We may receive a commission when you use our affiliate links. However, this does not impact our recommendations.
Store all the tools you need in easy reach
If I were to make three lists – the tools I want, the tools I own and the tools I need – the last would be the shortest. When I decided to build a wall cabinet for my hand tools, I put my most-used tools close at hand and at eye level, along with plenty of drawer storage for tools I don’t need so often.
I spent time sorting through my tools and experimenting. I cut some pieces of 1⁄4“-thick foam core (plywood or cardboard would work as well) to pin down the size and shape of the cabinet and the layout of the tools. My goal was to store as much as possible in a compact and organized space.
Tailor the Plan
If you’re thinking of building a tool chest similar to this, I suggest that you alter my design and adapt it to your tools, your shop and the way you work. The results will be more useful to you, and you’ll be happier.
I let function lead the way, with a single door for hanging storage. The stiles were turned 90° to provide depth. I wanted to hang a framing square in a corner of the door, and a bit of experimentation led to an overall height of 30″ and a width of 22 1⁄4“. A survey of the tools destined to hang in the door led to an overall depth of the door at 2 1⁄2” and I settled on a case depth of 11 3⁄4“.
My initial thought was drawers at the bottom of the case with hanging and shelf storage above. I didn’t want the drawers too tall and I settled on varying heights from 1 1⁄2” to 2 3⁄8” with one taller narrow drawer. A mock-up of the plane ramp left room at the top and rather than redo my layout, I sketched in three 2″-high drawers at the top.
I thought that looked pretty good, found a few people to agree with me and carried the horizontal division of the drawers down to the lower drawers. I wanted some wider drawers, and made those two-thirds of the space. Alternating the arrangement from side to side kept things interesting and the regular division meant fewer sizes to deal with.
From the Outside In
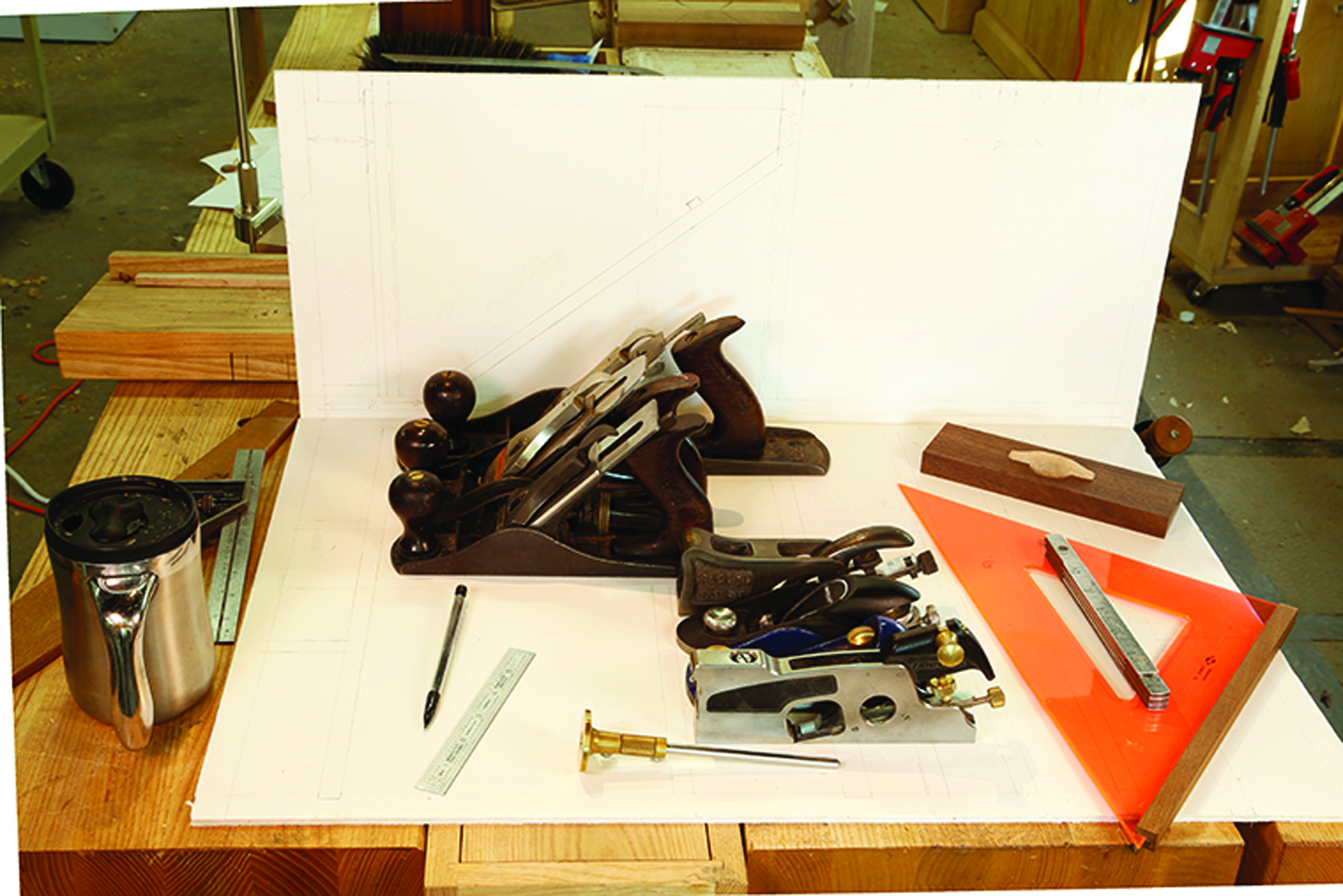
Function first. Plan the cabinet around groups of tools; put the most-often used ones where they will be near at hand.
The outer case is solid wood, connected with through-dovetails, as is the door frame. I laid out the dovetails to leave a half-tail where the case and door meet and half-pins at the wall and the outer edges of the door.
After sawing the pins by hand I lowered the end of the board in my vise to place it even with the top of a piece of scrap on top of a box. Then I used a trim router with a straight bit to remove the waste between the pins, stopping short of the saw cuts. The small amount of material that remained was cleaned out with a chisel.

Rapid removal. A trim router with a straight bit makes quick work of clearing waste between the pins, and it leaves a flat baseline.
With the pins complete, I marked and cut the tails then made the first of many trial assemblies. With a complex case like this, I lay out the joinery from existing parts when I can. With the outer case together, I marked the locations of the dados that capture the shelves and web frames.
I used a router with a straight bit and a right-angle guide to rout the dados. Because the dados are different widths, I set up a few different routers so I wouldn’t need to change or repeat my tool setups. There are times when you really do need four routers.
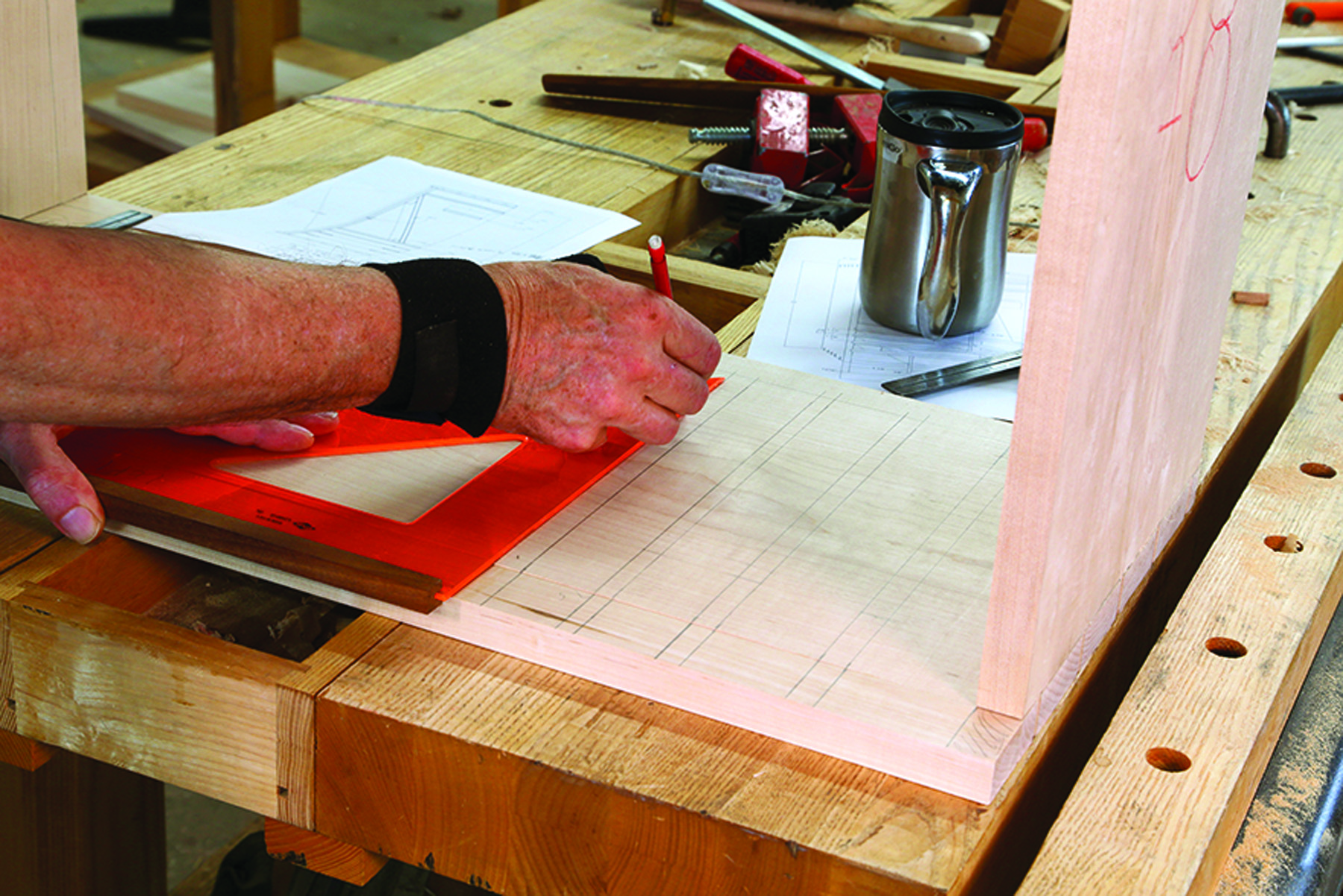
Plan meets reality. With the case dry-fit, dados for interior partitions are laid out from a story stick.
