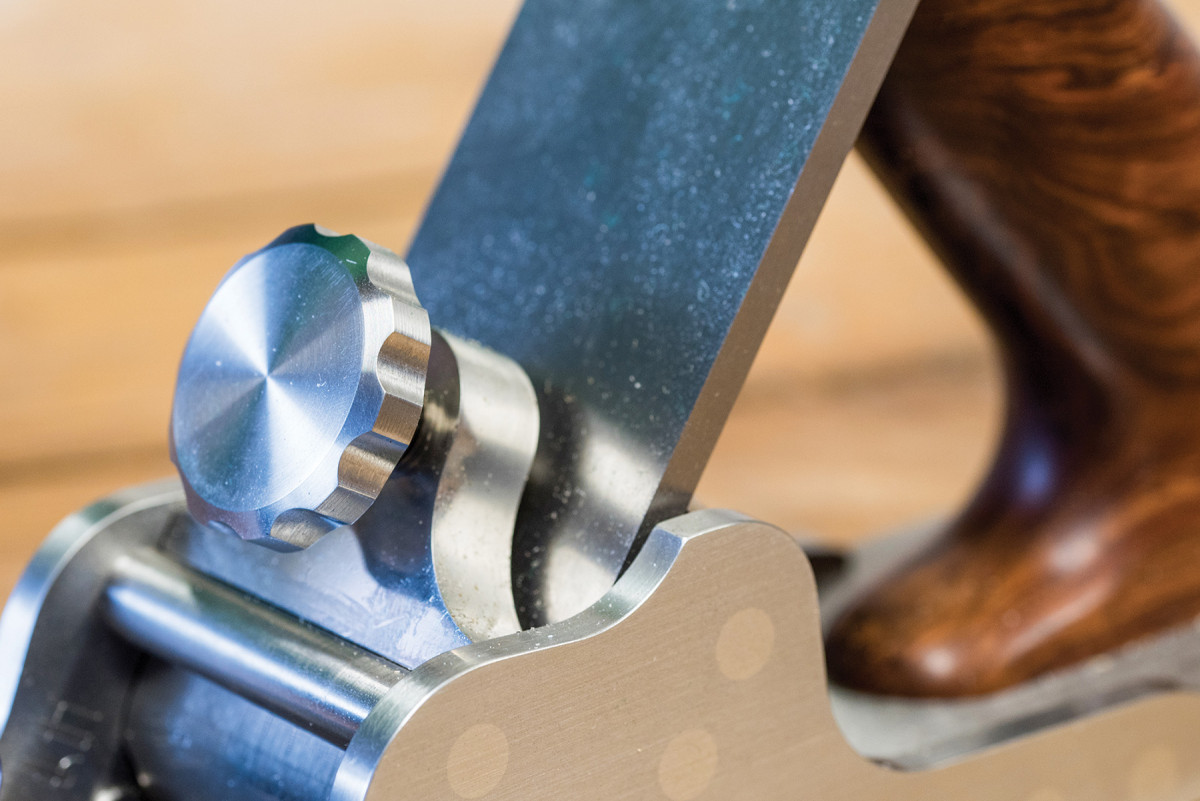
7. The 985 echoes the art deco stylings of previous Holtey planes including the 984 smoother.
Karl’s career has been marked by a strong aesthetic element to his designs, which is heavily influenced by art deco design, and by pioneering revolutionary designs which have filtered down to production planes. Notably, it was Karl’s 985 smoother, which rescued bevel-up planes from a nearly forgotten evolutionary cul-de-sac and proved their functionality, resulting in the widespread use of bevel-up planes by many woodworkers.
