We may receive a commission when you use our affiliate links. However, this does not impact our recommendations.
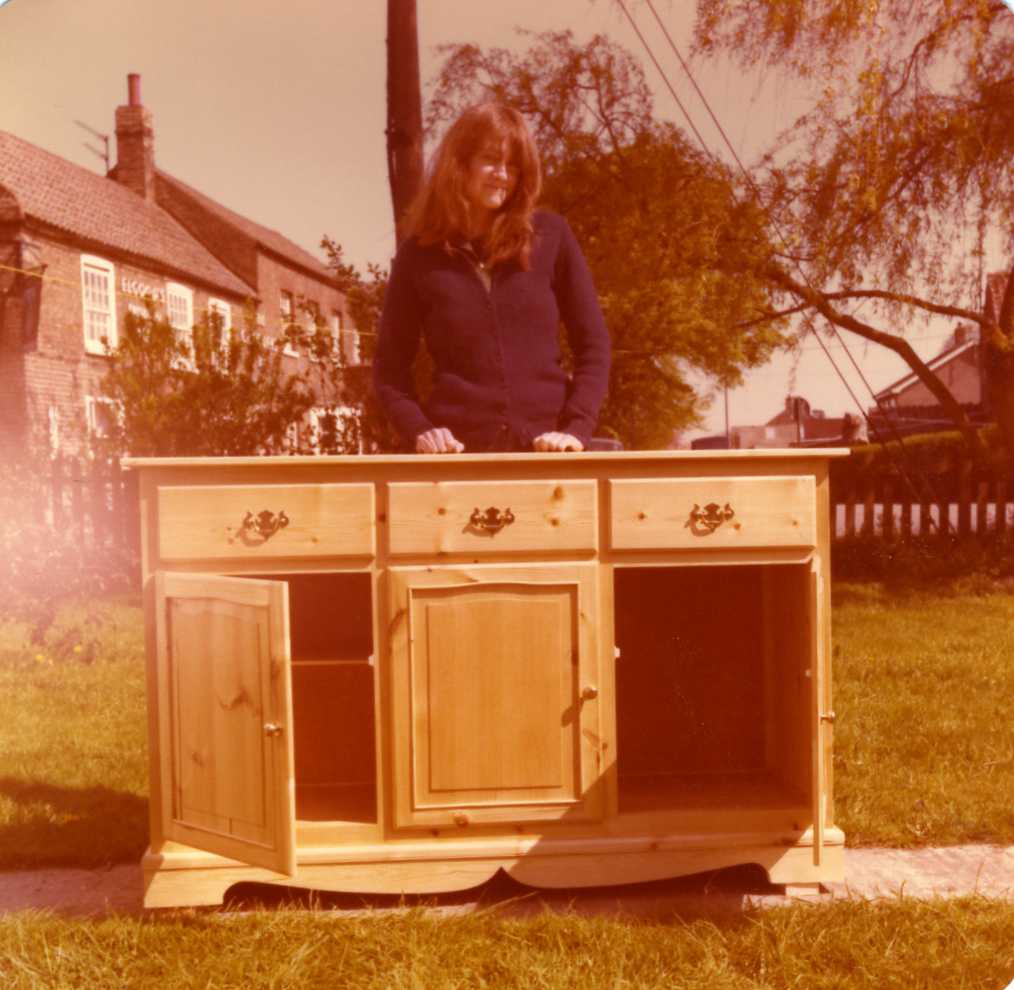
My first major commission, summer 1980: a Welsh dresser. This is the bottom section of the piece.
Every so often I find myself thinking about how much has changed in the 38 years since I got my first woodworking job. After a year of City & Guilds training in traditional furniture making I was hired by Roy Griffiths to work as a cabinetmaker at his business, the Crosskeys Joinery, in Wisbech, Cambridgeshire. Working for Roy was like jumping off a cliff into a world where efficient methods of work were absolutely critical to making a living when woodworking was a full-time occupation and the sole basis of my livelihood. That’s a world apart from the one inhabited by many of us in woodworking today, a point too easily glossed over in magazine articles about setting up a shop or Instagram posts about being self-employed and loving it.
It’s salutary to take the occasional look at where you are today from the perspective of how you lived before. Without this kind of reflection it’s dangerously easy to take your blessings for granted, not to mention imagine that things have always been this way. (They haven’t.)
