We may receive a commission when you use our affiliate links. However, this does not impact our recommendations.
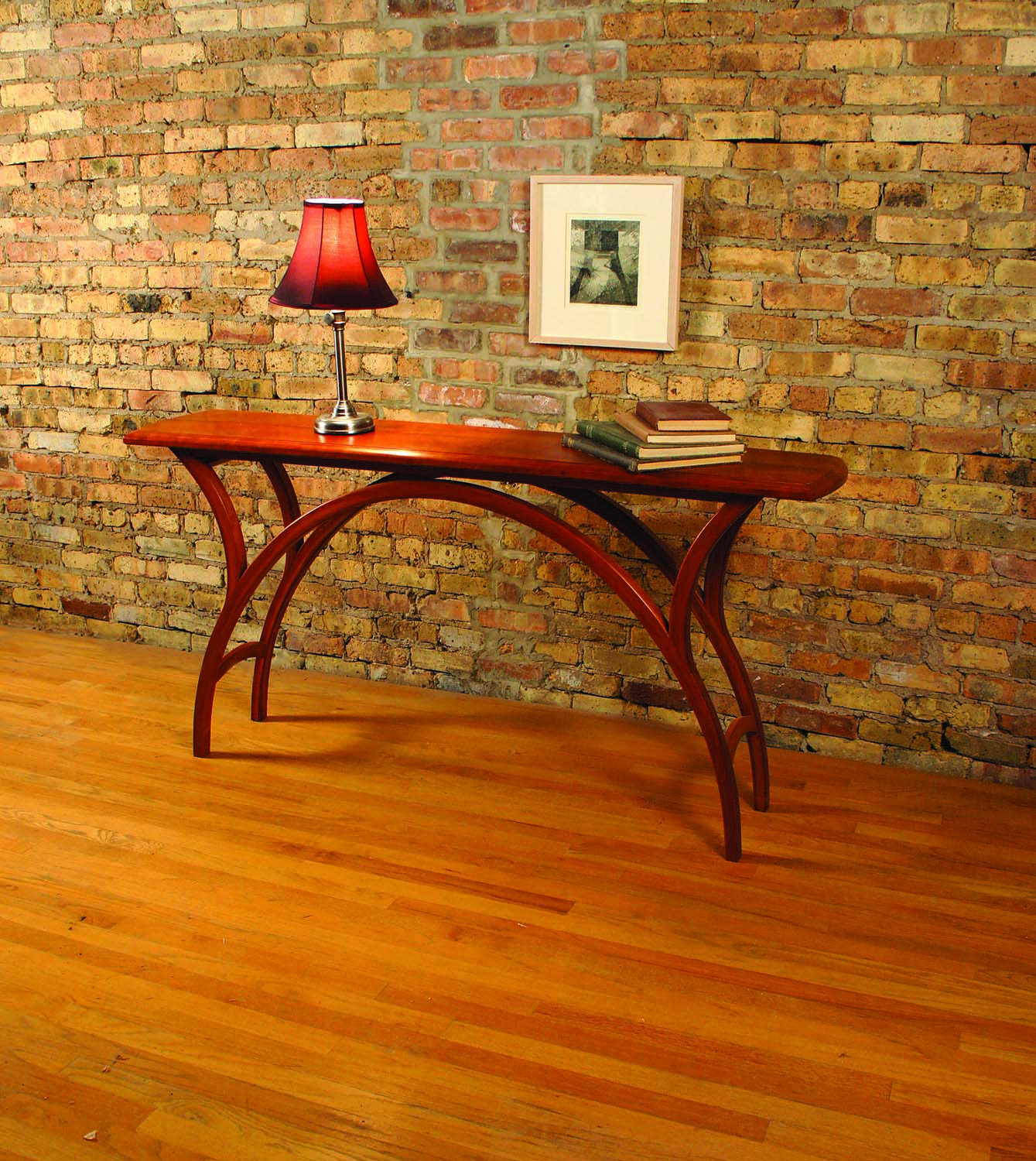
Simpler than it seems. This graceful arched table might appear to be a complicated build, but looks can be deceiving. The secret is in simplifying the joinery and providing flat areas where the curved pieces connect.
Many interesting pieces of furniture are deceptively simple. Deceptive, because although they appear simple, they are actually very difficult to make. Although this is occasionally true in my own work, that’s not the case with the Arch Table, a piece that looks more complicated to make than it actually is. I’m not saying it’s easy; there’s a lot of preparatory work, and it is quite demanding in terms of shop resources. But the stuff that looks hard to do is actually not all that bad.
This piece is a great introduction to bent lamination, which opens up an entire world of curved shapes and lightweight, incredibly strong components. There are a lot of ways to approach lamination; for this project I make use of table-sawn strips, and rely on forms and cauls for gluing up the curved components. The complex-looking joinery is mostly screwed and glued together. In early versions of this table, I used mortises and tenons for the branching joints, but because of short-grain considerations, I found the screws to be a much stronger solution.
Forms & Cauls
The major prep work is in making the forms for the laminations. For the table’s “wings,” you’ll need to make both a form and a caul (or a pair of each, if you want to speed up the process) for gluing together the layers. For the main arch, it depends on how many clamps you have available. I just glue up around a form with six layers of 1⁄4” Masonite acting as a caul, distributing pressure and preventing dents from the clamps. But I use 26 bar clamps in the process; without that large a collection, you’ll definitely need to make up the cauls for a successful glue-up.
Layout for the forms involves drawing sections of some large ellipses. I made up a fairly simple ellipse-drawing jig. You could also draw an ellipse on the computer and print it out full-size then tape the tiled pages together. It’s also possible to draw this ellipse with a loop of string and two nails. However you create the shape, it’s best to draw directly on a piece of 3⁄4” plywood. Then cut it out as accurately as possible, and smooth to your line. You can also cut out the center section of the form at this time. Accuracy there is not nearly as important.
Use this first layer of the form to mark out the next two layers (note: you can piece together one of the layers if necessary), and cut them slightly oversized. Then glue and screw these layers to either side of the original, and flush them off using a router and flush-trim bit. Finally, go over the edges with sandpaper to even out any irregularities, then wax the edges plus a little bit of the sides of the form.
To make up cauls, you need to know the overall thickness of your lamination. You should wait until you’ve actually ripped the strips for that, then clamp together all but one of your strips into a bundle to get an exact thickness (the last strip gets glued on after attaching the wings). With this information, you can make a scribing disk. This disk is used to draw the exact curve needed to apply even clamping pressure to the outside of the bundle of strips all the way around the curve.
