We may receive a commission when you use our affiliate links. However, this does not impact our recommendations.
Mortise-and-tenon joinery and side-hung drawers make for a simple but impressive build.
Early in my career I met an avid antiques collector whose focus was objects from the William & Mary period. Like many people, my first reaction was, “That stuff with those big, ugly ball feet?” Under his guidance I began studying various periods of furniture and their corresponding decorative and fine arts. Learning about the furniture, metalware, paintings and other decorative objects from the periods surrounding William & Mary helped me to understand how crucial and pivotal this period is to furniture design and construction.
The more I looked at Pilgrim, Queen Anne and Chippendale furniture, the more I began to like the sheer simplicity of the William & Mary designs, including those “big, ugly ball feet.” After looking at countless examples, I no longer consider them big or ugly, and have come to appreciate the variety of designs.
The best thing about making a William & Mary chest of drawers is that it provides great skill-building exercises for the novice woodworker, yet enough challenge for an experienced builder. Whether you make ball feet (sometimes referred to as bun feet) is entirely up to you. This chest looks just as good with bracket feet as it does with bun feet.
The carcase is made up of two end frames with flat, floating panels that are joined with a few structural members. Once the case is together there are applied mouldings that dress it up. The dovetailed drawers are supported using an early method – side-hung drawer runners. You may not have tried this technique before, but give it a whirl – you may come to like it more than other traditional methods.
Lay it Out
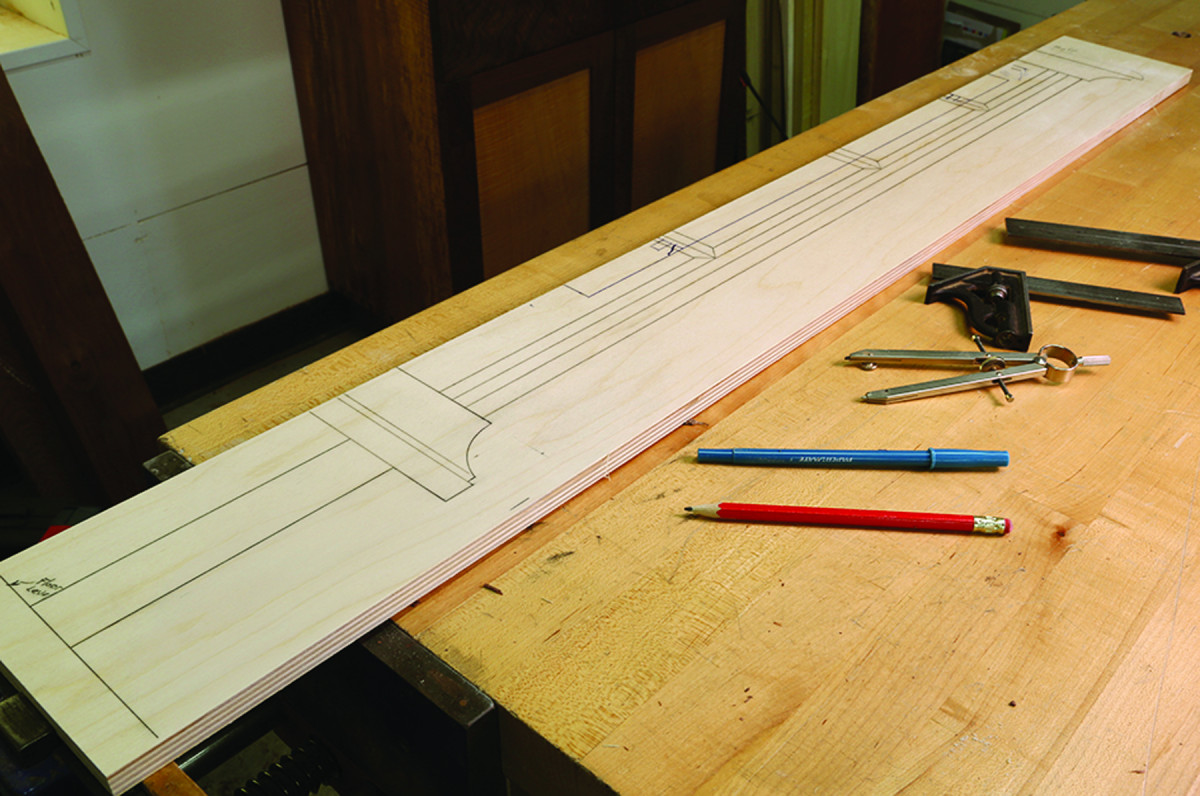
Layout stick. Using a full-sized sectional layout helps you avoid errors and visualize potential construction problems.
Even with a detailed computer model, the first thing I do when building any piece of furniture is make a layout stick. It helps me mentally build the piece before I’ve even selected the lumber. With a layout stick I can work out joinery problems before they become real, and I can double-check all my sizes because I’m drawing everything at full size. Plus, it helps identify the areas where I might need to pay particular attention.
In case you’ve never heard of a layout stick, it’s a simple sectional, full-sized mechanical drawing of each of the three views of a piece: height, width and depth. Occasionally, I’ll do special detail layouts as well, but for this project a three-section view is more than sufficient.
Another great reason to use a layout stick is that once you’ve double-checked all your measurements, you won’t need to use a tape or rule again during the construction process. Every time you measure, you introduce opportunities to cut things to the wrong dimensions.
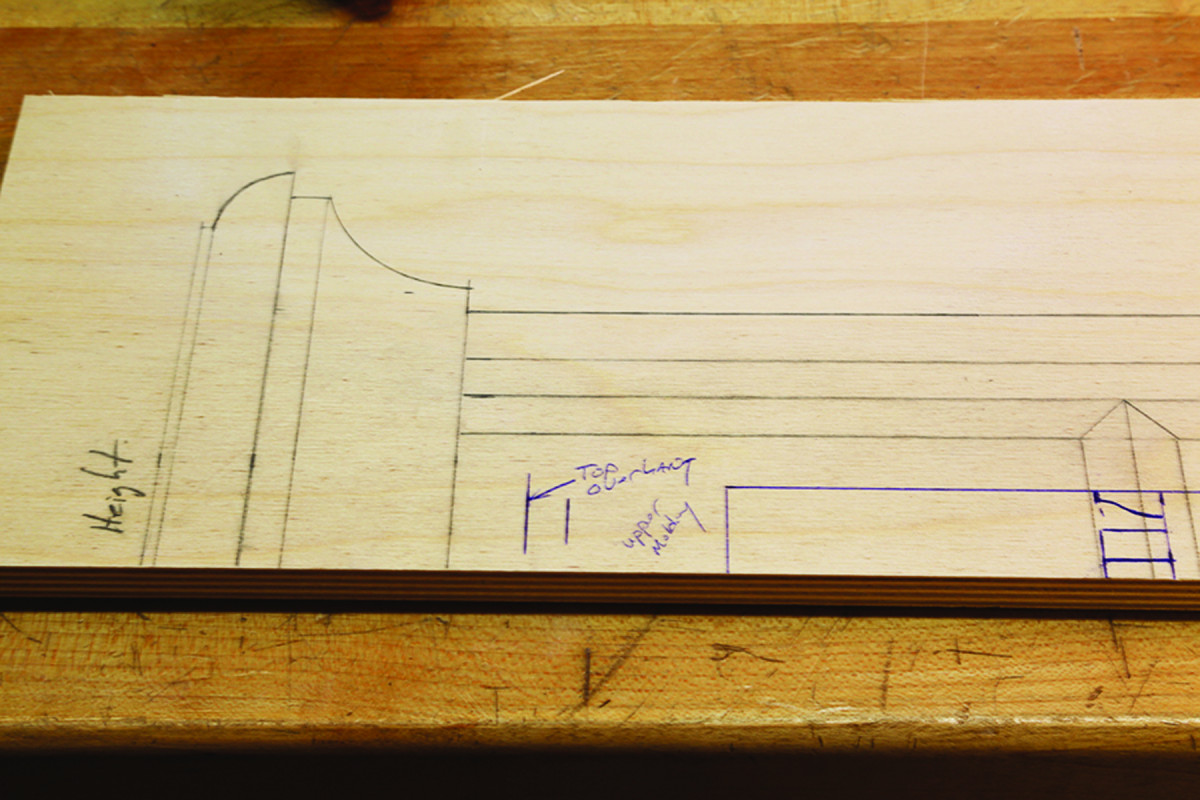
Info needed. Put as much detail on your layouts as you need, but keep it understandable. I use different colors for each of the three views.
Begin with a scrap of wood that exceeds the longest measurement on the chest, but is only as wide as necessary to draw the detail of a large part, in this case the width of a stile.
I begin with the height view by drawing a line that represents the floor, then I measure up and mark the overall height (here, that’s 383⁄4“). Measure down the thickness of the top and put a mark then do the same for the foot height, mouldings and all of the drawer blades. I also like to detail my layout sticks with moulding profiles and other pertinent details (parts that are hidden from view are represented by dashed lines).
It’s best if you make your layout stick as detailed as possible – without making it confusing. Sometimes, if you try to include every detail, the sheer number of lines can become so overwhelming that you render the layout stick useless. A good rule is to include each detail on at least one view; everything doesn’t need to be on all three. After the height layout is finished, I move to the width and depth layouts.
Figure it Out
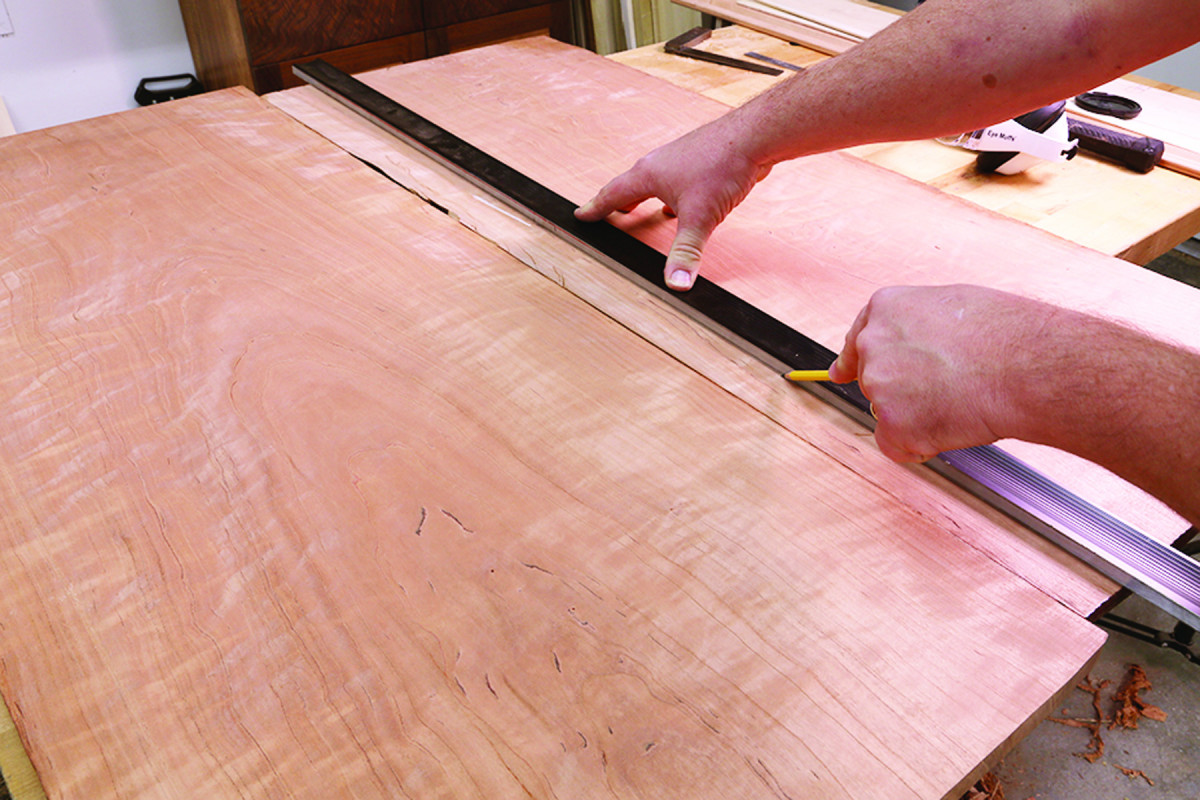
Figure match. Take the time to carefully lay out your materials to obtain optimal use of figured woods. Sometimes this means removing usable material to get the best match.
