We may receive a commission when you use our affiliate links. However, this does not impact our recommendations.
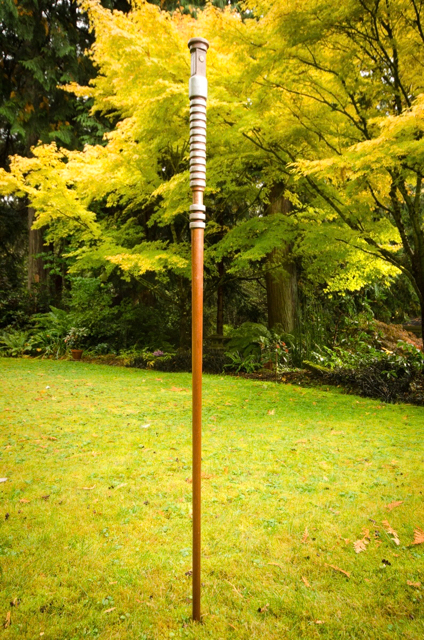
A Star Wars themed walking stick.
A New Lightsaber Walking Stick
Not long ago, in a small workshop far, far away…
It was a period of unrest in the woodworking world. With new technologies entering a galaxy of century-old traditions, the woodworking world was in a period of great change. At a remote base deep in the woods of the Great Northwest, a lone rebel faced a daunting challenge: to merge a traditional walking stick with a Star Wars Jedi Knight’s Lightsaber.
Related: Star Wars: Wood Episode II
The Challenge
It’s fair to say that I like challenges. Actually, I love them. From a designer’s perspective, challenges are the motivators we use to create new things. This challenge, as is often the case, started out with a simple need.
My terrific next-door neighbor Ron, with his dog Eli, go out for walks several times a day. Unlike a flat urban environment, we live on the edge of a very tiny, heavily wooded Puget Sound waterfront community. Walking around here is not a leisurely stroll on a sidewalk. It’s different, challenging and very beautiful. Ron walks up and down rocky roads and over woodland trails. For years, Ron has steadied his walk with a walking stick made from a piece of driftwood. Over the last few, I’ve watched that stick shrink down from 5’ to less than 3’. That’s way too short. It was time for some designer/woodworker action. Time to create a new walking stick.
My first instinct was to find a piece of Madrone — a beautiful local wood we’re fortunate to have in reasonable abundance. But, Madrone limbs are heavy and far from straight, thus making a walking stick unbalanced, asymmetric and awkward to hold. So, I decided to start from scratch and create an entirely new design using a modern set of tools new to the traditional world of custom walking/hiking sticks. CAD software and a CNC.
Before I began, I needed to understand the physical attributes of what an ideal walking stick should be. That took research and testing. Tall walking sticks, as it turns out, are a tiny world. In this case, the internet proved only marginally useful. I needed real-world information. I used shop scrap to measure and test various lengths, shaft diameters, tapers, hand-hold areas, balance points that actually aid in motion, and explore acceptable weights.
Armed with that information, I set out to create new designs in Rhino3D, the three dimensional CAD software I use every day in my furniture and sculpture work. But, before I began, I added one more challenge to my ingredient list. After all, I’m a designer and a simple pole wasn’t enough of a challenge. I decided to make the project interesting by merging two very different things together. In design terms, I wanted to incorporate a design theme around the practical function of a walking stick. And, that’s just what I did.