I make these disks on the drill press using a fly cutter – one of those rather terrifying circle cutters with an adjustable cross beam and cutter. You want the distance from the edge of the center hole (not the center of this hole) to the outside of the disk to be the same as your lamination thickness.
Set your form down on a piece of 3⁄4” plywood, and roll the disk around your form with a sharp pencil pressed against the edge of the center hole to mark out the caul. Cut, then smooth carefully to your line, and add two more layers of plywood and flush trim those just as you did for the form itself. If you’re doing this for the big arch, you’ll ultimately want to break up the caul into three sections to keep it manageable. You’ll also want to make registration marks, or even add some wooden registration strips, so the form and cauls will line back up exactly right when the time comes to glue your lamination.
Rip Strips for the Laminations

Safety first. The saw is set to rip strips to a precise width at the outside of the cut, which is safer than cutting thin pieces between the blade and the fence.
You will need roughly 16 3⁄32“-thick strips, ripped from stock that is 17⁄8” to 2″ thick, to make up the final thickness of 11⁄2“. Mark a layout triangle on the face of your board before you do anything else. I rip the strips on the table saw, and always set up so that I cut the strips to the outside of the blade. This means re-setting the fence after each rip (moving it over 3⁄32” plus the thickness of the blade). Setting the rip fence at 3⁄32” and trying to rip the strips is a major safety problem and can lead to some nasty kickback and shattered strips. Because this constant adjustment of the fence is a pain, it makes sense to cut down your wood into two or three equal widths (try for two pieces at least 33⁄4” wide). That way you can rip more than one board at the same setting. Be aware that it’s unsafe to rip strips out of a board that’s less than 1⁄2” wide. Don’t even try.
Use a featherboard to press the wood against the fence, but only in front of the blade. You’ll also need a push stick handy for when the board gets narrow. Pile up the strips in order as they come off the blade, or in multiple piles if you’re cutting from more than one board. If things go awry, you can always put the strips back in order by referring to the layout triangle.
You’ll need one less strip for each of the wing bundles than you’ll need for the arches; the outer layer will come from the outer layer of the arch, which gets glued on after you join the wings to the arch.
Glue Up the Laminations

On a roll. A paint roller makes quick work of spreading the glue evenly on all of the laminations.
Most wood glues have a small amount of flexibility to allow for joint expansion and contraction. When you’re gluing together a lamination, however, that flexibility can lead to the layers slipping a bit in relation to their neighbors. This glue-line “creep” can cause the laminated shape to lose some of its bend (springback), and can create little ridges between layers. The best bet is to use either Weldwood Plastic Resin Glue (a powder and water mix), or Unibond 800 (a powder and liquid mix). Both have rigid gluelines, long open times and work especially well for this type of work. These glues also require caution when working with them; be sure to wear a good dust mask and gloves while mixing, and keep the gloves on throughout the preparation and application.
Before you do anything else, set aside the outermost strip from each of your two main arch bundles. Label these strips so you’ll be able to glue them on later in their proper places.
There’s a little more preparation needed before you can actually glue up your laminations. First, you’ll want to figure out where you can do the glue-up. I work on the floor mostly because I’ve been doing it that way for 25 years, but my shop floor is completely covered with glue spots; this may not go over so well in your shop. It’s also easier to work at a more comfortable height. My knees have been lobbying for this change of late.
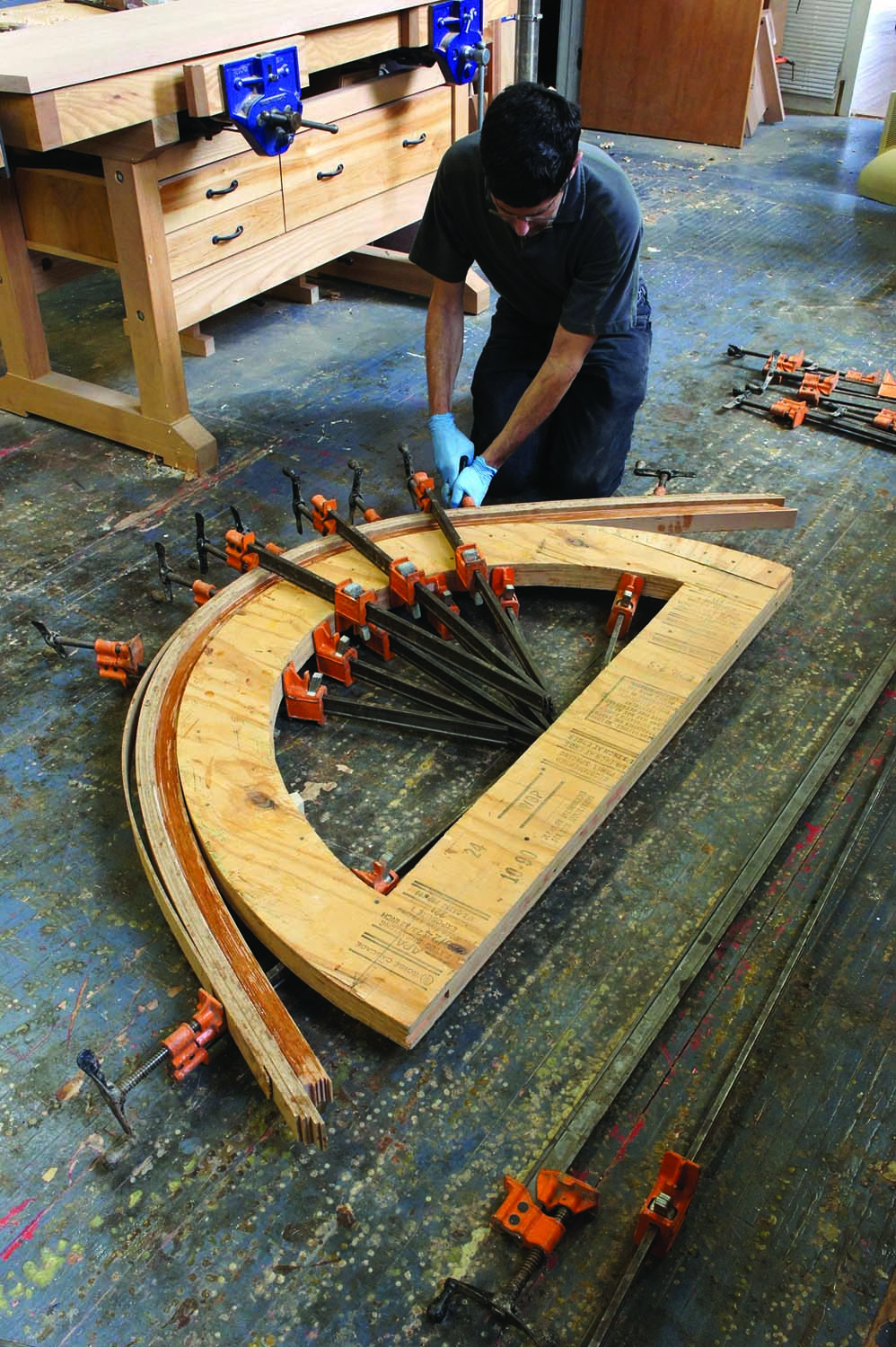
Practice first. Before you add glue, do a dry run to ensure you’ve enough clamps – and that when then glue is on, you know where to place them.
