We may receive a commission when you use our affiliate links. However, this does not impact our recommendations.
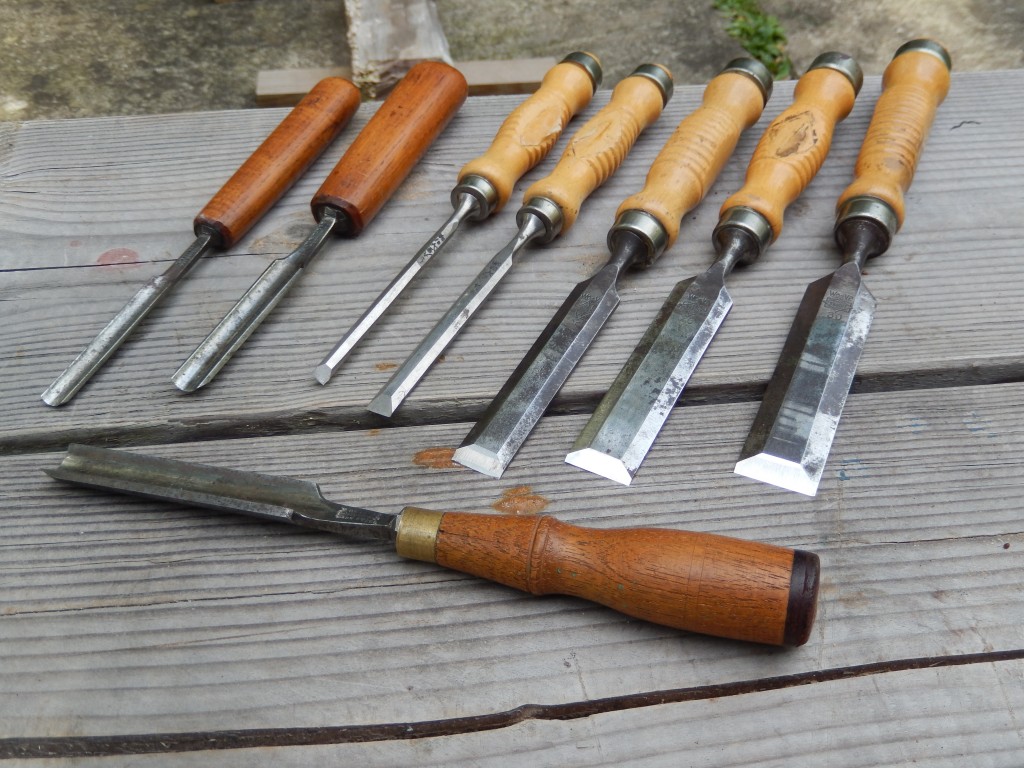
This is the lot of five chisels and three gouges that I won on eBay. At a cost of $34 I think it was a very good deal.
For me, as well as for many other woodworkers (see Graham Haydon’s recent entry on his chisel), eBay is a great resource for good-quality tools. When an item is well described, correctly identified and accurately photographed, the risk we take by bidding is small – yet it is very likely that the bidding war will be fierce and the concluding price will be high. On the other hand, there will be less competition on items whose descriptions, images or conditions are less than ideal. Of course the risk you take in committing to the purchase is higher, which turns the whole experience into a kind of gamble. In the case of the gouge lot that I won a few months ago, the gamble ended to be up a sweet deal.
I won $34 worth of tools that included a set of five German bench chisels by Bracht plus three gouges that the seller described as made by “Butche.” Two of the gouges seemed to be fitted with non-original custom-made handles, probably crafted by a previous owner. The widest gouge that was stamped “W. Butche, Sheffield England” appeared to posses the original handle – which looked to be in very good shape except for two cracks emanating from the socket mouth. When I had a chance to try it I noticed that the original handle was loose and the tang could be pulled out of its socket with no resistance. There was a very small gap between the tang and the socket which I realized I had to take care of. (In my next two posts I will explain how I did this.)
When dealing with recommissioning valuable vintage tools I think like a restorer. My guiding question is, “What do I need to do in order to bring it back to functioning order without drastically degrading its value or appeal?” I also respect the fact that I am probably not going to be the last person who will use it, nor will I be the last individual who will endeavor to restore it. That thinking dictates careful repair methods, closely matching materials, glues and finishing techniques. In essence, I try to intervene the least while achieving the most.
One of the traditional fixes for a loose tang is to drill out the socket, glue in a dowel, drill the dowel progressively with consecutive drill bit diameters (to match the geometry of the tang, of course), then reinstall the tang into the socket. This is an effective technique but it is considered drastic in the restorers’ book of conduct because it extracts a non-proportional amount of fine wood from the restored handle. A more measured technique that better fits restoration ethics is to fill in the tang socket with just enough wooden shims to provide the chisel tang with a tight fit. But filling in the socket with random or even nicely cut shims will not provide a long-term solution. To ensure the longevity of the restoration, you have to make sure that the shims fill the gap between the tang and the socket completely and are reliably glued to the walls of the socket. That task can be tricky.
You can imagine how difficult it can be to tailor-fit tiny strips of wood so they can fill a gap you can’t fully see. You don’t want an under-filled gap that will lead to the tang loosening again after a few months of use. And you need to be careful not to over fill the socket, because that might prevent the tang from mating well and create a gap between the chisel shoulder and the handle. Or worse, causing the tang to split the handle or perhaps even break the ferrule.
Thus, your major challenge is to assess how much exactly to overfit the supplemental wood in order to provide the tang with enough compression to sit securely in the socket.
In my next post, I will show how I did this.
Editor’s note: If you’re interested in restoring vintage tools, check out the new edition of Michael Dunbar’s classic book, “Restoring, Tuning & Using Classic Woodworking Tools.”
Here are some supplies and tools we find essential in our everyday work around the shop. We may receive a commission from sales referred by our links; however, we have carefully selected these products for their usefulness and quality.
Yoav you literally have a picture of my next project staring back at me from my bench! I have a lovely firmer gouge that requires a new handle. I was planning to make an 18th Century style handle as I don’t yet own or know how to use a lathe. I look forward to seeing how you bring yours back to working order.
Best
G