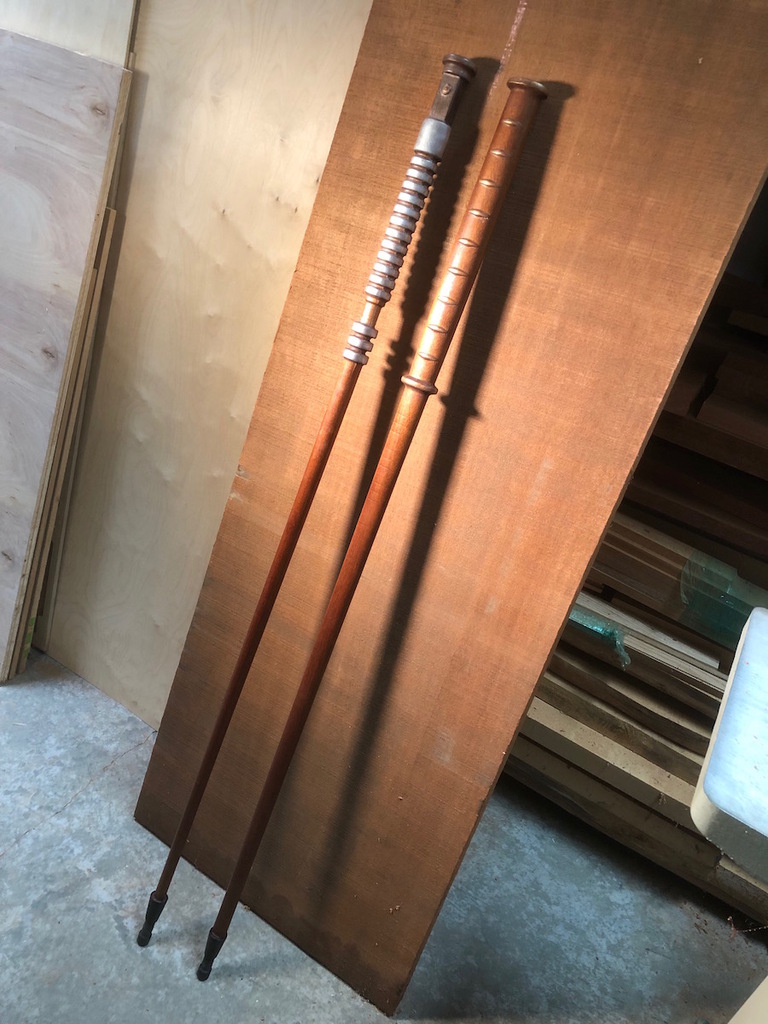
Mahogany prototypes of the Star Wars-themed Obi-Wan Kenobi and Kendo Walking Sticks
In the end, I used two themes and created two different designs. A walking stick with the characteristics of a Japanese Kendo practice sword, called a Shinai with a Samurai handle and a second walking stick designed to look like Obi-Wan Kenobi’s Lightsaber from Star Wars Episode Four: A New Hope. With the coming release of the film Star Wars: Episode IX —The Rise of Skywalker, for this article we’ll focus on the later. Someday I may post about the even more challenging and detailed, oval profiled Kendo Walking stick.
Hiking/Walking Stick Details
Being that this was to be a custom walking stick, I used scrap to find a good length for Ron. A hiking style stick that’s around shoulder height was the place to start. My stick, designed for men under 6’ tall, is about 54” long and made from a blank that’s 2″ x 2″ x 61” long. The reason for the extra length is I was going to machine the stick using my CNC and needed the room for an accurate pin registration setup for two-sided machining. In addition to the stick length, I allowed for adding an extra 1” for the English hiking stick ferrules I purchased to protect the bottom of the sticks from wear. Final height: 55″.
Upon observation, when using a tall walking/hiking stick, I noticed that walkers frequently move their hands up and down on tall walking sticks over a pretty long area. Different hand positions add comfort and allow for changing the balance of the stick as you’re walking. So, I reserved 16” at the top for a long handle. Also, I noticed that if the final length is just under chin height, a smooth rounded top is a great place to rest your hands when stopping for a chat with neighbors. Armed with lots of information plus photos of Obi-Wan’s Lightsaber from Star Wars: Episode IV, I created a light-weight, tapered, walking stick for Ron.
To machine the sticks, I created a custom base to hold my blanks and register them in position when the stick is flipped to machine the second side. On the base is a grid of 1’ spaced holes to position the custom 3D printed supports I designed to steady the newly machined areas once flipped over to work on the second side. These supports minimize the long, thin stick’s tendency to flex under machining.
After building a few prototypes in Mahogany, I had high hopes for using very tough Black Locust, but after a number of problems, I ended up using locally sourced Elm, known for its interlocking grain, strength, and flexibility.
