We may receive a commission when you use our affiliate links. However, this does not impact our recommendations.
I’ve recently become more comfortable with the basics of saw sharpening, through a combination of Christopher Schwarz’s hands-on tutelage, Pete Taran’s awesome primer (available free on his Vintage Saws site), Ron Herman’s excellent DVD, “Sharpen Your Handsaws” and, most important, getting over my fear laziness and simply doing it.
The new Saw File Holder from Lee Valley/Veritas helped with that – I’d filed a couple times in the past using the shop-made guides that Ron recommends on his video, but when Chris took his tools home, he took his Gramercy 14″ saw vise with him. And I guess I’ve just been too lazy to build our shop-made wooden version. (It’s also arguable that I have access to too many saws, so when one is dull, there’s usually a sharp one I can grab).
But when I opened the saw file holder and knew I had to test it out for the magazine, I finally broke down and built a saw vise.
I’m lying. I went over to Chris’s house and used his Gramercy.
As I was leaving, he gave me his old Wentworth saw vise (and the spider webs in which it was swathed) – the vise on which the Gramercy design is based. Today, I finally brought it into the shop, cleaned it up with some elbow grease and WD-40, then clamped it to a board that I clamped to my bench with holdfasts. (My bench at work is 2-3/4″ thick; the clamp on the bottom of the Wentworth opens to 2-5/8″.)
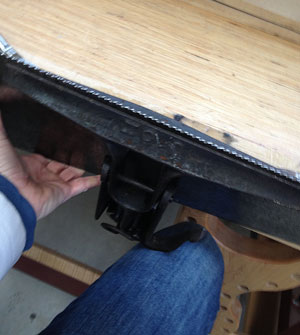
I do like that you can simultaneously hold the saw in place with one hand, lock the jaws with your knee and take a picture.
I clamped a saw in the vise and took a few swipes with a file. The saw slipped.
Then I came home and fell into the rabbit hole of Internet posts on saw vises…including Christopher’s glowing review of the Gramercy, in which he says the Wentworth (the Wentworth he kindly gave to me), “kinda blows chunks. It closes up tight on the left side, but not on the right. I filed the jaws a bit, tried a little leather, etc. etc. But I’ve not been able to get it right….The Gramercy saw vise turned my Wentworth into a bass boat anchor.”
But I’m not ready to give up on it (and I don’t have a bass boat), so I’m going to try what Matt Cianci (the “Sawwright”) recommends: rubber washing machine hook-up line split in half and glued in the V-shaped notch on the clamping jaws.
And if that doesn’t do it, well, I might be saving my pennies and sending them to Joel Moskowitz. I seem to have caught the saw sharpening bug. There are worse vices.
Here are some supplies and tools we find essential in our everyday work around the shop. We may receive a commission from sales referred by our links; however, we have carefully selected these products for their usefulness and quality.
I used a 3/16″ dowel in the slot on mine and it works likea champ!
OK. I can’t resist. If Chris were really a nice guy he would have given you his Grammercy instead. :):) I actually have both vises. I started with the Wentworth. It makes you appreciate the Grammercy soooooooooo much more. So maybe Chris did you a favor. Yeah, that’s the ticket. :):) I should point out though the Grammercy is not perfect either. It needs to be 19″ wide instead of 14 and mine has a few chatter spots in it.:) But it is my go to vise I use a lot. In fact I have a 26″ Disston No 7 clamped in it as I type. Now if you really want a vise. Think 26″ modified cast iron ACME saw vise. OOOOOOOOOOOO AAAHHHHHHHHHHH. Not exactly portable. But it is a poor craftsman that blames his/her tools. I have to blame something so I blame my tools. :):) Best wishes. Ron
The best solution I have found for this problem and is really easy is masking tape on the back jaw, if it is really worn put on two layers.
I had an issue like this with my Disston 3D vise. I just filed the jaw until they ran parallel, so an equal gap. then I shimmed the mechanism. This method works really well and I use my vise on everything from .015 – .045 saw plates with no problems.
Megan: I have a half dozen of the Wentworth No. 2 vises ( the 12″ type) that i use in my saw sharpening workshops. They were designed to have a knotted cord stretched between the ends of one vise face to cut down on squealing. Sometimes I have found them with some sort of rubber remnants molded into that slot. I would say that maybe half of them have been dropped in the past and braised back together. For this reason, the jaws often do not match exactly. I filed the top of the closed vise to get the faces to the same height. I then inserted two layers of adhesive felt into the vise faces, closed the vise and trimmed off the excess. I bolt my vises to a piece of 2X12 about 12 inches long. I can clamp this in my shoulder vise (or between the tailstock for shorter students), with the height of the jaws at the resting level of my elbow, with just enough space for the cam lever to work. The TFWW vise is great, but very industrial, whereas the Wentworth is romantic!
Is that vertical strand bamboo board on the benchtop in the background of your hand-knee-camera shot? If so, 1/would you use it again? and 2/where would one find a source for it? Many thanks.
R²
“There are worse vices.”
I saw what you did there.
Tom
“Worse vices,” eh? Well said! There are worse vises, as well (though you’d be hard pressed to find them). As a former Lit major, it’s both humbling and encouraging to see someone gainfully employed for a love of language. The only link I’ve had between my passions and paychecks, in regards to education, was someone admiring and requesting a frame I’d made for my degree. In short, cheers to you and the future of PopWood. I’ve enjoyed and look forward to the color you bring to the table.
If the jaws themselves are straight I’d be inclined to work on the other end…. Try shimming the cam surface on the loose side with various thicknesses of steel shim stock and see if that works. If it does the proper thickness shim (s) could be soldered in place. Alternatively, the surface could be built up with weld and reground/filed. A few thousandths change at the cam could made a lot of different at the jaw…
The Southern Solution is to simply put a vise grip on the loose side. You just can’t file the 2 or 3 teeth under the vise grips.
I love mine, I bought it as what I thought was a tinker’s small brake and used it as such for 30 years and just recently decided to learn about saw sharpening and voila, I already had the vise.
Take the vise to a machine shop. Tell them what the vise is for and what you need it to do. Ask what your options are. Machine shops are an excellent resource for woodworkers. I took a rather sad jack plane to a machinist (friend of mine) and told him I wanted the sole flat and perpendicular to the sides. The small investment of time and money beat the pants off trying to flatten the sole on sand paper.
You’re going to have to save a lot more pennies than Chris did. I just checked the pice at TFWW and it is up from $119.95 ,when Chris reviewed it, to $170.00.
Washing machine line split in half? Oh, come on, Matt. How about trying the high-friction sheet material that Lee Valley offers along with its bench hockey pucks? (Go, Sabres!) Has good hold and is PSA. I use it to line the jaws of the vice on Joel’s bench-on-bench. It is much easier to cut than that stupid hose.
Oh now. I’m just giving you grief. It’s better than the vise I had, and perhaps Matt’s suggestion will fix it right up — I’ll find out soon!
I don’t remember it sucking THAT bad. Oh well. Sorry.