There is a solid shelf below the top drawers and another solid shelf above the lower drawers. The two shelves are connected with a solid vertical divider that sits back 1″ from the front edge. The dados for the vertical divider stop back from the front by 1 1⁄2“, and the front of the divider is notched at each end to cover the ends of the dados. After fitting the two shelves and the vertical divider, I reassembled the case, then cut and fit the front rails of the web frames.
Next I laid out and cut the dados for all the vertical dividers between the drawers. These dividers have a short piece at the front glued cross-grain to a longer piece that runs front to back. These pieces are trapped in dados and have nowhere to go, even if the cross-grain joint should someday fail.
The last set of dados are for the small shelf that sits above the plane ramp. These stop about 1⁄2” from the front edge of the shelf, which is notched beyond the ends of the dados.
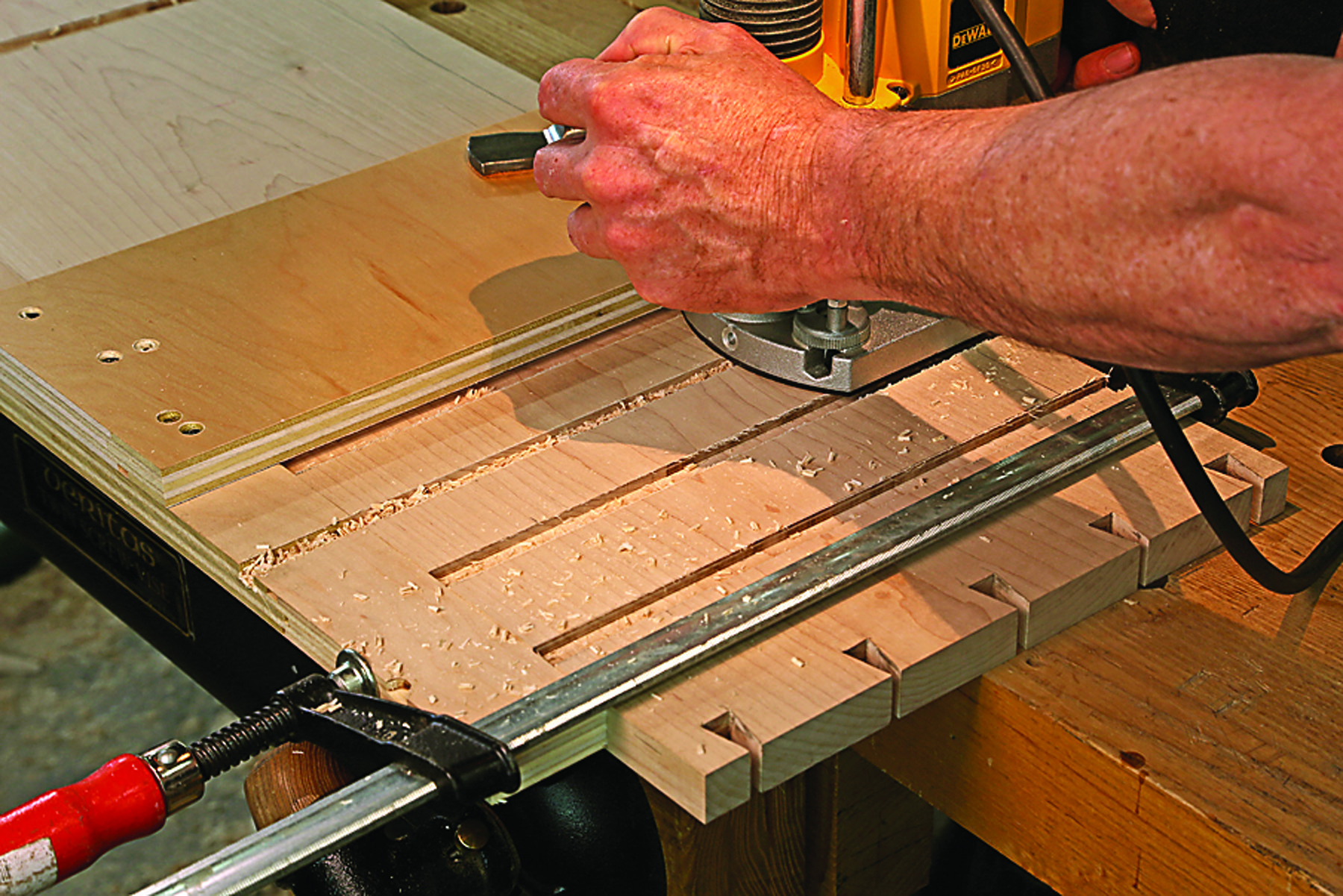
Right angle. This T-square jig indexes off the router cut in the arm. Line up that cut to your layout lines, then rout the workpiece.
With all the visible pieces in place, I made the secondary parts to complete the web frames. I made the back rails the same length as the fronts, and ran a groove down all the inside edges. I then cut stub tenons on the ends of the pieces that connect the rails front to back.

Fronts first. Dados for the vertical dividers are also laid out with the carcase together, before the web frames that support the drawers are assembled.
The web frames are glued together and dry-fit to the case to make sure all parts fit tight and square. This dress rehearsal also showed where I needed to clamp during the final assembly. Then the case came back apart to clean up all the visible surfaces.
The back of the case is a piece of 1⁄2” – thick plywood that sits in 1″-deep rabbets in the sides. I skipped the rabbets in the top and bottom to avoid cutting into the dovetails at the corners. There is plenty of material in the area to screw the back to, and the top and bottom of the back are hidden behind drawers.
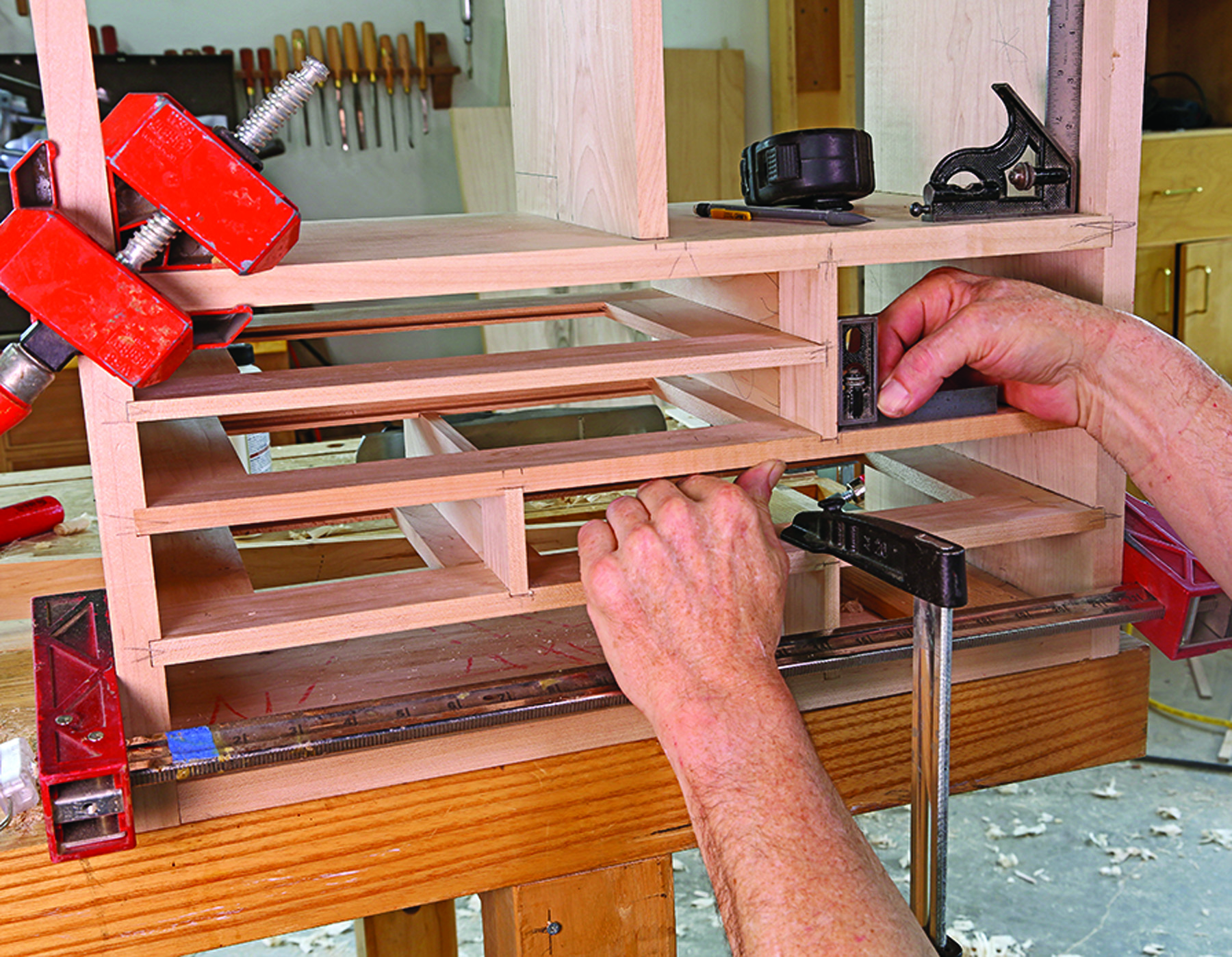
Take care. Good openings will ensure good-fitting drawers. Check and adjust each opening with a dry assembly.
