We may receive a commission when you use our affiliate links. However, this does not impact our recommendations.
I have completed the restoration of the 1960s-era Stanley hand plane I wrote about in “Hand Plane Quest.” Let me tell you that while I clearly have a lot to learn (and tweak) about this tool, it is already a lot of fun to use – and it has allowed me to finish a couple projects here in my apartment that were nagging me.
The only real sticking point in the tune-up process was sharpening the iron, a first-time practice for me that was accompanied by another of the usual challenges – money. I tallied up costs for new waterstones and a honing guide, and ended up simply freehanding it with my old waterstones. They are too narrow for the job. I couldn’t seem to get an adequate stroke going with the iron.
I checked my credit card balance again and called Ron Hock – a man I have needed to meet anyway. (I have already had an excellent tour and an amazing day at Lie-Nielsen, with Robin Macgregor and crew.) Ron would not listen to my credit card number. Since I don’t actually do tool reviews, this was an act of stupendous generosity for which I am deeply grateful.
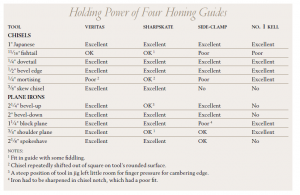
A handy chart for choosing a honing guide. The Veritas model listed is the Mk. II. Click on the photo to enlarge it.
Nonetheless, there will come a day when I need to sharpen my plane iron. Some say, in fact, that you should sharpen a new iron the day you receive it. When that day comes, I will be deciding between the freehand method and honing guide use. Which method do you prefer? Tell us in the comments section.
I have selected a couple opinions on the matter. The first comes from Christopher Schwarz and his totally comprehensive book, “Handplane Essentials” – a digital download that I keep right by my side at all times in the learning process. (Buy a copy yourself and follow along. It is also available in paperback.) The counterpoint opinion is from none other than Joel Moskowitz of Tools for Working Wood. Enjoy!
–Dan Farnbach
More often than not, I use a honing guide when sharpening. Though I can (and do) sharpen without them, I find them to be brilliant at providing repeatable and quick results. And when I teach sharpening, I like to show students how to use a guide. Many woodworkers sharpen infrequently and have difficulty training their hands to do what they want every single time.
–Christopher Schwarz
I disagree with a lot of teachers in the field on the subject of honing guides. These are teachers whom I respect, so it bothers me that I disagree with them. A lot of them say if they show sharpening using a jig, students will get sharp tools right away. Students won’t be discouraged and will be able to go on to building a project. Maybe there’s some truth to this, but I think students would end up with sharp tools and the ability to progress if they were instructed that freehand sharpening is a basic skill they could easily master.
Freehand sharpening the way we teach it is faster and more repeatable than using a guide because you don’t have to continually build secondary bevels. You can trivially sharpen and also include a true micro-bevel that can easily be erased with each sharpening (which improves overall performance, not just edge strength). And of course you can sharpen any tool, because the technique for one tool is the same for the others.
When I teach people good hand technique and they practice, most of them find the experience liberating. And with their newfound skills they’re able to trust their hands for more and more complicated work earlier on in their training.
–Joel Moskowitz, Tools For Working Wood
Here are some supplies and tools we find essential in our everyday work around the shop. We may receive a commission from sales referred by our links; however, we have carefully selected these products for their usefulness and quality.
I settled on the sandpaper/glass method, but I use4 3M honing film instead of sandpaper. Sandpaper has “give” to it and will round off a surface, and it doesn’t come in fine enough grits. I also use jigs. Freehand may get a blade sharp, but it will not be as sharp or as durable as an edge made using a jig. I also advocate micro bevels, which are impossible to do accurately freehand. Micro bevels same time and blade steel(don’t have space here to go into the science). Stones do not stay flat, even good Arkansas oil stones – I’ve used them enough to see them wear down and have to flatten them. Diamond stones are not fine enough for final edge prep, and tend not to be perfectly flat. Stones are great for initial bevel grind, though, where accuracy is not real important. I find the honing film provides the superior edge and at lower cost. As an engineer I look at the science and the results, not the myth or opinion. Freehand is quicker in the short run, as edges require re-sharpening more often. Do yourself a favor and use jigs. I have made my own (we are woodworkers, right?) and use shims to generate the micro bevels. Also, remember to hone the back of the blade. I use a micro bevel there as well – one at less than 1°. Doesn’t take much time at all.
I have done free hand since Boy Scouts (more decades ago than I like to admit). We Used hard stones and water or oil for lub. Today I own a jig but still do best with freehand. I have used sandpaper on marble (or glass) and it works very well and cheap. Never have bought water stones because of high cost, mess to use, and must be flatten after a few uses. Now days I do step up to quality stones (Arkansas is favorite). Takes years to round stone and won’t if you just move around on it. Diamond plates work well, even cheap ones (watch as they ware out quickly). Everyone who owns planes MUST have Chris book on hand planes. I’ve never found a single other source with as much complete helpful info. And back to Dan Farnbach, who started all this, as I learned years ago and still teach, there is only 1 way to do it right. Pick any method and practice, practice, practice.
