We may receive a commission when you use our affiliate links. However, this does not impact our recommendations.
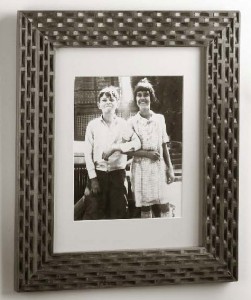
Tight corners and clean joints are the hallmarks of a quality frame. Deceptively simple in concept, yet demanding in execution, it is only simple to assemble a frame if all the parts are near perfection.
Sooner or later, someone will ask you to make a picture frame. Here is how to get it right the first time.
by Robert W. Lang
Pages 21-23
From the Summer 2009 issue of Woodworking Magazine, issue 14
Buy this issue now
Picture frames are one of those woodworking projects that we all assume we know how to make. After all, a frame is only four pieces of wood mitered together – isn’t it? And there’s a piece of glass of course, along with the mat and something behind it. Framing is actually a specialty within woodworking, and the people who do it all the time have it pretty well figured out. This article will review the basics so you don’t need to reinvent the wheel.
The drawing below at right shows the parts of a standard frame. The glass fits within a rabbet on the inside edges of the wood frame members. Behind the glass are, in order, the mat, the image and a piece of foam board. These should all fit easily in the opening without being forced; glazier points driven into the wood from behind the foam board hold everything together.
If you want to take do-it-yourself to an extreme, you can cut your own glass and mat. But to get good results, you will need some specialized tools. So unless you plan on making lots of frames, you are better off simply buying precut mat and glass. You can purchase these either at a frame shop (pricey) or a large crafts store (pretty reasonable). I made two frames for this article, and I started with 8″ x 10″ printed photos. The glass, mat, foam board and hardware cost about $10 per frame.
There is a good reason to stay with standard image sizes if you can. Most sources, such as Michael’s or Hobby Lobby, stock glass and mats precut to fit 5″ x 7″, 8″ x 10″ and 11″ x 14″ images. I saved time and money by pulling precut glass and mat board from a bin, instead of having them custom cut at an odd size.
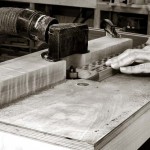
The rabbet in the back of the frame material doesn’t need to be wide, but it must be deep enough to fit the glass, mat and foam board.
The foam board that goes behind everything is sold in pieces, and the common size found in stores is 20″ x 30″. It isn’t expensive, and you can easily cut it with a table saw. Without a table saw, it can be cut with a straightedge and a utility knife by making repeated passes alongside the straightedge.
Most woodworkers assume that the rabbet in the frame needs to be both wide and deep. Picture framers realize that you only need enough width to keep things from falling out; 1⁄4″ is plenty. In the other direction, you want to keep the image close to the outer face of the frame. I cut my rabbets in the frame stock 1⁄2″ deep, leaving about 1⁄4″ of material at the show face of the frame.
Be Consistent
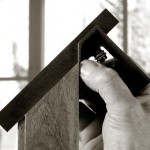
An accurate cut is essential. Check with a good square, holding the angled piece up to a source of light.
If the profile of your frame material isn’t consistent, it will create problems at some point in cutting and assembling the frame. Square stock, such as the wave-form mouldings I used, should be as straight, flat and square as possible.
If you’re making a frame with a shaped profile, use featherboards on the router table when you mill the profiles. Variations may not be noticeable in a stick of frame material, but they will be screaming for attention when two parts meet at a mitered corner.
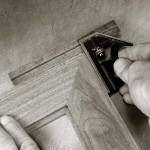
Check an assembled corner to be certain it is square. Place the material on a flat surface and use a reliable square.
The miter cuts also need to be as close to perfect as you can make them. A fraction of a degree may not seem worthy of concern in one cut, but there are eight edges in a mitered frame to put against each other. “Close enough” times eight becomes an ugly gap when you try to close the last corner.
Make some test cuts and check them with a reliable square. When you think your saw is cutting a good 45˚ angle, place two pieces together on a flat surface, such as the table of your table saw. Check the assembly with a good square. You can catch a variation you may have missed because the error will be doubled at the corner.
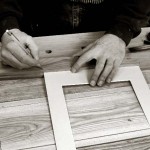
Calculating the length you need can be confusing. Mark your stock directly from what will fit within the frame.
If your saw setting is 1/64″ off the correct angle, you might miss it. A 1/32″ gap in the corner will be easier to see. If you don’t fix that tiny error before you cut all of the pieces, you will have 1/8″ of space to deal with at the last corner of the frame.