I clamped a straightedge to my layout line at the back of the sides and cut the rabbets with a large straight bit. A bearing above the cutter rode along the straightedge. I stopped short at the beginning and end of the cut and cleaned up the corners with a chisel.
Cabinetmaker’s Tool Chest Cut List
No.ItemDimensions (inches)Material
t w l
Carcase
❏ 2 Case sides 13⁄16 11 3⁄4 30 Maple
❏ 2 Case top/bottom 13⁄16 11 3⁄4 22 1⁄4 Maple
❏ 1 Shelf above drawers 5⁄8 10 3⁄4 21 Maple
❏ 1 Vertical divider 5⁄8 9 3⁄4 16 3⁄4 Maple
❏ 1 Shelf below drawers 1⁄2 10 3⁄4 21 Maple
❏ 1 Block plane shelf 1⁄2 5 10 3⁄8 Maple
❏ 2 Low frame fronts 1⁄2 2 21 Maple
❏ 1 Mid frame front 3⁄8 2 13 7⁄8 Maple
❏ 3 Vert drawer dividers 3⁄8 21⁄4 10 3⁄4 Maple
❏ 1 Vert drawer divider 3⁄8 25⁄8 10 3⁄4 Maple
❏ 1 Vert drawer divider 3⁄8 3 3⁄4 10 3⁄4 Maple
❏ 1 Plane ramp 1⁄2 10 17 7⁄16 Baltic birch ply
❏ 1 Case back 1⁄2 21 5⁄8 28 3⁄8 Baltic birch ply
❏ 2 Low frame backs 1⁄2 2 21 Poplar
❏ 7 Frame rails 1⁄2 2 7 3⁄4 Poplar
❏ 1 Mid frame back 3⁄8 2 13 15⁄16 Poplar
❏ 2 Mid frame rails 1⁄2 2 7 3⁄4 Poplar
❏ 2 French cleats 1⁄2 4 1⁄2 21 5⁄8 Baltic birch ply
Door
❏ 2 Outer stiles 13⁄16 2 1⁄2 30 Maple
❏ 2 Rails 13⁄16 2 1⁄2 22 1⁄4 Maple
❏ 1 Middle stile 1 3⁄8 1 3⁄8 30 Maple
❏ 2 Panels 3⁄4 10 3⁄16 28 7⁄8 Maple
Drawer Fronts
❏ 4 Fronts 13⁄16 2 6 5⁄8 Walnut
❏ 1 Front 13⁄16 2 13 5⁄8 Walnut
❏ 1 Front 13⁄16 1 1⁄2 13 5⁄8 Walnut
❏ 1 Front 13⁄16 1 5⁄8 13 5⁄8 Walnut
❏ 1 Front 13⁄16 2 3⁄8 6 5⁄8 Walnut
❏ 1 Front 13⁄16 2 3⁄8 13 5⁄8 Walnut
❏ 1 Front 13⁄16 3 1⁄2 6 5⁄8 Walnut
❏ 14 Pulls 3⁄8 11⁄16 1 3⁄4 Maple
Drawer sides & backs 3⁄8” thick, drawer bottoms 1⁄4“-thick plywood
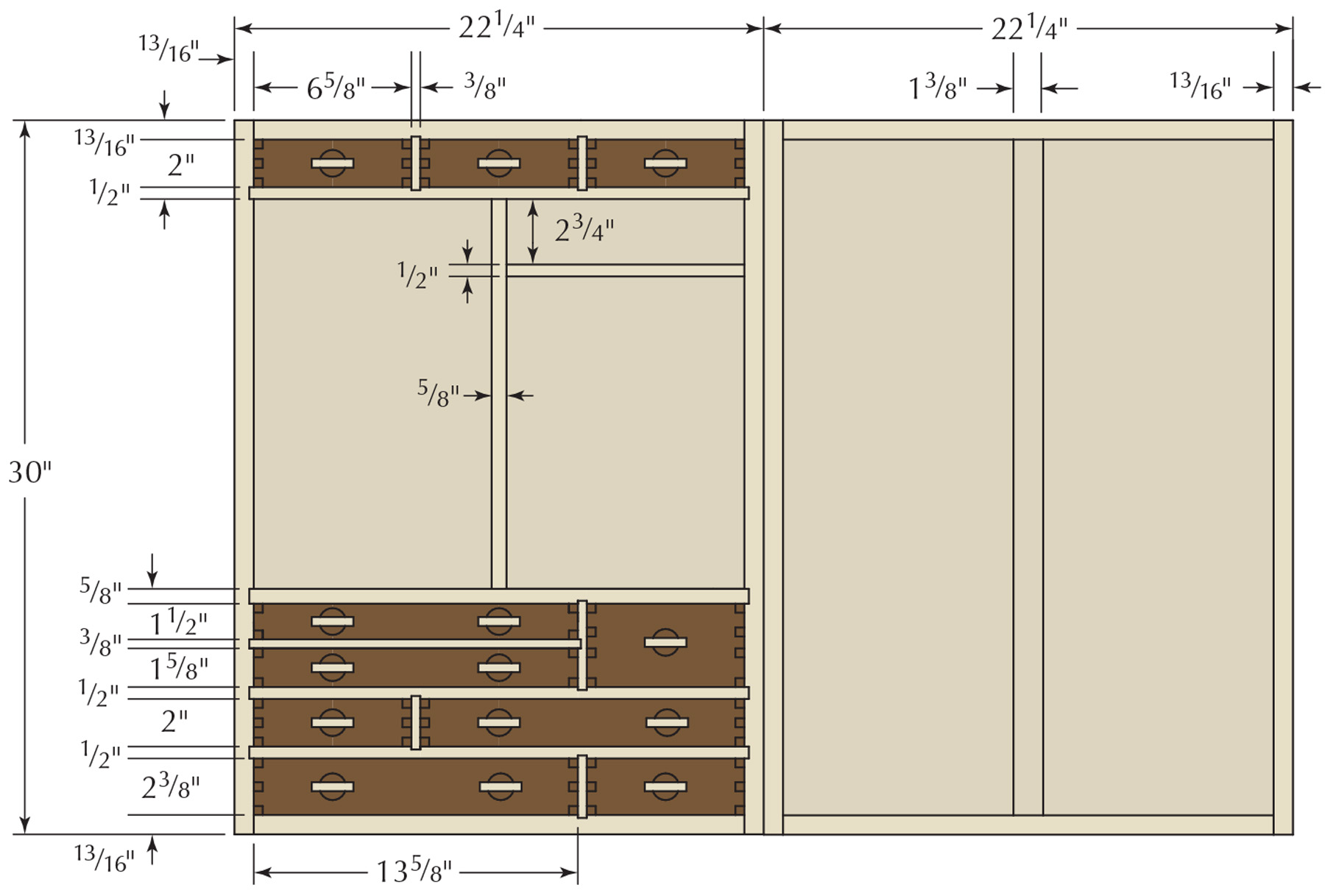
Front

Section


Not Your Average Door
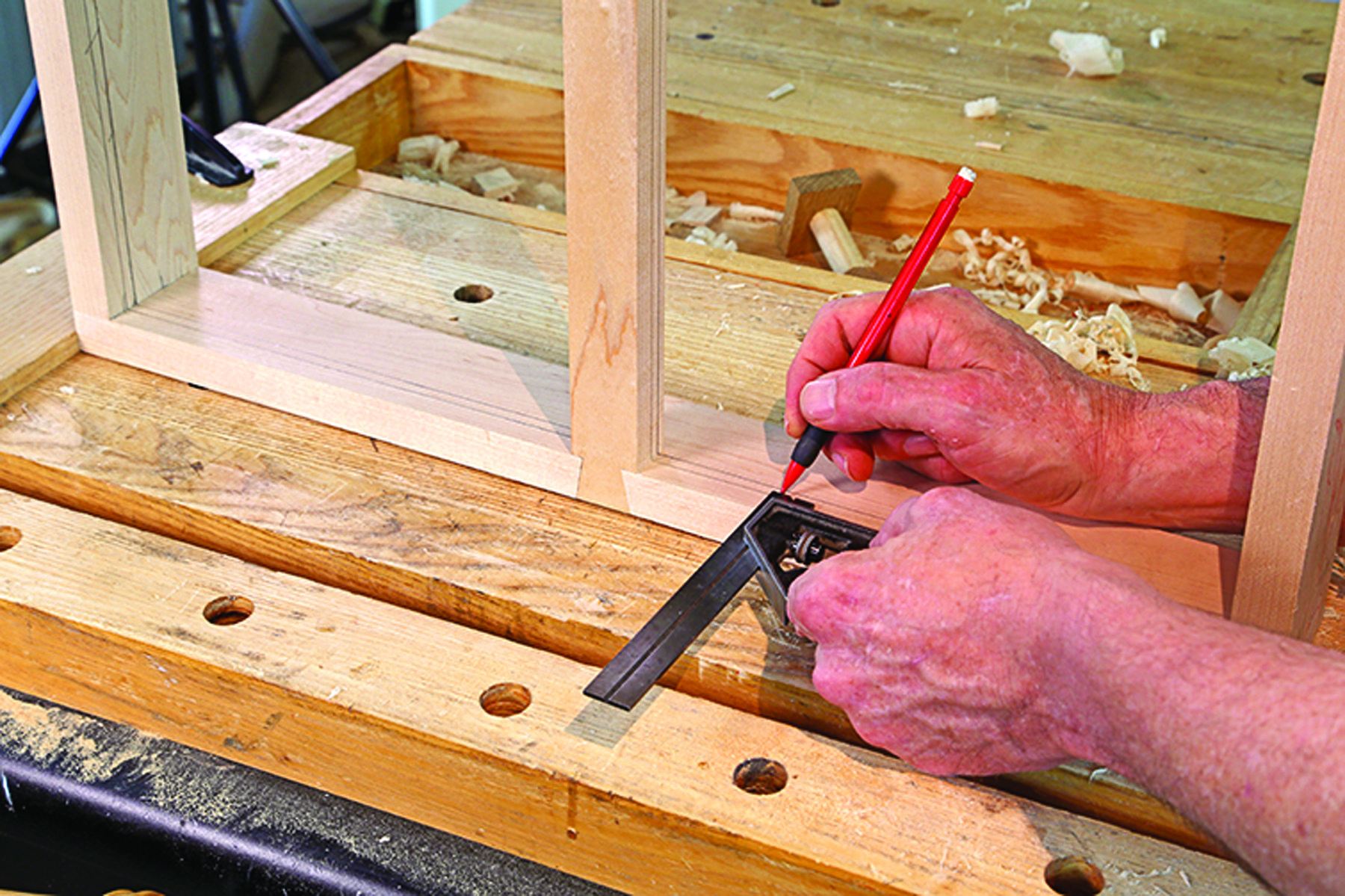
Mark together. Assemble the frame of the door before laying out the groove locations for the panels.