So here are a few of the most obvious changes I see–let’s call them the low-hanging fruit. I’ll leave to you the question of what’s good (or arguably not) about these changes. Please share your thoughts in the comments. Next week I’ll climb higher up the tree to start picking the really good stuff.
1. Cameras, cameras everywhere
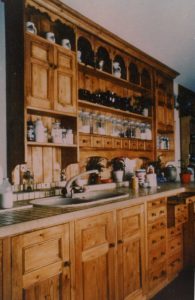
I am grateful to have this picture of the first piece I made in 1980 while working for Roy, this kitchen dresser (i.e., the upper section of cabinetry). With apologies for the low-res image.
Cameras used to be expensive. At least, a camera–even a cheap one–was well beyond my budget. What photos I have from my early woodworking years are from my mother, my employers, and friends.
Today, thanks to the plethora of products made with low-wage labor and automated machinery, almost everyone has access to a camera on a smartphone, and the quality of the images those cameras can produce is ridiculously high. It has never been so easy to document your work (and even the step-by-step processes involved in its making).
2. Affordable tools and machines
Cameras are not the only things made more widely available by low-cost production. When I was starting out, the kinds of machines I now use every day in my shop, such as my Grizzly 15″ planer and 24″ drum sander, SawStop professional table saw, and Bridgewood mortiser, would have been considerably more costly. The most affordable machines were old ones, like the 12″ Crescent jointer in my shop today; Roy’s shop was full of old machines.
The greater affordability of machines has made it more viable to turn a woodworking hobby into a way of making a living today than it was 40 years ago.
3. Access to instruction
My training was through a nationwide certification system that mandated curricula taught at colleges nationwide. (In the UK during the late 1970s, “college” was the equivalent of community colleges in the States today.) Americans often ascribe a Harry Potter-esque mystical value to this training because it has the word “Guild” in its name. In reality it was the opposite of exclusive: a solid foundation in the kind of tools and techniques deemed important for those going into small shop employment or managing those on the floor at furniture factories (this was prior to the adoption of CNC production), affordable to virtually anyone who could make time for classes, thanks to government subsidies.
Fast forward to our own day, at least in the States, where furniture training has largely been abandoned by high schools and community colleges. The past few decades have seen a proliferation of privately owned woodworking schools where you can take a week-long class for $800 and up (excluding the cost of travel and accommodations), a nine-month training for $21,000, and any number of options in between. Many schools offer scholarships and other forms of aid to increase affordability, but still, this is a universe away from the training I was fortunate to have.
For those who can’t afford instruction at a school or prefer to learn in their spare time, there’s a world of instruction available through magazines and online. One excellent craftsman in my locale told me he learned everything he knows by putting into practice the techniques he found in woodworking magazines. There are seriously affordable classes online such as Mary May’s School of Tradional Woodcarving, professionally produced videos for sale, and countless instructional posts on blogs at this site (as well as others). YouTube videos offer instruction on virtually anything you can imagine; just beware that the techniques are not always best practices and the quality of production sometimes means that details are inadvertently obscured from view.
4. Gender
When I was first in the trade, I was inevitably the only woman at the shops where I worked. On returning to the States in 1987 I found employment at a furniture making shop in Vermont where I was one of three women on the shop floor out of about ten woodworkers, a welcome change. There are many more women in woodworking careers today, especially on the studio furniture side.
5. The internet
On second thought, while this one certainly belongs with the lowest-hanging fruits, I’ll save it for next week, because I have to get to my own shop.
Here are some supplies and tools we find essential in our everyday work around the shop. We may receive a commission from sales referred by our links; however, we have carefully selected these products for their usefulness and quality.
Thats odd… we no longer teach young people woodworking in our schools, yet we have plenty of classes for older retirees on pensions. Maybe one is more profitable than the other?
As for changes…? Fasteners!
It used to be sloted or phillips? We now have square drive, hex head, torque screws, t25, t20, self drilling, pocket heads, etc. etc. I’m not complainig, most of these speciaty screws are much easier to zip in, but it makes finding a slotted head wood screw much more difficult.
Both great points. To the first I would add that many schools have been started by woodworkers who openly acknowledge that they got tired of trying to make a living by selling their work and decided it would be more profitable to teach their skills to others.
On fasteners, you’re right about the variety. I remember using slotted head wood screws exclusively and driving them in by hand. Now that seems a universe away! My best source for quality slotted head screws is Jamestown Distributors.