Like a few others here, I’ve gone through the various systems trying to settle on one that makes sense, both financially and from the perspective of the time it takes to get tools really sharp. For many years, I have been teaching woodworking students how to sharpen and use hand tools. Back in 2009, students asked me to fully describe the sharpening process on my blog so they’d have a handy place to refer to after classes were done. The first post appears here: http://jszcbf.wordpress.com/2009/07/08/sharpening-class-part-i/. There are subsequent posts that follow this one, sprinkled throughout the blog. This system works, and while it is difficult to pick up any woodworking skill by reading about it, I hope these posts give readers a sense that anyone can learn to get sharp tools without spending an arm and a leg for equipment.
I USE WET DRY SANDPAPER ON GLASS WITH OIL FOR LUBRICANT. Glue the paper to glass windo panes with contact adhesive. I start with 600 grit. Use however many panes as you want and put progressively finer grit on each one. I personally use 600, 1000, 1500. The glass is flat and keeps the plane iron flat. The first pass stroke the iron like you are stropping it till you have a wire edge, then progress to the next grit etc. till you are satisfied with the edge. This is the cheapest and the best method for sharpening. Feel free to contact me if you need more information.
I did not read any of the other reply’s but to sharpen a plane iron is to use wet dry sand paper on glass. Take spray contact adhesive and spray the glass lightly. Then spray the back of the sand paper lightly. Wait a few min. then stick them together. I usually fold the paper and tear or cut it in strips. and use the strips. use 600 grit for one side then use 1000 for the other side. Oil the paper before stroking blade down the 600 grit till you see a wire edge forming. Then go to 1000 grit and repeat process. You can fix up as many glass panes as you want and keep using finer grits such as 1500 grit and you can keep going all the way to 6000 grit if you chose. It will be perfectly sharp after 1500 grit. I use this method on some of my bench chisels also. Any questions feel free to contact me.
There’s literally a host of options for sharpening. I suppose I’m a hybrid sharpener, using both freehand and “jig-based” sharpening depending on what I need to do. I believe, the bottom line as has been noted, “go with what works for you” and it certainly makes sense. Sharpening has been argued and debated ad nauseum–and will continue to be so debated…
Pick a method based upon your budget, ease of use, and the best outcome for you. WIth each method, there is a learning curve, requiring patience, repetitive practice to achieve “quality” sharpening and execution of cutting edge you seek. If you are seeking “perfection”–this is possible, but rarely probable. Keep on, keepin on!
Hey guys,
This, like most either/or propositions, boils down to results. It doesn’t matter which technique/jig/stone/paper/laser emitter you use, as long as you’re competent and consistent. If you do wood working infrequently, you might want to use a jig. If you’re doing it everyday, by all means, learn to sharpen free hand. I “learned” how to sharpen freehand, and quite frankly it is no where near as accurate and repeatable as using a jig; at least for me. But it’ll cut. I use a jig on everything except axes, knives, drawknives, and machetes. BTW, that side clamp type jig is probably the best, along with being cheap.
I’m a recent convert/fan of the Norton water stones; that 1k/8k is the bomb! So I went out and got their 220, for those really beat up edges and reforming tasks. Still have to pick up a DMT Dia-Flat though; that’ll be next time.
Back to the question though. If it were me, I would get the side clamp guide, a piece of glass, and a few sheets of wet/dry paper. We’re talking less than twenty bucks. You can always put the bevel on the glass and clamp the blade in place, or use trigonometry to figure out the cosine… or is it sin? Anyway, you guys get the gist of it, and you will be close enough that the wood’s grain won’t notice.
Eventually though, you’ll want to get a couple of good quality stones. But even beyond that, you want to be consistent and sharpen to the same angle each and every time. A jig allows you to do that without too much fuss.
best regards!
Albert
I’m a freehand guy and very much in the same camp as Joel. I had to teach myself freehand once I started working with curved blades for moulding planes, carving gouges, and travishers. So it just took over and now everything is done freehand. Good thing too because there are no honing guides allowed at the history museum where I volunteer and often a lot of dull tools. Here is a quick vid of my honing process in response to Chris Schwarz’s post a while back http://www.renaissancewoodworker.com/how-do-you-sharpen/
I sharpen freehand. Since the blade in every plane I ship out is fully honed, I do a LOT of sharpening. I was tired of setting up the jig every time, so purely out of a desire to be done quicker, I forced myself to learn free hand. It wasn’t as hard as I had made it out to be. After a few days of working at it every time I needed to sharpen, the results were very passable. Now, I barely have to think about it. It really doesn’t take too long to develop the muscle memory on how to hold the blade.
I use a jig for planes because of the wide blade needing a consistant bevel across the whole edge. For a really cambered blades I free hand and for chisels I always freehand.
I use the side-clamp jig frequently, but I can also sharpen freehand. For sharpening newbies, I usually recommend the kit from Lie-Nielsen with the Norton 1K/8K stone. I also use a 4K stone and a DMT diamond stone to flatten. That is a pocketbook friendly kit over the long haul. By the time you wear out the stones you will be good enough to decide what to buy next.