We may receive a commission when you use our affiliate links. However, this does not impact our recommendations.
One of the oldest designs for a dining table is also one of the most highly engineered
and contemporary. But will its unusual dimensions work in a modern home?
By Christopher Schwarz
From the Autumn 2006 issue of Woodworking Magazine
Traditional trestle tables have a bit of an austere reputation. They show up in Gothic churches, prim pilgrim homes and in severe, stripped-down Shaker meeting halls. They are a form of furniture that has been boiled down to its bare bones – take any one part away, and a trestle table will surely collapse.
Once you build one, you will also realize that they are an engineering marvel and a clear precursor to the invention that built our skyscraper cities: the I-beam. Still, despite their spare charm and long history, there are some things about the dimensions of trestle tables that don’t conform to our typical expectations for tables.
For starters, they are shockingly narrow. Most furniture-design books insist that the top of any dining table should be 36″ to 42″ wide – and 48″ wide isn’t out of the question. But when you look at the historical record, the widths of trestle tables are, quite literally, in your face. One of my favorite early 17th-century trestle tables in Millis, Mass., is a slim 25″ wide. By comparison, Shaker trestle tables seem positively luxurious with 27″ and 311⁄4″ widths.
And the trestle form frequently looks quite fragile, which seems at odds with the fact that these tables are typically the centerpiece of a casual dining area. They show up in taverns, meeting halls and other communal dining rooms, and the surviving examples exhibit the marks and scars of heavy use.
For many years, I’ve wanted to build a trestle table to replace the store-bought, white-pine apron table my wife and I got soon after college. The pine apron table was a testament to everything I disliked about commercial furniture: The top was pieced together using narrow, knotty and poorly matched boards. (A monkey could have done a better job of planning the tabletop.) The legs had bulbous turnings that were sloppily sanded. And the hardware that joined the legs to the aprons had to be snugged up regularly.
But if I hated our dining table, then I was equally afraid of the trestle table I wanted to build, which looked narrow, tippy and ready to collapse, so I put it off for 15 years. But during a recent day trip to the Shaker Village at Pleasant Hill, Ky., I sat at the tables there. They were indeed narrow, but that made them more intimate for conversation. They were lightweight, which allowed them to be moved with ease. And after 150 years of use, they were still rock-solid.
I left Pleasant Hill that evening during a spectacular thunderstorm, but the fireworks over Harrodsburg, Ky., didn’t catch my eye. I was too wrapped up in working out the details of my table in my head.
An Economy of Materials
After a few hours of CAD work on my laptop, I had another small revelation: These tables require remarkably little material. For the prototype, I had planned on using Southern yellow pine for the base. For the tabletop, I had set aside two flitch-cut cherry boards from a local farm that were each about 18″ wide, if you measured the bark. I had purchased these cherry boards green for about $90 and had been drying them in my shop – I thought they were quite the bargain. But when I made my shopping list for the base, I was pleased
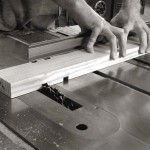
To keep your hands as far away from the dado stack as possible, use a fence with a stop on your miter gauge to set your cut.
to discover that the base required only three 10′-long 2 x 12s – about $37 of yellow pine.
There is a definite downside to using yellow pine – it can be wet. And a check with a moisture meter pointed out the problems in this pine. Fully acclimated yellow pine usually reads about 9 percent moisture content (MC) in our shop. This stuff ranged from 12 percent to 16 percent MC.
So I began by marking out all my parts and ripping and crosscutting them to rough size – about 1″ longer and 1⁄2″ wider than their finished dimensions. If your wood is fairly straight, this is a safe operation for the table saw. If your wood is quite twisted, plan B should be a band saw or handsaw. Cutting up the 2 x 12s wet does two things: First, it speeds their drying by exposing end grain – most of the moisture enters and leaves wood through the end grain. Second, it helps squeeze the maximum thickness out of the parts – bows, cups and crooks are minimized by cutting a larger board into smaller pieces.
After a week of waiting, the boards were all within a couple points of equilibrium and construction could begin. The first step was to mill all the yellow pine to 11⁄4″ thick using a
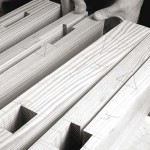
After the joinery is cut, match up the pairs again. Note the cabinetmaker’s triangles I’ve scribed on each piece.
jointer and planer. The joinery in surviving trestle tables is remarkably robust: usually wedged or pegged through-tenons. And so I followed suit.
Each end of a trestle table has a foot, leg and brace. And these end assemblies are joined by a long stretcher. In this table, the leg and foot are joined by a wedged and pegged through-tenon. The brace and leg are joined by a bridle joint. And the two end assemblies attach to the stretcher with a big pegged and wedged through-tenon.
The feet, legs and braces are each made up of two pieces of pine that have been face-glued together to create 21⁄2″-thick pieces. To ease construction, I milled the mortises in the feet and legs before face-gluing these components together. This technique allows you to mill the mortises with a saw (such as a table saw, band saw or handsaw) instead of a boring machine, and it results in more accurate joinery.
Download the PDF here for drawings and cutlist:
American_Trestle_Table
Here are some supplies and tools we find essential in our everyday work around the shop. We may receive a commission from sales referred by our links; however, we have carefully selected these products for their usefulness and quality.