Setting up a piece of melamine board (which can be scraped clean when you’re done), or plywood on solid sawhorses or benches is probably preferable. Or just cover your floor with cardboard, plastic or paper. You’ll also want to protect the floor or set up a second worksurface where you can roll out the glue on all of the remaining strips.
It pays to go through a dry run to be sure you have everything ready to go and to familiarize yourself with the process. Set your form on top of a few wood blocks sized to make it easier to get the first clamps into place under the form. If you haven’t already, prepare the six 1⁄4” x 2″ Masonite strips or a set of cauls.
You may want to position a handful of clamps under the form, ready to receive the lamination. In any event, all the clamps should be at hand. Center the bundle of strips on the form, then bend the strips into place for your dry run. Start clamping at the top of the arch and work down the sides, alternating clamps above and below the form as you go.

Caul of the wild. A form for the outside of the curve helps to spread clamp pressure, reducing the number of clamps needed.
The actual glue-up starts with laying out all of your strips in order, then separating the top strip from the rest, so you don’t accidentally get glue on it. Mix up your glue – about a cup and a half should be enough for the main arch – according to the directions. Then roll the glue onto your strips with a foam paint roller. I don’t bother with a paint tray; I just pour a little glue on the strips and spread it around. Make sure you cover the strips completely, and go over any spots that look a little dry. Stack up the bundle in order (including the top strip), and clamp it to your form as you did during the dry run. Try to keep the edges of the strips reasonably well aligned; it will make smoothing the edges much easier. Let the glue set for at least 12 hours – longer if it’s colder than 70° Fahrenheit in your shop. Finally, before you remove the clamps, transfer the marks for the bottoms of the arch from the form onto your laminations
The process is the same for gluing up the wings.
Smooth the Laminations
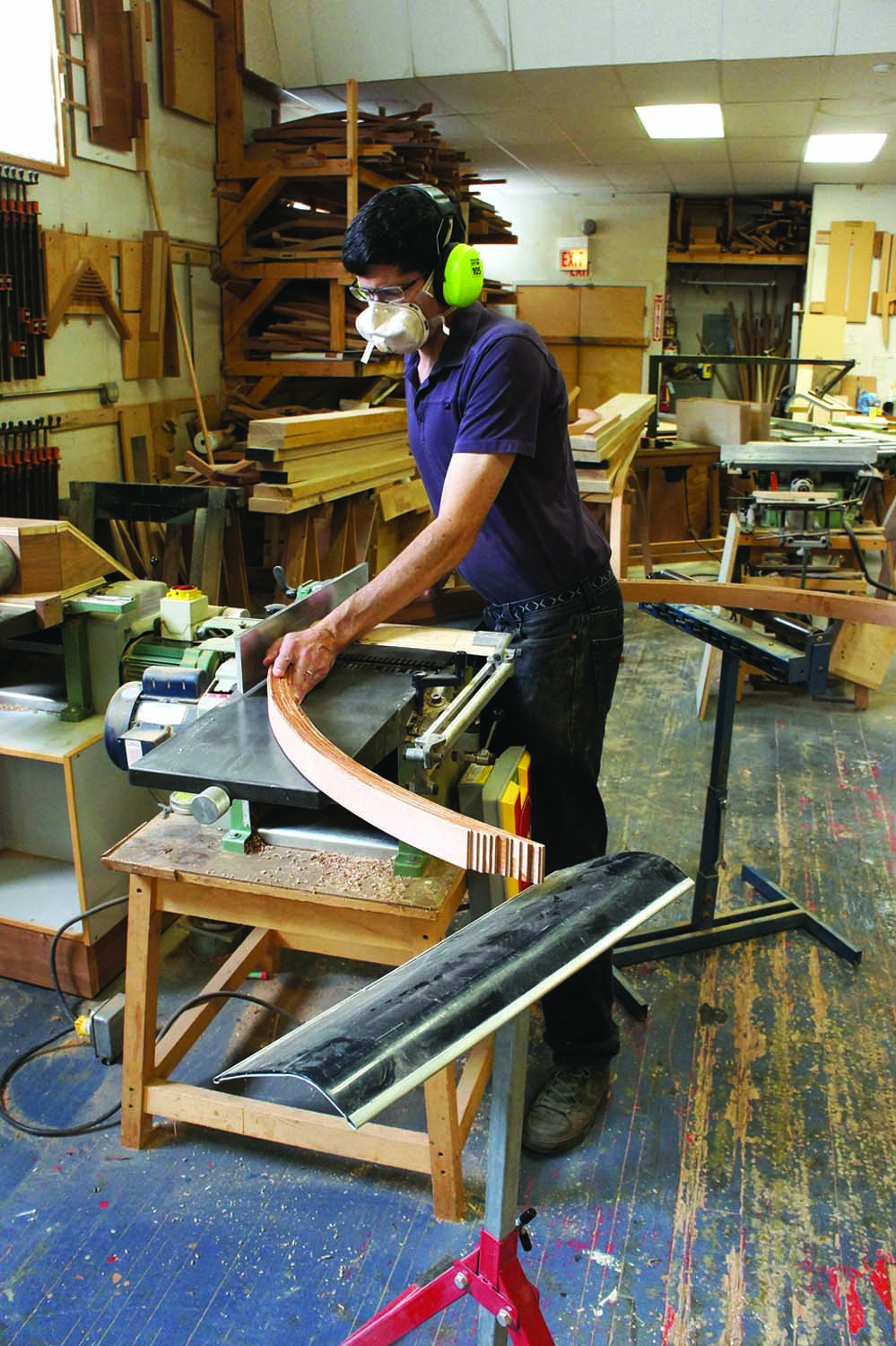
Ahead of the curve. The jointer levels the surface of the lamination. Infeed and outfeed supports help keep the material flat on the machine bed.