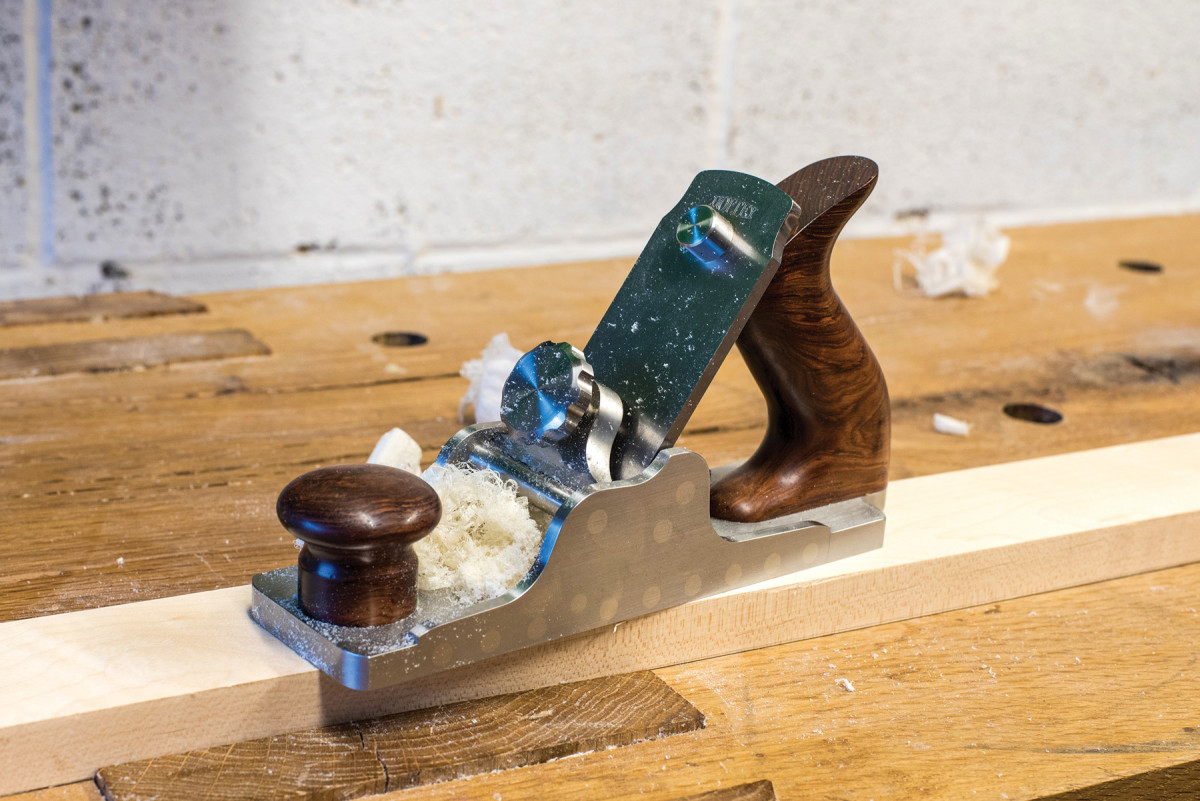
8. The 985 at work smoothing a piece of maple.
So how does Karl approaches designing a new plane? “I like simplicity,” he says; “it has to be functional, and I want to create the effect of precision at a glance.” Alongside functionality, “the look of a plane is incredibly important—it has to have a ‘wow’ factor.” How Karl approaches the “wow factor” is the use of exotic timbers or striking synthetic polymers for totes and knobs. “When I go to design a new plane, I’m looking for ways to introduce more wood to it,” he comments, as particularly on Instagram, “people respond to pictures of pretty wood, not to explanations of the technical processes and engineering that go into making a plane.”
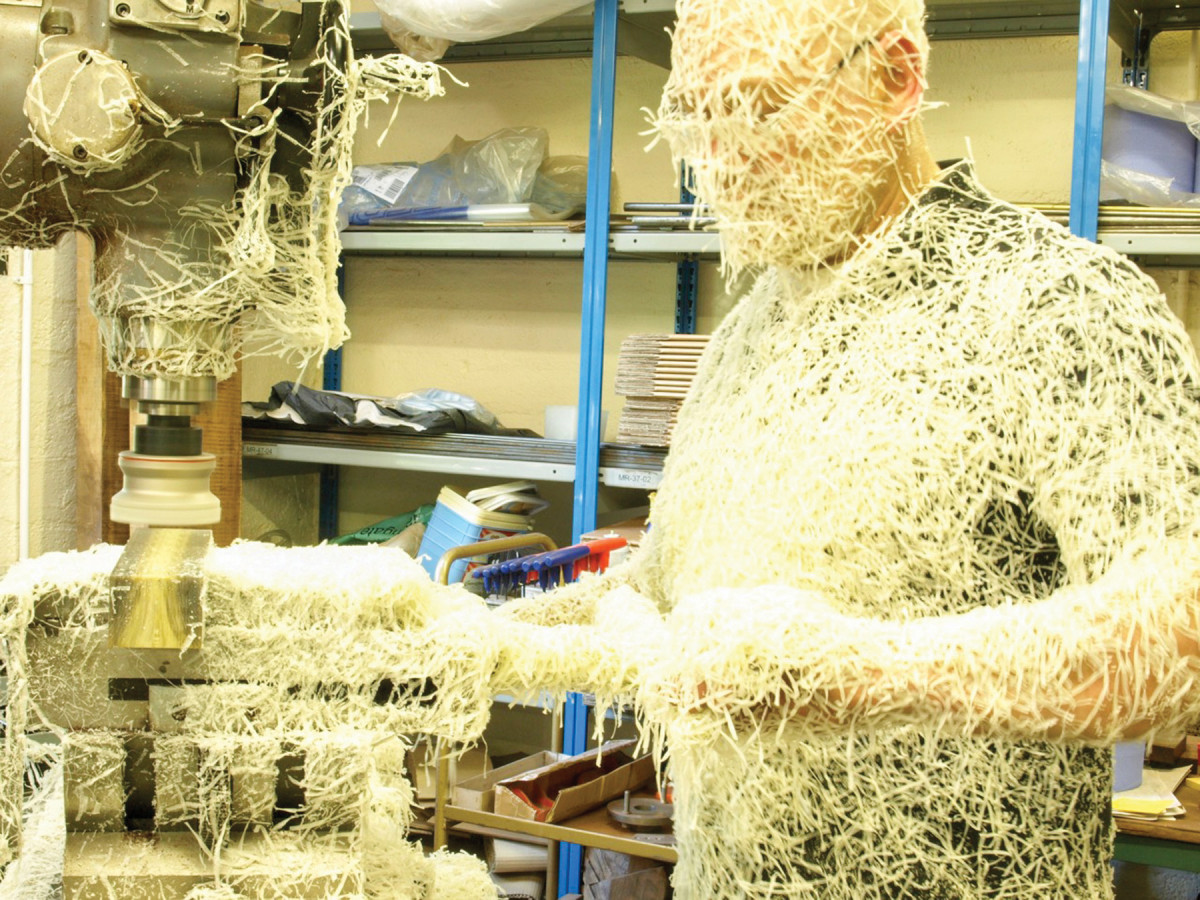
9. Holtey milling synthetic polymer for plane totes. It’s a messy part of his process.
On the technical aspects of design, he is very matter of fact, explaining that plane design “is not really rocket science. I look at things in more detail than what has gone before,” and taking a new approach to problem solving and design: “I think I like to go to places where people haven’t quite been. I’m reinventing the wheel, but in a way that other people haven’t done.”
