We may receive a commission when you use our affiliate links. However, this does not impact our recommendations.
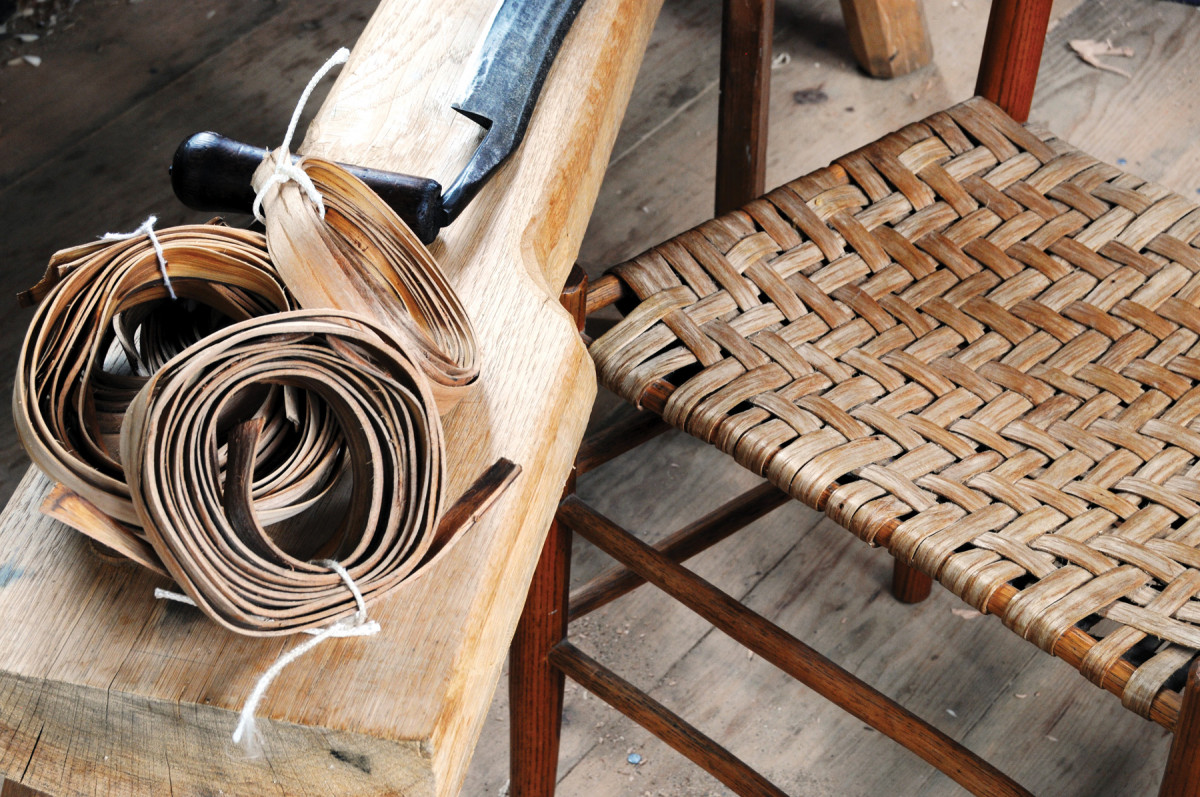
Hickory bark. If a hickory log comes my way in the springtime, all other work stops while I harvest first the inner bark, then the wood. Bark seats like these are the best there is. I also use straight-grained hickory wood in many ways.
This hardwood is best harvested for its bark and wood soon after cutting.
Green woodworking has a different set of criteria when it comes to stockpiling material. Unlike those who work with seasoned stock, those of use who use green wood try to keep a large log from drying at all; we want to rive and work the stock with a high moisture content. Ease of cutting is one principal reason for this.
One question I often get from people wanting to try their hand at this work is, “How long will the wood stay green?” With the oak I typically use, it’s an amazingly long time. Left in large unsplit sections, an oak log will begin to decay before it will truly dry. Over time, the sapwood will rot away, but inside, the heartwood will be wet, smelly and just as strong as the day it was felled.