When you take the laminations off the forms, they will look like a mess. Before you clean up the edges, move the arch bottom location marks to the inner faces, where you won’t cut them away.
Set up infeed and outfeed supports next to your jointer, and joint one of the edges of the lamination. Unfortunately, this is pretty hard on the jointer knives, but I haven’t found much else that will do the job as easily and quickly. A few passes and you should have a clean edge. Then you get to pass the lamination through the planer. I know it looks odd, but it does work. Apologies to the planer knives as well.
Joinery
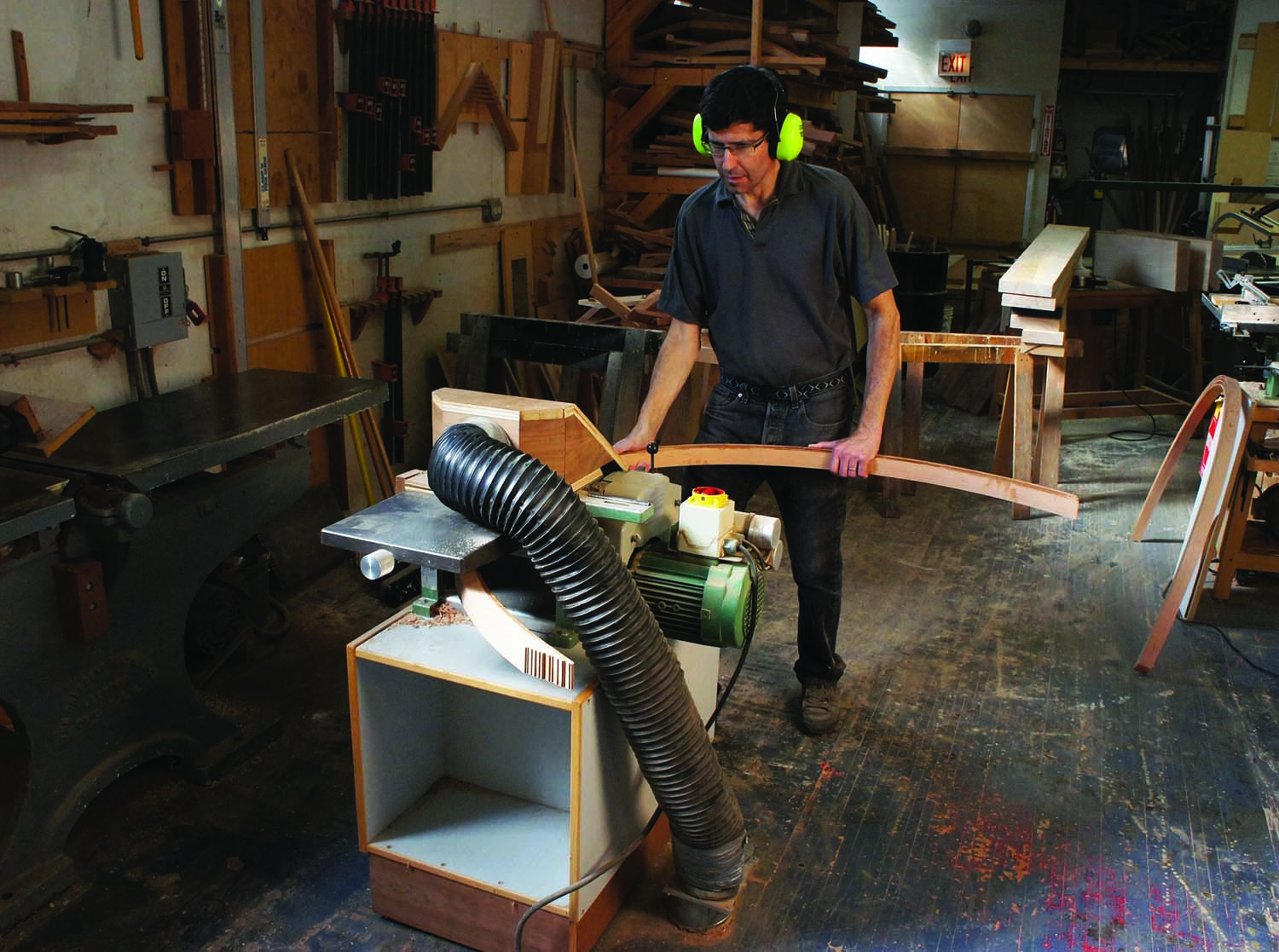
Around the bend. The opposite side of the glued lamination is surfaced with the planer.
Once the laminations have been machined smooth, it’s time to move on to sizing and joinery. The ends of the arches can be cut off at the marks using whatever method works best for you (you can always go back to the forms and re-mark if you forgot that step earlier). An outfeed support will be necessary if you’re using the table saw or band saw. Hold off on cutting the wings to length for now.
The joint between the arches and the wings has a routed flat on the arch where the bottom of each wing attaches. The flat begins 169⁄16” up from the bottom of the arch (along the outer curve, or 1511⁄16” measured straight up from the floor) with a 3⁄32” step down to the flat. The flat is roughly 41⁄4” long, and simply feathers out at the top; there is no step there. Start by marking the step-down locations on each side of the two arches. Then at one of those locations, measure down 3⁄32” and draw a line from there to 2013⁄16” up on the lamination as a reference for where the flat should end.

On the level. This jig supports a router, used to create a flat surface for the wing to connect with the large arch.
Make up a jig for routing the flats as shown in the photo on the next page. Two shims added between the jig and the lamination will set the jig up for the right cut. Put the jig (without shims) in place on top of the lamination, then shim it up so the top of the inner edges is flush with the layout lines for your flat. Glue or tack the shims into place, and you won’t have to repeat this process at the other locations. Clamp the jig in place on the lamination.