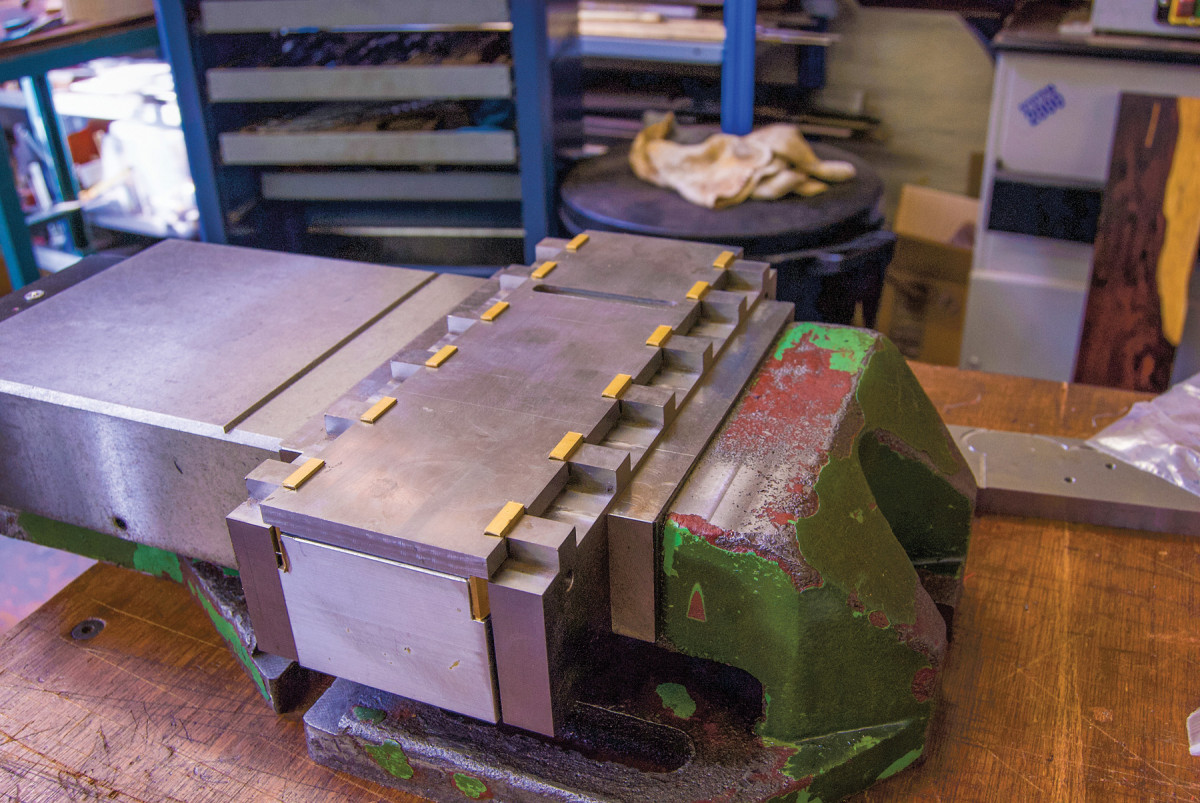
10-11. Peining the dovetail joints locks the sides to the sole of the plane.
So once Karl has decided the type of plane, and what the “wow factor” will be, he then decides what type of adjuster he will use, before drawing on aspects of old planes that he likes. The design process usually involves many hours spent at the drawing board; he says that he cannot afford to make iterations of prototypes and so he focuses on getting the design perfect on paper before moving to the workshop.
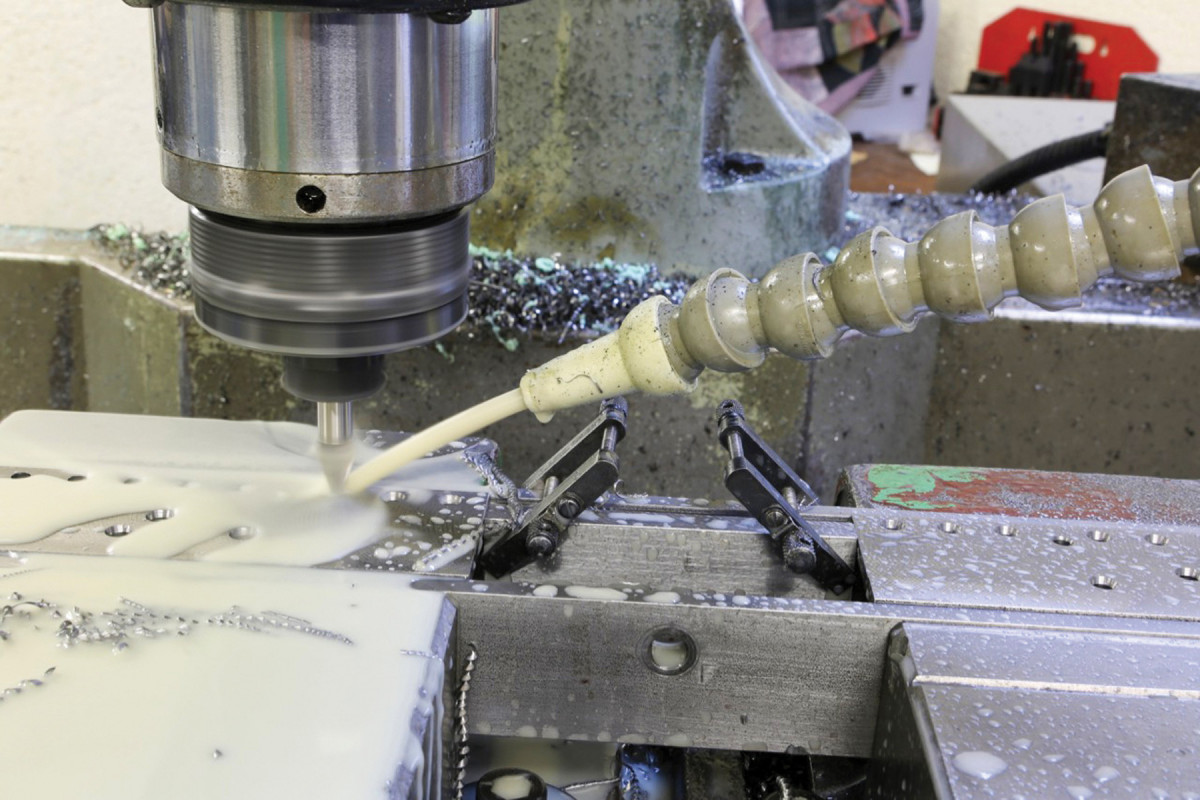
12-13. Cutting the integral rivets on his milling machine.
What does perfect mean to Karl Holtey, a maker who is renowned for a relentless focus on technical perfection? “When I find it, I’ll let you know,” he chuckles, “I don’t think its achievable. All you can do it try to be more perfect than anyone else.” In terms of his strong aesthetic style, Karl says, “Design is an interesting thing because everyone has different taste. And it’s hard to find an equilibrium to please everyone. I love to look at interior design. All of my inspiration comes from the past. Talent has been around for a long, long time, and I am just a newcomer.”