My next consideration with any project is wood selection. This is particularly important when building anything with frame-and-panel construction. I like to use straight-grained or quartersawn material for the stiles and rails to visually outline highly figured panels – but that’s not where the process ends.
Consider the visual balance of the individual pieces as well as how they will be part of a whole. I like to orient figure to give the piece a sense of symmetry and to draw the eye to various features.
This concept is particularly important when it comes to drawer fronts. If, for example, you’re using curly or striped material, you don’t want all the stripes angled in one direction because that would make your piece look as though it leans to one side.
While you can use highly figured material throughout an entire piece, that tends to visually homogenize the wood rather than accentuate the grain. When composing with wood, it’s worth taking the time to get your materials properly laid out before you start building.
Frame it Up
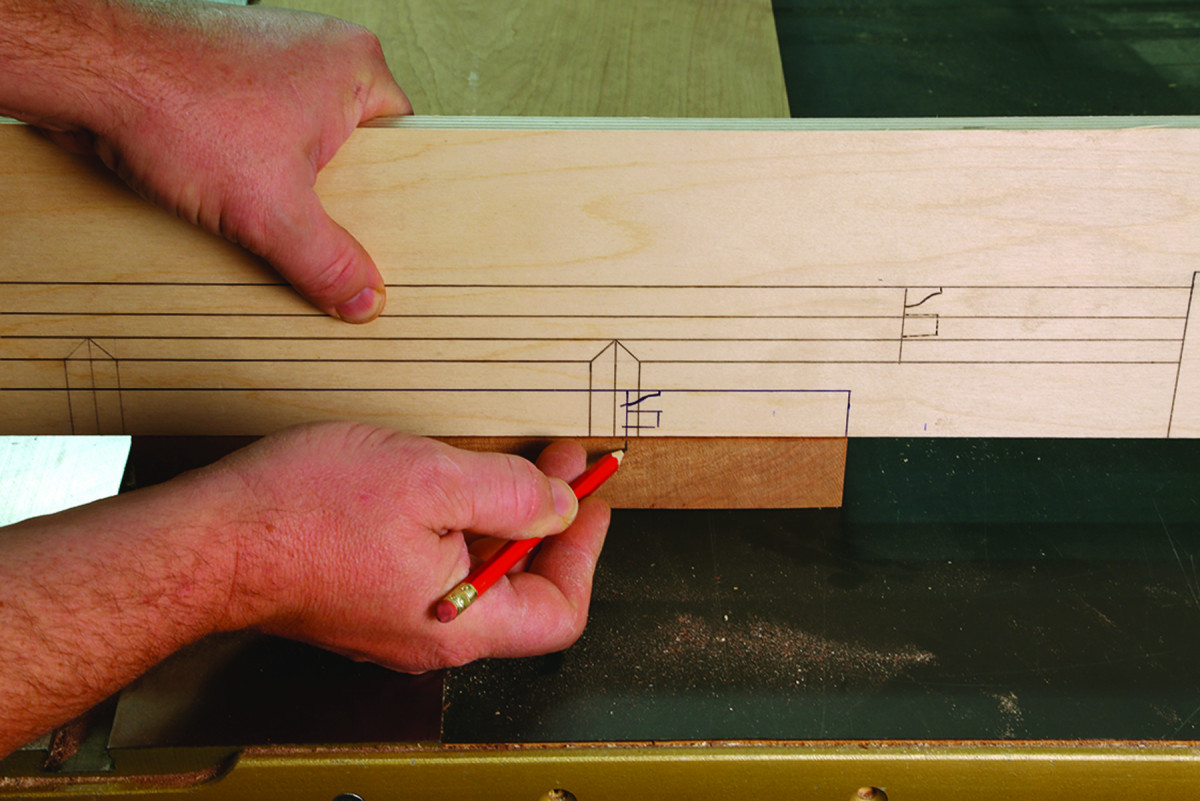
No measuring. Transferring dimensions directly from the layout stick to the material reduces the potential for miscuts.
With your lumber milled to rough size, the best place to start is to make the frames for the case ends. Working directly off the layout stick, you can quickly and easily mark all your parts to final dimension. Joint the edge of your stiles and rails then take them right to the layout stick; if you line up the jointed edge with the appropriate mark on the layout stick, you can directly mark the width of the pieces. At the table saw, rip them appropriately.
To cut them to length, square one end and use the layout stick to transfer the final length before you cut. Whether you’re working with power tools or only hand tools, having a single benchmark (your layout stick) from which to mark multiple parts increases your accuracy.
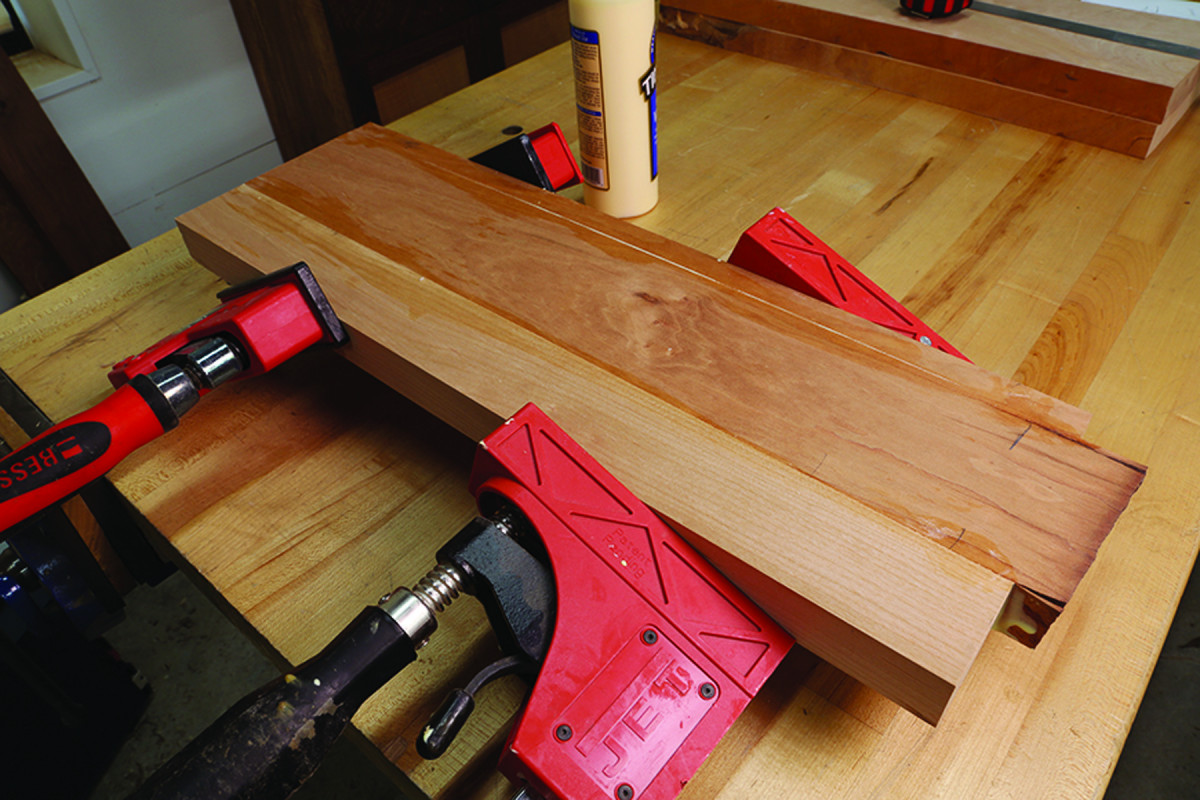
Add a little. Sometimes the materials just don’t cooperate. In this case, the lumber for the bottom rails wasn’t wide enough. I scabbed on one strip that will be covered by the base moulding at the glue line, and another for the sticking, in which the seam will fall at the fillet.
Now that the stiles and rails are cut to size, I “stick” the edges of the pieces. (“Sticking” is the term used for running a moulded edge.) There are a couple of ways this can be done; I prefer a router.
This chest has a cyma recta moulding along the edge of the stiles and rails. Most commercial router bits are too exaggerated to provide the proper look. But if you think of your router as a motorized version of a set of hollows and rounds, the moulding is easy to make.
Begin by sketching the profile onto the end of a scrap that’s milled to the same thickness as the stiles and rails. If you’re not good at drawing, use tracing paper and copy the profile from the drawings provided. Whether you are using hollows and rounds or a router, you can benefit from cutting rabbets and chamfers to remove the bulk of the waste. This step helps ensure more uniform mouldings throughout.
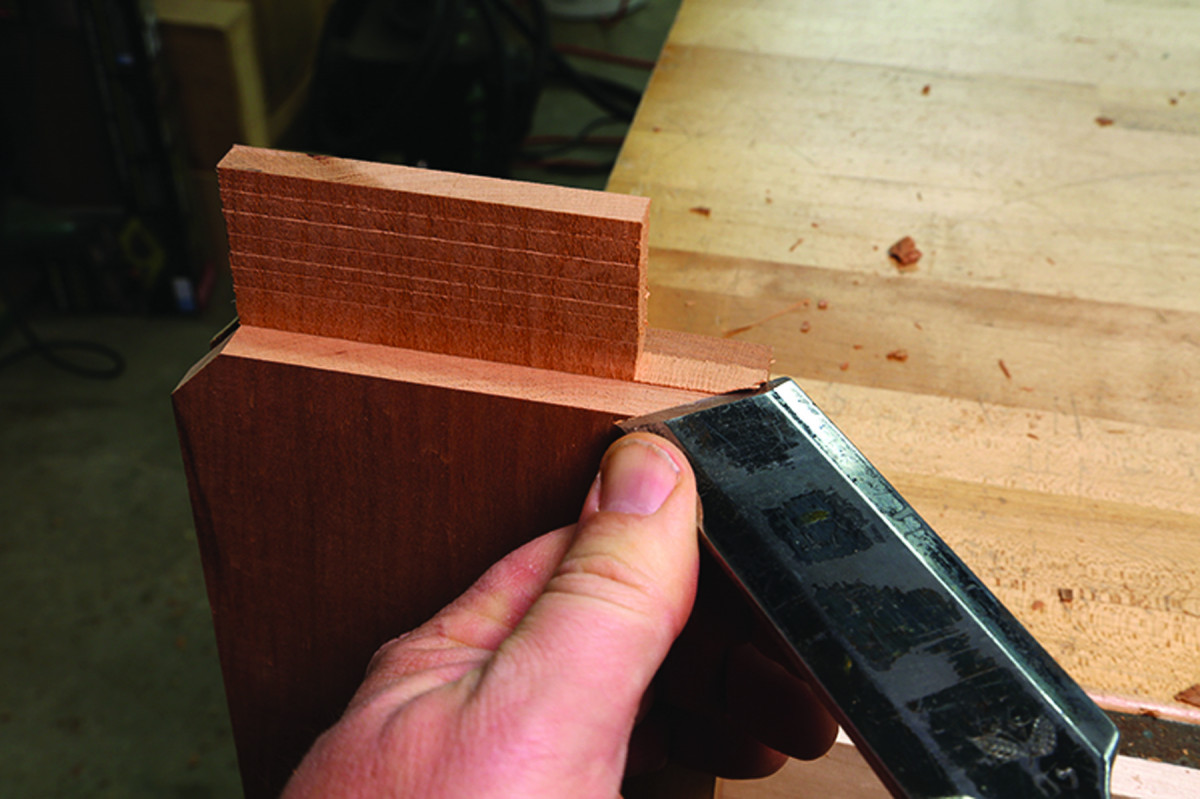
Paring. Use a chisel to clean up the shoulder after you’ve cut the haunch.
Using an appropriate core-box or round-nose router bit, run the hollow portion of the cyma curve. To cut the convex or round portion of the curve, I find a shoulder plane easier to use to achieve the shallow arc than using a commercial router bit – a No. 6 hollow plane does the trick nicely as well.
After running the sticking, head to the table saw and use a dado stack to run a 3⁄8“-wide x 5⁄8“-deep groove for the panel in all eight frame pieces. The groove does several things; most importantly, it gives me a place to align my mortises, and it serves as a haunch on the inside edge of the frame parts.