Set up your router so that a 1⁄2” straight (or spiral-upcut) bit just touches the top of the inner surface of the jig. Start the router in an upper corner, safely away from contact with the lamination. Then rout around the edges clockwise (in a gentle climb cut) to give you a clean edge. Go slowly across the step at the bottom so you don’t blow out the wood as you exit the cut. Then rout away the remainder of the flat. Finish the other three flats the same way.
Layout for the wings requires a little more work. Do this on a large surface of at least 31″ x 55″, with a square edge (I used a piece of plywood a little bigger than that). The base of the table actually fits into a rectangle roughly 54″ wide by 303⁄4” tall (your base may vary slightly in from this size).

Full-size layout. A piece of plywood locates the corners of the large arch and the wings. Mark the wings from the flats on the arches.
The ends of the wings are directly above the bottom of the arch (on the outside face). You’ll use this to lay out where the flats need to be cut on the wings. Measure 303⁄4” up from the bottom of the plywood along the square edge and mark a line. Set up the arch on three or four 11⁄2“-thick scraps (I used the lamination offcuts) with the bottom aligned with the bottom edge of the plywood and one side at the square edge. Now take one of the wings and place it on the plywood with the more curved end toward the arch.
The goal is to find a location for the wing that allows the curve to flow well into the bottom of the arch while the top part of the wing touches the edge of the plywood at the 303⁄4” mark. Once you’re satisfied with the location, trace the flat and the step onto the wing. You can also make a mark 1⁄2” above the 303⁄4“ line, where you’ll be able to trim the top of the wing roughly to size.
Now you need a way to cut the flats on all four of the wings. The easiest way to do this is to create a positioning jig. Start by tracing the inside curve of a wing onto a piece of 3⁄4” plywood, particleboard or MDF, and cut out the shape. Place this curved piece on a larger rectangle of plywood. Move the wing and the curved piece so that the line you marked from the flat of the arch is located over the edge of the rectangular plywood. Confirm the location, then screw the curved piece down. Now, if you set up to cut flush with the edge of the plywood, you can cut each of the wings held in place on this positioning jig just where they need to be cut.
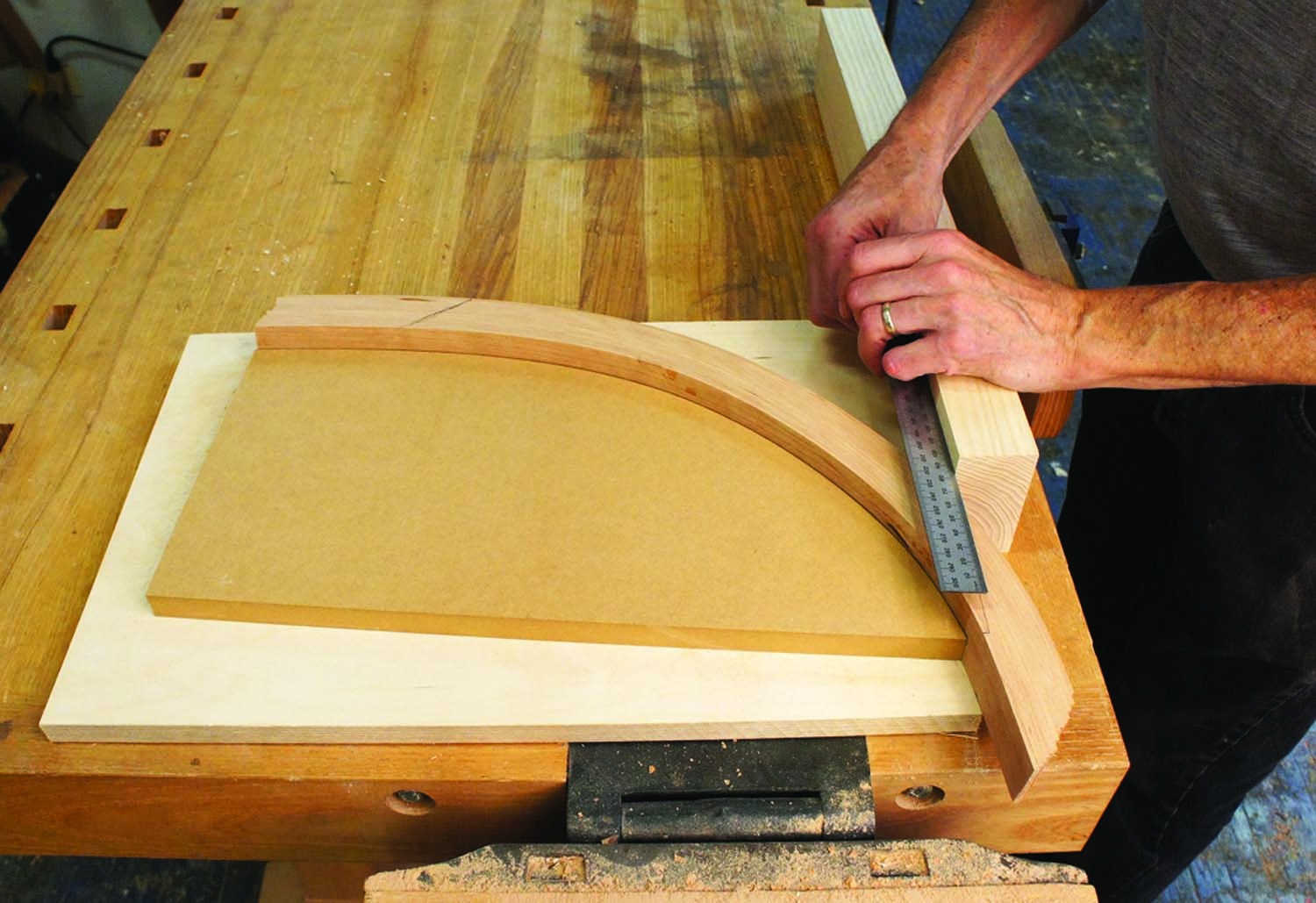
Let it ride. Align the straight cut on the wing with the edge of the jig base.
You still have to crosscut the pointy end you just created on each wing so it will match up with the step on the arch. This is an easy crosscut on the table saw using the miter guide with a sacrificial fence. Mark out the cut location, and place the wing’s flat down on the saw table. Clamp to the miter guide so nothing slips, and make the cut.
The main arches need two small mortises each for the stretchers. The basic approach to cutting these joints is to create a simple positioning jig you can clamp into place that will allow you to rout (or use a hollow-chisel mortiser, or drill) as if the part were a rectangle.