Advice for the Next Generation
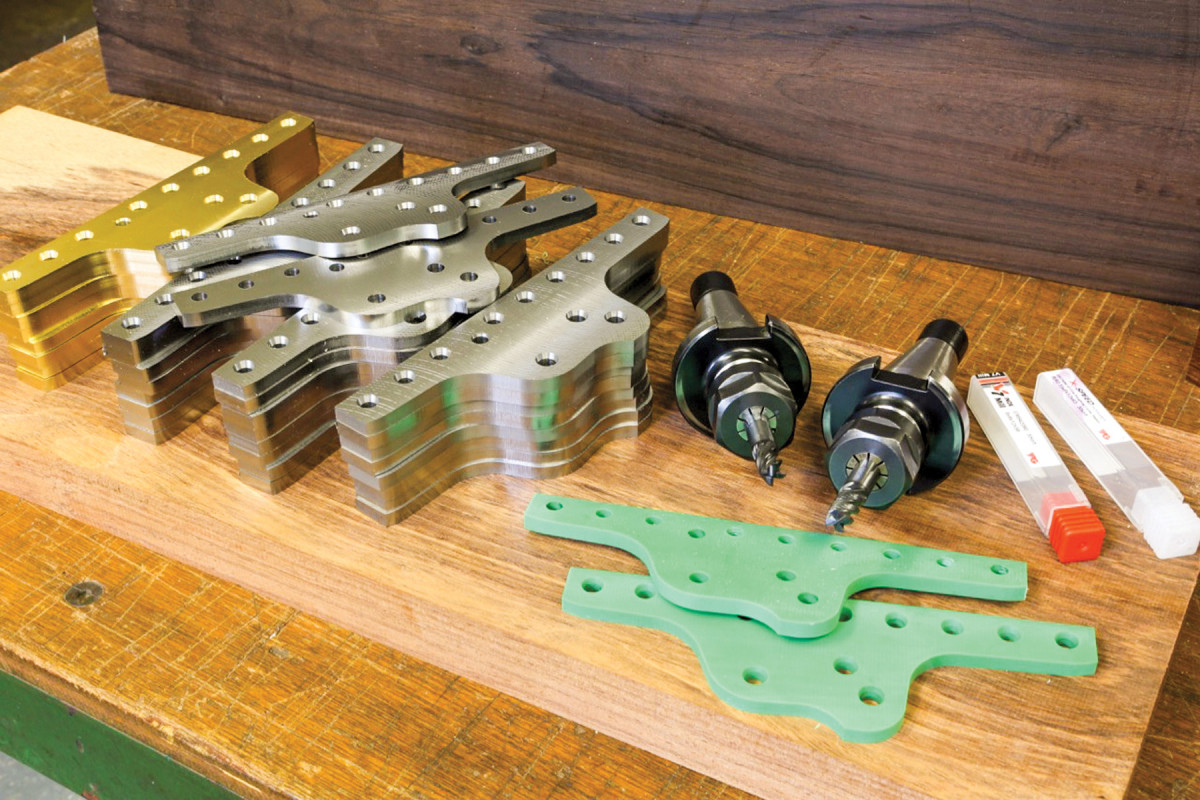
14. Some components of the 985 smoother with plastic prototypes and milling tools.
Karl Holtey offers a unique vantage point from which to discuss professional plane making. When he first started making reproductions of Norris infill planes, the only other British plane maker was Bill Carter. Since then, he has seen (and in many ways inspired) the growth of the boutique plane market. So what advice does he have? “You don’t have to be mad to do this, but it helps a little,” he laughs. “It’s not an easy life, but if you set your mind to where you want to go, there’s probably no stopping you.”
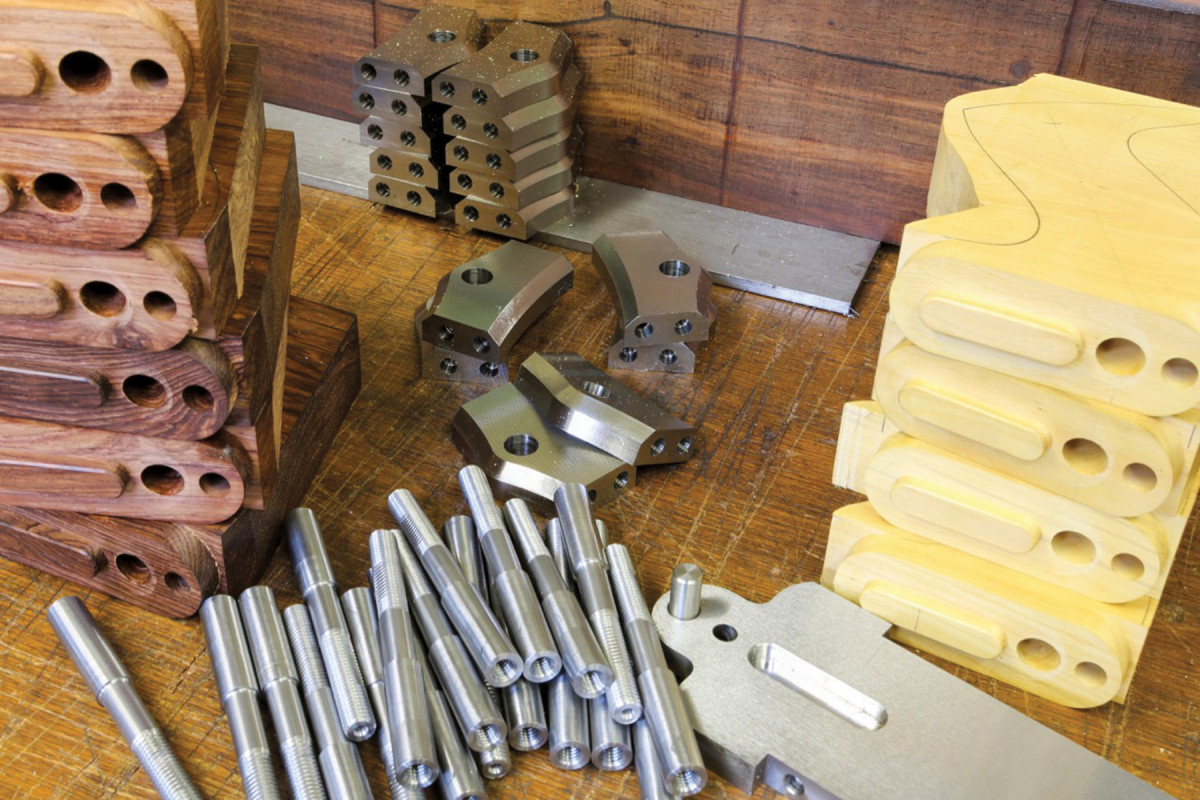
15. Boxwood and rosewood totes and the substantial stems which fix them to the sole.
In terms of the right temperament for a plane maker, he says, “In my early days as a furniture making apprentice, I was more interested in learning and my work than I was in earning money. And that counts for a lot. You have to be that kind of person. You have to be dedicated.” As for appropriate skillset, Karl considers that to be a plane maker, “You need an engineering bias, a good knowledge of engineering and woodworking machines, and you need to be good with your hands. It is not all machine work.” But the “most important thing of all is you need lots of insanity. Then there is the cost of acquiring the equipment and reasonable working space. As well as all this, you need to be able and find the time for sales and marketing along with the personality to do this.”