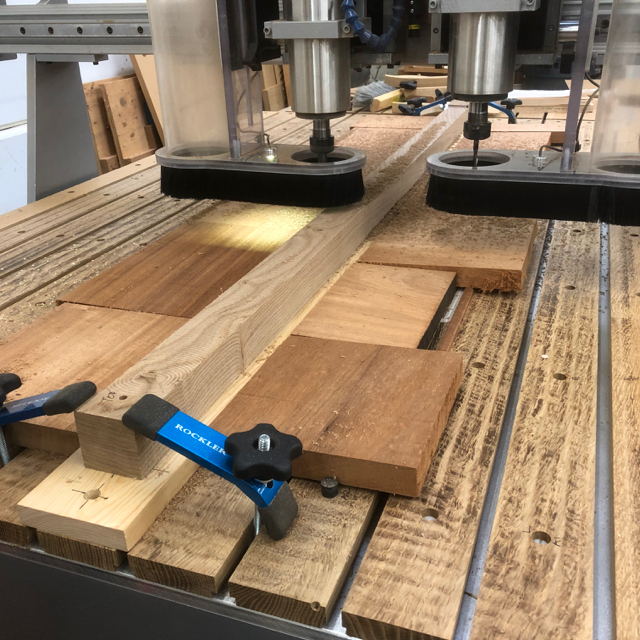
Starting with a custom pin board and a 2″ x 2″ x 61″ blanks
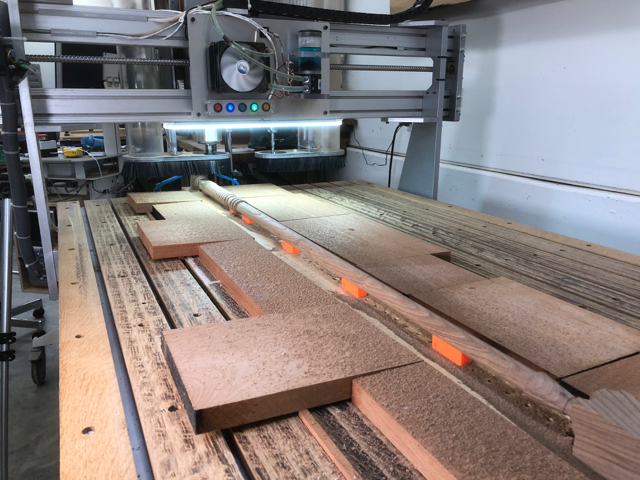
Two-sided machining a long walking stick comes with a lot of challenges
CNC machine or Turn on a Lathe
If you don’t have a long CNC, you could make a Lightsaber walking stick with a lathe. It’s mostly round, so why not? But, there are some special challenges to consider. For one, most woodworkers don’t have lathes that can turn a 60” blank. Also, turning a long thin piece can be difficult as it flexes a lot when applying gouges. To solve both problems, consider turning a Star Wars walking stick in two pieces. The handle area at 16” long and the shaft at around 40” long. Add a turned 2” long, stout dowel at the bottom of the handle and machine a matching mortise into the top of the shaft and glue the two pieces together.
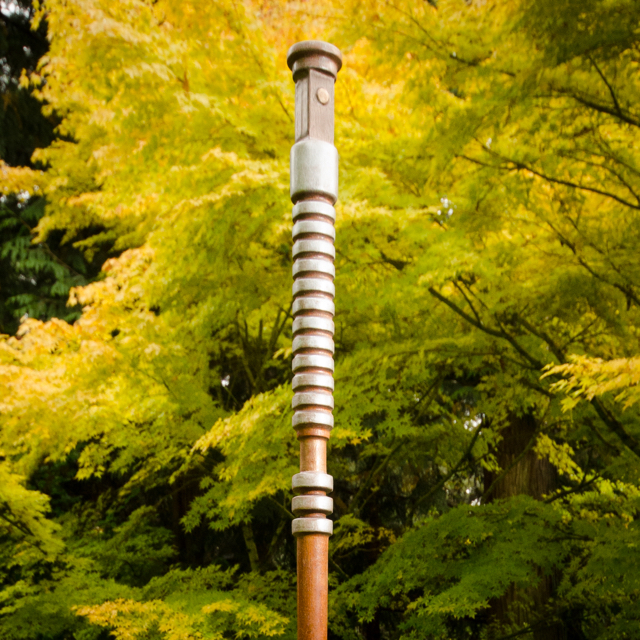
Yes, you could turn this walking stick. Two parts make it easier. Handle and tapered shaft.
Sweating the Details
The beloved Lightsaber used by Obi-Wan Kenobi has a few extra design details worth incorporating. Unlike the rest of the stick, which is primarily round and perfect for turning, the Jedi master’s Lightsaber has a square area near the top. Before mounting the blank of your lathe, you could pre-cut a square area on a table saw with a dado set. Note to Star Wars purists: It’s about ergonomics. My walking stick handle is thinner and longer than the canon Lightsaber and I left off the large knurled area near the top of Obi Wan’s Lightsaber because I thought it would be uncomfortable in the hand. But if you’d like to add that or any other hand-carved details to personalize your Lightsaber walking stick, go for it. After all, each Jedi Knight’s Lightsaber is supposed to be unique.
Finishing
Like the Force always being with you, sanding will always be with woodworkers. As much as we face sanding on every project, a walking stick needs special attention. Sure, we all like to sand every piece until smooth. But, because your hand is constantly moving over surface details, you feel the tiniest imperfections. You need to sand to the extreme and make sure there are no sharp edges that catch your skin. Very, very smooth. It’s all about “feel”. Take your time, you will.
With a tough outdoor life ahead, I finish my walking sticks in Brazilian Nut based deep penetrating oil: Penofin Hardwood Oil. For the metallic detailing in the handle, I turned to a trick for imitating the look of worn metal used for super-hero costumes crafted by serious Cosplay players. I used a unique metallic wax finish called “Rub ’n Buff Metallic Finish”. This is an amazing product, where just the tiniest amount gives any surface the look of metal. It needs to be applied carefully and sparingly and depending on your application technique, different effects can be achieved. I used multiple metallic colors on my walking sticks to replicate the different metals used in a Jedi Knight Lightsaber.