I made the door before I glued the carcase together, just in case I needed to adjust one or the other to ensure they fit together nicely. The outer corners of the door are simple through-dovetails. The extra stile in the middle of the door makes it a beefier structure and allows for two solid-wood panels.
A single dovetail at each end of the central stile holds it to the rails. This tail is lapped back to the edge of the groove that holds the panels, about 1″ from the front edge. I dry-fit the five frame parts, then marked the location of the groove with these pieces together.

Stop right there. It’s easiest to make stopped grooves by bringing the tool to the work. Plunge first close to the ends, then make the cut in between. A mortise chisel makes short work of squaring the ends of the grooves.
The panels are 3⁄4” thick, with a cove cut from both sides to leave a 1⁄4“-wide tongue. The cove is a 1⁄2” radius and I set the front by eye until the cut looked pleasant, then lowered the cutter to make a smaller cut at the back. I then put a 1⁄4“-diameter spiral-upcut bit in a small plunge router and cut the grooves in my door frames.
The door is sturdy and easy to put together as long as the panels can slide easily in the grooves. The center stile is fit to the top and bottom rails, the panels are slid into place, then the stiles go on either end.
Moment of Truth
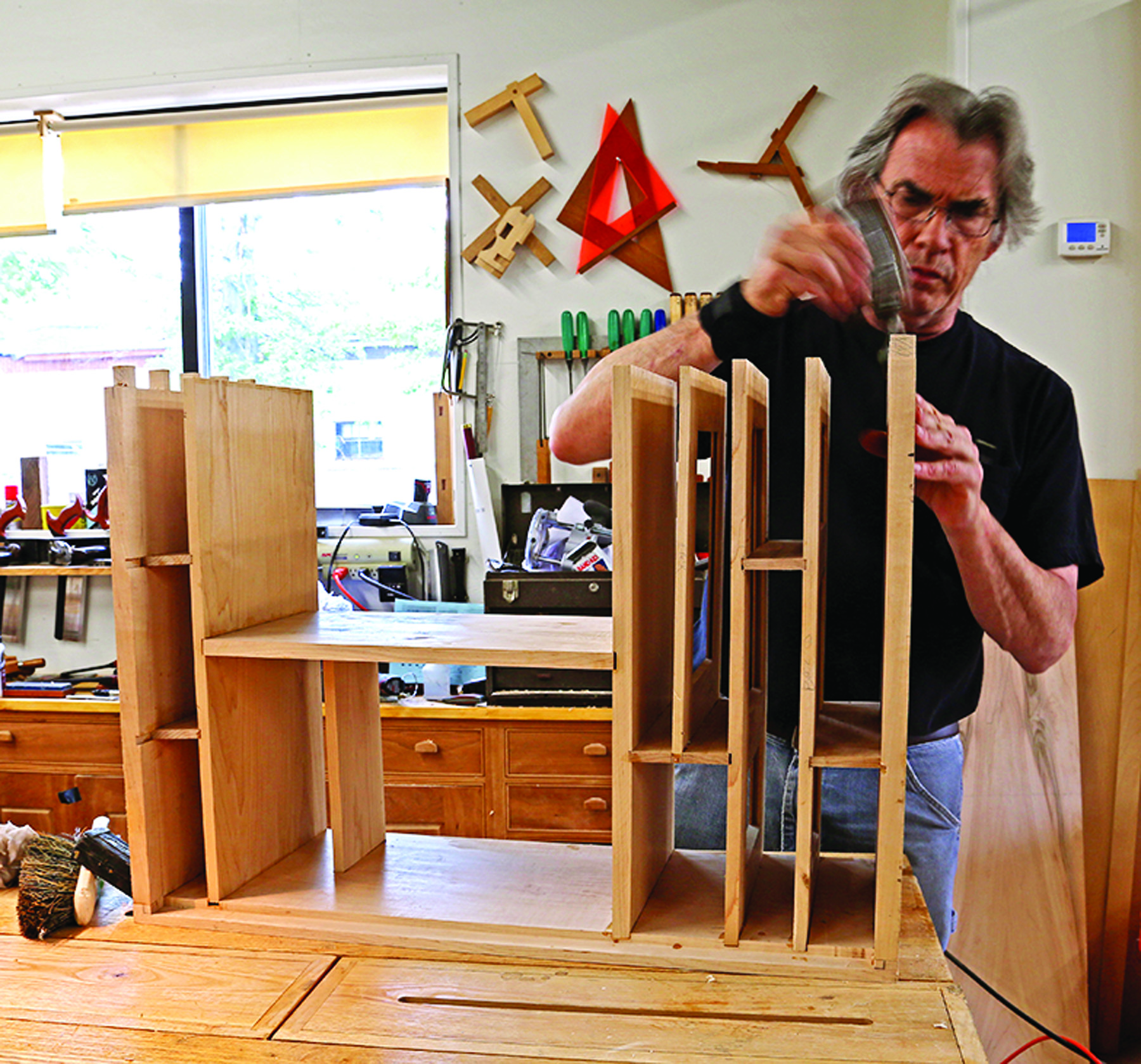
In sequence. There is a logical sequence to the final carcase assembly; with this many parts, it is worth a couple of practice runs to make sure everything fits
If all of the carcase pieces have successfully gone together in the dry-fit, final assembly can be done in one go. I made a couple of practice runs to be sure of the sequence and that I had the right number and type of clamps ready.
I laid one side down on my bench, with the dados facing up. Then I brushed liquid hide glue (for its long open time) into the dados and on the end-grain surfaces of the dovetails. (Letting the glue wick into the end grain gives much better glue joints.)
Assembly is from the center out. I fit the large vertical divider into the two solid shelves, then placed the shelves into their dados. The small shelf above the planes also goes in at this time. Then I placed the web frames, along with the small vertical dividers. There should be enough play between the frames and the shelves so that the dividers can drop into their dados.
Sliding the dividers in from the front would be silly unless the fit were too loose. If the fit is right they will get stuck before they get halfway back. With the dividers and frames all in place, I brushed more glue on the dovetails and added the top and bottom.

Square & tight. Liquid hide glue has a longer open time than yellow or white glue. That gives me time to make sure the corners are square and the joints are tight.
Before adding the second side, I brushed glue on the joining surfaces of the shelves and frames. Adding the second side is tricky, but not bad if the parts fit. I started the dovetails at the top and bottom, then lined up the shelves and frames and tapped them into the dados. When all the joints were started I drove them home with a mallet.
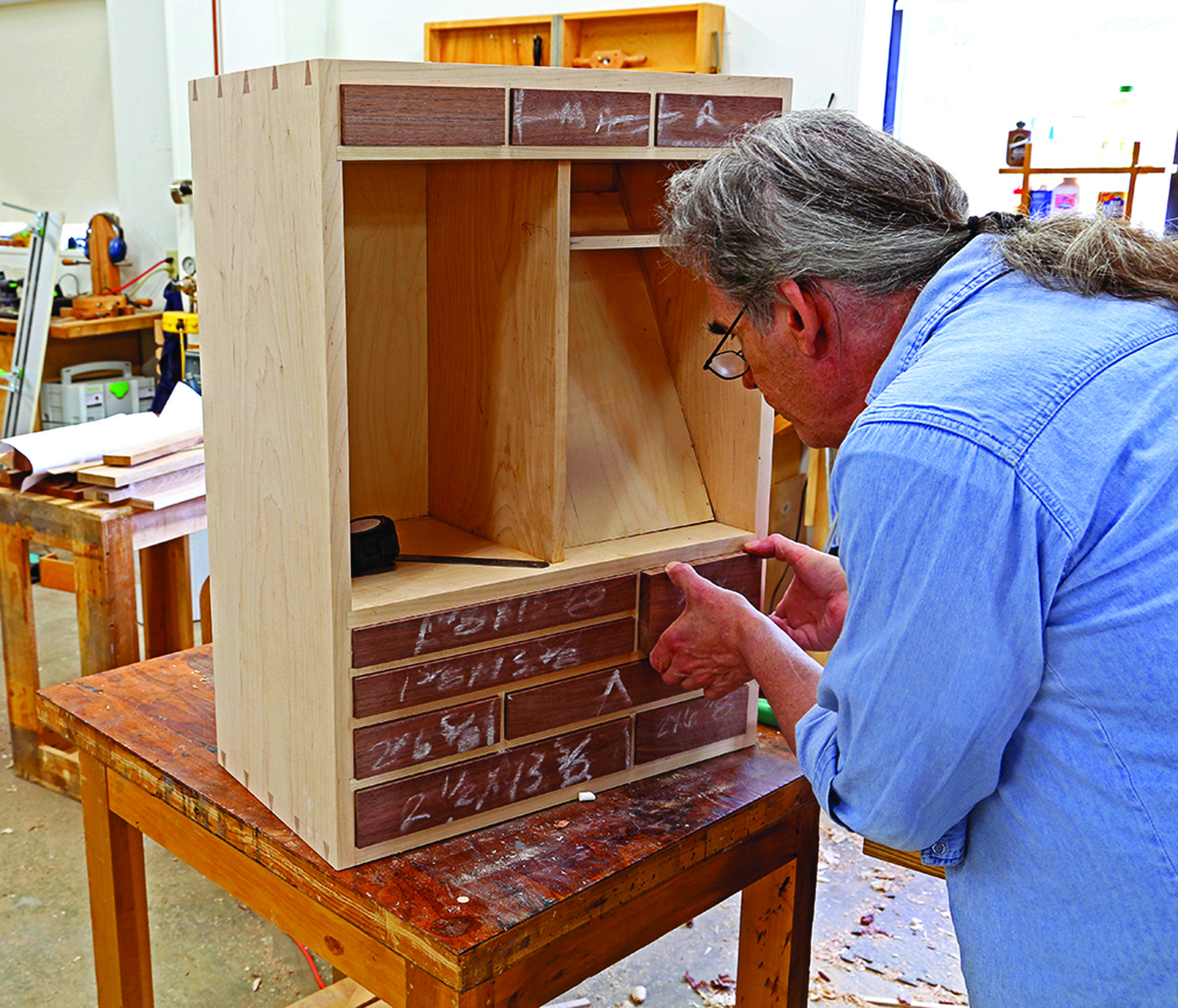
Fit first. I make sure that the drawer fronts fit in their respective openings before assembling the drawers.