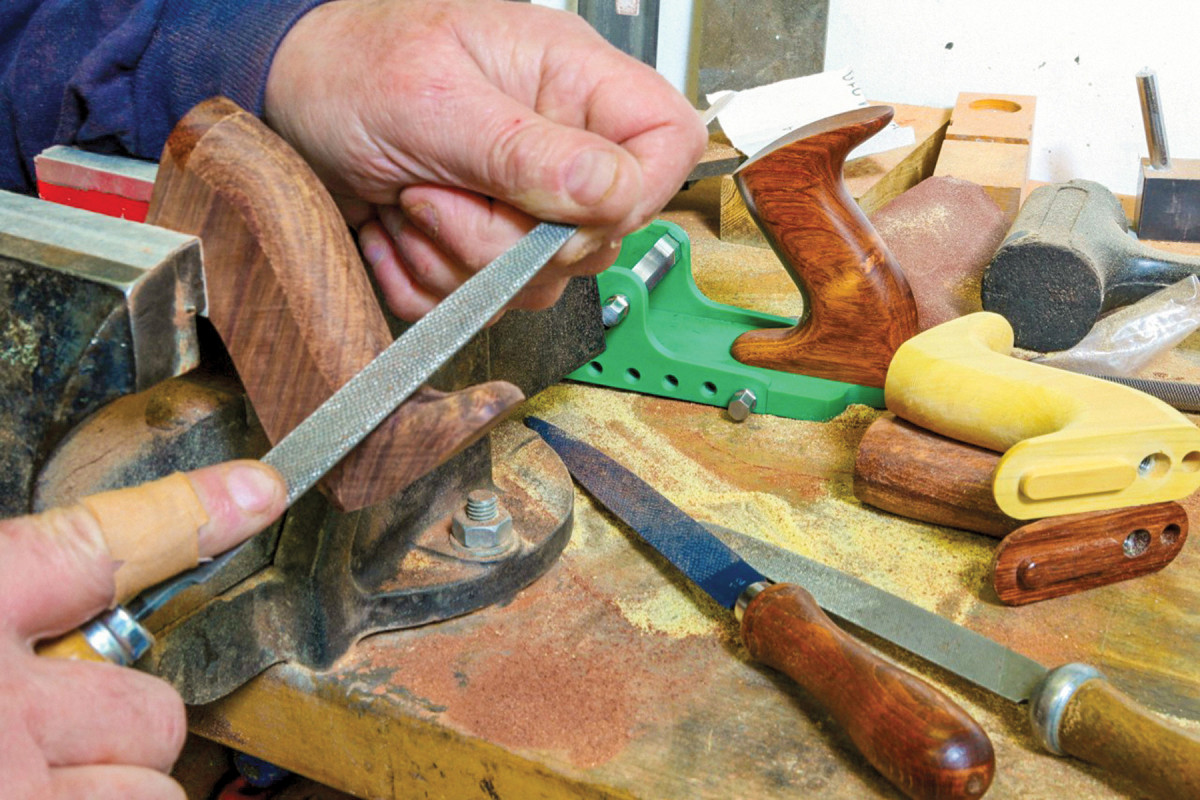
16. Final shaping the totes is done by hand.
Those not familiar with metal work might be surprised to find that actually working on a plane body is not where the majority of Karl’s time and effort is spent. “The main skill and most of the work involved is making fixtures to make and hold the work,” he says. “Workholding solutions, and problem solving, take a lot of my time.”