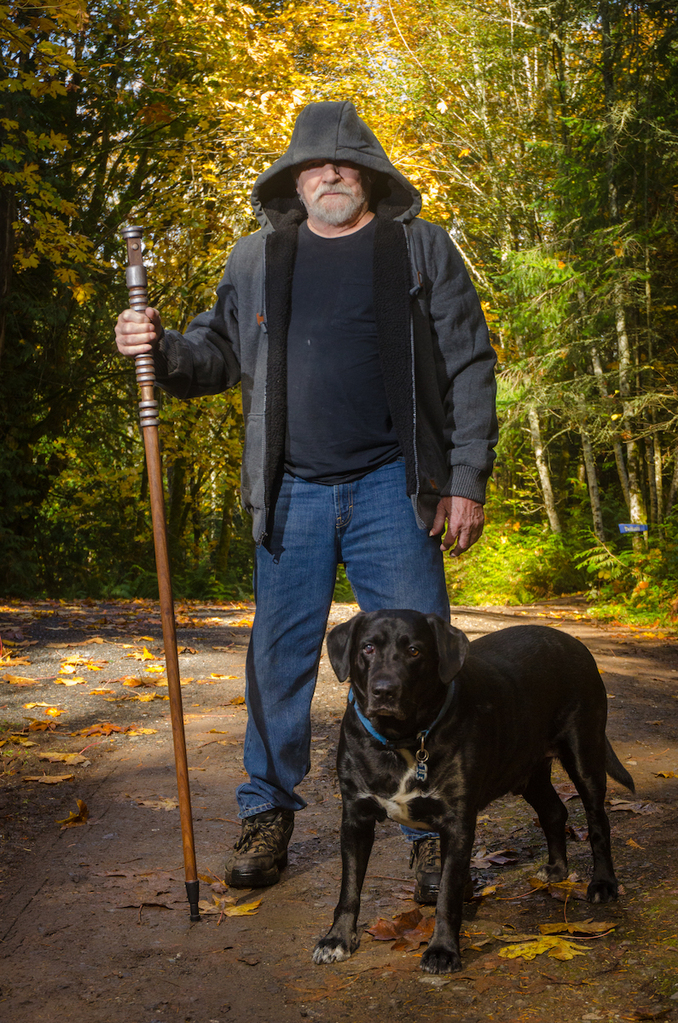
Jedi Knight Obi Ron Kenobi and his trusty dog Eli.
Epilog
Armed with his new walking stick, my neighbor Ron now is now called: Obi Ron Kenobi, Jedi Knight. His stick is light, well balanced, and the Force is strong with him as he walks through the woods.
On the practical side, one of the realities of making these custom walking sticks is “the math”. Usually, a CNC makes quick work of highly detailed projects, but not in this case. It takes around 10 hours to machine each one plus a few more hours to complete them. That’s a lot of time. With considerable time investment in special setups, custom jigs plus the attention I was getting friends as I was making them, I made a few extras as gifts.
Because the Lightsaber design is essentially a cylinder, I’m sure a skilled turner could make one much faster. If that’s you, a Star Wars Lightsaber walking stick would make a great gift for any Star Wars fan. But be forewarned if you have dreams about selling them. You will face the considerable copyright protection challenges of the powerful Disney/Star Wars/Marvel empire. In any case, a Star Wars walking stick is a fun, challenging and unique woodworking project. Make one if you must.
See you at the premiere of Star Wars: Episode IX, The Rise of Skywalker on December 19th. Until the next time, may the Force be with you…
But, wait, there’s more! Next week I’ll have another Star Wars-themed woodworking project: Star Wars: Wood Episode II —The Star Wars Universe. This one is very cool, perfect for small CNC owners, and just in time for Christmas…
Additional Resources
- Star Wars: Wood Episode II
- Digital Woodworking on Instagram
- Digital Woodworking YouTube Channel
- Personal Work on Instagram
Here are some supplies and tools we find essential in our everyday work around the shop. We may receive a commission from sales referred by our links; however, we have carefully selected these products for their usefulness and quality.
Minor nit: they’re called ‘ferrules’ not ‘ferrells’ 🙂
A neat solution to the ‘this is too long to turn on the lathe’ problem is to break the whole thing into three pieces, and use cane joint parts like these to connect them
https://www.leevalley.com/en-ca/shop/hardware/fasteners/connectors/41005-brass-cane-joins
Also lets you travel more easily for those of us who fly the Millenium Fal- err, commercial airlines to our hiking destinations…
You are correct about “ferrules”, of course. Grammarly, a great tool for last-minute checks, was down the day I uploaded the story, so I missed it. All better now.