We may receive a commission when you use our affiliate links. However, this does not impact our recommendations.
A must-have device for sharpening saws.
By Robert W. Lang
Pages: 52-53
From the June 2010 issue #183
Buy this issue now
One of the cardinal rules of woodworking is that the purchase of one tool begets the need for several others. Sawing by hand is both easier and more accurate than many people think, provided the saw is sharpened properly. Old saws can be an incredible bargain, and if you’re a frugal sort you likely won’t want to spend a lot on sharpening equipment.
There are three things you need: a triangular file to make the teeth sharp, a saw set to bend the teeth away from the body of the blade and a vise to hold the blade while you work. A file costs about $5 and a new saw set less than $20. But a new saw vise will set you back more than $120 – unless you make your own.

Three clamps. Two F-style clamps hold the vise to the bench, the third tightens the jaws. Keep the handle of the third clamp away from you.
This was the problem we faced a couple years ago when we held a hands-on saw sharpening class at the 2008 Woodworking in America conference. We needed 50 saw vises and we didn’t have a lot of time or money. So we looked at some vintage vises, consulted a saw guru and came up with this design.
Any hardwood will do; we used odds and ends we had in our shop of ash, poplar, cherry and oak. Most of the joinery is simple butt joints reinforced with yellow glue and #8 screws. The jaws sit in shallow rabbets in the two uprights, and should be held in place with screws only. You will likely want to modify the jaws at some point to accommodate a different saw, or tweak the way the jaws hold the saw blade.
A saw vise does two things: It puts the blade at a convenient height and the jaws keep the blade from vibrating as you file. Before you follow our plan, however, give some thought to the type and size of saws you plan on working with, and don’t be afraid to change the size or shape of the jaws.
Lacking 50 bench vises at our conference location, we made the base so we could secure the saw vise to a workbench with a couple Fstyle clamps. The addition of a square block secured below the base will allow you to hold the saw vise easily in your bench vise.
The Great Debate
When the vise is assembled, there should be a slight gap between the two jaws, and a hollow should be planed in the middle of the jaw faces. When the uprights are clamped together, this hollow forces the ends of the jaws to close first. As the clamp is tightened, pressure is applied along the length of the jaws to hold the blade firmly.
There is an unsettled debate about whether or not the faces of the jaws should be parallel, or just meet at the top. One camp asserts that the faces of the jaws should be angled slightly in at the top to ensure that the gripping force is strongest directly below the saw teeth, thereby reducing vibration.
The opposition believes that parallel jaws increase the mass in the wood-to-steel contact area, thereby reducing vibration. Changing from one to the other takes only a few minutes of planing, so try both ways and decide which works best for you.
Ideally, the length of the jaws ought to match the length of the saw blade, so the entire length of the blade can be filed without repositioning. For backsaws, the height of the jaws should be reduced to provide room to grip the blade above the back.
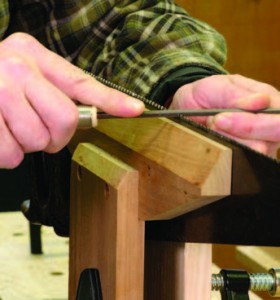
Tight Fit. The jaws of the vise hold the sawblade and keep it from vibrating. If you hear an awful noise, the jaws need some work.
First Things First
Make the two uprights and the two jaws first. Next, attach one of the uprights to the base with glue and screws, then insert the two corner braces. While the glue is drying, bevel two long corners of the 11⁄2″-square fulcrum. The angle and size of the bevels aren’t critical; you simply want to reduce the width of the attachment point on the movable upright. This makes it easier for the upright to bend slightly when you tighten the clamp to secure the jaws.
Attach the fulcrum to the uprights with a dab of glue and a couple screws from each side. Offset the screw locations in the uprights so they don’t interfere with one another. Be careful to keep the uprights aligned when you attach the second one to the fulcrum.
Spend some time preparing the jaws, and check them against one another as you work to ensure that they match. There should be a slight, bowed gap along the length of the jaws when viewed from above, and both ends should come tightly together when viewed from the end.
Fix the jaws to the uprights with screws only. The odds of getting the exact fit you want on the first try are slim, and this reversible connection lets you easily remove them for adjustment, or to swap jaws for a different type or size of saw. The wooden jaws may also warp or twist over time and need to be removed for an adjustment.
Clamp the assembled saw vise to your bench and put your saw in place. Set the blade so the teeth are parallel to the top of the jaws, and as close as possible. Place an F-style clamp on the uprights above the fulcrum and below the jaws, then tighten it. If the jaws secure the blade, you’re ready to start sharpening.
If the grip isn’t strong enough, be sure the clamp is centered in the width of the upright and try a different vertical position for the clamp. If that doesn’t work, check the way the jaws fit the blade and adjust the faces of the jaws with some judicious planing.
Practice Makes Perfect
The good thing about learning to sharpen saws is that you can pick up a decent old saw at a yard sale or flea market for a few dollars and use that to practice on. Filing the teeth of a saw is more about consistency than skill, and it doesn’t take long to get the hang of it. Put a good light on the work (and get a pair of magnifying goggles if you’re older than 40) and have at it.
Begin by matching the existing angles of the saw you have. Set the file in the gullet between two teeth and take a few strokes. The goal is to make the metal shiny all the way across the front of a tooth that points away from you and the back of the tooth ahead of it. The teeth will tell you when you have the angles right.
If it’s a crosscut saw, angle the file about 15˚ back toward the handle when viewed from above. Start at the end of the blade closest to the handle, as these are the least-used teeth. File every other tooth, then turn the saw around and file the opposite set of teeth.
If it’s a rip saw, file straight across. When you are adept at matching existing angles, you’ll have the skills to experiment with differing rake angles (the slope of the front of the tooth from vertical) and fleam angles (the angle of the face of the tooth from the body of the blade).
It’s best if you can find someone to show you how, but the next-best thing is to watch a good video. In the box below we’ve listed one of the best we have found, as well as sources for instruction and supplies. PWM
Download the full article PDF:
Shop-made Saw Vise
Video: Watch Thomas Lie-Nielsen’s video on “Techniques and Sharpening.”
Web site: Read detailed sharpening instructionsin Pete Taran’s “Saw Filing – A Beginner’s Primer” on VintageSaws.com.
Buy: Shop for saw sharpening supplies, including files, sets and a modern saw vise from Tools for Working Wood.
In our store: Purchase “The Perfect Edge,” Ron Hock’s new book on sharpening.
From the June 2010 issue #183
Buy this issue now
Here are some supplies and tools we find essential in our everyday work around the shop. We may receive a commission from sales referred by our links; however, we have carefully selected these products for their usefulness and quality.