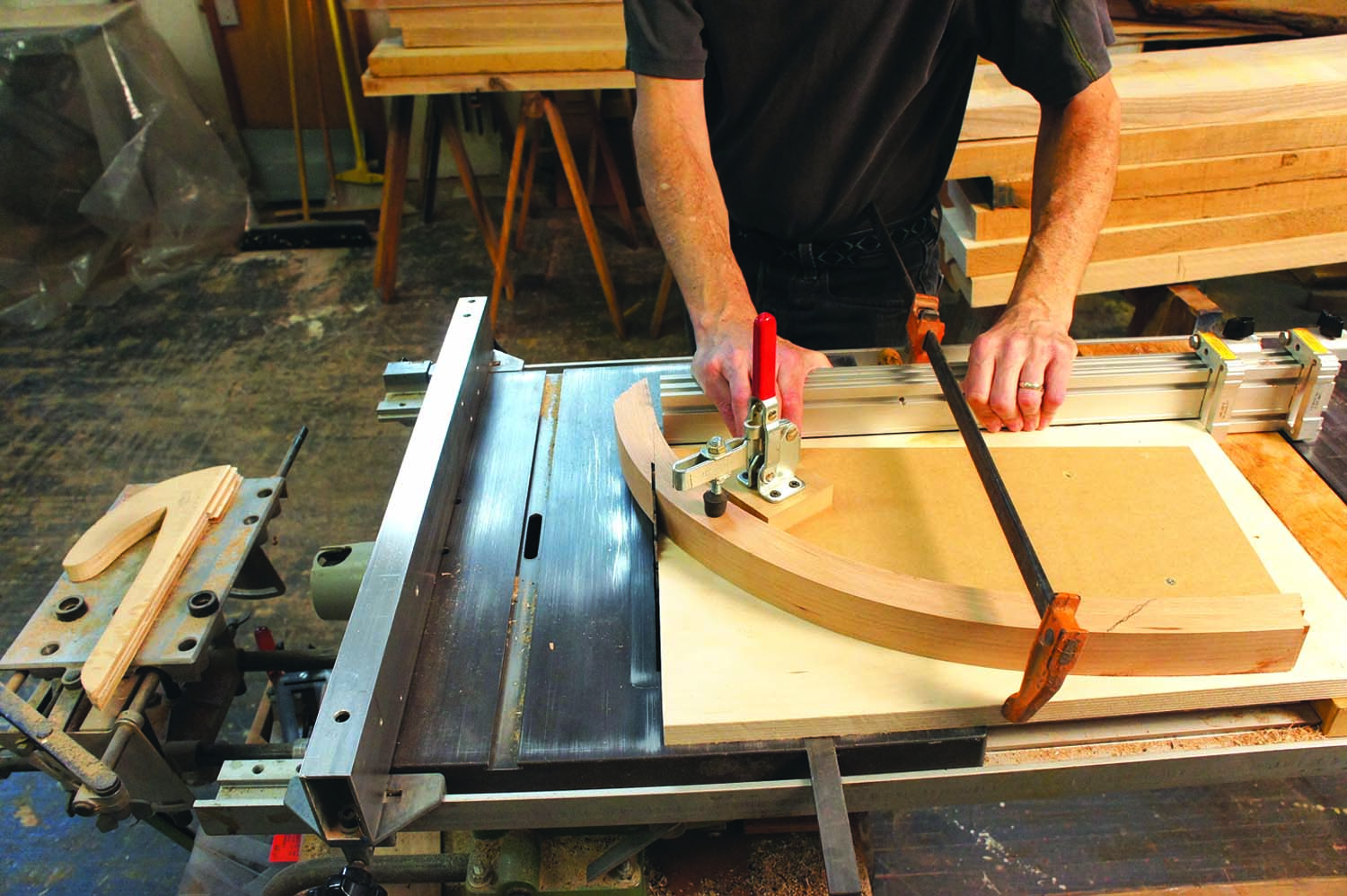
Safe & secure. The jig holds the curved part securely to make the cut, creating a flat surface to attach the wing to the arch.
Plunge routing requires a wide, stable platform for the router to rest on, so I used a 4″-wide board of the same thickness as my lamination to make the jig. Start by measuring 83⁄8” up from the bottom along the outside of the lamination. Mark a line there for the center of the 3⁄8“-wide x 7⁄8“-long mortise. The centerline of the mortise will be 19⁄32” from the outside edge of the arch. This is slightly off center, but there’s still another lamination layer to add to the outside of the arch.
The goal now is to mark a cutout in the positioning jig so the outer edge of the jig lines up parallel with where the mortise needs to be (basically tangent to the curve at the centerline of the mortise). Cut out the arch shape, then transfer the mortise location to the jig, and square it around to the other side as well.
Clamp the positioning jig in place, and set up a plunge router with a fence. Set the fence so the 3⁄8“ x 7⁄8” mortise will be centered 19⁄32” from the outside edge of the arch. You can either transfer marks to the arch and rout by eye, or set up some stops to limit the travel of the router. Rout the mortise roughly 1″ deep. I find that a series of very shallow passes gives a more accurate result, with less chatter of the router bit. You can simply flip the jig over to rout the opposite side of the arch.
Drill and countersink three holes in each wing, perpendicular to the flat face. Now screw the wings into place temporarily (no glue!) so you can lay out the tops of the wings and the front and back aprons. The aprons are 1″ high, 11⁄8” wide, and roughly 60″ long. Save a couple scraps from milling them so you can prop up the arch for an easier layout. The layout process takes place on the plywood you used to set up the wing alignment. Here, prop up the arch on the scraps at the bottom and the stretcher at the top. Align the bottom of the arch with the bottom of the plywood and clamp it in place.