The length of the individual pieces is as important as the angle. Parts on opposite sides need to be exactly the same length to avoid gaps. You can try to force them together at the end, but the chances of success are slim. Closing a gap on one corner opens another one at a different corner. Instead of measuring, place the mat in the rabbet, and mark the stock directly. Make the 45˚ mark from this point, and leave 1⁄16″ or so of extra room. Set up a stop on the miter saw so you can repeat the exact length.
It’s fashionable among handplane aficionados to make a shooting board to fit the miters. With a decent blade in the miter saw, you can set a stop for the length. If you make sloppy cuts and try to shoot the miters, you will need to reference one piece off another to make them equal lengths, then adjust the rabbet with a shoulder plane. Glass-smooth surfaces on the miters may be impressive, but they won’t show in the finished frame. Gaps from varying lengths will.
You Need to Have Some Pull
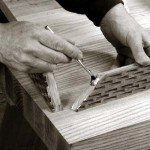
Size the joints by brushing on a coat of glue and walking away for five or 10 minutes. Apply a second, thin coat just before you clamp.
Unless the frame is extraordinarily large, glued butt-miter joints will have sufficient strength. Getting a good glue joint requires some extra care as the nature of the wood cut at an angle introduces a problem. The gluing surface is mostly end grain, and glue tends to wick into the wood and away from the joint. Coat the surfaces with glue and leave them alone for five or 10 minutes.
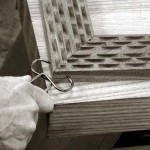
The right clamps will make a world of difference. These spring clamps pull the pieces toward one another, so the joints are tight and the pieces don’t slide around.
This sizing coat will allow a second coat of glue, applied just before jointing, to do its job. The angled cuts also tend to slip and slide as clamp pressure is applied. It isn’t the same situation as gluing a square end to a straight surface. Special clamps, such as the spring clamps shown in the photo below, pull the faces of the joint toward one another, and are more effective than the clamps you use every day.
Some framing clamps hold the pieces at a right angle, but don’t exert any pressure across the joint. These are fine if a fastener, such as a nail or brad, is used to pull the joint tight. Without a fastener, they are good only for positioning – they can’t press the parts against each other as a clamp should. Don’t be afraid or ashamed if you decide to use nails. Drive them in from the top and bottom rather than the sides of the frame and they won’t be obviously visible.
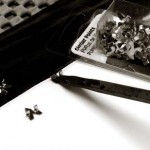
There is a special driver made for glazier points, but they can also be pressed into the wood with the tip of a common screwdriver.
The glue joints should be given ample time to dry. Wood glues dry in stages; you may be able to remove the clamps within an hour, but the bond won’t achieve full strength for a much longer period. If you use good old yellow glue, let it sit overnight before doing anything to the frame that might stress the joints.
When the glue has dried, you can sand the frame and finish it. On flat stock, use a plane or a flat sanding block to level the surfaces at the joints. On a moulded edge, you can roll a piece of sandpaper into a tube, or wrap it over a sponge or piece of foam. Work carefully to bring the higher surface down to the level of the lower surface.
I like to keep the glass, mat board and image out of the shop until the frame is completely finished and I’m ready to assemble it. Dust or a greasy fingerprint on the image or the inside of the glass will mean taking the assembly apart.
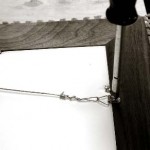
Braided wire is twisted around the loop in the hanger, and the hanger is held in place with a screw.
Put a pad on your bench and lay the frame facedown on the pad. Next, drop in the glass, mat board, image and foam board. Glazier points are the preferred way to hold everything in the frame. Place them flat on top of the foam board and push them into the wood. There is a special driver for these points, but if you don’t want to buy a tool for one task, you can push in the points with the end of a common screwdriver.
A hanging loop is screwed to each of the vertical frame parts, and a length of braided wire goes between the loops. Twist the ends of the wire around the loops to secure it. If the frame is large or heavy, add a third loop in the middle of the bottom frame member and run the wire in a triangle around all three loops. This will take the weight of the frame off the joints at the bottom and transfer it to the wire. WM
To download a PDF of this article, click here: MakingFrames
Here are some supplies and tools we find essential in our everyday work around the shop. We may receive a commission from sales referred by our links; however, we have carefully selected these products for their usefulness and quality.