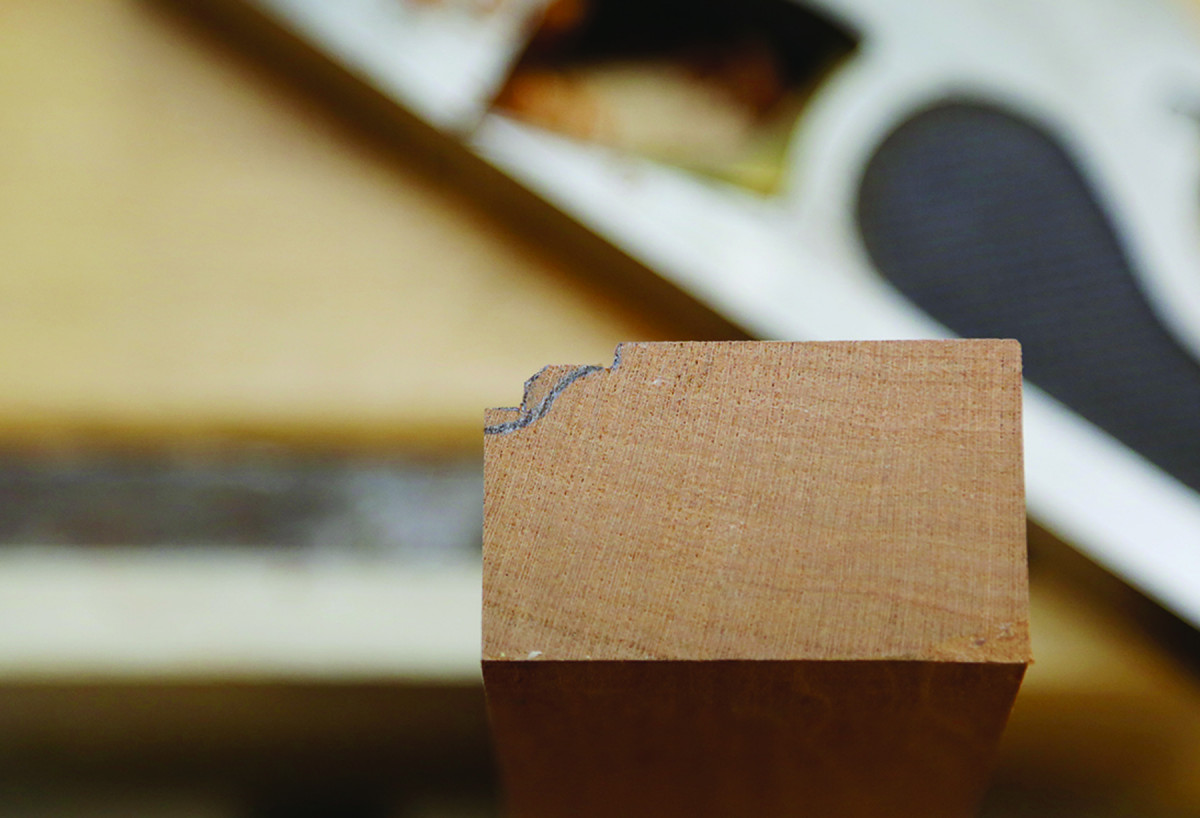
Make it easy. You’ll get a cleaner cut off the router bit if you rabbet and chamfer the workpiece prior to running the profile on the stiles and rails.
The top rail tenons are haunched 1″ off the outside edge; the bottom rails are haunched at 13⁄4“. With the mortises laid out on the stiles, grab your favorite 3⁄8” mortise chisel (mine fits into a hollow-chisel mortiser) and chop them. Once you’re set up, it makes sense to cut all your mortises at the same time. So use your layout stick to mark the mortise locations on the stiles for the drawer blade and the vertical drawer divider mortises, then cut them, too.
Now cut the drawers blades and center divider to final dimensions before moving onto the tenons – as with the mortises, it’s more efficient to cut those in one session.
I use a dado stack to make my tenons. It’s quick and cuts the cheeks and shoulders in one motion. After cutting the tenons, the miter cuts (that allow the stuck moulding to meet nicely in the corners) need to be marked. Forego using the layout stick for this. At several points in any build, using the layout stick becomes counter-productive. The layout is theoretical; the real parts give you actual dimensions. Always go with the actual dimensions when you can. I align the stiles and rails, then transfer the miter locations directly from one frame member to another.
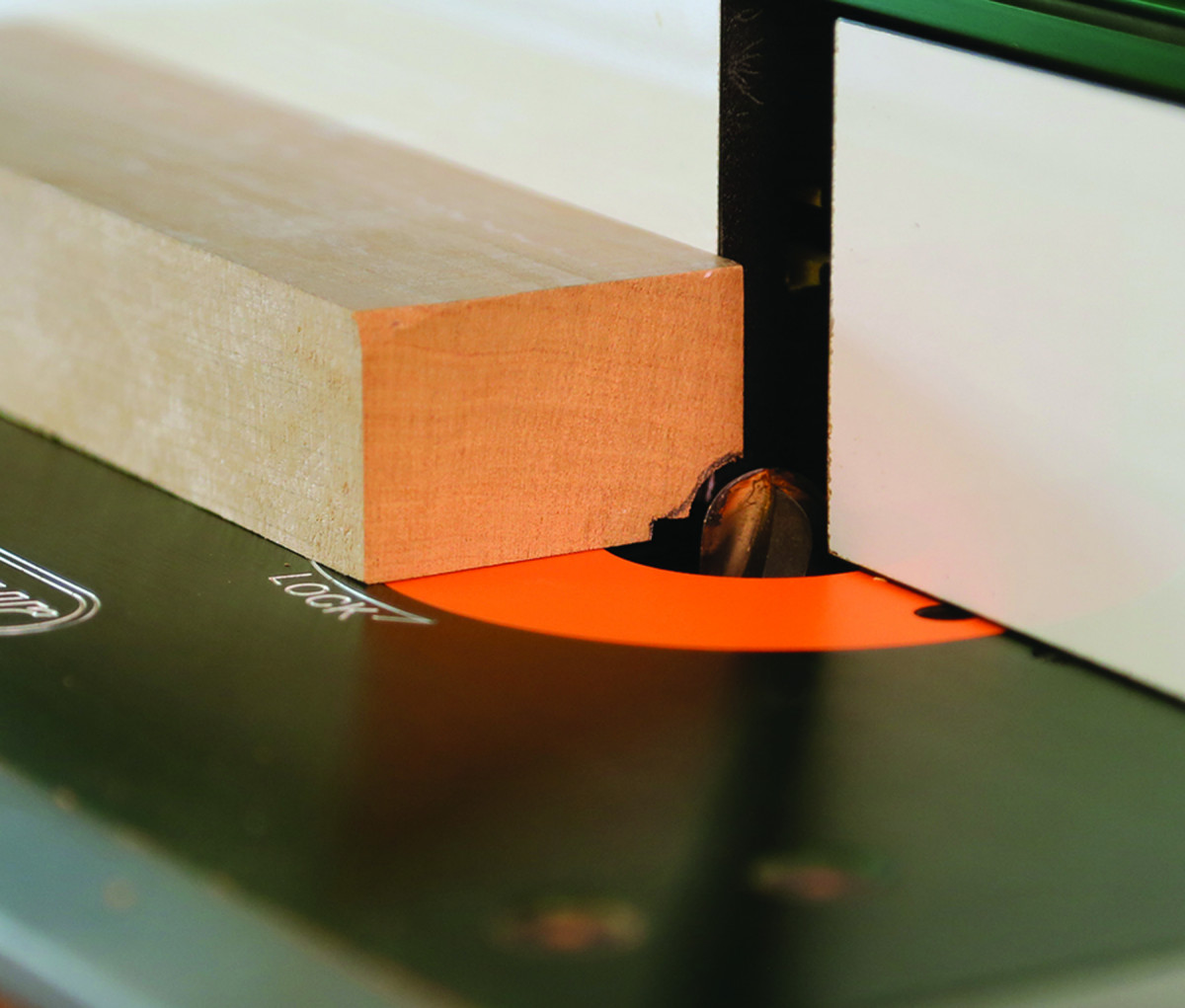
Half cyma. Using a round-nose router bit to make the concave portion of the cyma recta moulding allows you to get the proper shape without specialized tooling.
Tilt the table saw blade to 45° and, using the rip fence as a stop (one position for the rail cuts and a second for the stile cuts), cut the miters. Set the stop to leave the miters a little heavy. They are easily adjusted by passing a handsaw through the assembled miter to remove minute bits of excess material until the tenon shoulders and miters come together.
With the miters cut on the frame moulding, you still need to remove excess sticking material from the stiles. My preferred method is to use the jointer. I set the depth of cut to match the width of the sticking (on some frames this could be considerable, so be careful when using the machine). In one deep pass, I remove the waste, stopping just short of the cutline. Then I clamp the stile in a vise and pare away the remaining waste.
Dry-fit the frames and cut the panels to size, using the actual frames for the dimensions, not the layout stick. Then bevel the inside face so the panel fits into the stile-and-rail grooves. Now it’s time to prepare for assembly.
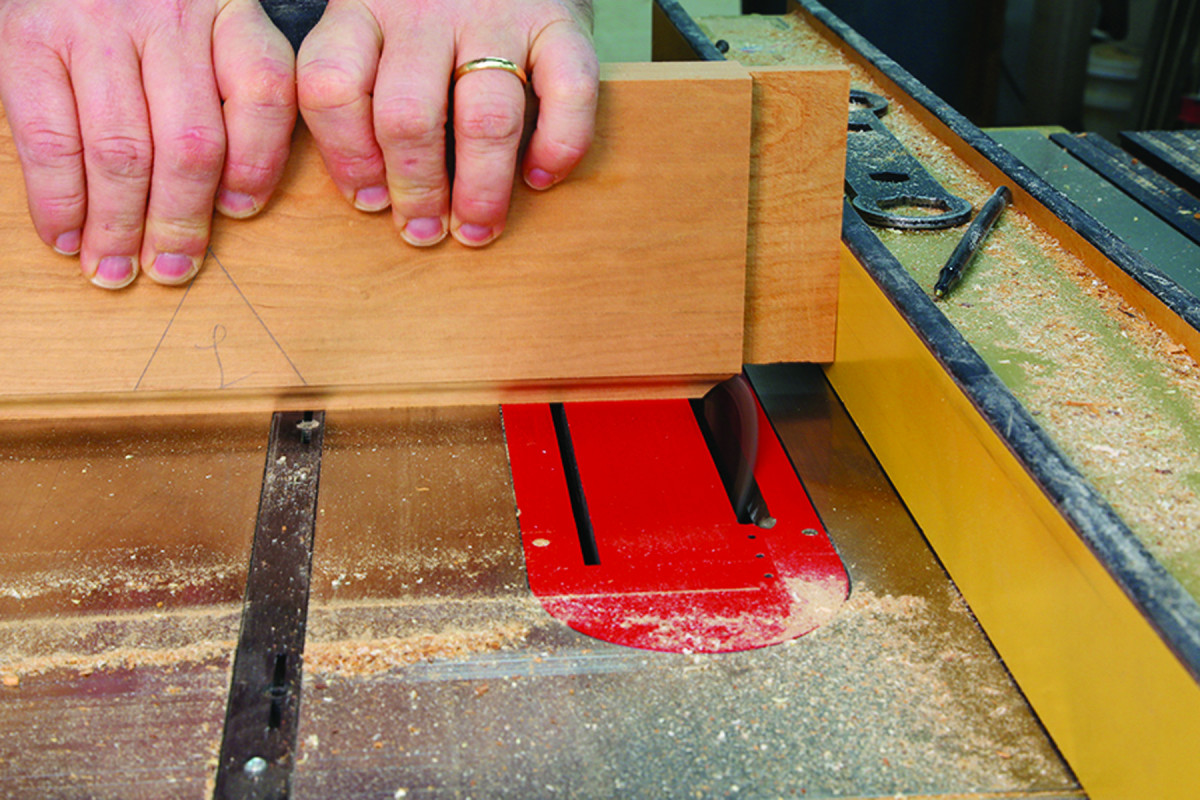
Stop miter. Use the rip fence as a stop to make accurate miter cuts a breeze. (Use the miter gauge to guide the workpiece.)