If the dovetails fit, they shouldn’t need to be clamped, but I needed clamps front and back at most of the dado joints. As I clamped I checked to be sure that both the entire assembly and each corner was square. The final step was to cut and fit the plane ramp from 1⁄2“-thick plywood. It attaches to 3⁄4” x 3⁄4” cleats nailed to the side of the case and the vertical divider.
A Fitting Strategy
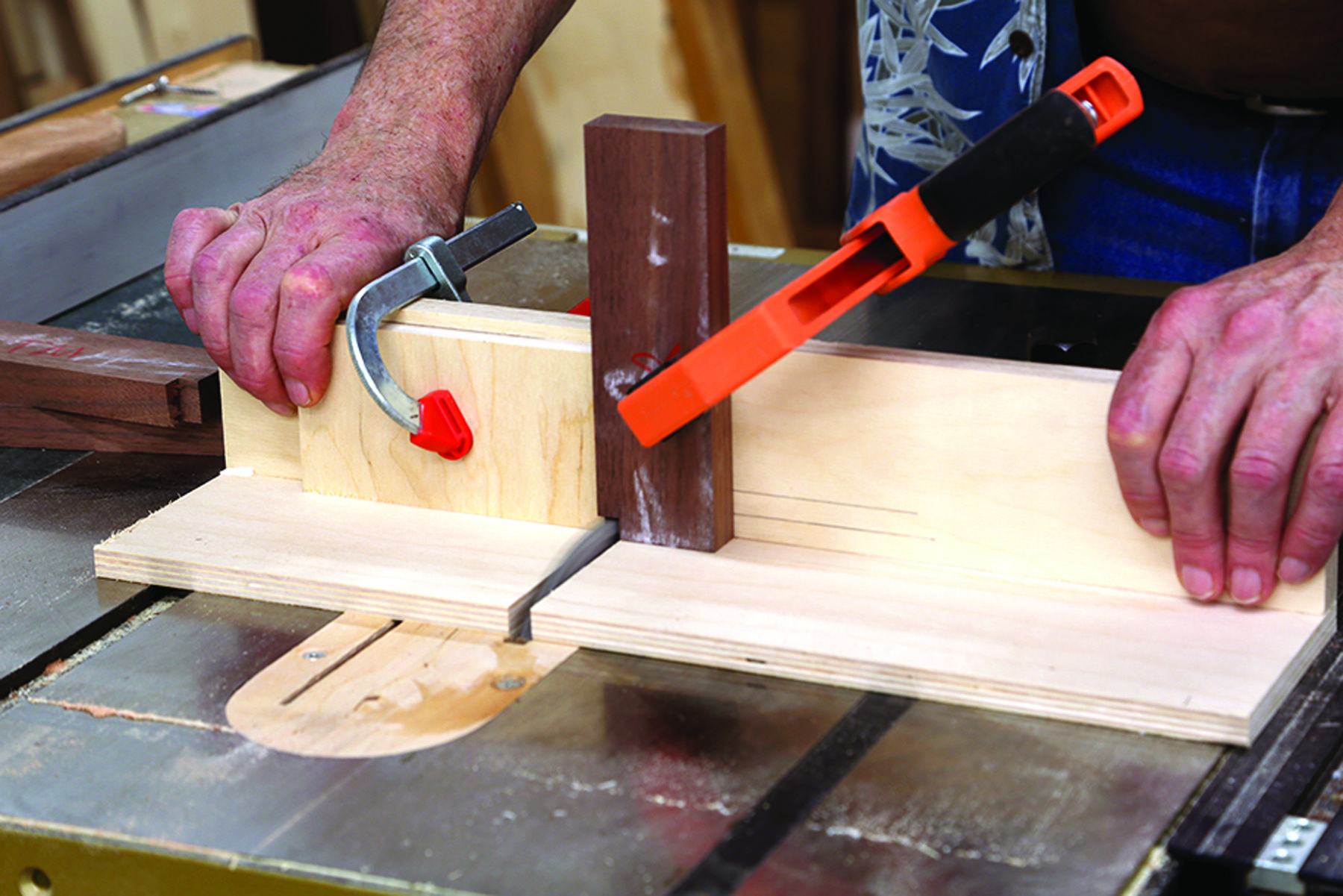
In this corner. A stop-block on the jig (attached to the table saw miter gauge) is used to make identical cuts on all corners of the drawer fronts.
I have two methods to ensure nice-fitting drawers. The first is to fuss over the openings and try to get them as perfect as possible. The second is to fit the parts of the drawers to the openings before assembling the drawer boxes.
I start with the drawer fronts. After marking a rough layout with chalk, I cut the fronts slightly larger than the openings. I carefully trim each front until it just fits in the opening. I want a slight gap when I’m done, but at this point I aim for a snug fit.
I fit each side to easily slide into an opening. If there are any variations in the openings, I plane the edges of the drawer sides to compensate. My goal is a gap of 1⁄32” at the top of the sides. This means the sides can vary, so I mark each one with its location.

This to that. Much like a dovetail joint, the finished fingers of the drawer fronts are used to mark the sides for the matching half of the finger joints.
My theory is this: If the fronts and sides fit nicely, the assembled drawer should fit with minimal fuss, as long as the joints between them are correct. I chose to use Greene & Greene-style finger joints, but the principle applies no matter how the pieces are joined.
I started by laying out the joints on the fronts. Each has a 3⁄8” x 3⁄8” notch at the top and bottom corner and except for the two short drawers and the tall drawer there is a 3⁄8” x 3⁄8” notch centered vertically. The tall drawer has notches that line up with the notches in the short drawers next to it.
I made a jig from two pieces of plywood and attached that to the miter gauge of the table saw. I used a Freud box-joint cutter set to make 3⁄8“-wide cuts and set the height of the blade to 3⁄8” above the flat part of my jig. I ran the jig over the blade then set the pieces vertically, lining up the layout lines to the edge of the cut.
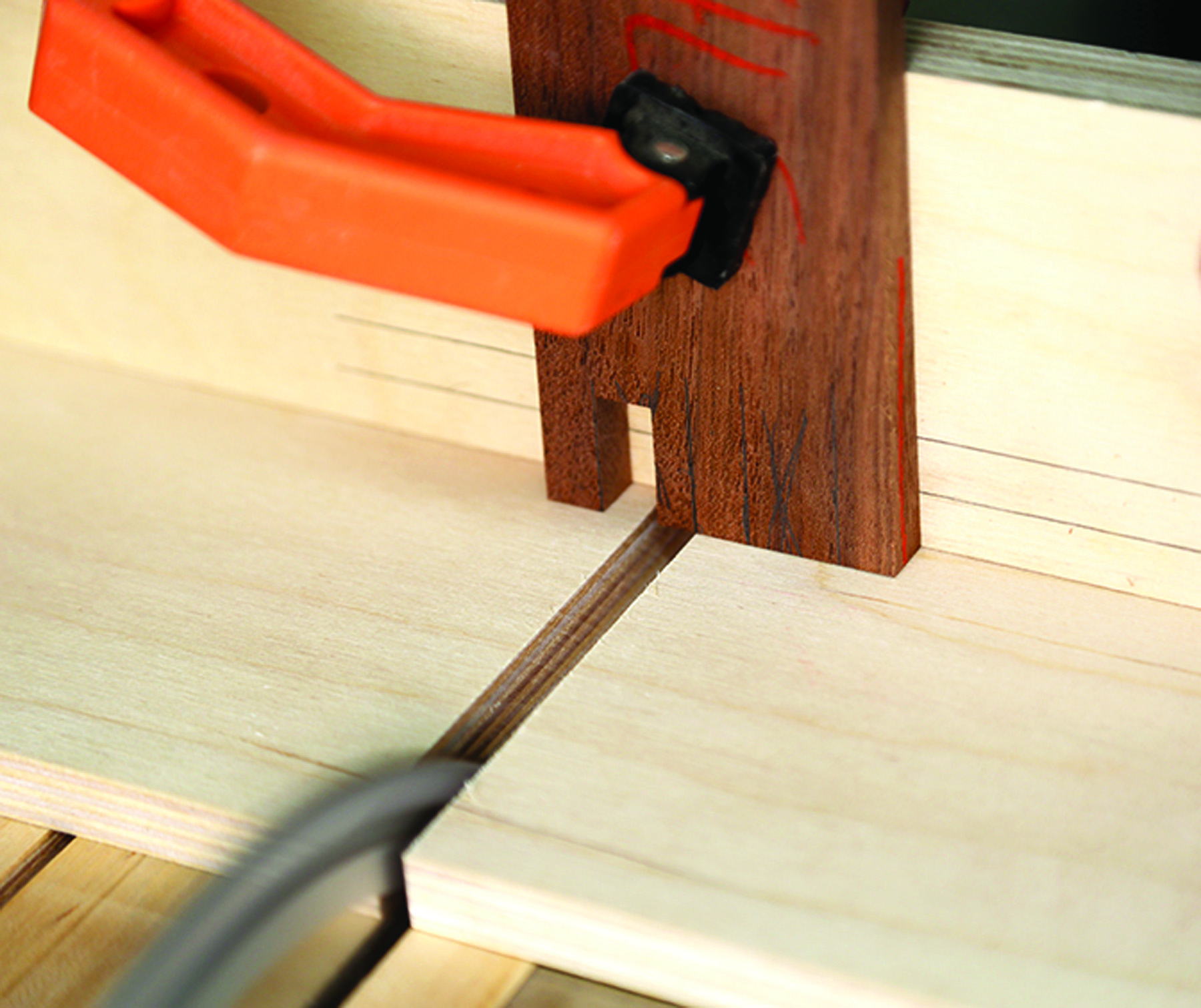
A little higher. The same jig is used to cut the fingers in the drawer sides. The saw blade is raised to the thickness of the drawer fronts plus 1⁄16″.