As a result, I am a green woodworker who is usually in no hurry. Recently, I split and planed some red oak that was rough-split out more than a year ago. It’s not quite as easily worked as it would be if it were just felled, but the semi-dry wood is still within my strength limits.
A group I work with held the second annual Greenwood Fest in Plymouth, Mass., last summer. Among the leftovers were two hickory saplings that Tim Manney used to demonstrate making woven bark seats for his elegant ladderback chairs. Once Manney’s program was done, I quickly moved to stash the hickories, knowing I could make good use of them afterward.
Getting a Jump on Hickory
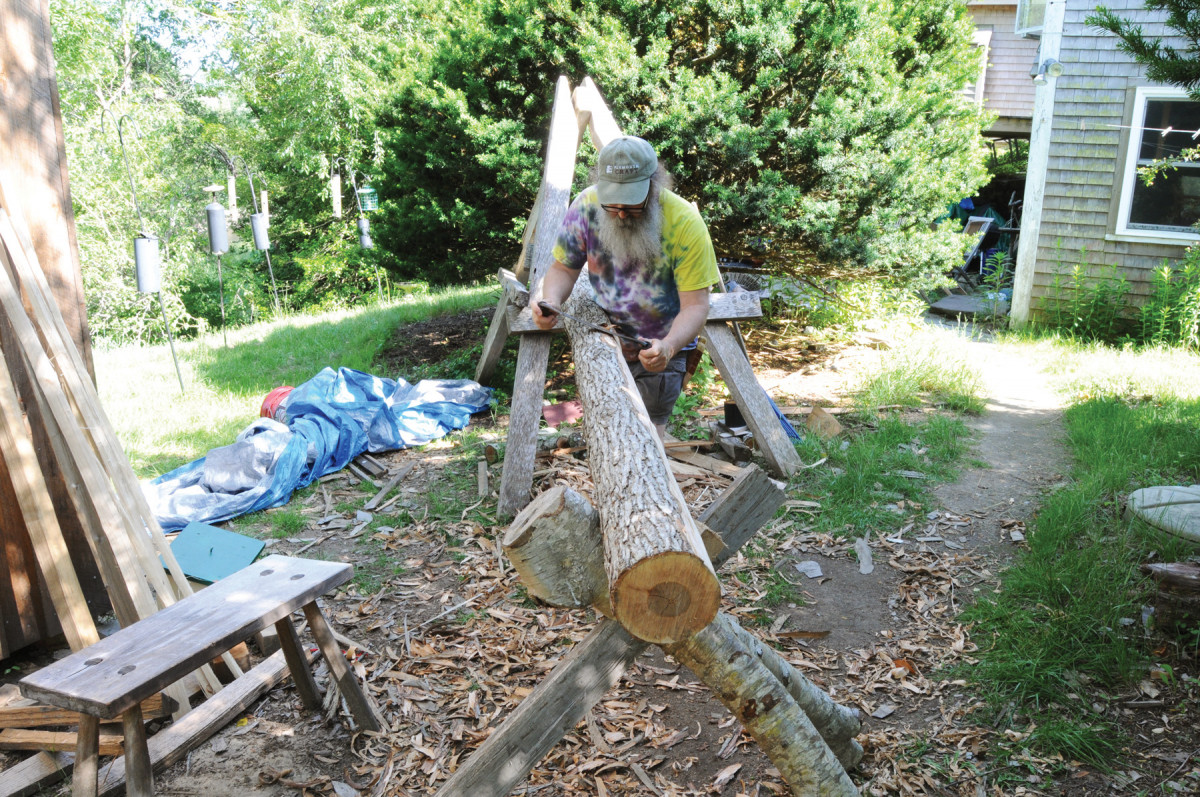
First the outside. Shaving off the crusty, tough outer bark is hard work. I place the piece in my riving brake and shave off about 3″ at a time, leaving the bark in place on the rest of the log. This helps prevent the inner bark from drying out if I get interrupted.
But hickory won’t wait. Neither, for that matter, will ash, maple and birch among others. So when I got settled after our festival, I jumped right on the hickory to strip the inner bark off the sapling and store it for future seat weaving and other similar uses. I propped the log up on a bench with one end stuck in my riving brake. Then I used a drawknife to shave away the rough, scaly outer bark. Under this layer is the stuff seat-weaving dreams are made of – the leathery inner bark that in the spring peels off the sapling like a 10′-20′ banana.