Begin by marking the peg locations on the stiles (see the drawing at right). Drill 5⁄16” holes for the pegs at the drill press. Dry-fit the mortise-and-tenon joints, making sure to transfer the peg-hole locations onto the tenon cheeks. Disassemble the frames to drill the same size holes in the tenons. Offset the holes about 1⁄32” toward the shoulder to take advantage of drawboring the joint.
You’ll need to make some pegs out of straight-grained cherry. Rip the stock to 5⁄16” x 5⁄16” and cut pegs that are slightly longer than the thickness of the frame parts (about 1⁄4” longer should do). Use a chisel to sharpen the pegs to a blunt point (a pencil sharpener also works well for this).
With the joints ready to go, I use a cabinet scraper to remove all the machine marks on the interior and exterior surfaces. After I have all the parts of the frames scraped, I sand the outside faces of the panel and frame, as well as the sticking. Slather up the mortises and tenons with your favorite glue and assemble the frames. Lock the joints in place by driving the pegs home; a little beeswax on the peg sides helps them glide through the offset holes.
William & Mary Chest Cut List
No.ItemDimensions (inches)MaterialComments
t w l
❏ 2 Front stiles 1 1⁄4 x 3 3⁄8 x 32 Cherry
❏ 2 Back stiles 1 1⁄4 x 3 3⁄8 x 38 Cherry
❏ 2 Top rails 1 1⁄4 x 5 x 19 3⁄4 Cherry 2″ TBE*
❏ 2 Bottom rails 1 1⁄4 x 6 1⁄4 x 19 3⁄4 Cherry 2″ TBE
❏ 2 Panels 3⁄4 x 15 3⁄4 x 22 Cherry
❏ 1 Case bottom 7⁄8 x 19 3⁄4 x34 Poplar
❏ 1 Top front rail 7⁄8 x 1 5⁄8 x 34 1⁄4 Cherry 3⁄4″ TBE
❏ 1 Bottom front rail 7⁄8 x 2 1⁄8 x 34 1⁄4 Cherry 3⁄4″ TBE
❏ 3 Drawer blades 3⁄4 x 2 1⁄2 x 34 1⁄4 Cherry 3⁄4″ TBE
❏ 1 Back drawer blade 3⁄4 x 2 1⁄2 x 34 1⁄4 Cherry 3⁄4″ TBE
❏ 1 Drawer divider 3⁄4 x 2 1⁄2 x 6 1⁄2 Cherry 3⁄4″ TBE
❏ 1 Back cleat 7⁄8 x 2 3⁄4 x 35 1⁄4 Poplar 11⁄4″ DBE**
❏ 1 Runner support 3⁄4 x 6 x 17 3⁄8 Poplar
❏ 1 Top 3⁄4 x 24 x 38 1⁄8 Cherry 15⁄16″ back overhang
❏ 2 Cove mouldings 1 3⁄8 x 2 1⁄8 x 96 Cherry Base mould cut down
❏ 6 Double-arch mould 3⁄16 x 3⁄4 x 36 Cherry Cut to fit
❏ 2 Drawer fronts 7⁄8 x 5 x 16 Cherry
❏ 1 Drawer front 7⁄8 x 6 x 32 3⁄4 Cherry
❏ 1 Drawer front 7⁄8 x 7 x 32 3⁄4Cherry
❏ 1 Drawer front 7⁄8 x 8 x 32 3⁄4 Cherry
❏ 10 Drawer runners 1⁄4 x 8 x 19 1⁄4 Oak Nailed to stiles
❏ 1 Back 1⁄2 x 32 x 34 Poplar Multiple pieces
❏ 2 Foot dowels 7⁄8 x 7⁄8 x 6 7⁄8White oak
❏ 2 Feet 5 1⁄2 x 5 1⁄2 x 6 Cherry Glued up
*TBE = Tenon both ends **DBE = Dovetail both ends







Get it Together
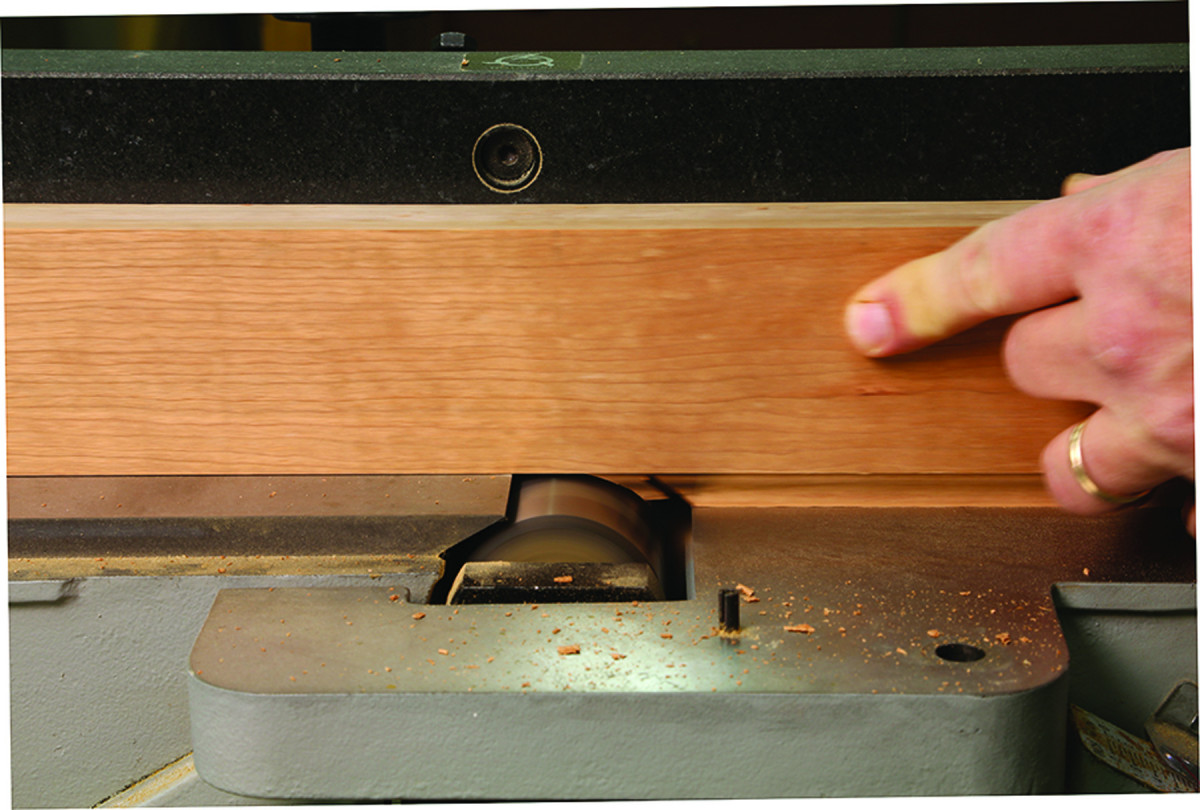
Waste removal. At the jointer, a single pass to remove the sticking waste is fast and accurate.
While the glue dries on the frames, mark out and cut the center waste on the three drawer blades’ double tenons. Hold the drawer blades in place on the end assembly and transfer marks from the inner face of the mortises to the ends of the blades. These become the inner cheeks of the double tenons. I find it best to cut these on the band saw. A little paring with a chisel is usually needed for a proper fit.
Also fit the single tenons of the top and bottom front rails, and the double tenons on the drawer divider, which fits into both the top front rail and the drawer blade immediately below.
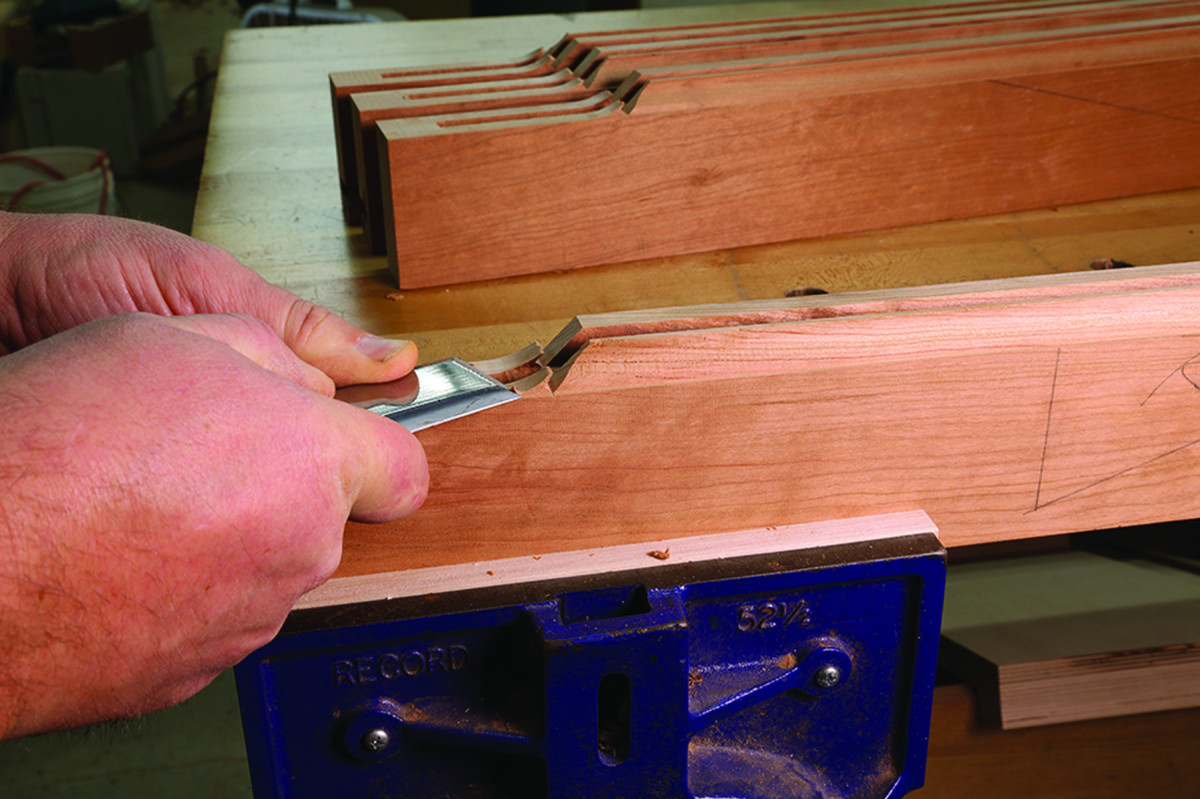
Clean it up. After jointing off the waste, use a sharp chisel to pare the shoulder to the miter.
With the frame glue dry, level the mortise-and-tenon joints with a cabinet scraper, plane or sander. Set the frames inside up on a worksurface and lay out the 5⁄8” x 5⁄8” stop rabbets for the backboards, and the 5⁄8” x 7⁄8” rabbet for the case bottom. I use an edge-routing jig and router with a straight bit to make these cuts.
The next step is to dovetail the back cleat into the top end of the rear stiles.