For the corner cuts I clamped a stop-block to the jig and for the interior cuts I positioned the fronts by eye. These pieces are rather small, so I recommend clamping the work to the jig.
When the notches were all cut in the fronts, I cut a shallow rabbet in the back face behind the pins to make them easy to register on the sides and marked the joint locations with a pencil. (I fudged the sides down from the fronts about 1⁄32” when marking the joints.) This leaves the desired gap at the bottom of the drawer front after assembly.
I raised the blade by the thickness of the drawer fronts plus 1⁄16” and cut the fingers at the table saw. These joints should fit easily together with hand pressure only. When I had two sides connected to a front, I tested the fit in the corresponding opening. The offset in the joints raises the front, so I planed the top edge of the drawer fronts to leave a slight gap.
I cut the drawer backs to length, matching the distance from side to side of the dry-fit sides and fronts. The drawer bottoms fit in 5⁄16“-deep rabbets to maximize space in the drawer, so the width of the backs is 5⁄16” less than the sides. The backs and sides join with through-dovetails.
After cutting the back joints, I dry-fit each drawer and made sure it fit in its openings before cutting the rabbets at the router table. The rabbet should be as narrow as possible because the drawers slide on what remains beyond the rabbet. After routing, I cleaned up the corners with a chisel.
Get a Grip
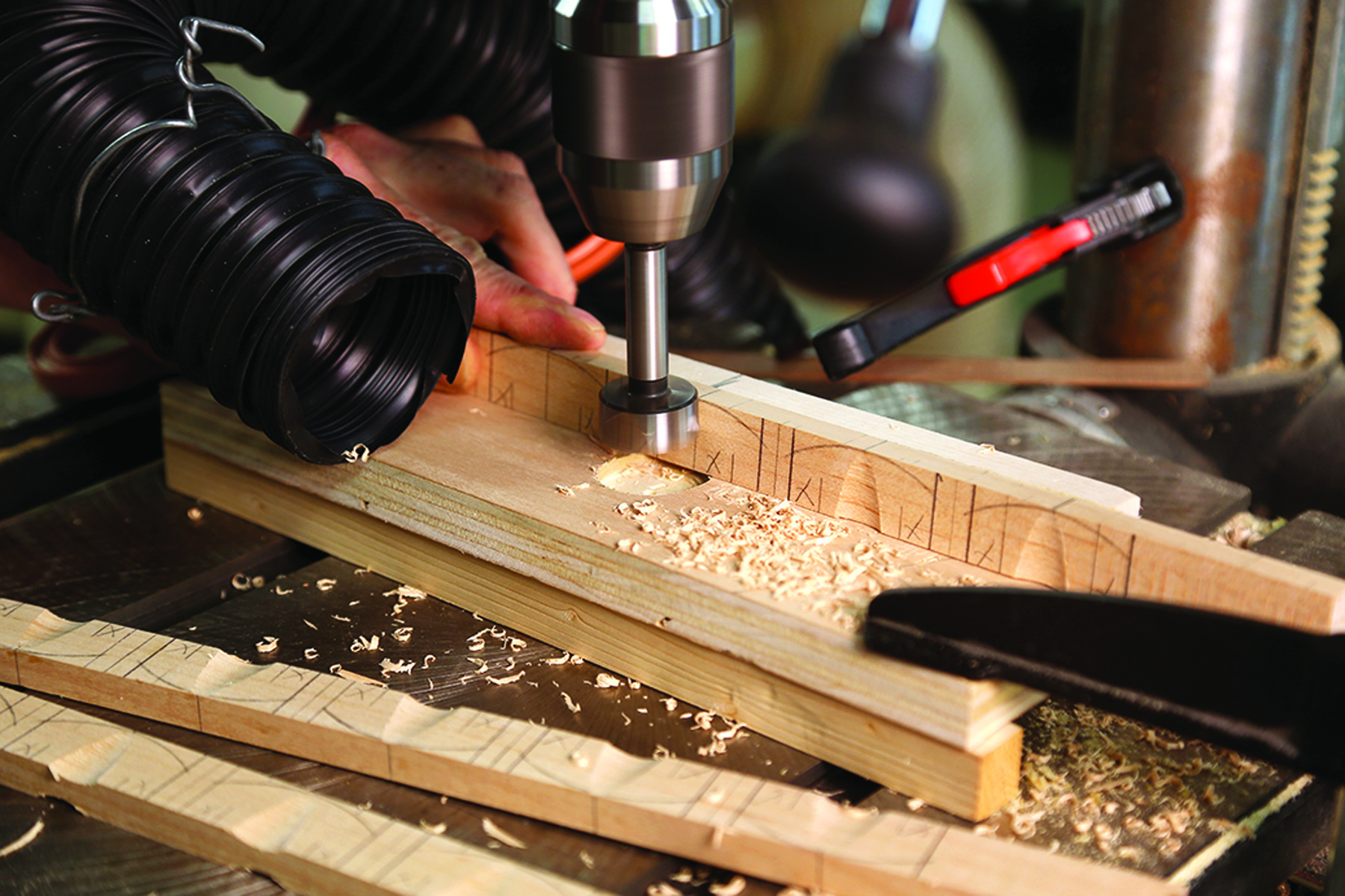
Here’s the scoop. This blank will become a half-dozen pulls. After laying them all out, the Forstner bit makes an angled cut on each side for make a finger-friendly pull.
Rather than throw money at the drawer pulls, I decided to make my own. I played around with the concept of a shaped wood pull in a shallow hole. After settling on a design that looked and felt good, I needed to come up with a way to efficiently and safely make 14 pulls. I prepared a few pieces of maple 3⁄8” thick x 11⁄16” wide.
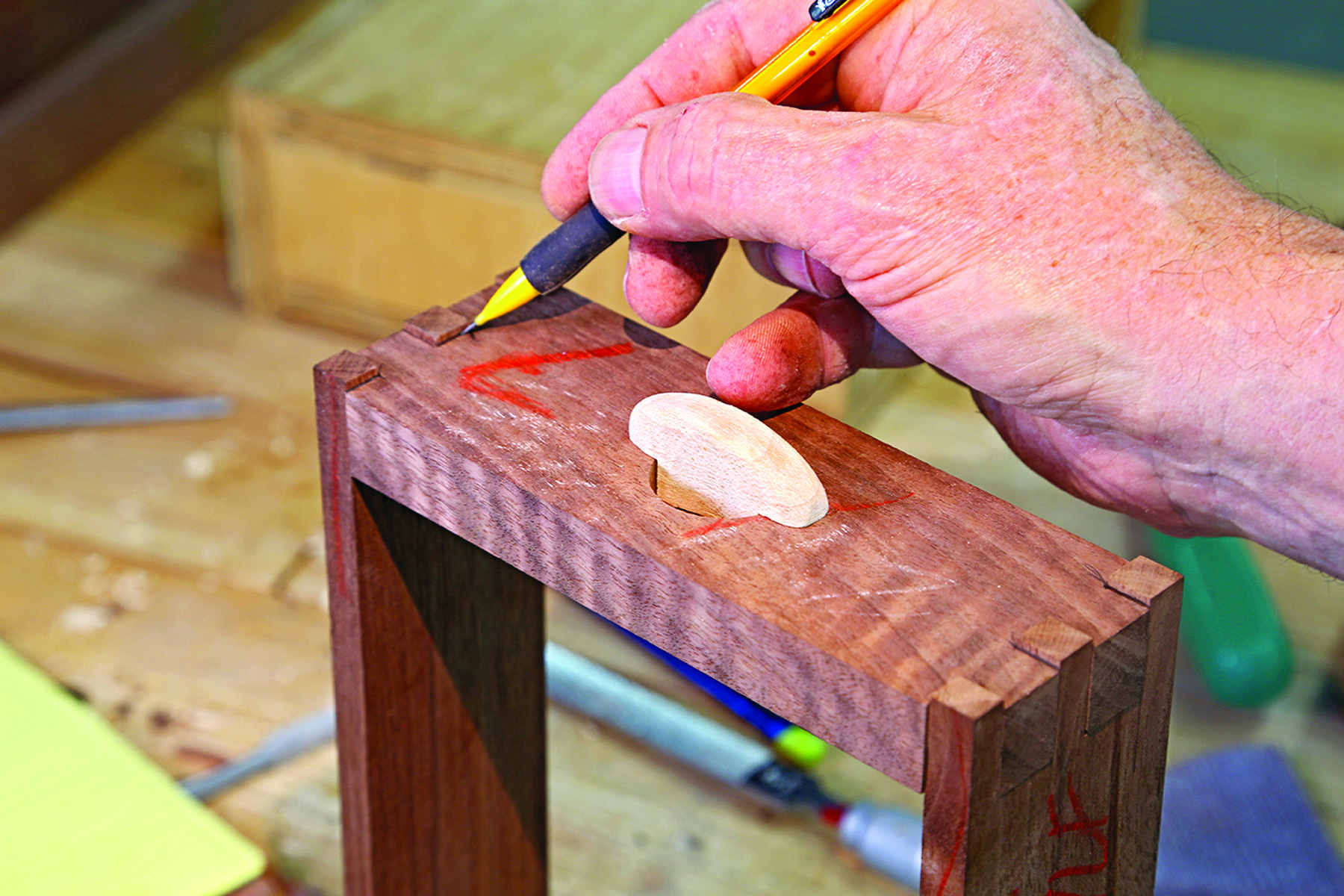
Make the target. The face of the drawer front is marked directly on the fingers of the drawer side in the dry-assembled drawer.
