We may receive a commission when you use our affiliate links. However, this does not impact our recommendations.
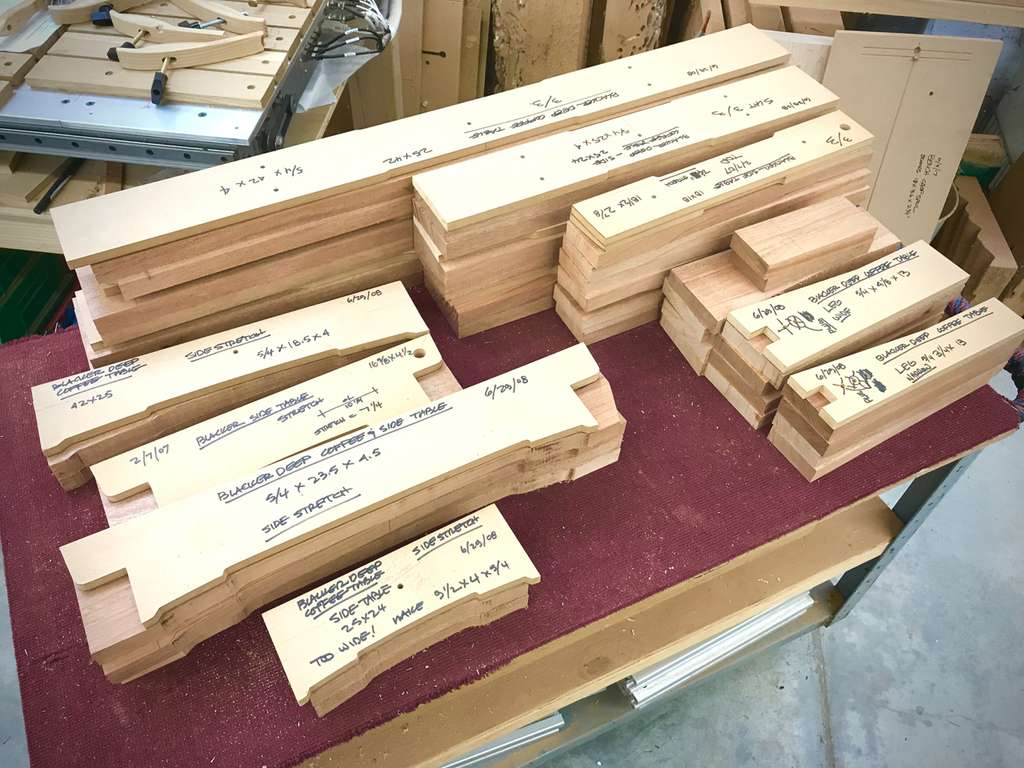
It’s the design that matters most. Thanks to the use of precision patterns, the issue of part, joinery fit and dimensions being correct are separate from design.
Part Three: Design
Though digital woodworking tools may be different and the scales are finer, the importance of precision is the same for every woodworker. If you’re working to a precision standard and your processes reinforce it, then the only differences between digital and machine tool woodworking are the numbers. Essentially, digital woodworking is to .001” or better and machine tool woodworking is to .010” or better. As a practical matter, I can’t see .001” on a ruler, but I can program a CNC routine and get measurable results and perfect joints every time. The point here is to establish standards and stick to them in whatever form of woodworking you prefer.
Pure hand tool woodworking is different. It works with a different and often immeasurable scale. For the most part, you’re making one part at a time and despite it being just as important to establish standards for measuring and process, precision for you comes down to fit and appearance. A hand-cut dovetail on a blanket chest is not about numbers. Making the pins and tails come together just right with an invisible line is precision without measurement and is hand tool woodworking at its best. But, holding to that standard for eight drawers, sure enough, is a more difficult challenge.
Precision and Design
Though some may think otherwise, a committing to precision does not interfere or compromise design. In fact, it frees it. If your standards are in place and you exercise them regularly, then you can forget about it and move the issue to the background and focus on design. I’ve been a designer my entire adult life and have yet to have the issue of precision get in the way of creating something new. Besides the practical benefits, in a way, precision is kind of something you can apply to your designs. Because I have standards and practices in my shop and stick to them, I don’t worry about it. I work knowing that all dimensions will match my drawings and everything will come together and fit exactly as expected. I find that it makes woodworking a lot easier. I think of precision as a solid foundation that sits underneath a design. Always there when you need it. My focus is first and foremost always on design.
Some designs are less about precision. Designing the sweeping curve of a crest rail of a dining chair, for example. I focus on the aesthetics and the visual balance or tension with other design details. Other than repeatability, critical overall dimensions, architecture of the hard points and joinery issues, measurements take a back seat to design. On the other hand, I do care that all the crest rails in a set of 8 dining chairs match up, so it’s important to start with perfect blanks. In other design situations, precision can become a component of the design, itself. Something geometric with precise detailing, for example. To pull it off, it needs to be as perfect as you can make it. People notice the precision. Patterns or better yet, a CNC, really help when precision is a feature, not a supporting character.
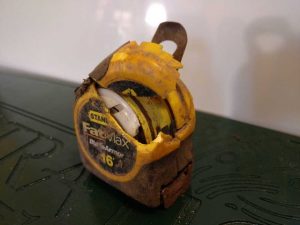
This ugly tape contest winner spent the winter underground after being buried and tilled into a field. Though it still retracts, it might be not a good choice for fine woodworking.
This concludes the last of the three-part series on precision in woodworking. No matter what tools you use or the level of precision needed in your work, I hope that readers establish a standard that they’re comfortable with and stick to it. And, please throw out that beat up 35’ super heavy-duty tape measure and any other tapes that shouldn’t be in your shop..
Additional Resources
- Precision Tools. A Five-part Popular Woodworking series.
- Digital Woodworking on Instagram
- Digital Woodworking YouTube Channel
- Personal Work on Instagram
Here are some supplies and tools we find essential in our everyday work around the shop. We may receive a commission from sales referred by our links; however, we have carefully selected these products for their usefulness and quality.