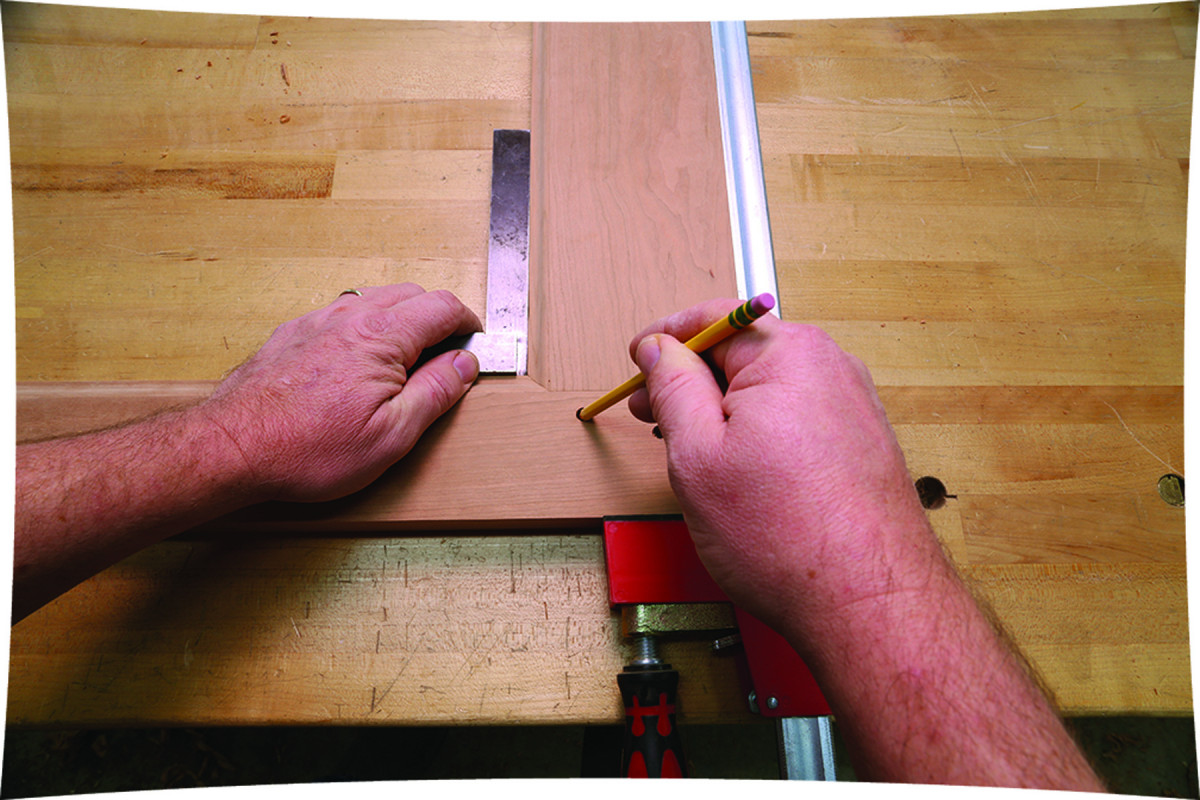
Transfer the mark. With the frame dry-assembled, it’s easy to transfer the location of the peg holes to the tenons.
Dry-fit the entire case to determine the dimensions for the drawer runner support. (Its sole purpose is to hold the drawer runners on which the top two drawers slide.) In typical early 18th-century fashion, this support piece is notched around the drawer divider and top rear cleat. It’s then nailed into place at the front and back after the case is glued-up. Prep all the case parts and glue up the carcase.
Dress it Up
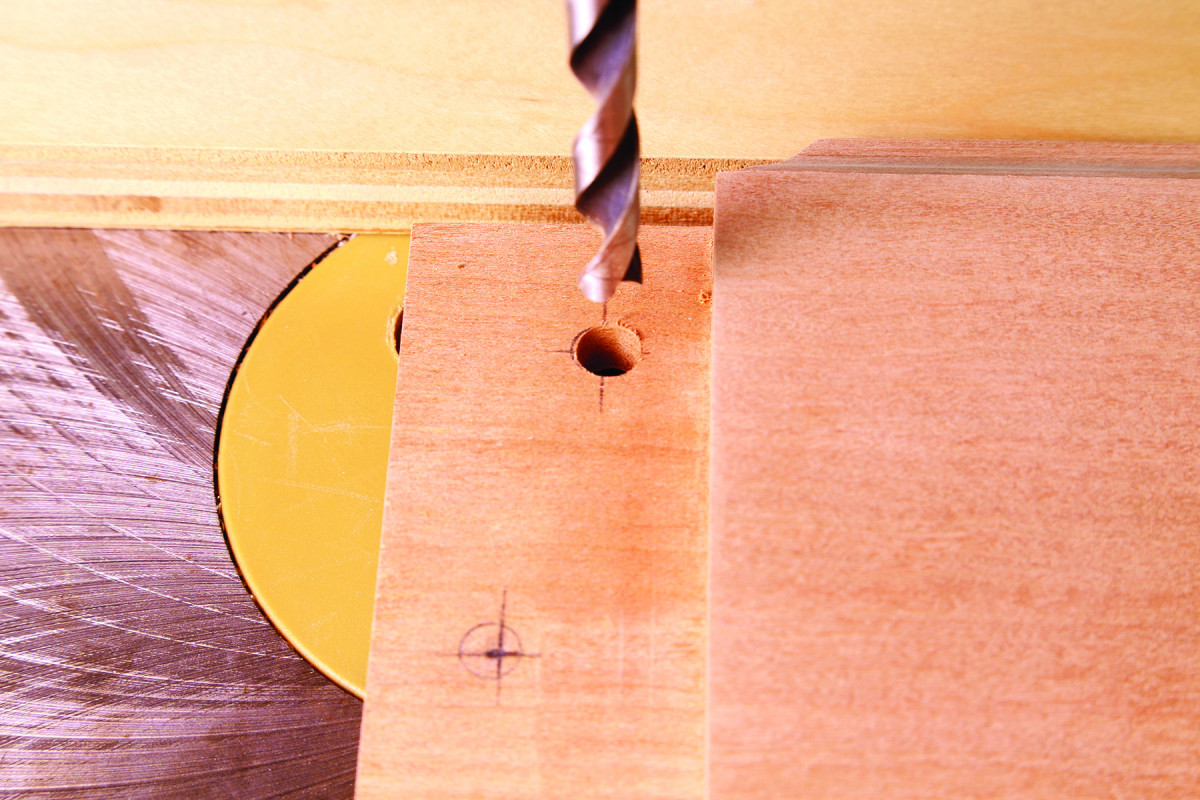
Offset the hole. At the drill press, offset the tenon’s peg hole about 1⁄32″ toward the shoulder to drawbore the joint tight.
While the glue dries on the carcase, all the case mouldings can be made. It’s fairly common on early pieces to find upper and lower mouldings that use the same plane in different ways. For the upper and lower mouldings, I’ve used the same radius, but modified the overall size by making the lower moulding taller and deeper than the upper moulding by adding a 3⁄32” step and a vertical flat.
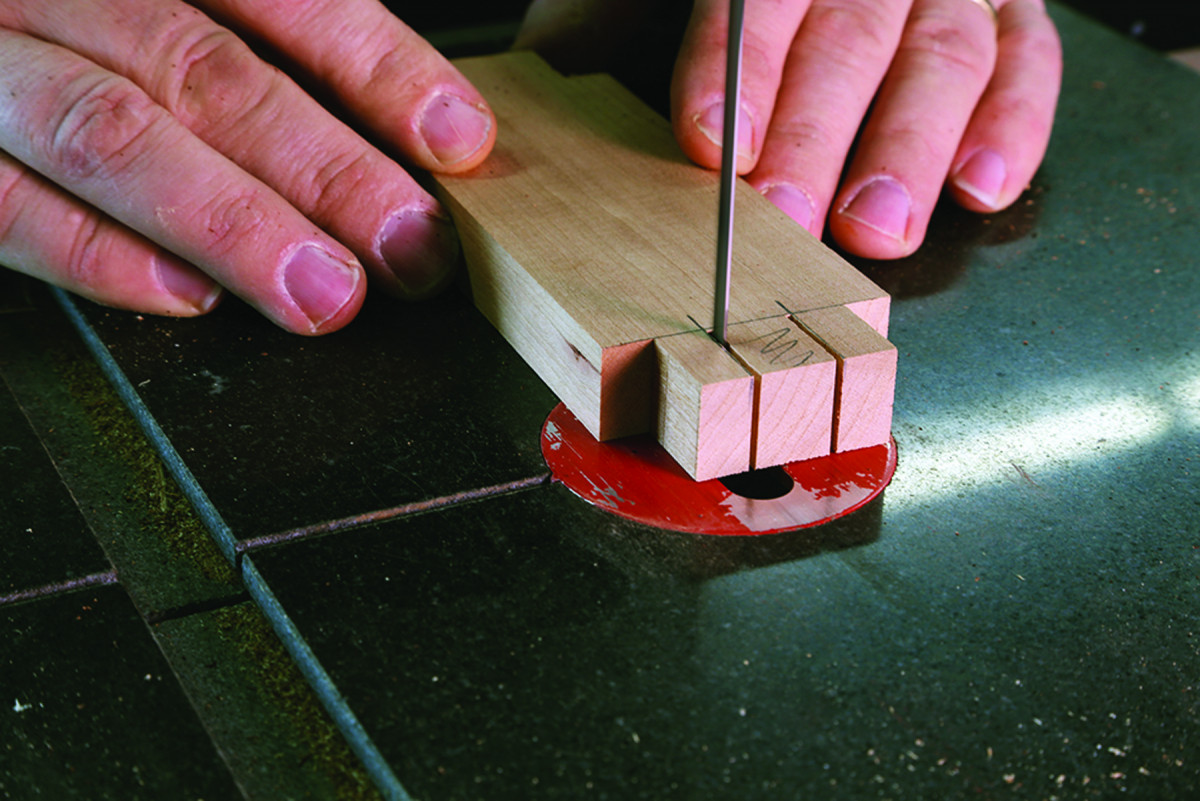
Quick twin tenons. Transfer the inside lines from the stiles, then trim the waste on the band saw on all the double tenons. They will most likely need paring to fit perfectly.
Because the coves are made at the table saw, there is a single setup to make the foundation of both the upper and lower mouldings. Use tracing paper to draw the profiles on the ends of the blanks to help orient things properly. Position and attach an angled fence on the table saw, then run the blanks diagonally through the saw to create the coves. (For more on how to make cove moulding on the table saw, see the online extras.) Use the drawn profiles to set the saw to the various angles needed to complete both mouldings.
One quick tip: I like to prep (with a scraper, No. 18 round or sandpaper) the cove portion of the mouldings prior to making the angle cuts. This way the moulding blank lies flat on the bench and is easily gripped between a tail vise and bench dog.
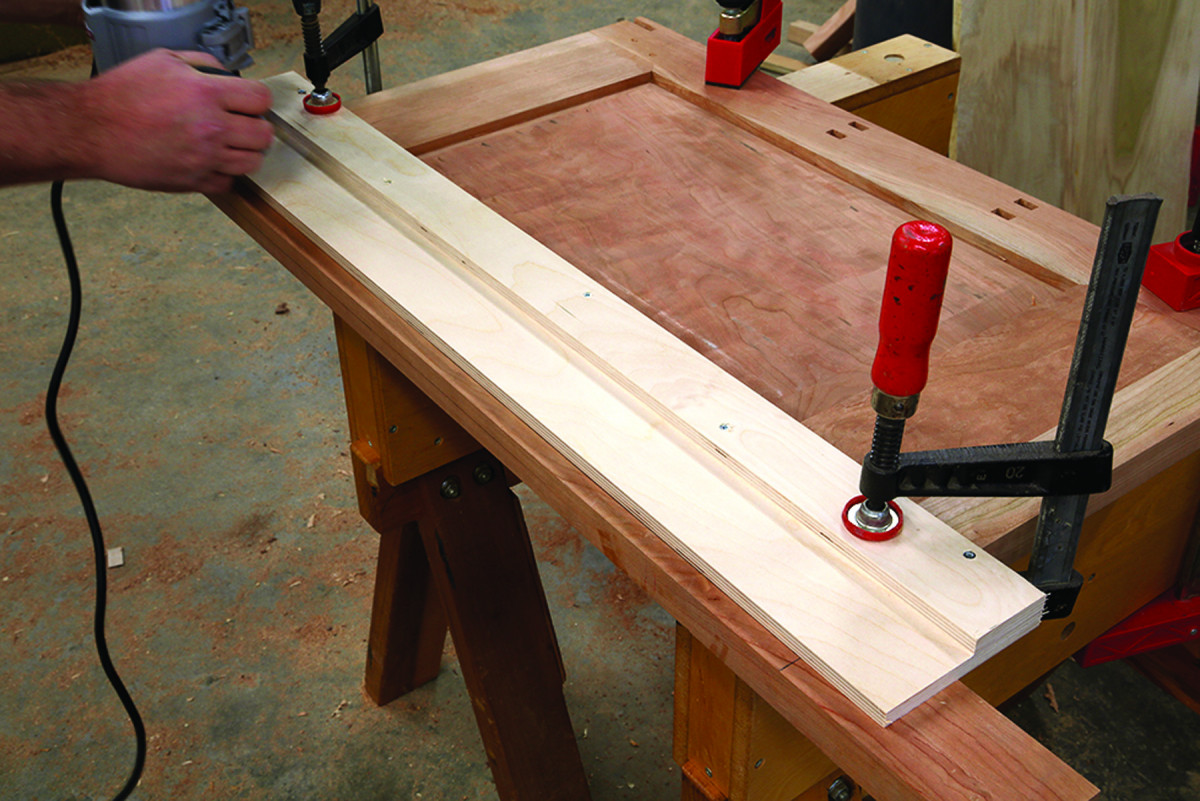
Rout it. Using an edge-routing jig to make dados and rabbets just means lining the jig up with the layout line then routing to the proper depth. It also makes cutting the stop rabbets for the backboards easy.