I laid out the pulls on the blank stock, leaving a couple of inches extra on each end. I set up at the drill press to hold the blanks at an angle below a 1 1⁄8“-diameter Forstner bit, then lowered the bit to scoop the center of both sides of each pull.
I took the blanks to the table saw (where the 3⁄8“-wide box-joint cutter setup was still in place) and cut notches at the end of each pull. At the band saw I cut the arcs on the other edge of the blanks then separated the pulls. I refined the edges of the scoops with a gouge, rounded off the curved surfaces, then drilled a 3⁄8“-deep x 1 1⁄8“-diameter hole in the center of the narrow drawer fronts. The holes in the wide drawer fronts line up with the holes in the short ones.
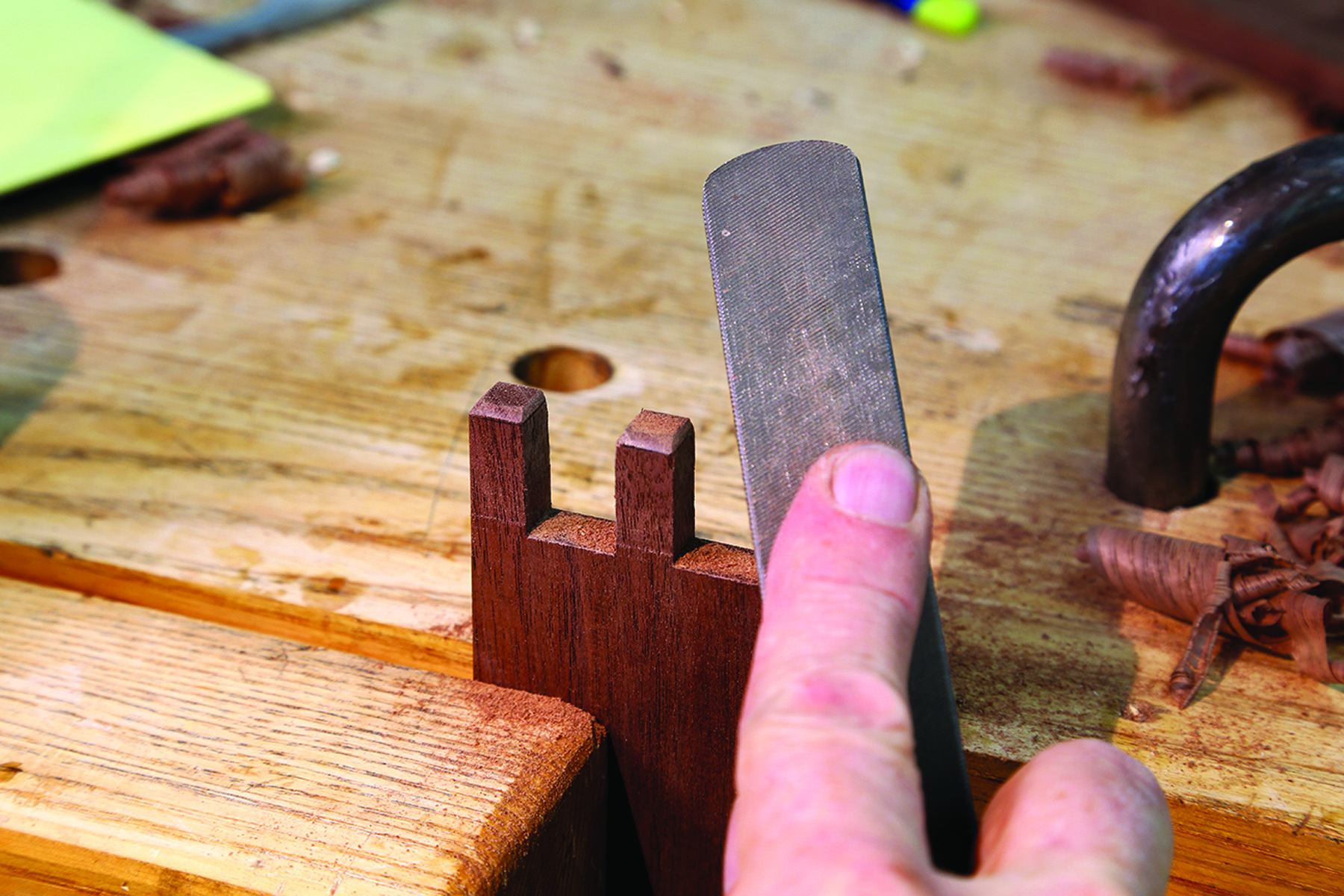
Hit the target. The edges are rounded over to the pencil line with a file. The file also cleans up the saw marks of the end grain.
With the drawer fronts and sides dry-fit together, I marked the location of the drawer fronts on the fingers of the sides. I pulled the sides off and rounded the edges of the fingers back to the pencil lines with a plastic laminate file. After that, I glued the drawers together, cleaned them up and made sure they still fit.
The Tools I Need & Where They Live
Hand tools have much in common with the medical profession. When you look at a catalog, or a list of recommended tools in a magazine or online, you see many specialists along with a few tools that tend to most tasks. The problem is that without experience, you can’t tell which specialized tools you need (or want), or if problems are the fault of you or the tool.
Too many tools, too early on, cause more problems than they solve. One saw will get you started. When you learn how to control it, you’ll be able to assess its shortcomings and make an informed decision about what might suit you better. It’s the same with chisels and planes. Start with one tool, learn how to sharpen and set it up then put it to work.
If your goal is to make attractive and useful things, either as a hobbyist or a professional, you need to be familiar with all your options, both hand and power. If you’re new to woodworking and stick with it, you’ll eventually have a lot of tools, but the secret is to understand what they do and how they do it. That takes experience.
I started with a few good tools and added to them as my experience saw the need and my budget allowed. The following are the tools that I consider essential; they suit my budget and the way I work. Don’t blindly follow my list – think about what makes sense for you and where you want to go with woodworking.
In my tool chest, marking, measurement and layout tools are the most visible for good reason. And buying good tools for those tasks was the first investment I made. My combination squares, marking gauge and calipers plot the path before work begins, and check it when it is done. What matters is that the parts are the right size and in the right place – not what tool made them. If I were starting out, the first tool I would get would be a quality combination square. I also rely on a pair of fractional dial calipers, a 6″ precision rule, a marking gauge and a sliding bevel. Don’t try to get by cheap with your layout tools.
Chisels aren’t just for dovetails; they trim little bits and pieces left over from machine work, reach into places power tools can’t, scrape excess glue away and perform dozens of other tasks. Inexpensive chisels will teach you how to grind and sharpen (you won’t have to worry about ruining the good ones), and the jobs that these can’t easily tackle will let you know what specialized chisels to buy when you need them.
Smacking things is more specialized than you might think. You need something metal to pound nails, and something softer to beat on things a metal hammer would damage. A claw hammer and a dead-blow mallet are essentials, although I can justify the others in the photo and the other half-dozen I have tucked away.
Many woodworkers get by without a handsaw, but there are times when pieces are too small, too close to something else or inconveniently located to cut by machine. Or the machine is set up for something else and a single cut needs to be made. One middle-of-the-road saw (in quality and price) will suit your needs, and may lead you to discover the situations where cutting by hand is more efficient, gives better results or both. Practice with a single tool teaches you more than wondering which of the bunch to pick up.
I have more than a few handplanes, and they are called into service to refine the grunt work done by machines. My smoother removes machine marks faster and better than a belt sander or random-orbit sander, and my shoulder and rabbet planes tweak and refine joints that my table saw and router get pretty close. I began with a block plane, and it is still the plane I use most often. It is versatile and simple to set up and use, and its limitations taught me which of its more specialized brethren to add. Of course, if you are building a collection, you’ll want one of each. If you’re building furniture, experience will lead you to the tool kit that is best for you.
— RWL
A Happy Home
I arranged the tools on the door in logical groups. My framing square is in the upper-left corner with my combination squares nested within the legs. The holders for the small squares have a rabbet in the top edge. That leaves a ledge to keep the stocks in place, and a notch in the end holds the blades. The curved shapes reflect the shapes of the stocks of the squares.
To the right of my squares is a block to hold smaller tools. The front and back are 3⁄8” thick, separated by 1⁄2” x 1⁄2” squares. At the far right, the end extends above the front and ends in a semi-circle. A screw in the top secures that end to the door stile. At the other end, a screw goes through the block and into the center door stile.