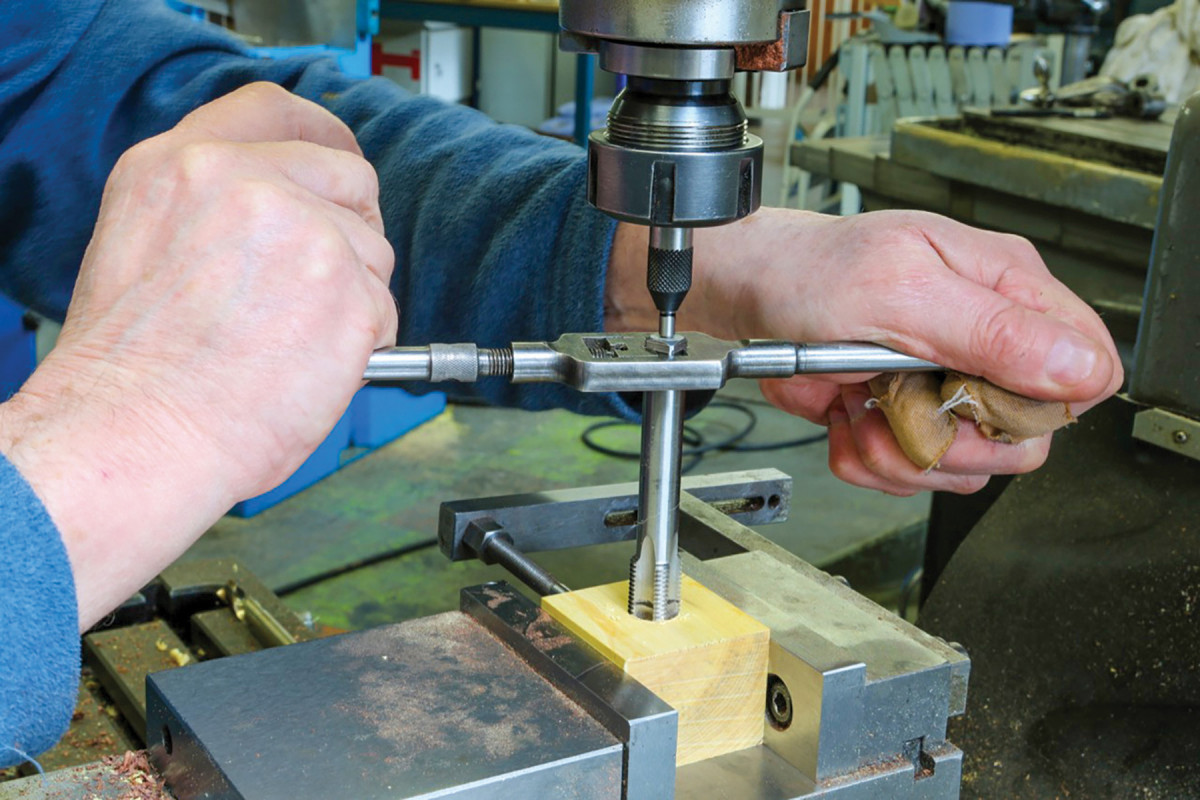
17. Tapping the thread in boxwood for the front knob.
And while he has incorporated CNC and other machine tools in his manufacturing process, Karl still considers his planes to be handmade. “People think that the CNC is the proverbial Heath Robinson gadget,” he tells me. “They think you press a button and a block plane drops out.” But that is far from reality.
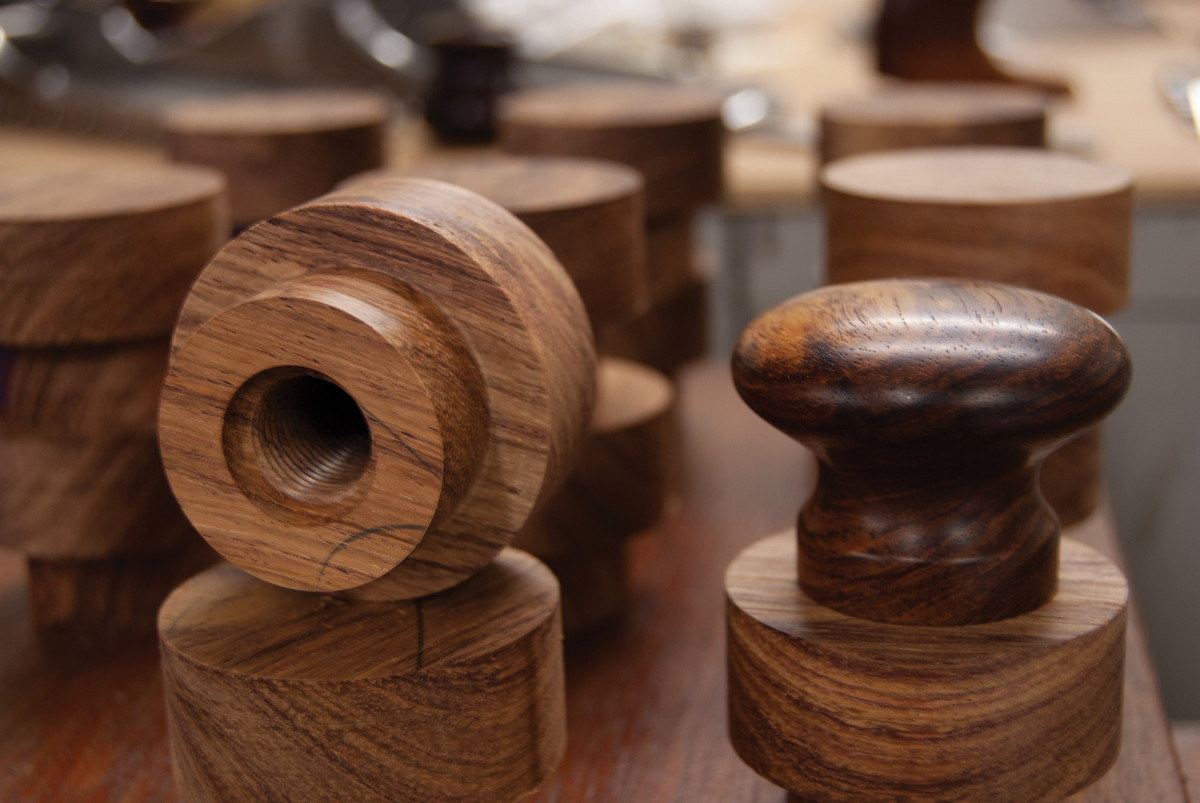
18. Rosewood knobs in their preliminary milled shape, and one in its final form.
The benefit of incorporating CNC tooling, Karl has found, is repeatability—spare parts in his stock will fit any plane of the model he built it for. But despite the use of CNC, a great deal of his time is still spent doing handwork on the fine details of his planes, such as polishing the swooping body chamfers on the 984 panel plane (which he says can only be done by hand).
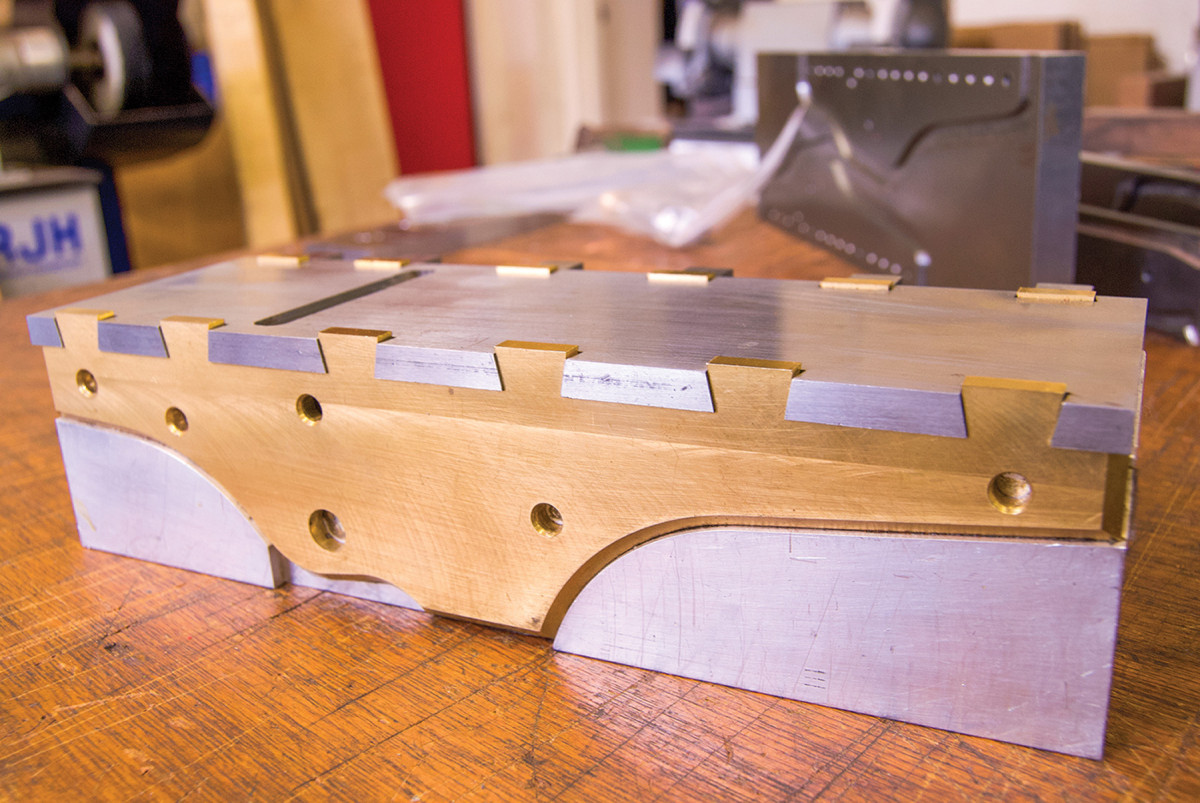
19-20. Devising work holding is where much of Karl’s time is spent. This fixture holds a plane body for peening the dovetails.