The double-arch moulding can be made using a stock 3⁄8” bead cutter or moulding planes. (You can use short sections of stock here; no need to stick a continuous 18′ run.)
Run the double-arch mouldings on the edge of a wider blank; that makes it easier to hold the workpiece in a vise for sanding before you rip the moulding free.
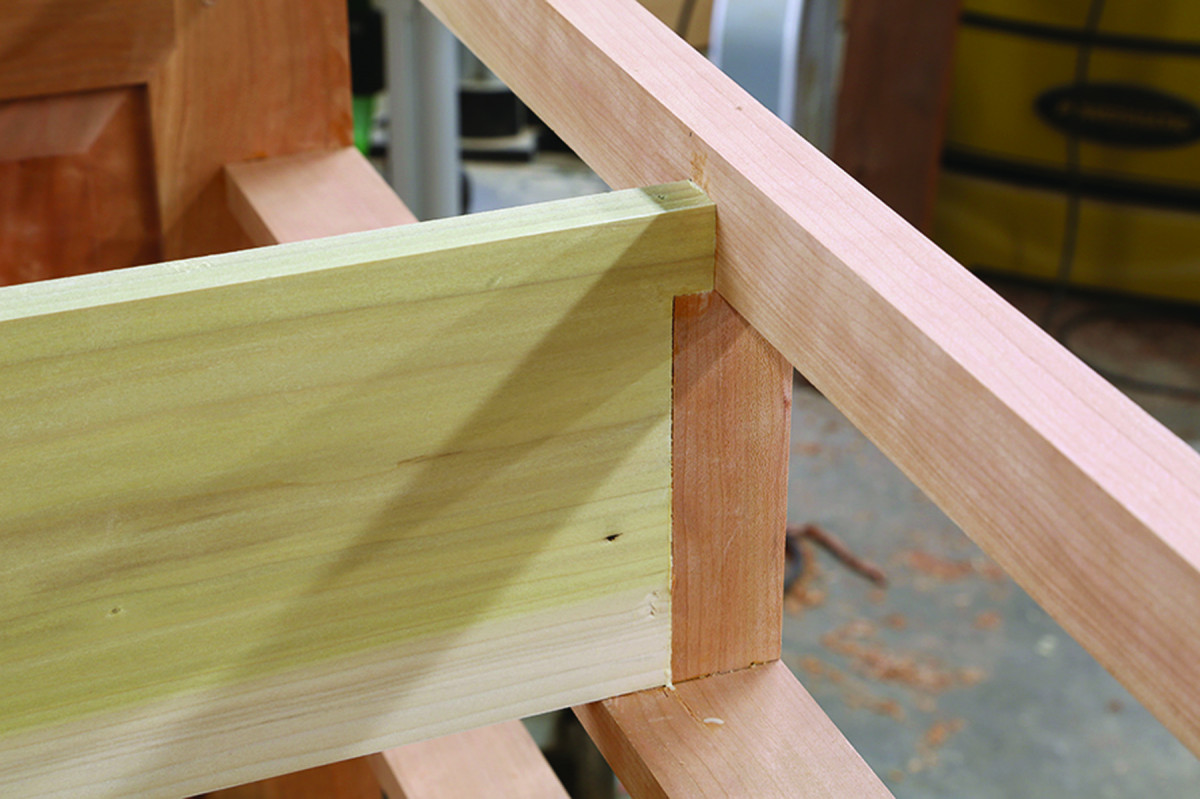
Notch it. The poplar drawer-runner support is notched around the back cleat and drawer divider, then just nailed into place.
Before attaching the upper and lower mouldings, cut the top to size and install it. Measure the dimensions of the carcase and add the appropriate overhang for the sides and front (17⁄16“), and the back (15⁄16“). Yes, I said back. Another fairly common practice on period furniture is to have the top overhang the back. When the piece is pushed against the wall, the top clears the baseboard and chair rail, preventing your stuff from being trapped between the chest and the wall.
After the top is cut to size, run an ovolo along the front edge and ends using a 1⁄2” roundover bit. There is about a 3⁄32” flat at the top of the ovolo, which means the router bit falls short of the bottom edge. Sandpaper easily knocks off any residual line.
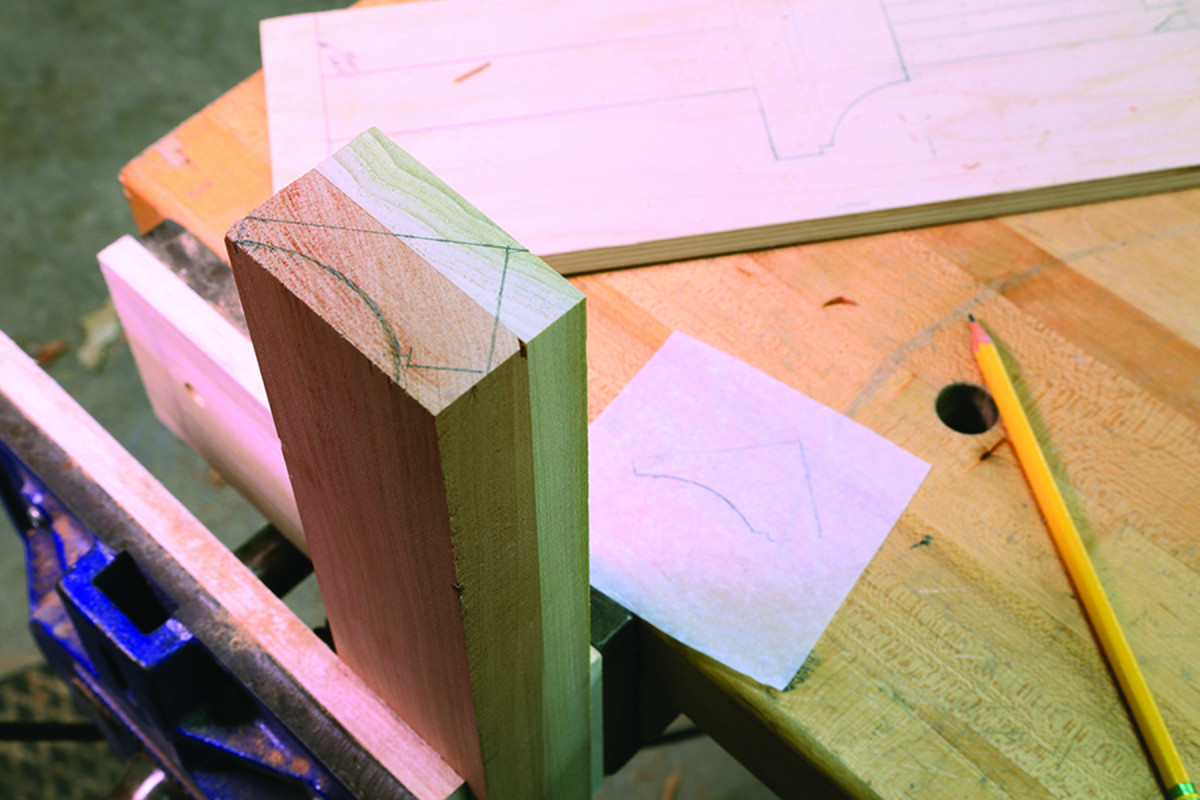
Moulding layout. Thick stock isn’t always available. “Packing out” the back side of mouldings has been a practice in use for centuries. I’ve laminated a piece of poplar to each cherry moulding blank. The profile is transferred from my layout stick to the end of the moulding.
After the glue dries, level the joints (if needed) and remove any clamp damage to the case then attach the top. Simply align it properly and drill through the top into the stiles. The pegs on this chest are 5⁄16” square. It’s better to drill that size hole through the top and a slightly smaller hole into the framework. (I reduced the diameter by about 1⁄32” for this cherry. In pine I’d reduce it more.) This allows for the compression of the fibers in the peg as it passes through the top.
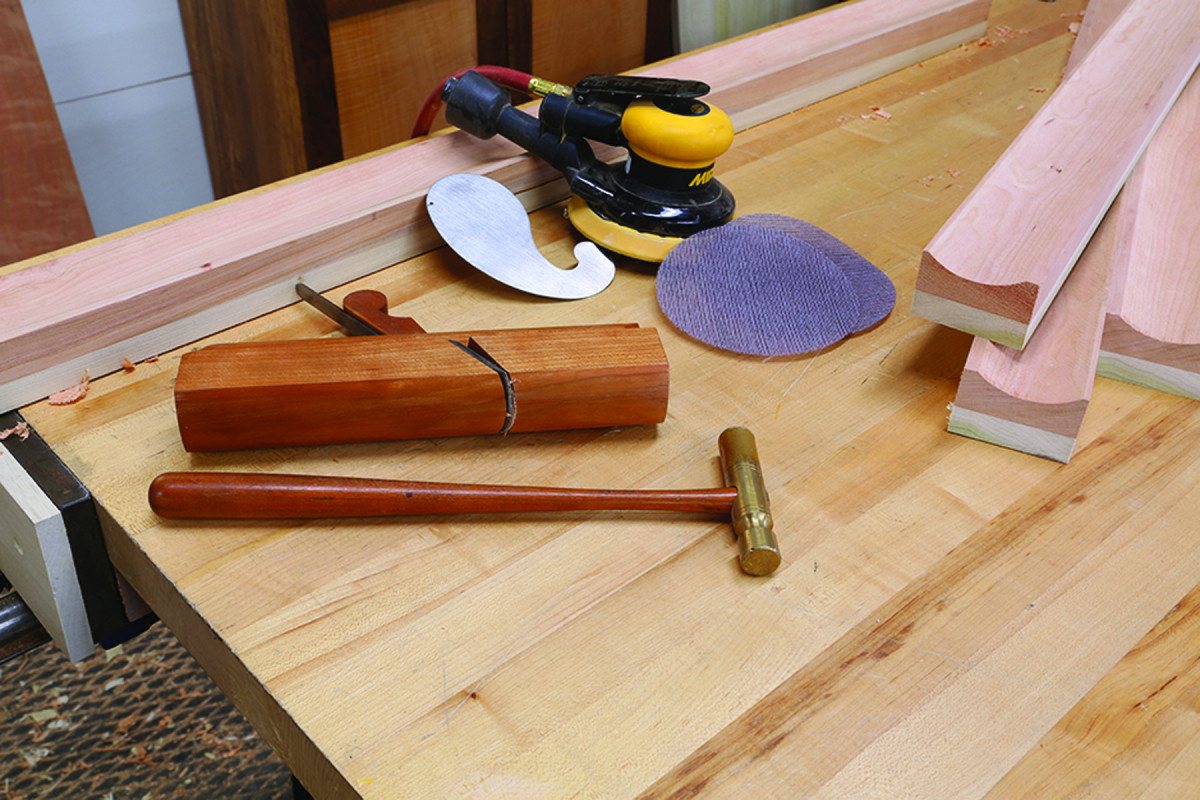
Moulding prep. I typically scrape, or plane and sand, the blank prior to finishing off the moulding. This way I don’t inadvertently obliterate additional elements of the moulding.
If the holes in the top and frames were exactly the same size, there’s a chance that the pegs might not grip the stiles. If you want a removable top, this is the way to go, but I like mine permanently attached. Once the top is pegged in place, wrap the upper and lower mouldings on the carcase then fit the double-arch mouldings around the drawer openings.