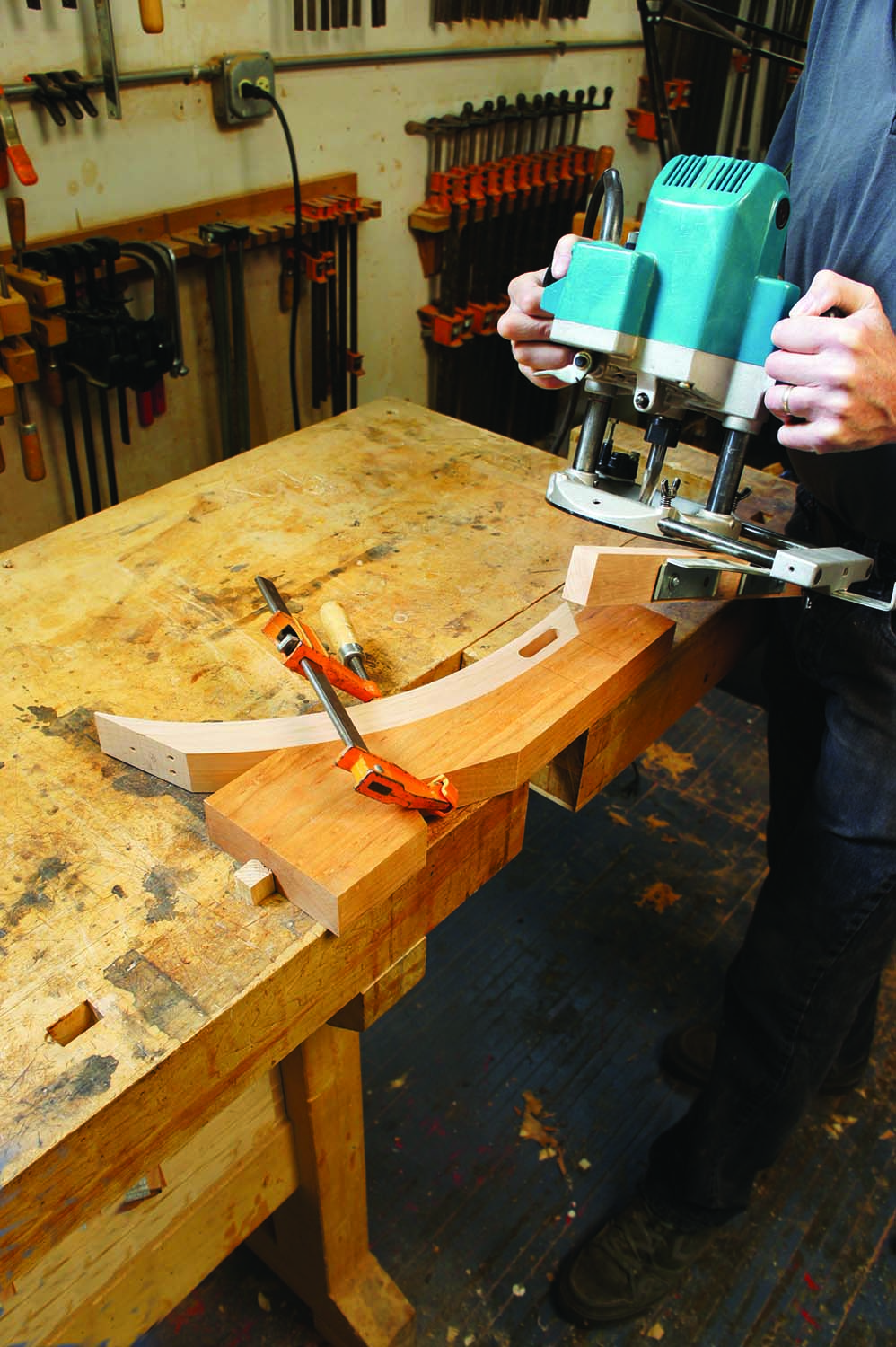
Create a line. This jig provides a flat reference for the router fence and holds the wing securely to make the mortise.
The apron should be set so the line that is 303⁄4” up from the bottom of the plywood is at its top. Now you can mark the curvature of the wings onto the apron, and the tops of the wings from the top edge of the apron (use a short pencil stub to mark from underneath). Label each location so you can put everything back together the way you marked it. Carefully saw to your lines. You’ll have a chance to rout the tops of the wings flush later, but you should try to smooth the ends of the aprons carefully to fit the wings. You can undercut the center portion of the apron’s ends a little bit if you like.
Mortising the upper part of the wings for the side aprons is very similar to mortising the arch for the lower stretchers. Make a similar positioning jig with a straight edge parallel to the mortise you need, then locate the mortise by referencing off that edge. These mortises should be 1⁄2” x 2″ x 11⁄4” deep.
Shaping & Smoothing

Cover your tracks. The final strip covers the joint, leaving uninterrupted grain on the outside of the assembly.
Lay out a curved taper on the inside of the arches, starting opposite the wing joint and tapering down to 1″ wide at the bottom of the arch. You can use the outside of the other arch to draw this curved taper. Band saw the waste off, then smooth the curve. This can be a little tricky, because the glue lines are harder to cut than the wood, but a sharp spokeshave followed by a scraper usually does the trick. Sandpaper on an appropriately curved sanding block will work, too. While you’re at it, smooth out the rest of the arch and the convex parts of the wings and chamfer the very bottoms of the arches’ “feet.”
Assembly

Fair curve. Clean up the transition between the wing and the arch to provide a smooth bed for the last laminate.
It’s finally time to attach the wings to the arch. Glue and screw them into position and plug the holes. Then refine the transition (and flush off the plugs) with a spokeshave, rasp, scraper and/or sanding block so you’ll be able to glue and clamp the final layer to the outside of the arch and wing. Be careful not to round over this surface from side to side or you’ll never be able to glue the final layer on effectively. Check to be sure that the outside strip will actually conform to the refined curve and adjust as necessary. Then cut the outer strips so that they are a few inches longer than needed. They should remain wider than the laminations to leave some room for misalignment.
It takes a lot of smaller clamps to glue on the final layers. I only do one of the four glue-ups at a time. I use 1⁄4” Masonite strips or extra sliced layers as cauls and to protect the inside of the arch from the clamps. I also screw some shaped blocks to the masonite to help position some of the clamps appropriately. A dry run will help you figure out what you need to do to stay in control when the glue is finally applied.

What chisels are for. A router bit won’t reach the inside corner to shape the edge. Carve into the corner from both directions.
When the glue is dry, cut the excess length, plane off the excess width and finish smoothing out all of the edges as well. There are probably little bits of the routed flat sections above where the wings attach to the arches. A bit of sandpaper backed up by a thin scraper makes it easy to get in there to ease that transition. Round over all of the edges with a 1⁄4” roundover bit set to about two-thirds of its normal depth, then follow this up by carving, filing and sanding the inside corners of the arch-to-wing intersections.