Shaping plane totes is also largely done by hand, and the result is a supremely comfortable tote that supports the hand through extended use. “It’s all the little details,” he says. “It just goes on and on.”
What’s Next
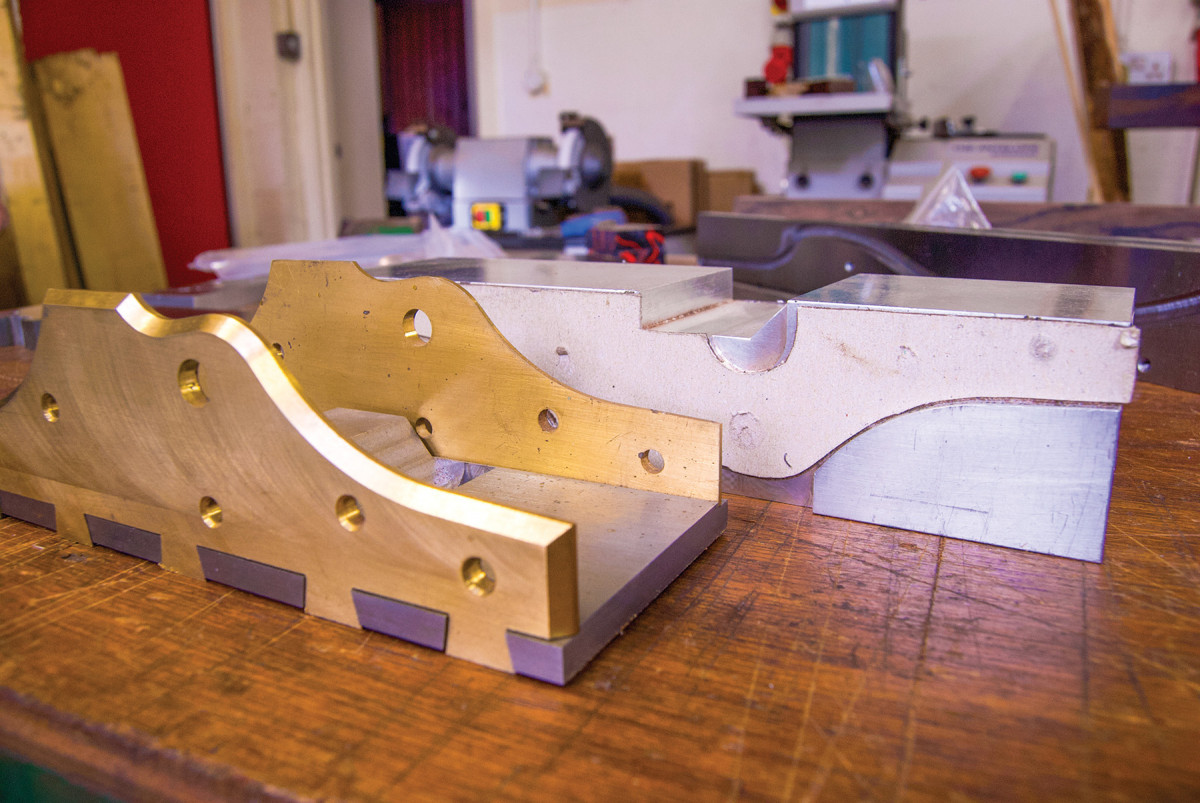
21. A finished version of Holtey’s Norris-style A28 Chariot plane.
Despite retiring, Karl seems to show no sign of slowing down. “I want to be making planes for at least another 10 years and am looking at different approaches and designs.” At some point, he also hopes to find some time to build furniture.
