We may receive a commission when you use our affiliate links. However, this does not impact our recommendations.
Most warp takes place as green wood dries, but the potential for movement remains after lumber is brought into your shop.
By Glen D. Huey
Pages 6-10
From the Summer 2009 issue of Woodworking Magazine.
The quick answer to why wood warps is simple: There’s a gain or loss of moisture content (water). We’ve all brought perfectly flat boards into our shops only to discover that, while sitting on the rack, some have warped. And we’ve been told to give lumber time to acclimate to our shop surroundings before milling operations begin. There are reasons for these woodworking words of wisdom.
Predicting the movement of wood is not easy. For this, we need to examine a tree’s journey from freshly cut to dry and ready to use. And we need to know where in the tree the lumber existed prior to being slabbed into pieces.
Fresh-cut or green wood is loaded with water. Moisture content, when the tree is felled, can vary anywhere from 30 percent to nearly 250 percent of the final dried weight, depending on the species and whether the wood is from near the center of the tree or located more toward the outside.
Water within green wood is classified as either “free water” or “bound water.” Free water is lost quickly and bound water needs to be forced from the wood’s cells. When free water is totally dissipated, the wood has reached its “fiber saturation point” (FSP). Drying beyond the FSP is when the wood begins to give up bound water.
In “Understanding Wood” (Taunton), R. Bruce Hoadley explains this phenomenon using a sponge to represent wood. A fully soaked sponge pulled from a bucket of water quickly gives off free water. Even as the sponge is wrung out, additional free water is released. But when no additional water can be wrung from the sponge, the sponge has reached its FSP. Moisture still in the sponge is bound water. It is only with the removal of bound water that the sponge begins to shrink and harden. It’s the same with wood. It is only after the board passes below its FSP that the wood begins to shrink and move. Conversely, wood will swell as moisture is added or absorbed. This is why you need to allow the wood to acclimate.
As wood moves below its FSP and begins to shrink, three typical directions of movement are possible: longitudinal (movement along the grain), radial (movement perpendicular to the growth rings) and tangential (movement perpendicular to the grain and parallel to the growth rings).
Three Typical Movements
Longitudinal movement in normal wood is negligible. When going from green to dry, movement along the grain averages less than 0.1 percent – a 10′ piece of green wood shrinks about 1⁄8″ along its length. This movement is so small it has almost no impact on our woodworking techniques. If, however, the hardwood is juvenile wood (less than 20 years from the tree’s center) the shrinkage can be upward of 2 percent or some 20 times greater.
Radial movement is shrinkage that occurs as you move outward from the center of the tree. In flat-sawn lumber, radial movement affects thickness. This shrinkage is intermediate to the other two kinds of movement and is generally, in North American species, stated to be between 4 percent and 6 percent. On a flat-cut, 2″-thick piece of hardwood, movement could be as much as 1⁄8″ in thickness.
The third movement, and the one that is most substantial, is tangential movement. This is movement across the grain and should always be considered when building projects. Wood movement across the grain, again based on North American species, can be from a low of 6 percent to a high of around 12 percent. A flat-sawn 6″-wide board could move up to 3⁄4″ from the green to the dry stage. As you can see, tangential movement is nearly double that of radial movement.
It’s important to note that each example given to this point is for flat-sawn stock. Quartersawn stock – where the width of the lumber is perpendicular to the growth rings – reacts differently. Quartersawn lumber is more stable because the faces of the boards react to radial movement instead of tangential movement.
Any of the movements or shrinkages discussed thus far are natural, normal reactions to wood drying. These are expected and accounted for by those who cut or dry wood. For most of us these movements are not as severe. We’re not moving from a felled tree to dried lumber, but we do need to consider movement due to humidity changes (be they extreme changes or not) and exposure.
Movement by the Numbers
The Department of Agriculture’s Forest Products Laboratory has established a set of numbers that indicates the amount of movement you can expect within a given species for flat-sawn (tangential) and quartersawn (radial) boards. These numbers, which represent the amount of movement that occurs per unit of width given a 1-percent change in moisture content, can be found in their information-packed “Wood Handbook.”
To determine what amount of movement to expect, measure the width of your board, establish the average yearly change in moisture content for your area, find the appropriate coefficient for your wood and do the calculation. (For more information see Woodworking Magazine Autumn 2005, Issue 4.)
Let’s work an example: If we have a 6″-wide, fully flat-sawn piece of red oak (a species with a high propensity for movement), and we experience a moisture-content change of 3 percent, and with the guide coefficient at .0037, we can expect an overall movement of .0666″, or just more than 1⁄16″ (6″ x 3 x .0037 = .0666″).
This number is far different from the 3⁄4″ figure given earlier and that illustrates the difference in working with lumber that is dry and is simply fluctuating with changes in humidity, and lumber that is moving from green to dry.
Most woodworkers use this guide to confirm what they are already doing. We know wood moves. We know you need to allow for movement. If you do the calculations, you begin to understand just how much wood moves.