I tend to shave a swath of outer bark about 3″ wide down the length of the log, then score through the inner bark down to the wood with a sharp-pointed knife. Once that score is cut, I pry under the end of this inner bark and lift it slowly off the log. As I peel it, I look to make sure no fibers are sticking to the log. If they are, it’s usually because the scoring wasn’t deep enough. Get in there and snip it, then keep lifting.
I coil the strips into rolls then proceed to the next one. Once the first strip is off the log, it’s easy to see the thickness of the adjacent strips. This allows me to refine the shaving so I get an even thickness of the inner bark. Carefully shave this bark to a consistent thickness, then score it and peel it. Then coil it, and go on to the next strip.
I want to peel the whole thing in short order. Once the log starts drying, the bark doesn’t peel as easily. If I’m interrupted in this work, I leave the outer bark intact. That’s why I only shave off the outer bark a few strips’ worth at a time.
This stuff gums up the drawknife something awful, so hone your tool frequently as you work.
Use the Whole Sapling
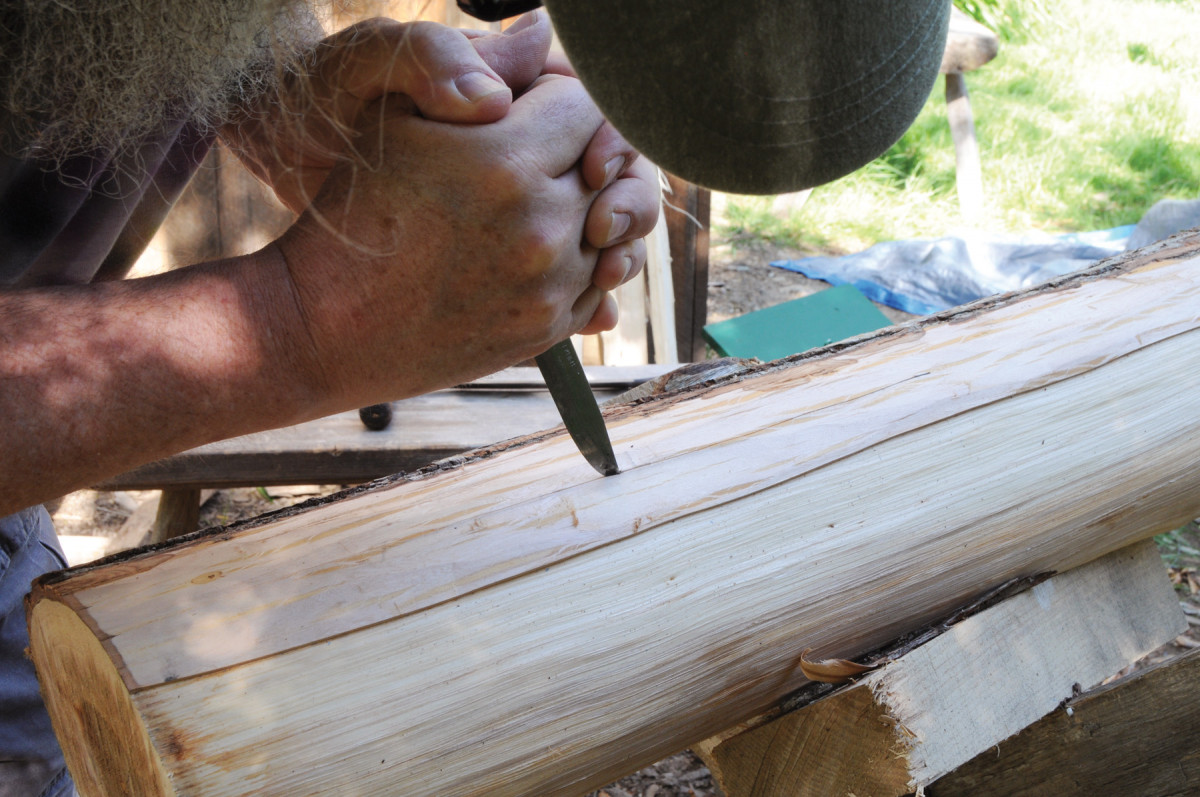
Score! After removing the hickory’s outer bark, score the inner bark with a knife to establish the strip width.
