We may receive a commission when you use our affiliate links. However, this does not impact our recommendations.
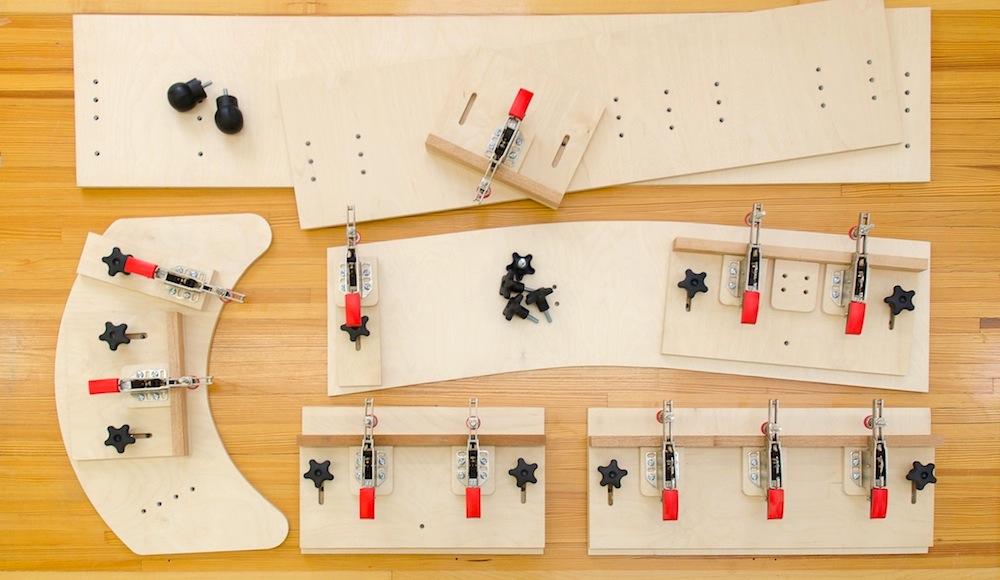
Modular shaping jigs. With this setup, I can mix and match components for different situations. I can shape small parts, furniture-sized parts of any shape, curved parts big and small, and parts up to 96″ long. The way they’re designed, the jigs adjust to the shape of the particular part being cut. It’s a great setup, and I love using it, but sometimes a CNC can do the job better and faster.
If you build furniture out of wood, you’ll find that once your design becomes more than a collection of straight lines and begins to include curves, shapes and other details – you enter the world of pattern shaping.
What is pattern shaping? It is a woodworking process for accurate duplication. Instead of creating repeated parts from scratch, an existing pattern of the part is used to produce an exact copy. Shaping a part involves machining it with a straight bit (in a shaper or router) that has a bearing that is the exact diameter of the cutter (the bearing can be on either the top or bottom, or both). To begin, place a rough-cut part on the table, attach it to your pattern and run the pattern along the bearing. The excess wood is accurately removed and the remaining part is shaped into an exact copy of the pattern. The process works great. However, to shape safely and easily, there are various techniques to learn. It is an important skill that all woodworkers should learn.
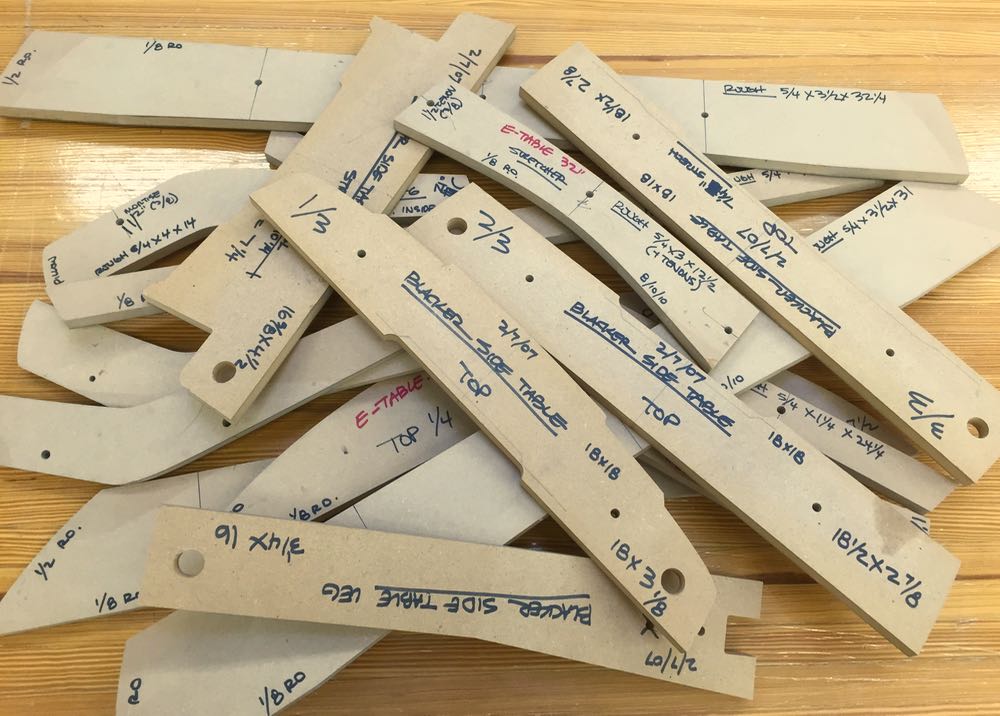
Patterns, patterns and more patterns. I’ve done a lot of shaping over the years and as a result, I’ve got hundreds of patterns in my shop.
As a furniture maker, with hundreds of pieces completed, I’ve shaped thousands of parts over the years. Shaping is justifiably an intimidating process. But, once you understand safe procedures and how to hold the pattern and material securely, shaping is a very satisfying process. In fact, I actually like shaping. I love the results it gives. However, as a professional, sometimes I have to spend days at a time doing it — which is time-consuming, tiring and a lot less fun at times. Looking for a better way to achieve the repeatability and accuracy of shaping is one of the primary reasons that I acquired a CNC. As I’ve pointed out in the past, these machines do all kinds of tasks well, but they excel at cutting parts.
CNCs or Shaping
To demonstrate the differences between the two woodworking methods, I’ve put together a video showing both techniques.
Is there a clear winner here? No, because both techniques will give you good results. However, a CNC does this particular job exceptionally well. So well in fact, that it’s rare that I use my shapers anymore. That being said, they are great for specific tasks such as machining thick, compound curved parts where the amount of time to build a new dedicated fixture for the CNC might be time-consuming. But, for almost everything else, it’s a real pleasure to quickly set up a cut, let the CNC do its thing and just walk away. Then I can go off and work on other things in the shop.
Here are some supplies and tools we find essential in our everyday work around the shop. We may receive a commission from sales referred by our links; however, we have carefully selected these products for their usefulness and quality.
In the video, when describing using a template at a router table you talk about the need to avoid routing uphill to avoid tear-out. But when the CNC runs, it appears to be going the same direction all the way around and routing uphill in some of the curves. How do CNCs get away with that?