For me that’s a bit more information than necessary and too exacting. Besides, most panels that we glue up, and any wide boards used in our projects, are generally not one type of cut. Most are a combination of quartersawn and flat-sawn, and some may be rift-sawn (the face of the board meets the growth rings at angles between 30 degrees and 60 degrees). With different grain patterns involved, to use the charts requires us to make judgment calls – a potential for error.
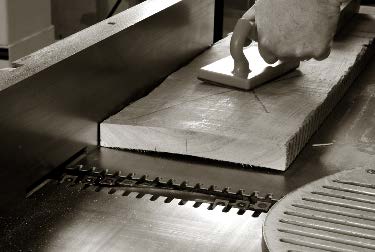
Knowing that boards generally cup toward the bark side of the tree is a quick indication of how the piece should be surface planed.
It’s better to keep in mind which woods have a higher potential to move, cup or twist. Armed with that information, we can make calls that affect the way we work in the shop. If you know that Eastern white pine moves more than poplar, and you are assembling drawer bottoms in either wood, you know whether to complete the process that day or if you can allow the panels to sit until the next time you’re in the shop.
This information is available from the numbers supplied by the Forest Products Laboratory. To get a general assessment of wood warp, divide the number given for tangential movement (T) by the radial movement number (R). This figure, expressed as a ratio (T/R), is the tendency for wood to distort while drying. The closer this ratio is to 1, the less warp you have to worry about. Mahogany and walnut, each with a 1.4 T/R ratio, are more stable and less prone to warp with changes in humidity than red oak or soft maple (T/R = 2.2) or Eastern white pine with a T/R ratio at 2.9.
What is Warp?
Warp is comprised of a few different movement issues. The three major movement issues we consider in woodworking are cup, bow and twist. Of the three, the most common warp is cup.
A board cups when one face shrinks more in width than the opposite face. The rule of thumb is that boards cup toward the bark side. An easy way to visualize this is to imagine that the growth rings are trying to straighten. While this is most often the case, you will find boards that cup in the opposite direction. Again, this is an issue in flat-sawn lumber. In quartersawn stock, it’s not so much of a problem due to quartersawn stock being cut across the growth rings.
Information about cup in stock is important for a couple reasons. First, if you know that in all likelihood the cup is facing the bark side, you can quickly ascertain the face that should be milled first at the jointer.
Additionally, if you’re planning a project you may choose to position the bark side of the stock in a particular manner. Attaching backboards is an example. Position the bark side of each board to the cabinet, then if the board were to cup, the movement would force the edges of each board tight to your case.
Occasionally, although it is rare, boards have enough moisture variation along the grain to cause excessive movement. One face of a board shrinks more than the opposing face. Wood movement of this kind is referred to as “bow” and it happens in both flat-sawn and quartersawn lumber. Quartersawn lumber also experiences “crook.” Crook is movement along one edge of the lumber. Boards almost always bow in one direction, toward the center of the tree.
Bow and crook are found most often in lumber cut near the center of the tree. This lumber is generally designated as a lower grade of stock.
Twist is where the opposing pairs of diagonal corners of a board are not in the same plane. If you position a twisted board flat on your jointer or flattened benchtop, the opposing corners on opposite ends touch the surface and the two other corners do not. Place pressure on one of the corners that is held off the surface and the board rocks to that side. Remove the pressure and the piece rocks back.
If you have to flatten twisted material, trim the high corners of the piece until you eventually plane the entire face. If you’re using handplanes, the process is simplified. If machines are your method for milling, position the piece at your jointer with pressure on the trailing end’s corner that’s hovering above the table to secure it to the surface, then begin your pass over the knives. As the board reaches the middle of its length, switch the pressure off the trailing corner and onto the leading corner that is now off the table. This change causes the knives to trim the trailing high corner. After you flatten one face, use standard procedures to get your workpiece ready to be surfaced on all four sides.
Follow the Basics
After discovering why wood warps, types of warp and how to predict potential movement, you realize how important a couple basic steps are to make milling lumber easier.
You should always allow lumber to acclimate to your shop – a period of seven to 10 days should do the trick. Any movement prior to surfacing stock is much better than boards moving after you have reached your final dimensions. And it’s best to trim your material to rough-cut sizes prior to milling operations. I suggest 1″ of additional length and 1⁄4″ extra width. Reduce the pieces to your rough-cut size and you reduce the overall warp in your stock. There is no reason to walk away from an 8″ board that’s cupped 1⁄2″ at the center if you can rip that piece at 4″ and greatly reduce that warp. The same methodology holds true with bow and twist.
Of course, the best advice is to buy properly cut and properly dried lumber – then cup, twist and bow will seldom visit your shop.
Here are some supplies and tools we find essential in our everyday work around the shop. We may receive a commission from sales referred by our links; however, we have carefully selected these products for their usefulness and quality.