After I have the bark stripped, coiled and stored, then it’s on to the wood. The diameter of these trees was too small to make ladderback chair parts, but there was enough straight-grained wood for some bending parts. I started two firewood carriers, and bent various basket rims and handles.
This work is right smack in the middle of green woodworking – shaving horse, drawknife, steam-bending. Straight, clear hickory rives like almost no other wood I know. It shaves beautifully when green and gets like iron when it dries. That’s part of why you don’t wait with hickory.
The stuff with knots is destined for froe clubs, the wooden persuader used to knock the froe into the end grain when riving stock. I hew and shave down a handle, then let it dry before putting it to use. Green froe clubs self-destruct.
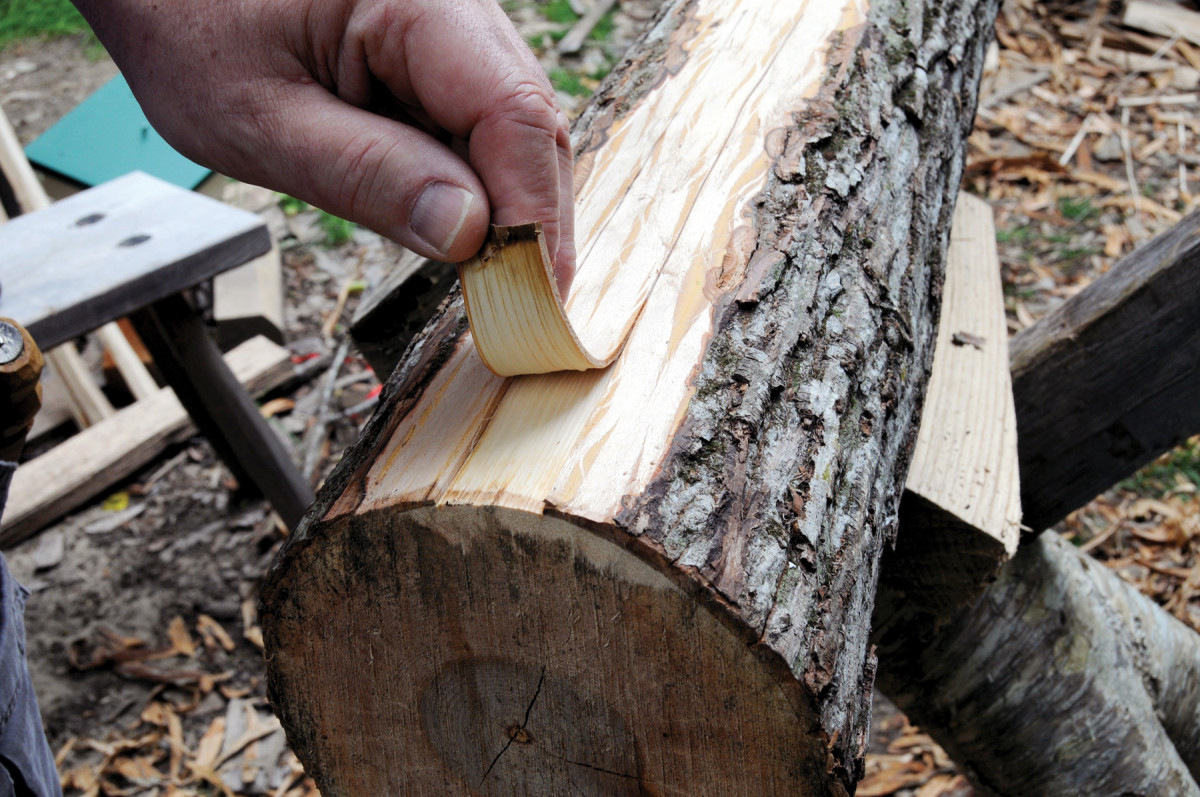
Inner bounty. After scoring the inner bark, I lift the end of that strip with my knife then peel the strip off down the log.