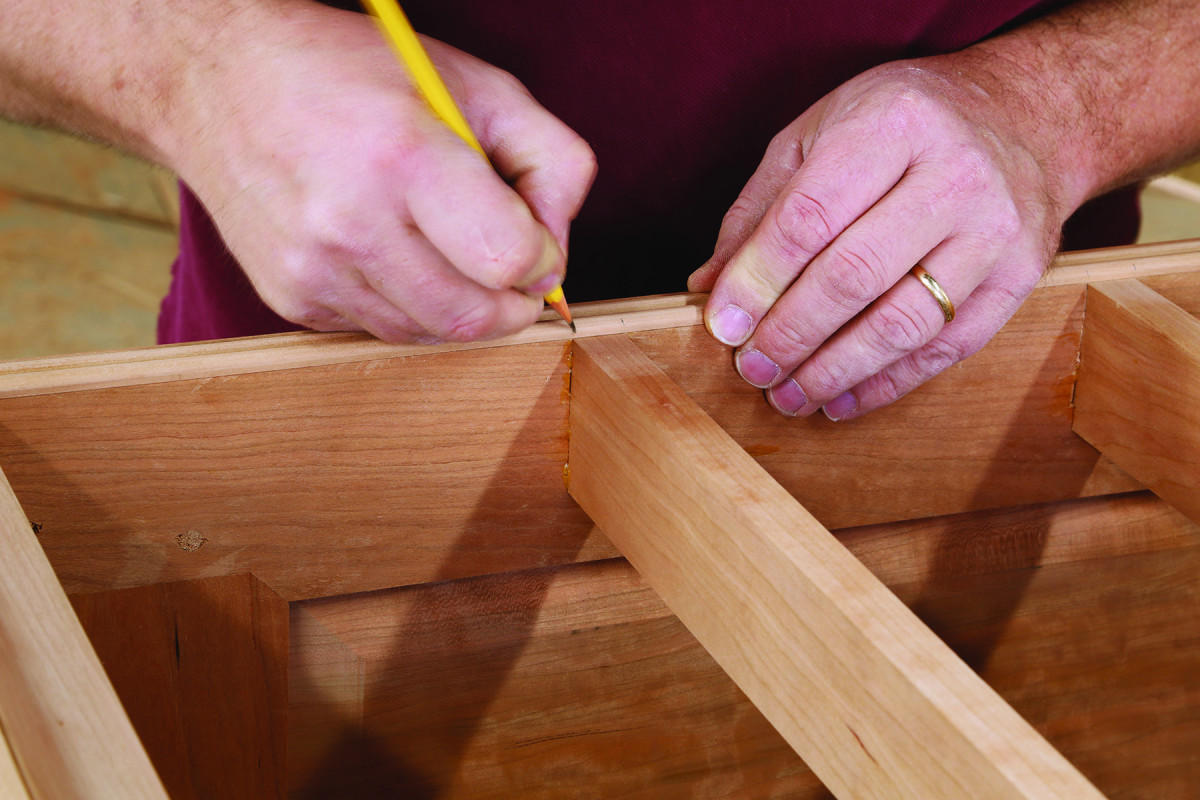
Double-arch mark. Hold the double-arch moulding in place to mark off the position of the drawer blades.
The double-arch mouldings align to the inside of the chest sides and are flush with the drawer blades. The mouldings on the blades are mitered into the stile mouldings. The drawer-divider moulding is mitered into the drawer blade below. Attach these pieces with glue and pins.
Half-lapped and beaded backboards complete the case. But don’t attach them yet; you’ll find the next steps easier without them in place.
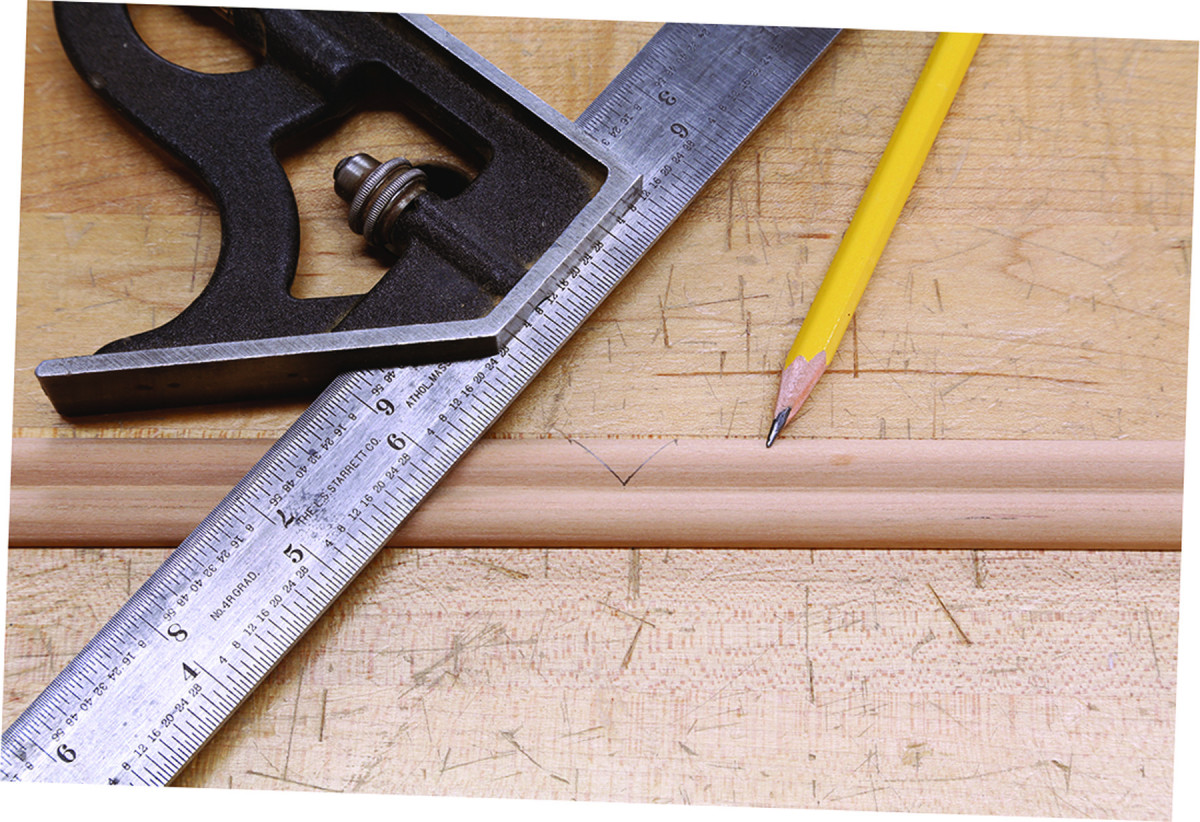
Bevel it right. Once the location marks are in place, draw the miters to ensure a proper cut.
Brush It Off
I’m often asked how I apply my finishes. While I’m not opposed to spraying, most of the time I find myself brushing. My finish of choice is shellac, so brushing is easy and quick.
Whether you color your pieces or go au naturel, you are going to need something to stop the wood from becoming soiled and damaged. That’s what a top coat does – protect the wood. Many believe that brushing finishes is a skill that takes a lifetime to acquire. I believe, with a little practice and a few tips, you can be successful in short order.
To brush shellac you’ll need a decent brush. I prefer a badger hair brush to other types. While they are not the cheapest brushes on the market, they aren’t the most expensive, either (a 2″ brush can be had for around $15). A good brush makes all the difference to me in how the final finish looks.
Regardless of whether you make your own shellac from flakes dissolved in alcohol or pour it out of a can, the key to getting a good finish is using it at the proper viscosity. More layers of thinner material are better than a few thick layers. Shellac’s thickness is measured by how much is dissolved in the solution. A 3-pound cut, for example, is 3 pounds of flakes dissolved in 1 gallon of alcohol; a 2-pound cut consists of 2 pounds of flakes dissolved in 1 gallon of alcohol, and so on.
I usually start by putting on a washcoat (a.k.a. sealcoat) that is around a 1- to 11⁄2-pound cut. The idea is to apply a thin coat of finish to seal the wood so additional coats build on top instead of soak in. The first coat will raise the grain of the wood regardless of how well you sanded prior. If you are worried about rubbing through the color as you sand between coats of shellac, you can raise the grain on the piece with water then lightly sand prior to coloring it. This reduces the amount of grain raising that takes place with the washcoat of shellac.
After the washcoat has dried, lightly sand with #280- to #400- grit “A” weight sandpaper. You can tack the surfaces clean or not. The dust left behind from sanding is primarily shellac that will re-dissolve as the next coat is applied.
Subsequent coats are applied at a thicker viscosity (I tend to use about a 2-pound cut). On this chest I ended up applying an additional five coats of shellac. If your shop is warm and dry, you can easily apply two or three coats per day without any trouble.
As I mentioned, I apply very thin coats. Regardless of the viscosity, I work with a relatively dry brush, dipping the tips of the bristles about 1⁄8” into the liquid then wiping them on the side of the container. The most important part of brushing shellac is to cover as much of the surface as quickly as you can. By keeping the entire surface wet with shellac you can use the tips of the bristles to flow out the finish and reduce brush marks.
When applying shellac to large, flat surfaces, begin brushing a few inches in from the edge and brush outward off the end of the board. Always brush along the length of the grain, not across it. Once you have the two ends of the surface brushed, you can flow everything in between without worry about runs or sags on the ends.
After the final coat is applied, my favorite way to complete the job is to rub out the surface with #0000 steel wool, mineral oil and pumice. Dab some oil onto a steel-wool pad then sprinkle a little pumice on it. Use your finger to knead the pumice into the oil-soaked steel wool, then lightly pass the pad across the finished surface. You’ll need to frequently add oil and pumice to the pad until it becomes saturated. A light, deft hand will leave a silky-smooth finish.
— CB
Hang ’em Up
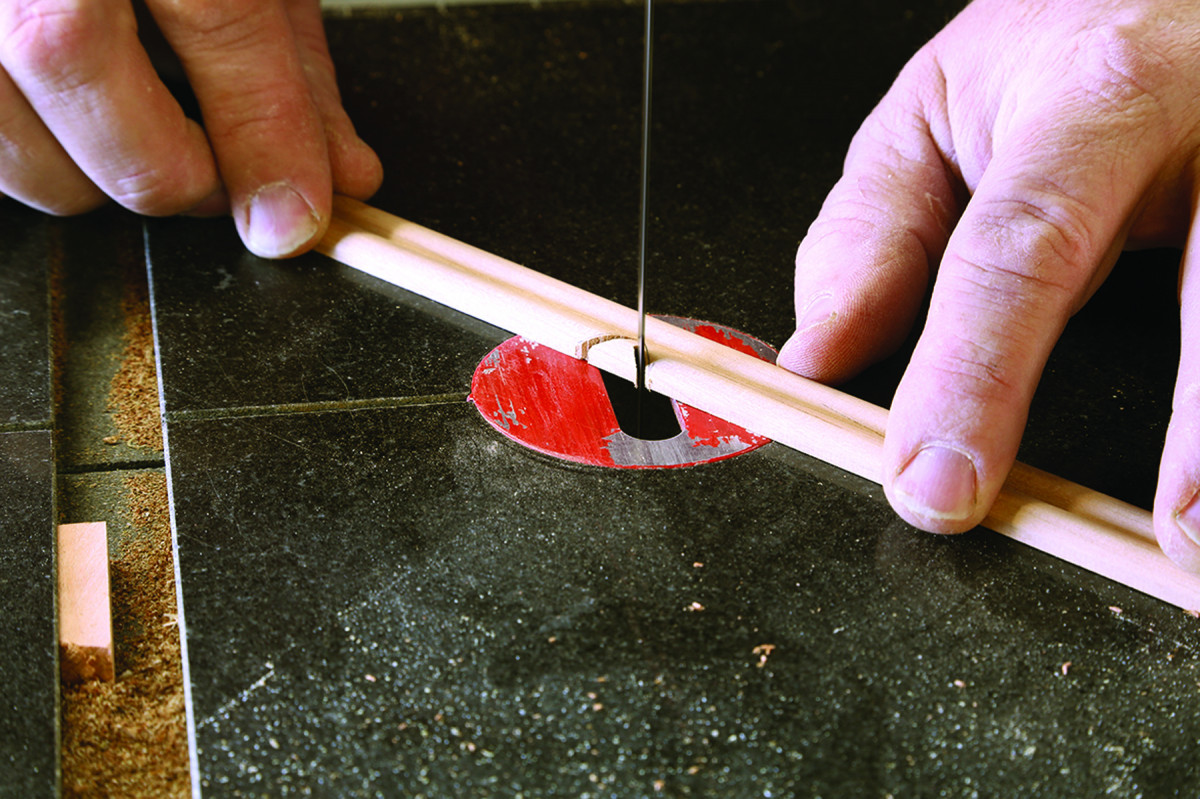
Miter it right. Cut the double-arch moulding miters on the bandsaw. Leave a little extra to be trimmed off before installation.
