We may receive a commission when you use our affiliate links. However, this does not impact our recommendations.

I suspect I was around 18 at the time of this photo. I clearly had already chosen what would become my alma mater, Ohio University. Whew, that was at least 30 pounds ago.
I’m still not sure if I’m more comfortable walking on metal shavings or wood shavings.
Growing up, metal is what I knew. In my first blog post as the online content director for Popular Woodworking, I talked about growing up in a machine shop and the transition to woodworking I made as an adult. Grinding, welding, fabricating, following shop drawings, running mills and cleaning urinals was how I spent my summers as a teenager at Kent Automation. My time at my father’s business instilled in me an appreciation and connection to modern metal working that I think would be a pity to shake off entirely, just so I could present myself as a traditional woodworker. It’s simply not who I am.
This is why I was eager to write about furniture that brought both of my worlds together–metal and wood. The funny thing is, these mediums have grown into an extraordinarily popular design trend. Mixing materials is more popular than ever, hobby furniture builders are scooping up MIG welders and jumping into metal framed furniture with both feet. So why not address the trend head on?
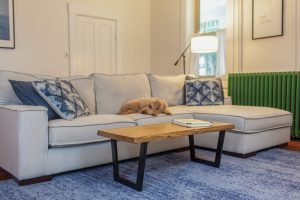
The opening image of my article in the November issue. I fabricated the base from rectangular tube and fed my golden doodle a treat or two to pose for the camera.
So I did in the November issue. The article is designed to serve as an introduction to welding–think of it as welding 101 and nothing more. I shared the big picture of the different systems you’ll see on the market and why I chose a flux-core MIG welder for my shop.
But allow this retired preacher to preach for a moment. We all bring a different set of experiences to the workbench. Whether you grew up in an apartment in the city, a farm with no electricity, or in the suburbs of Cleveland, each of us has a different understanding and expectation of what it means to interact with the furniture that’s all around us. Perhaps your parents valued fine furniture and you unconsciously demand everyone uses coasters to this day, maybe every piece of furniture in your home came from a flatpack box because you had to carry it up three flights of stairs–I had a dad that would throw retired furniture on the firepit and move on. (BTW, this is a tradition that I carry on today. Kitchen cabinets are best for creating monster bonfires, the open cavity allows the fire to breathe and they go up fast.) These experiences matter and they should influence your work. Without this diversity, we risk becoming clones of one another, with everybody making the same thing in the same way. Sure, I could have made the exact same table base out of red oak using some nice bridle joints, but I knew another way, in another medium, because of my life experience.
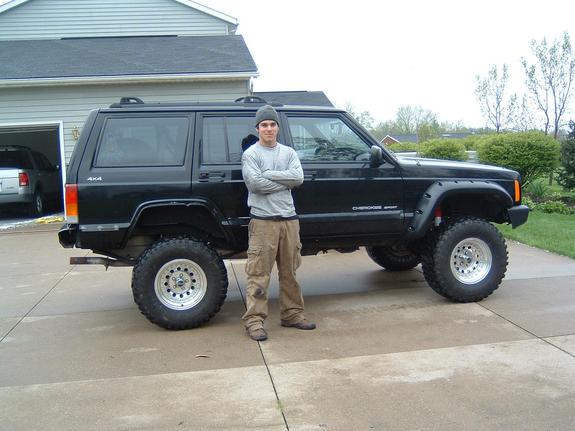
Toward the end of high school, my dad and I reworked the suspension on my Jeep. We told my mom it was going to be an inch or two lift. It was 6″. After this, I spent some evenings at the shop and built front and back bumpers out of 12ga plate and got a set of appropriately sized tires.
I hope what you’re hearing me say is that if you know a process that is technically sound, don’t let rules scare you off. Share what you know because it will make our craft more interesting and better suited to receive others who can relate to your experience.
Gary Knox Bennett kept coming to mind as I wrote this blog post. I have one of our videos embedded below.
– David Lyell
Here are some supplies and tools we find essential in our everyday work around the shop. We may receive a commission from sales referred by our links; however, we have carefully selected these products for their usefulness and quality.
As far as I am concerned, your article was the best of the issue. It was timely for me as well, given that my next project is an outfeed/assembly table, a hybrid of wood and aluminum.
Hey! I appreciate the encouragement!
The first sentence has a typo.