Any straight-grained leftover short bits will become tool-handle stock – I keep a stash of roughed-out stock for replacement handles. It makes perfect sense to save long stuff for axe handles and the like, but it can get ridiculous saving 4″-long pieces for chisel and gouge handles. I can’t resist though; hickory excels in impact applications. Why waste it? It can always burn later. As firewood, hickory is outstanding.
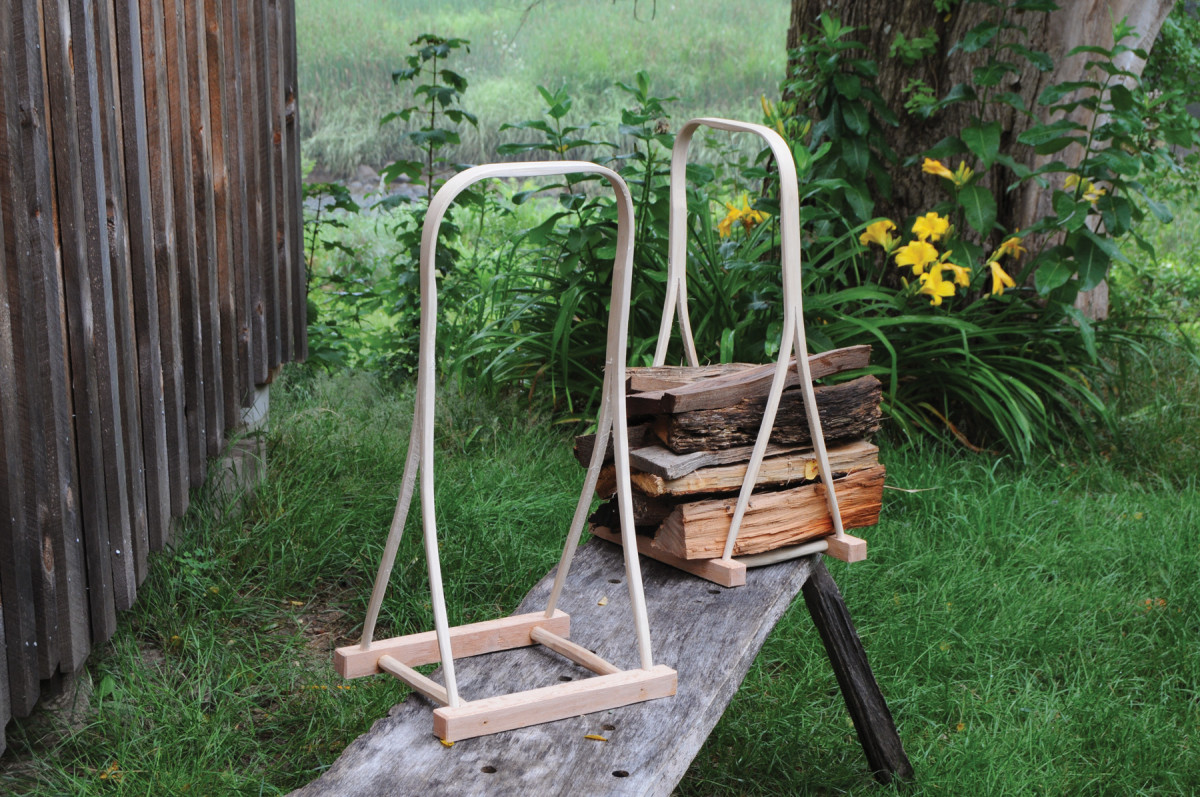
Wood-carrying wood. The bows for these firewood carriers are steam-bent from riven hickory. A clear riven piece of hickory is ideal for bending. I even prefer it over white oak, and that’s saying something.
It took me about three days to harvest the bark and work the riven wood of these two 10′ saplings. Time to get back to the red oak; I’ve got the hickory right where I want it now.
Here are some supplies and tools we find essential in our everyday work around the shop. We may receive a commission from sales referred by our links; however, we have carefully selected these products for their usefulness and quality.