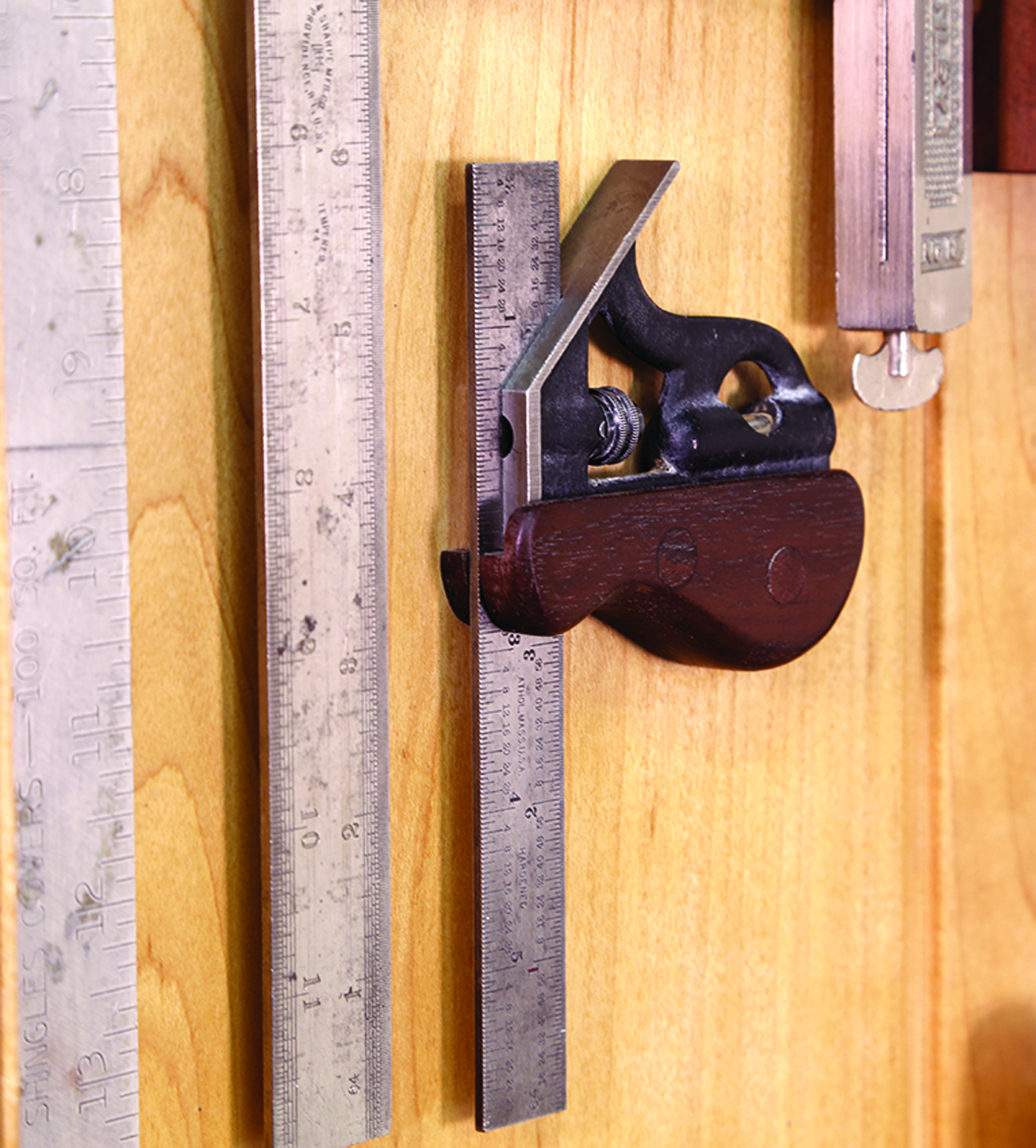
Reflection. This holder for an adjustable square uses the shape of the tool for its overall form. The slot holds the square securely when the door opens and closes.
In the lower half of the door is a rack for chisels, placed high enough to clear the drawer pulls. That rack is 1 1⁄4” wide, with 1″-diameter holes drilled on 1 1⁄2” centers. The centers of the holes are 3⁄8” back from the edge. I made saw cuts to square the ends of the openings so chisels can be put in from the front. Two screws through the outside of the door hold the rack in place. Plugs cover all the screws.
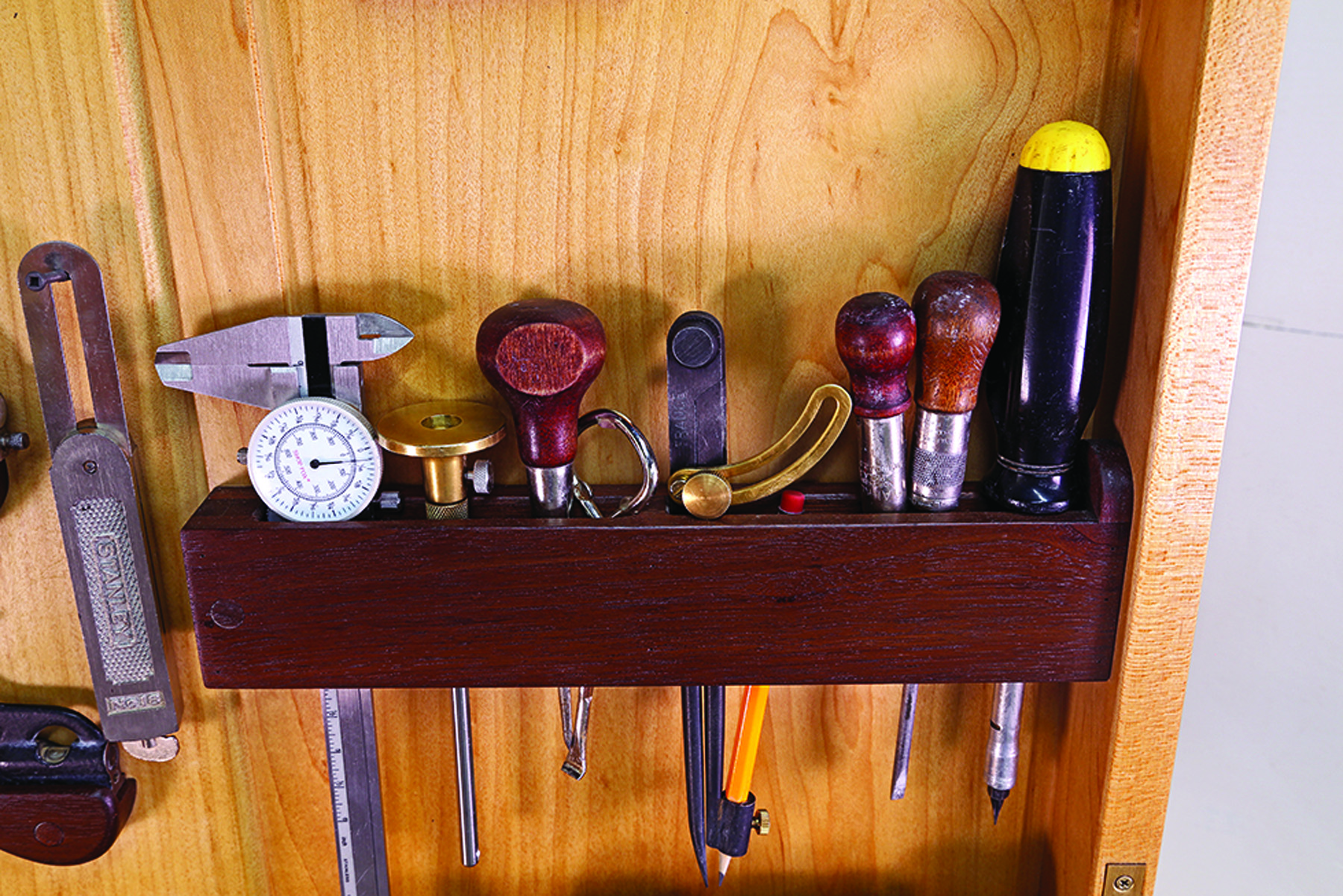
In the gap. The 1⁄2″ space between the front and back of this simple rack provides flexible storage for tools I might need in a hurry.
I cut some thin pieces of walnut to the shape of the back of my planes, and fastened them to the face of the plane ramp. I put the smooth and jack planes as far up the ramp as I could to make room for smaller planes below.
On the left side of the case is an open area; saws and hammers fit on walnut holders at the sides and back, leaving room for small power tools or my mug.
And Swing It

Router base. A scrap clamped inside the door keeps the router base from tipping and the fence defines the back edge of the hinge mortises.
The door is heavy on its own, and the tools inside add even more weight. I decided to go with three 111⁄16” x 3″ brass butt hinges. I centered the middle hinge vertically, and centered the top and bottom hinges on the top shelf and lowest web frame.
I routed the gains for the hinges 1⁄16” deep. The hinges were not swaged, so I used a chisel and cut the outer edges of the gains deeper to leave the smallest possible gap when the door is closed.
The lock is a full-mortise piano lock let into the door halfway up. It has two wings that extend past the strike when the key is turned.
I sprayed shellac for the finish. The first coat was amber to warm the color, followed by two coats of clear. After letting this cure over a weekend, I took the sheen off with an abrasive pad and applied a coat of paste wax.
The back is screwed in place and the cabinet hangs on a French cleat – two 41⁄2” wide pieces of plywood with a 45° bevel on one long edge. The cabinet side of the cleat is screwed to the shelf below the top drawers and the vertical divider. The other part of the cleat is screwed to the wall studs.
I’m not the most organized person, but I like the tools I use the most hanging near my bench. If I can’t find a tool I need, then turn around to find the cabinet empty, I know it is time to stop and clean up a bit.
Blog: Learn the tips and techniques that Bob Lang uses as he fits the drawers in his chest.
Video: Get a look inside one of the country’s most notable makers of machinists’ tool chests.
Blog: Learn how to transform a simple drafting square into a highly prized shop tool.
Here are some supplies and tools we find essential in our everyday work around the shop. We may receive a commission from sales referred by our links; however, we have carefully selected these products for their usefulness and quality.