Unlike drawers where the runners are underneath (you’re likely familiar with this type), side-hung drawers literally hang on a runner that mates with a groove on the drawer side. The runner is nailed to the inside of the case.
When planning joinery for side-hung drawers, the primary consideration is groove placement for the runners. The dovetails need to be laid out so that these grooves fall into a tail. This avoids having to remove end grain of a pin and allows the drawer front to act as a stop.
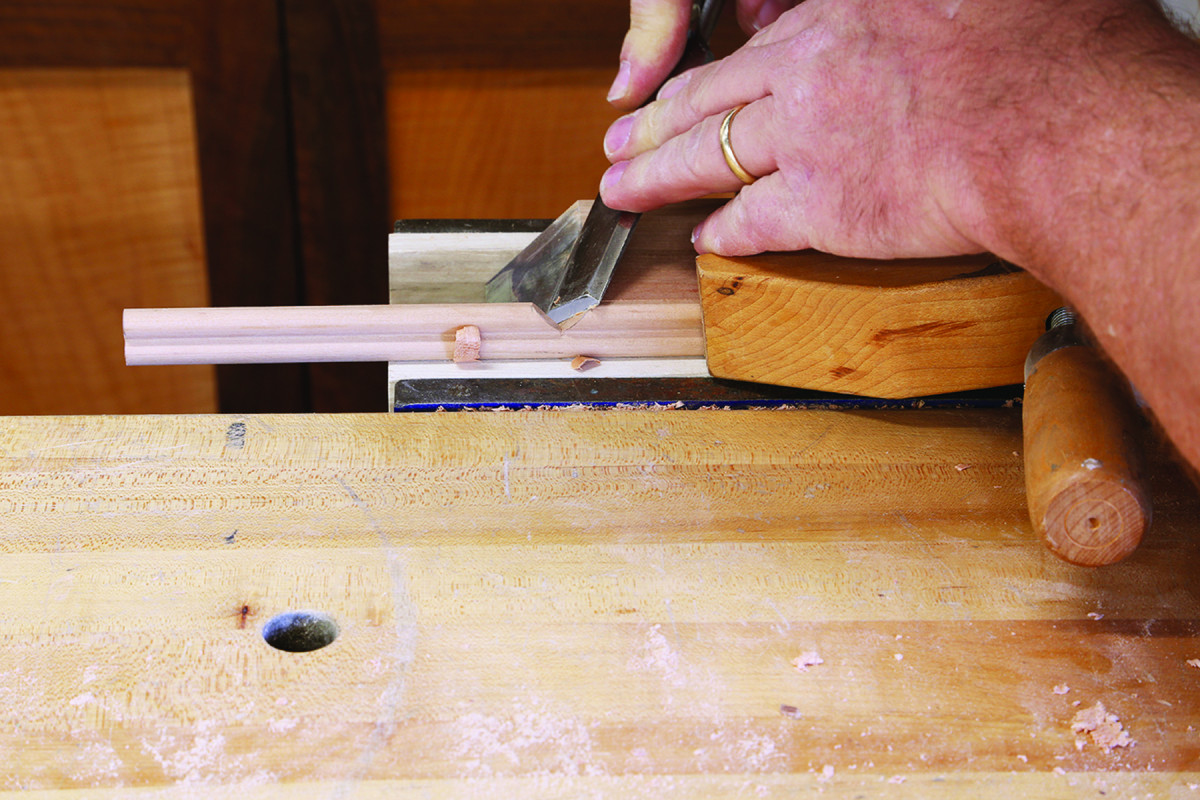
A little help. Make a 45° guide block to accurately trim the miters on the double-arch mouldings.
The grooves are 1⁄4” deep x 3⁄4” wide. I make the runners from 1⁄4“-thick material that is about 23⁄32” wide.
The runners are nailed into the stiles of the case at the proper position. To find that location, I dry-assemble the drawers and place them into the openings. Working from the backside of the carcase, transfer a mark for the top of the groove to the case side. I bump the line up about 1⁄32” or so toward the top of the opening to ensure the drawer bottoms don’t drag on the drawer blades. Use a large square to strike the line across the inside face of the case sides and the center divider.
With the locations marked, tack the runners in place using small brads. This allows you to test the position. Once the drawers are complete, make any adjustments then nail the runners. Rosehead nails were commonly used in period work to secure runners. If you go this route, be sure to drill countersink holes to allow the heads to be set flush.
The drawer construction is straightforward. The fronts are rabbeted and the bottoms are nailed to the bottom of the sides and back, and into the front rabbet.
And Now the Feet
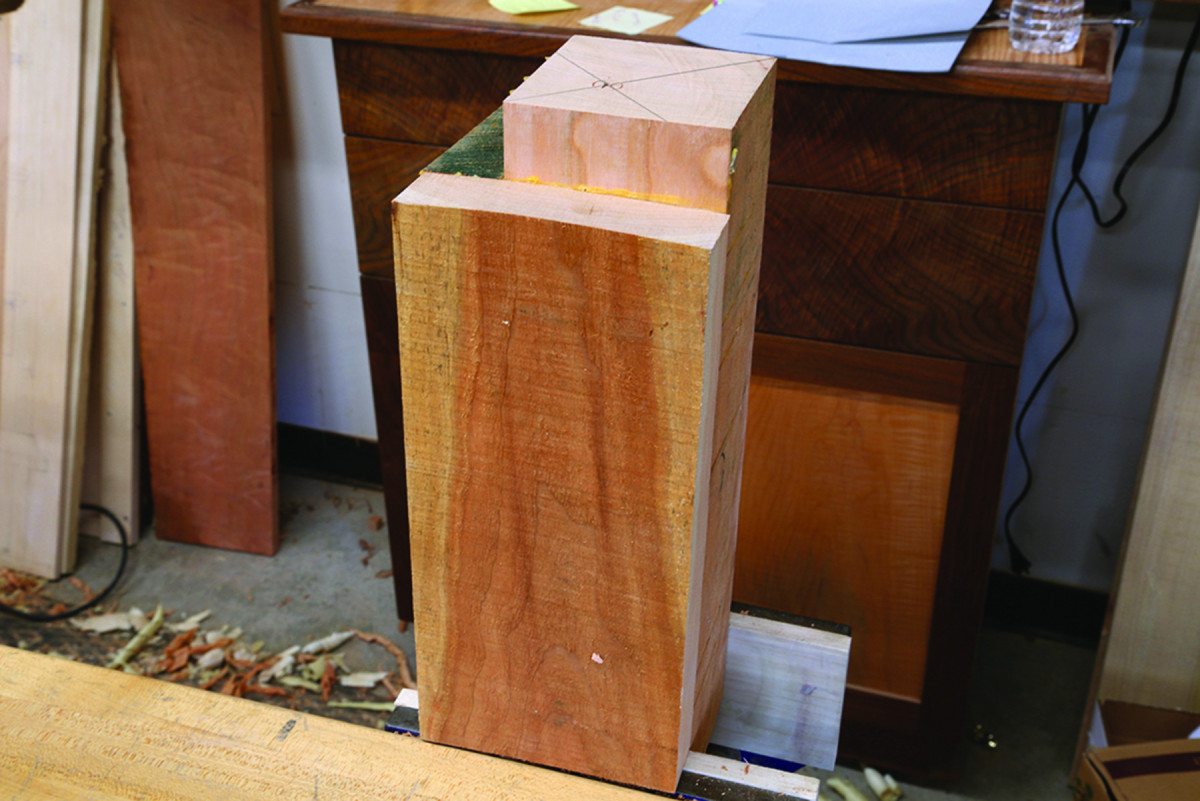
Scabs. Adding extra stock to the core material for the feet allows you to get a larger-diameter foot from readily available material. When complete, orient the glue lines so they are not apparent from the front of the chest.
Because the feet are of a large diameter, you may be-hard pressed to find stock of the appropriate size at your lumberyard. To achieve the proper diameter for these feet, I milled two faces of a 16/4 board flat and square. To these faces, I glued a flattened piece of 6/4 material with matching grain and color. This allows the foot to be turned the proper diameter while hiding the glue joints as much as possible. Once the foot is turned, rotate the two patches to the inside and back of the foot. No one will notice your laminated feet.
The bun feet are attached with 7⁄8” oak dowels that extend through the foot and are glued into matching holes in the case bottom.
Wrap it Up
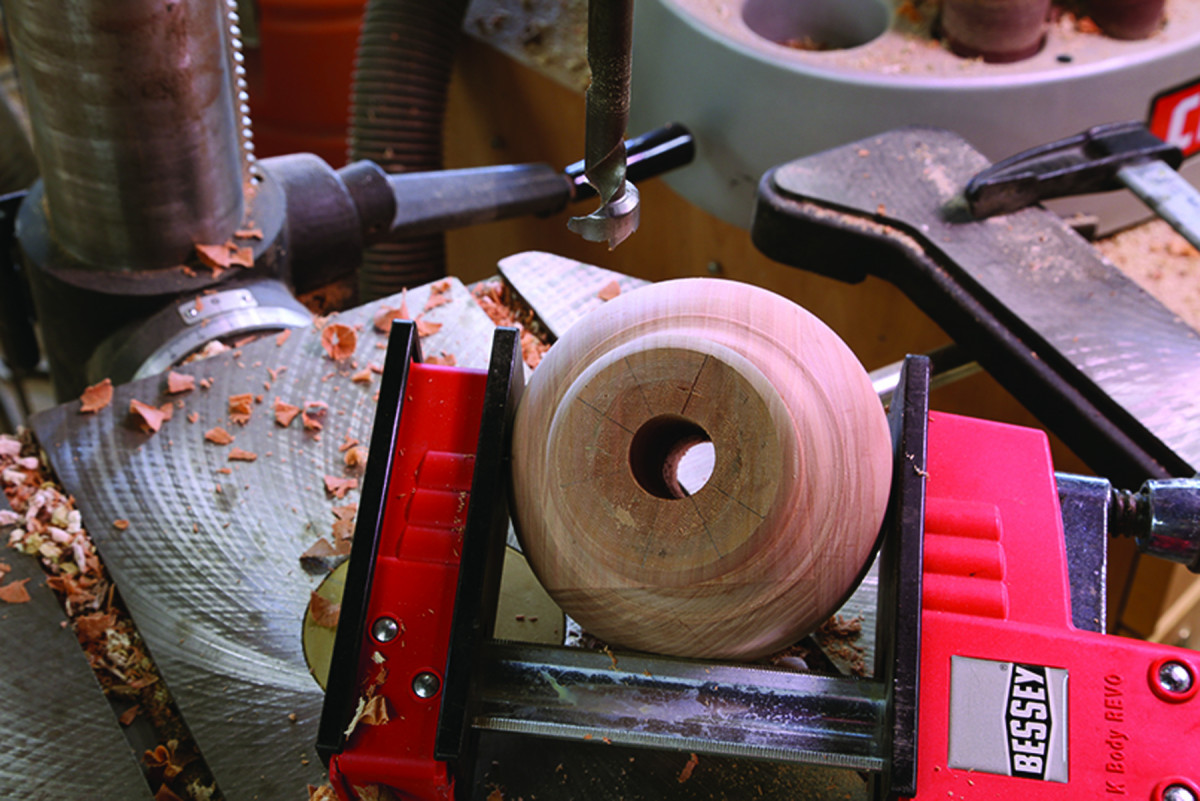
Holey feet. Clamp the feet to get a grip on them while drilling. The peg holes go all the way through.
Before installing drawer bottoms and backboards, I color and finish the chest. This does two things: It helps to avoid unsightly drips on the secondary woods, and it allows you to install the brasses without having the drawer bottom interfere. This is particularly important if you are using brasses attached with wires (or “snipes,” as they are often called).
After your finish dries, all that remains is to install the hardware, and decide in which room you’re going to display the fruits of your labor. PWM
Chuck is senior editor at the magazine.
Here are some supplies and tools we find essential in our everyday work around the shop. We may receive a commission from sales referred by our links; however, we have carefully selected these products for their usefulness and quality.