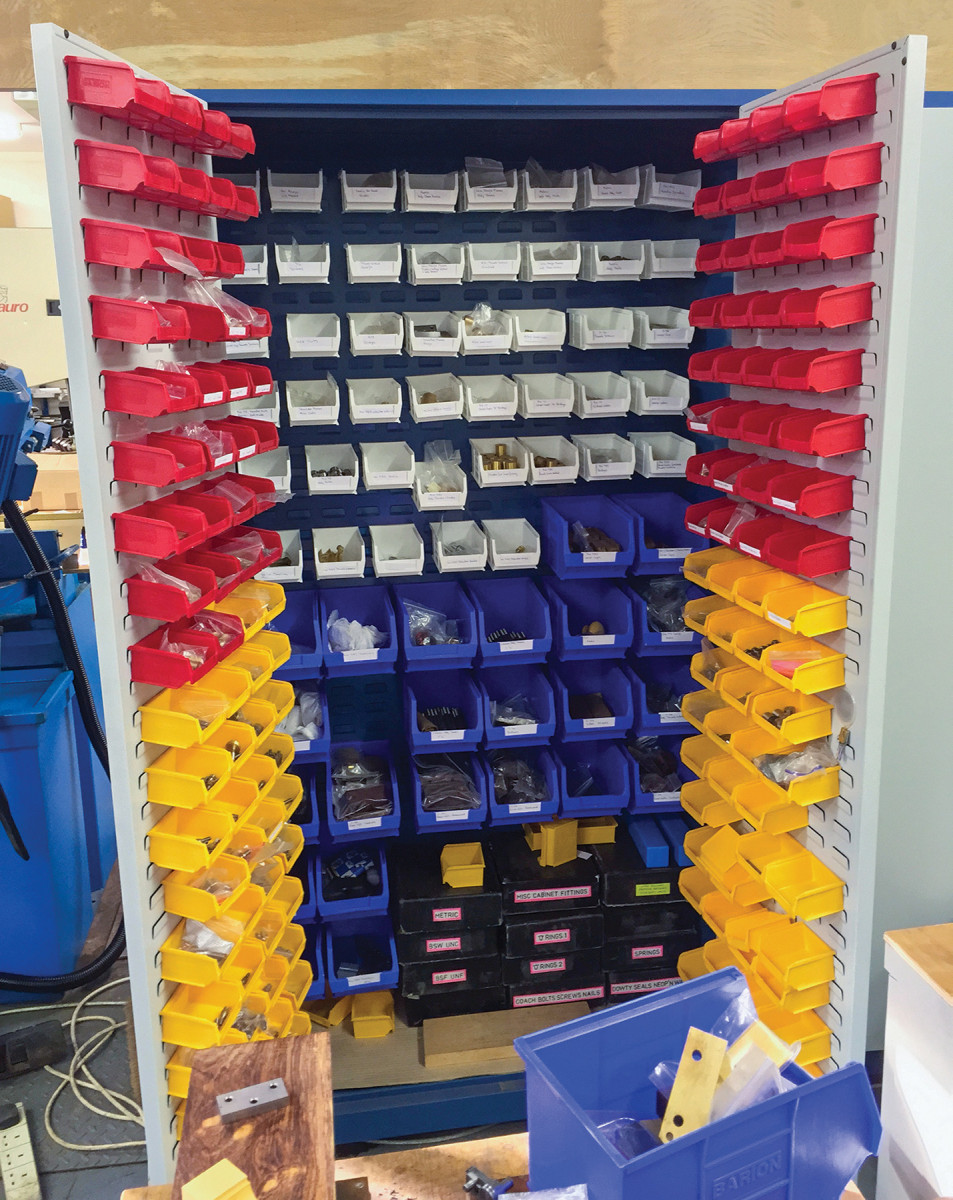
22. Karl’s component store contains parts for many of his planes. The benefit of CNC machining he tells me is that parts are guaranteed to fit any plane of the correct model.
“I miss my days working with wood. I’d like to do some Chinese dynasty style furniture, and a Barnsley Hayrake table—that is a piece I’ve wanted to build for a long time.” One thing is for sure, however he spends his retirement: Karl Holtey is going to be busy.
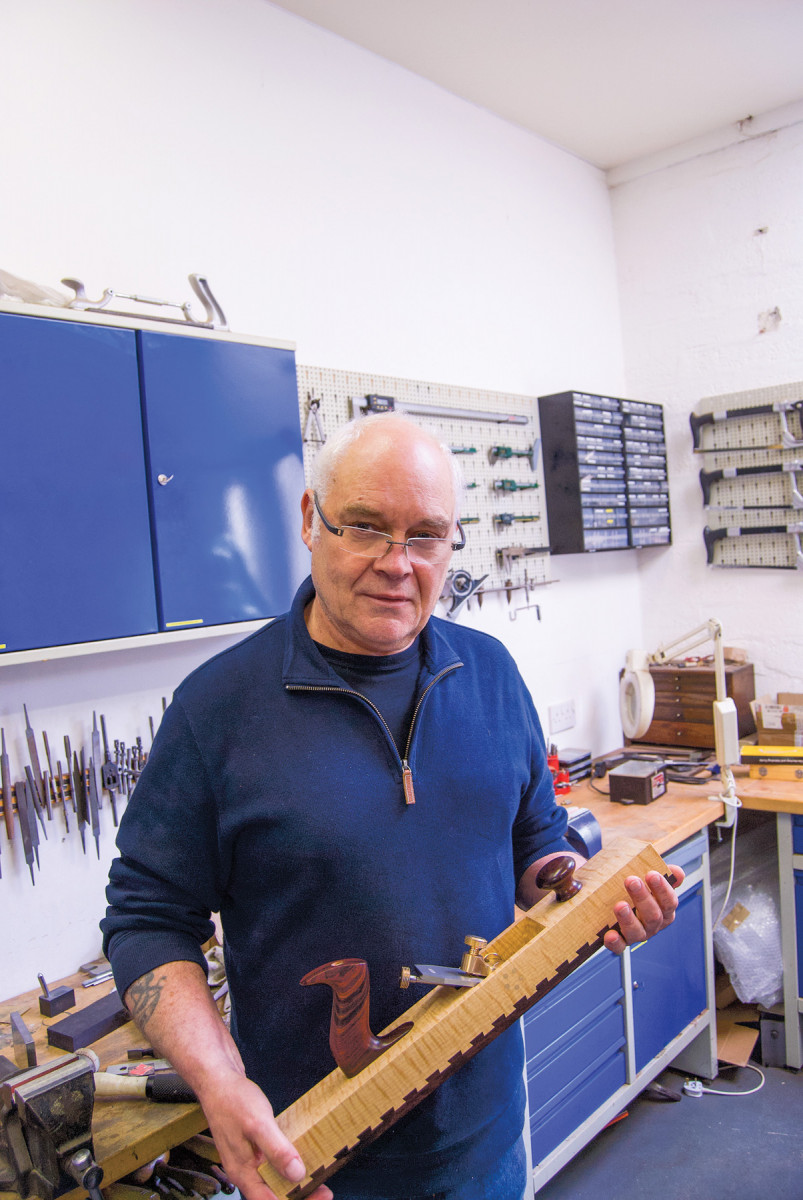
23. Karl with his T21 panel plane.
See more at holteyplanes.com. Kieran Binnie is a furniture maker and woodworking writer. You can read more from him at overthewireless.com.
Here are some supplies and tools we find essential in our everyday work around the shop. We may receive a commission from sales referred by our links; however, we have carefully selected these products for their usefulness and quality.