Mill the side apron and lower stretcher blanks. Cut and fit the tenons. Then band saw and smooth the lower stretchers to shape. Make sure to ease the bottom corners of the stretchers a little to avoid the short-grain weakness there. Then round over the edges to match the arches. Bevel the tops of the aprons to roughly the angle of the wings, but leave them a little long for now.
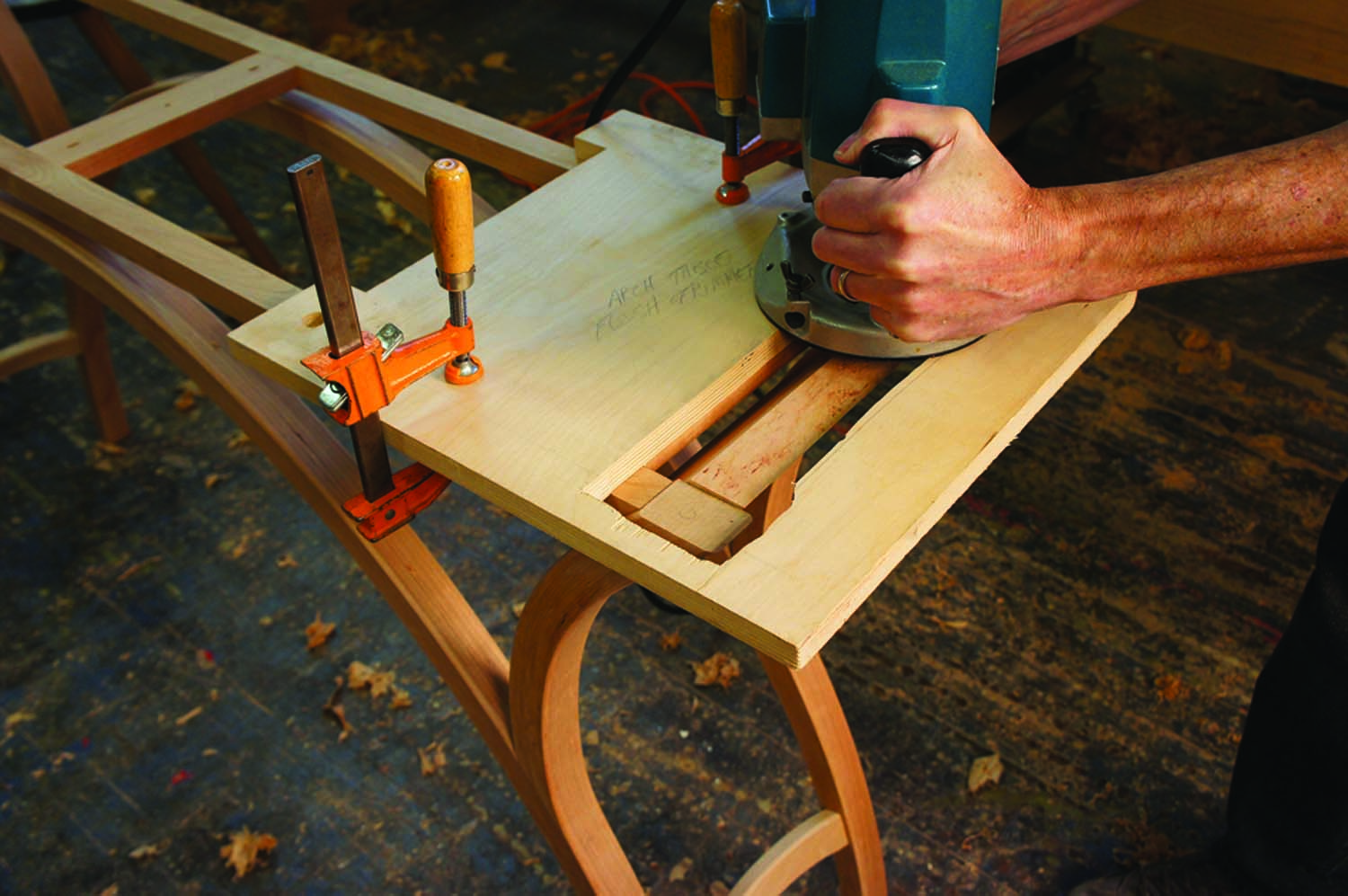
Plane truth. This jig provides a flat surface for the router base, bringing the front-to-back rails and the tops of the wings flush with the aprons.
Drill countersunk pilot holes – essentially pocket holes – in the ends of the front and back aprons so you can attach them to the wings. These should be roughly perpendicular to the angled ends of the stretchers. You also need to mortise the inside faces of these aprons for three crosspieces you’ll use to attach the tabletop to the base. You can determine the length of these crosspieces by dry-fitting the arch assemblies and the aprons together, then setting the front and back aprons in place centered on the width of the wings. Measure the distance between aprons, then add the tenon lengths to get the overall lengths.
Cut and tenon the crosspieces, then drill them for the screws to attach the top. The center holes can be left as-is, but the holes to the front and back should be elongated to allow for expansion and contraction of the solid top. Smooth any components that still need attention.

Independent top. After shaping and finishing the top, attach it to the base with screws through the front to back rails.
Glue up the arches with the lower stretchers and side aprons. Separately, glue up the front and back aprons and the crosspieces. Once the arch is out of clamps, you can screw the upper apron assembly in place. I flush off the tops of the aprons and legs using a large piece of plywood that has a rectangular opening that fits over the ends of the legs and end apron. I clamp this in place on the front and back aprons, then rout away anything that projects above the height of those aprons. Be sure to use a light climb cut to avoid blowing out the edges.
Making the top is nothing out of the ordinary. Shape the end curves on the band saw set up with adequate support to the side. Plane everything smooth, then rout and smooth the edge profile on top and bevel the underside. You can screw the top on now, but I usually wait until after finishing the table; it’s much easier to finish the top and base separately. I finish with five or more coats of an oil/varnish blend followed by a coat of wax, but any finish you’re comfortable with will work.
BLOG: Read Jeff’s design and furniture making blog.
VIDEO: Jeff talks about his table in our free online video.
VIDEO: Watch our free video of Jeff’s ellipse jig in action.
Jeff is a Chicago-based furniture maker and woodworking teacher.
Here are some supplies and tools we find essential in our everyday work around the shop. We may receive a commission from sales referred by our links; however, we have carefully selected these products for their usefulness and quality.